Needle roller bearings have needle rollers as rolling elements. Needle roller bearings are defined where cylindrical rolling elements are classified as needle rollers if the rolling element diameter is ≦6 mm and the ratio of the rolling element diameter to the rolling element length is Dw/lw<1:3. These bearings are known for their high load-carrying capacity and ability to operate in tight spaces with limited radial and axial clearance. Their use at high speeds is restricted.
The types of needle roller bearings we are discussing are Drawn Cup Needle Roller Bearings with Closed End, Drawn Cup Needle Roller Bearings with Open Ends, Machined Needle Roller Bearings, Aligning Needle Roller Bearings, and Inner Rings.
This article will take a closer look at these different types and discuss their various characteristics.
What are the characteristics of needle bearing?
A defining feature of needle roller bearings is their use of long, slender cylindrical rollers, with a length-to-diameter ratio of 3 to 10. This contrasts sharply with the shorter rollers found in conventional bearings. The extended roller design is not merely for space-saving; it’s a strategic choice that significantly enhances radial load capacity without increasing the bearing’s radial size.
The elongated nature of these rollers enables a more extensive contact area with the raceways. This extended contact zone allows for a more effective distribution of loads over a broader surface area. Consequently, needle bearings boast a superior capacity to handle higher radial loads, a critical factor in many engineering applications.
The compactness of needle bearings is one of their most appealing attributes. Despite their high load-bearing capacity, these bearings maintain a significantly smaller radial section height compared to traditional roller bearings. This makes them exceptionally suitable for applications where radial space is limited but high load capacity is essential.
While needle bearings are adept at handling high radial loads, they are generally not designed to withstand high axial or thrust loads. Their suitability for high-speed operations is contingent on various factors like bearing design, lubrication, and operational conditions. Engineers must carefully consider these parameters, as needle bearings might not be optimal for applications requiring very high speeds.
In their standard form, needle bearings exhibit limited tolerance to misalignment between the shaft and housing. However, certain designs incorporate features to accommodate slight misalignments, expanding their application scope.
How Needle Bearings Differ from Other Bearings
When comparing needle bearings to other types of bearings, their distinct design and performance characteristics stand out. Unlike ball bearings or larger roller bearings, needle bearings feature a compact profile and slim needle-like rollers. This unique design serves specific needs, particularly in applications where space is limited but load-carrying capacity is critical.
Key Advantages of Needle Bearing
Needle bearings offer several advantages that make them indispensable in certain applications. Below, we highlight their primary benefits and explain why these characteristics matter.
High Load Capacity
- Despite their small size, needle bearings can support high radial loads. Their elongated rollers distribute weight efficiently across a larger contact area, ensuring reliable performance in demanding conditions. This feature offers an advantage in applications like automotive and aerospace where restrictions for space are necessary along with higher load capability.
Low Cross-Sectional Height
- One of the standout features of needle bearings is their minimal height. This slim design allows them to fit into tight spaces, where other bearings simply wouldn’t be an option. For example, in compact machinery or intricate assemblies, needle bearings help engineers keep designs streamlined without compromising functionality.
Compatibility With Compact Designs
- Needle bearings thrive in setups where compactness is key. Whether it’s a small gearbox or a confined motor, they deliver the required support while saving space. Their ability to slot into narrow gaps without sacrificing load-carrying capacity makes them a go-to choice for engineers aiming for precision compact designs.
To better understand how needle bearings are utilized across various systems, consider exploring our Needle Roller Bearings Archives, where you’ll find examples of applications and designs they’re commonly incorporated into.
In summation, needle bearings distinguish themselves through their ability to balance small size with impressive performance capabilities. This makes them a unique solution compared to other bearing types and an essential tool in applications requiring both strength and compact designs.
Drawn Cup needle bearings
Drawn cup needle roller bearings are the more common type of needle bearing and are designed with a thin-walled outer ring and a needle roller and cage assembly. Full complement needle roller bearings, have the maximum number of rollers with no cage, which results in a higher load-carrying capacity.

Drawn cup needle roller bearings with open and closed ends both have a very small radial section. Drawn Cup needle roller bearings are thin walled with drawn cup outer rings and needle roller and cage assemblies which become a complete unit. The outer rings conform to the dimensional and geometrical accuracy of the housing bore during fit up.
The dimensional and geometrical accuracy of drawn cup needle roller bearings with open and or closed ends conforms to DIN618 standards. The main dimensions of the bearings correspond to DIN 618:2008 and ISO 3245:2015. Nominal dimensions of bearings applied directly to a shaft inner ring can be used if necessary.
If axial locating elements such as shoulders and snap rings are not used, the housing bore can be produced easily and particularly economically. This also allows simpler mounting and dismounting of the bearings.
Overview of needle bearing designs and structures
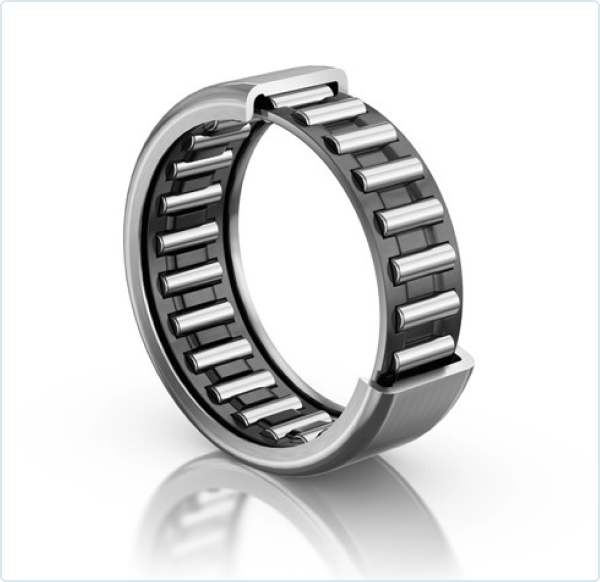
All types of Needle bearings are designed with a cylindrical rolling element. The needle bearings with the highest speed capability are designed with a cage where rollers are guided, which maintains spacing and reduces friction. Full Complement type needle roller bearings have rollers not separated by a cage. With only a few exceptions, the cages are made from sheet steel. Bearings with a plastic cage have the suffix “TV.”
The outer ring of a needle bearing can be stamped steel or hardened steel depending upon the type, where rollers are made from hardened steel.
Comparison with other types of roller bearings
Compared to other types of roller bearings, such as cylindrical and spherical roller bearings, needle bearings have smaller cross-sections and are used in completely different applications.
Components of a Needle Roller Bearing
Needle roller bearings are essential components in various machinery and equipment. Let’s look further at the key components of a needle roller bearing:
- Outer Ring. The outer ring is typically the stationary part of the bearing and provides support and housing for the other components. It is usually made from hardened steel to withstand external loads and ensure dimensional stability.
- Inner Ring. The inner ring is mounted on the rotating shaft and is responsible for transmitting the load from the rotating element (such as a shaft) to the rollers. Like the outer ring, it is also made from high-quality steel and may have a raceway for the needle rollers to move along.
- Needle Rollers. Needle rollers are the load-carrying elements in a needle roller bearing. These cylindrical, needle-shaped rollers have a much smaller diameter compared to their length, allowing them to handle high radial loads efficiently. They roll within the raceways of the inner and outer rings, distributing the load evenly.
- Cage or Retainer. The cage or retainer is an integral part of needle roller bearings, serving to maintain proper spacing and alignment of the needle rollers. It prevents direct contact between adjacent rollers, reducing friction and wear while also enhancing the overall stability of the bearing.
- Raceways. The raceways are groove-like channels or paths in the inner and outer rings. They guide the movement of the needle rollers, ensuring they remain in place and distribute the load evenly. The shape and design of these raceways may vary depending on the specific application and type of needle roller bearing.
- Seals and Shields. Needle roller bearings may include seals or shields to protect the internal components from contaminants, such as dust, dirt, and moisture. Seals provide better protection but may increase friction, while shields offer some protection while maintaining lower friction.
Choosing the Right Needle Bearings for Your Needs
Selecting the best needle bearing for your application requires evaluating several factors,
Load and Speed Requirements
One of the first things to consider when choosing needle bearings is how much load they need to handle and how fast they’ll be spinning. Why? Because the wrong choice here can lead to failure or shortened lifespan.
Radial and Axial Loads: Needle bearings are particularly suited for high radial loads. However, if your application involves significant axial forces, you might need an alternative bearing design. It’s always vital to match the bearing’s load capacity to the forces present.
Operating Speed: Bearings designed for high-speed applications differ in construction compared to those intended for slower operations. Faster speeds generate more friction and heat, so choosing a bearing built for high-speed rotations is critical in avoiding wear and damage.
For a more comprehensive guide on bearing design considerations, check out Bearing Design Fundamentals: A Complete Guide for Engineers. It offers insights tailored to varying load demands and speed factors.
Environmental Factors and Operating Conditions
The environment where the needle bearings operate is just as important as the loads and speeds. If the external conditions aren’t right, even the most durable bearing can fail prematurely. Here’s what to watch out for:
- Temperature Extremes: Bearings often operate in heat-intensive environments. Depending on the application, you may require bearings with heat-resistance coatings or specific materials to handle elevated temperatures.
- Moisture and Debris: In settings exposed to water or dust, you’ll want bearings with proper sealing to keep contaminants out. Open or shielded bearings, for instance, work better when immersed in fluids, whereas sealed designs offer better protection against grit.
For in-depth comparisons of bearing types based on environmental suitability, check out Sealed, Open and Shielded Bearings Comparison.
Lubrication and Maintenance Needs
Think of lubrication as the lifeline for your needle bearings. Without it, even the best-engineered bearing will face excessive wear and tear. But what kind of lubrication system do you need? And how often should you maintain it?
- Choosing the Right Lubricant: The type of lubricant—grease or oil—should match the application and environmental conditions. Bearings running at low speeds might do fine with standard grease, but high-speed applications may demand specialized lubricants.
- Routine Maintenance: Regular inspections for proper lubrication levels are non-negotiable. It helps to catch issues early, whether it’s low grease levels or contamination.
For strategies on maximizing lubrication efficiency, visit Understanding the Importance of Lubrication, which also shares best practices to make maintenance a breeze.
By considering these factors — load and speed, environmental conditions, and lubrication needs — you’ll be well-equipped to choose needle bearings that perform reliably and efficiently over time.
Common Issues and Maintenance Tips
Needle bearings are good options for ensuring the smooth operation of machinery and equipment
Identifying Wear and Failure Signs
Spotting issues early can save you a headache (and your budget) down the road. Needle bearings typically exhibit specific signs of wear or impending failure that, if left unnoticed, can escalate into larger system problems. So, what should you look out for?
1. Noise and Vibration: An unusual increase in noise or vibration is often an early indicator of wear. Bearings in good condition should operate quietly, so if you notice grinding or rattling sounds, it may signal improper alignment, insufficient lubrication, or surface wear.
2. Temperature Changes: Does the housing feel unusually warm during operation? Increased temperatures can signal friction due to wear or the breakdown of lubricant.
3. Visual Inspection: Regularly inspect your bearings for rust, pitting, or deformation. Discoloration in lubricant could also indicate contamination or elevated performance stress.
4. Load Inefficiency: A decline in performance, such as reduced carrying capacity or limited rotational speed, may point to internal bearing damage.
Routine checks and tools such as vibration monitors or temperature sensors can add an extra layer of confidence. For comprehensive guidance on preventing bearing failures, explore The Most Common Bearing Failures and How to Prevent Them.
Proper Lubrication for Longer Bearing Life
Think of lubrication as the heartbeat of your needle bearings — it keeps everything running smoothly. Without the right lubricant (or enough of it), friction and wear are inevitable. But it’s not just any lubricant that will do the trick.
- Lubricant Compatibility: Always use lubricants compatible with both your bearing materials and the operational environment. For instance, lithium-based grease is commonly used due to its versatility and long-lasting performance.
- Application Frequency: This depends on your equipment’s usage. High-speed applications often require periodic relubrication, while low-speed systems may sustain longer intervals.
- Signs of Lubricant Degradation: Be mindful of lubricant breakdown, often observed as a hardened, dry texture or leaking. Using degraded lubricant can cause more harm than good.
Tip: Follow recommended guidelines from the bearing manufacturer regarding the type and quantity of lubrication. Proactively managing this can significantly extend your bearing’s useful life span. Need tips on selecting the best lubricants? Visit Guide to Selecting the Right Grease for Ball and Roller Bearings.
Preventing Contamination and Premature Failure
Keeping your bearings clean is crucial — it’s the unsung hero behind their long service life. Contamination is a sneaky culprit that leads to premature wear, corrosion, and even catastrophic failure. Here’s how to avoid it:
1. Sealing Mechanisms: Use high-quality sealing solutions that block out dust, moisture, and debris. Double-sealed or shielded bearings are often more effective in harsh conditions.
2. Proper Handling: Mishandling during installation or maintenance introduces dirt and foreign particles. Always use clean, lint-free gloves and store bearings in their original packaging until use.
3. Regular Cleaning Protocols: When in doubt, wipe down and clean components before reinstallation. This simple step can prevent tiny particles from wreaking havoc.
Contaminants don’t just damage bearings — they also compromise performance, leading to unnecessary downtime. For a deeper dive into bearing best practices, explore Bearing Maintenance Guide, which covers essential steps to protect bearings from contamination and wear.
Taking a proactive approach to identifying wear, managing lubrication, and avoiding contamination ensures your needle bearings run efficiently for years. Use these tips as part of a regular maintenance routine, and you’ll thank yourself later.
Main industries and equipment in which needle roller bearings
Needle bearings such as Drawn Cup Needle Roller Bearings with Closed End, Drawn Cup Needle Roller Bearings with Open Ends, and Machined Needle Roller Bearing. Those with Aligning Needle Roller Bearings and Inner Rings are commonly used in the automotive industry, where they are used in transmissions, engines, and gearboxes. They are also used in the aerospace industry, where they are applied in aircraft engines and landing gear. In the industrial equipment industry, needle bearings are used in a wide range of applications, including printing presses, textile machinery, and machine tools.
Benefits and challenges of using needle bearings
The main benefit of using needle bearings is their high load-carrying capacity and ability to operate in tight spaces. However, they are more prone to wear and fatigue due to their high contact stresses. In applications where misalignment or shock loads are present, there may be better choices than needle bearings.
Installation and selection of needle bearings
Proper handling and storage of needle bearings are important to ensure their longevity and performance. Needle bearings should be stored in a clean and dry environment and should not be exposed to moisture or corrosive materials. During installation, it is important to ensure that the bearings are properly aligned and lubricated. The selection of the appropriate needle bearing for a specific application will depend on several factors, including the load requirements, operating conditions, and design envelope.
Frequently Asked Questions
Needle bearings may seem straightforward, but there are always common questions that arise when working with these essential machine components. Let’s tackle some of the most frequently asked questions about needle bearings to help you better understand their applications, maintenance, and design considerations.
Q: What is the primary purpose of needle bearings?
A: Needle bearings are designed to manage high radial loads while occupying minimal space within a system. Their slender, cylindrical rollers provide a larger surface area for evenly distributing stress and reducing wear caused by friction. This unique design makes them ideal for compact spaces where robust performance is still required, such as in gearboxes, engines, or power tools. For more details on their uses, explore Needle Roller Bearings.
Q: Can needle bearings handle axial loads?
A: Unlike ball bearings, needle bearings are primarily designed for radial loads. They offer limited capacity for axial (thrust) forces, so if your application requires support for both radial and axial loads, you’ll probably need a combination solution or a different bearing design entirely. For comparison, it’s useful to review the capabilities of related products in our bearing catalog.
Q: How do I maintain needle bearings to ensure longevity?
A: Maintenance is essential for keeping needle bearings in working order. Key steps include accurate lubrication with the right type of grease or oil, regular inspections to detect wear signs, and keeping contaminants out of the system. To implement better maintenance strategies, consider reading our detailed bearing maintenance guide.
Q: What are some telltale signs that needle bearings need to be replaced?
A: Over time, needle bearings can wear out due to constant use and environmental exposure. Warning signs include increased noise, vibration, overheating, or visible damage like rust or chipped rollers. Acting quickly when you detect these symptoms can prevent total system failure and downtime.
Q: How do I choose the right needle bearings for my application?
A: The selection process depends on key factors such as the kind of load (radial or axial), operating speeds, environmental conditions, and available space. Needle bearings come in various types, including drawn cup and machined variants, each suited to different needs. If guidance is required, take a look at our expertise in drawn cup needle roller bearings.
This FAQ section aims to clear up confusion and give you practical insights into working with needle bearings. Use this information as a foundation, and remember to reach out to professionals if detailed questions about your setup arise.
Conclusion
Needle bearings are a crucial component in industrial applications that require high radial load capacity within a limited space. By selecting the right type of needle bearing, handling, storing, and maintaining them correctly, you can ensure optimal performance and longevity of your machinery and equipment.