The development of bearings, bearing materials, and lubrication have taken place over centuries in incrementally small steps. A typical standard bearing has dimensions and ratings which are universal, while the ISO standards have created a worldwide commonality for design.
It is important to understand that basic bearing dimensions are time tested and manufacturers’ ratings for loads and speeds can be steadfastly relied upon for design purposes.
It would be most suggested to use a standard bearing when possible, to take advantage of the economy’s scales in manufacturing. As a rule, there are certain bearing sizes within a series of bearings where bearings are manufactured in such volume that the price should be a leading design consideration. For example, the 6200 series bearing part number 6203 has the dimensions of 17mmx40mmx12mm. The 6203 bearing is highly produced and is used in numerous applications making it an attractive candidate when designing. If your design can be accommodative, then you would choose this bearing over the nearly identical 6202 size measuring 15mmx35mmx11mm, which does not have the scale of production and cost advantages of using a 6203 bearing.
Types of Custom Bearings
While standard bearings offer cost-effective and reliable solutions for many applications, there are instances where unique requirements demand specialized designs. Custom bearings are engineered to meet these needs, providing tailored solutions for applications where standard bearings fall short. Below are the primary types of custom bearings, their unique features, and their most common applications.
Thin Section Bearings
Thin section bearings are designed to save space and reduce weight while maintaining high precision and load-carrying capacity. These bearings feature a small cross-sectional profile relative to their bore diameter, which makes them ideal for compact, high-performance applications.
Feature | Details |
Cross-section | Constant cross-section, even for varying bore sizes. |
Space efficiency | Ultra-thin design minimizes axial and radial dimensions. |
Material options | Stainless steel, chrome steel, and ceramics. |
Applications:
Thin section bearings are widely used in applications requiring compactness and precision. For instance, in robotics, these bearings allow for lightweight yet strong joints, reducing the overall payload and increasing operational efficiency. In medical equipment such as CT scanners, their low profile enables smooth and precise motion within limited spaces.
Large Diameter Bearings
Large diameter bearings are custom-designed for applications that require high load capacity, durability, and precision over a significant range of motion. These bearings can handle large axial, radial, and moment loads, making them ideal for heavy-duty and slow-rotating applications.
Feature | Details |
Size range | Diameters ranging from 12 inches (300mm) to several meters. |
Load capacity | High radial, axial, and moment load handling. |
Customization | Designed to exact specifications for fit and performance. |
Applications:
Large diameter bearings are frequently used in heavy industries such as renewable energy and construction. For example, wind turbines rely on these bearings to support the main rotor shaft and nacelle. Similarly, large slewing bearings are critical in cranes and excavators to ensure smooth rotation under massive loads.
High Precision Bearings
High precision bearings are engineered for applications demanding exceptional accuracy, low friction, and consistent performance at high speeds. These bearings are manufactured to strict tolerances (ABEC 5, ABEC 7, or higher), ensuring superior rotational accuracy.
Feature | Details |
Precision class | ABEC 5, ABEC 7, or ISO P4, P2 standards. |
Speed capability | Optimized for high-speed applications with minimal vibration. |
Material options | High-grade steel, ceramic, or hybrid materials. |
Applications:
High precision bearings are critical in machine tools like CNC spindles, where even the slightest deviation can compromise the final product’s quality. In aerospace systems, these bearings ensure smooth, reliable operation in actuators and control mechanisms at extreme speeds and conditions.
Specialty Bearings for Extreme Conditions
Specialty bearings are custom-designed to operate under extreme environmental conditions, such as high or low temperatures, corrosive environments, high contamination, or heavy shock loads. These bearings often feature specialized materials, coatings, and seals to enhance durability and longevity.
Feature | Details |
Temperature range | Can operate in temperatures ranging from -200°C to +400°C. |
Corrosion resistance | Special coatings (e.g., PTFE, chrome) and materials (e.g., stainless steel, ceramics). |
Vibration resistance | Designed to absorb extreme impacts and vibrations. |
Applications:
In the oil and gas industry, specialty bearings are used in pumps and drilling equipment, where they endure high pressures and exposure to corrosive substances. In cryogenic applications, such as liquefied natural gas (LNG) processing, bearings are designed to perform reliably at extremely low temperatures without failure.
Designs and applications of custom bearings
For bearings, it is a good idea to never attempt to change envelope dimensions due to the relationship between outer race, inner ring, and rolling elements. Centuries of development have proven the standard design to meet certain speed, load, and life results.
Certain applications and conditions will require the customizing of standard bearings, with the benefits for customizing bearings being to achieve optimal performance and life.
One of the most common changes or selections to customize bearings is to adjust the internal radial clearance. Clearance in the bearings can be changed in manufacturing to accommodate the designer’s requirement for fit and function.
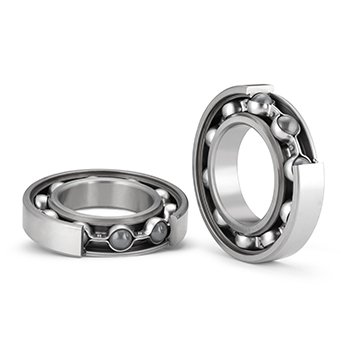
Changing ball size and number can be a practical way to increase load or increase speed depending on the direction of the sizing.
Lubrication is an area with major consequences to the user. Selecting the correct lubrication can increase life and functionality. The primary role of bearing lubrication is to place an oil film between all rolling or sliding surfaces. When customizing your bearing you will need to do research on the best lubrication for your application. Speed ratings are also affected by anywhere from 25-50% depending upon the lubrication selected.
Custom bearing design features can include changes to the raceway curvature, ball size and material, ring material, and ring design, which can include flanges and extended inner rings.
Sizes and materials
Custom bearings can be hybrid in design where the rings are usually manufactured from AISI 52100 chrome steel, or 440C stainless steel. In combination with these standard ring materials is the use of ceramic balls. There are many benefits in using Hybrid bearings, which include no or little lubrication, lighter weight, and higher speeds. Hybrid bearings are commonly used in machine tool spindles.
Hybrid bearing ceramic balls
In most instances, you will want to start your design using a standard bearing and then add or change elements to create the best solution for your application. Standard bearings can be improved to increase speed ratings by 10% when specifying ceramic balls. Another 10% can be achieved when increasing the precision rating. For machine tool bearings, increasing the precision from ABEC 7 to ABEC 9 is commonly done to increase the speed rating. Work with your supplier to help with these calculations.
How to Choose the Right Custom Bearing for Your Application
Standard bearings are suitable for many designs, custom bearings address specific requirements where precision, load capacity, or environmental conditions demand more specialized solutions. Below are key considerations and steps to guide you through the selection process.
The first step in choosing the right custom bearing is understanding the exact demands of your application. Consider factors such as load type and capacity (radial, axial, or moment loads), speed requirements, and the expected operating environment. For example, a high-speed spindle in a CNC machine requires bearings with minimal friction and exceptional precision, while a bearing for heavy-duty mining equipment must handle substantial loads and shock resistance.
Ask yourself the following:
- What types of loads will the bearing need to support?
- Will the application involve high speeds, oscillations, or frequent stops and starts?
- Are there extreme temperature or environmental conditions to consider?
These answers will provide a foundation for determining the right bearing design and specifications.
Environmental conditions, load capacity, and corrosion resistance needs should guide the selection of materials.
- Steel bearings: suitable for general applications where high strength and durability are required.
- Stainless steel bearings: preferred for corrosive environments, such as marine or chemical processing applications.
- Ceramic bearings: lightweight, resistant to corrosion, and ideal for high-speed and high-temperature applications.
- Hybrid bearings: a combination of steel races and ceramic balls, offering benefits like reduced friction and higher speed capability.
Selecting the right material ensures that the bearing will withstand the challenges of your application while minimizing maintenance needs.
With custom bearings, you have the flexibility to define dimensions and features that standard bearings may not offer. This includes:
- Bore size, outer diameter, and width that fit precisely into your design.
- Special profiles, such as thin-section or large-diameter bearings, where space or load constraints exist.
- Custom sealing solutions to prevent contamination in harsh environments.
- Lubrication options, include dry lubrication for extreme temperatures or food-safe grease for medical applications.
For applications like robotics, where weight reduction is essential, thin-section bearings with compact profiles are often the best choice. In contrast, large-diameter bearings may be necessary for heavy machinery.
Custom bearings must be designed to withstand the conditions they will face throughout their lifecycle. Analyze key environmental factors such as temperature, humidity, pressure, and potential exposure to contaminants. Bearings used in cryogenic conditions, for instance, need materials that remain stable at extremely low temperatures, while bearings in oil and gas applications require resistance to high pressure and corrosive chemicals.
FAQs About Custom and Special Dimension Bearings
Q: What are custom bearings, and when should they be used?
A: Custom bearings are specially designed to meet unique application requirements where standard bearings are insufficient. They are ideal for applications requiring specific dimensions, load capacities, or performance features, such as in aerospace, robotics, or extreme environmental conditions. PIB Sales works closely with manufacturers to deliver tailored bearing solutions that align perfectly with your design and operational needs.
Q: How do custom bearings differ from standard bearings?
A: While standard bearings are produced in high volumes with universal dimensions, custom bearings are engineered for specialized applications. They offer greater flexibility in size, material, and performance specifications. At PIB Sales, we help you determine whether a standard or custom bearing is the right solution based on your technical requirements and budget.
Q: What industries benefit the most from custom and special dimension bearings?
A: Custom bearings are widely used in industries such as aerospace, medical devices, robotics, automotive, and heavy machinery. For example, thin-section bearings are crucial in robotics for weight reduction, while large-diameter bearings excel in heavy construction equipment. PIB Sales provides bearings tailored to the unique demands of each industry.
Q: How do I determine the right custom bearing for my application?
A: The selection process involves evaluating load types, speed requirements, operating conditions (temperature, corrosion, vibration), and material suitability. PIB Sales offers expert guidance to help you navigate these factors and choose the ideal bearing solution for your application.
Q: Can PIB Sales assist with both design and sourcing of custom bearings?
A: Yes! PIB Sales collaborates with leading manufacturers to offer end-to-end solutions, including design support, prototyping, and sourcing of custom and special dimension bearings. Our team ensures you receive high-quality bearings that meet your exact specifications and performance standards.
Our team is here to help! Don’t hesitate to reach out if you’re looking for expert advice on custom bearings, need guidance selecting the right solution for your application, or want to explore our full range of products.
Contact us today to discuss your needs and find the perfect bearing solution!