Self aligning bearings are one of the unique types of bearings that have the ability to self adjust to accommodate changing conditions in an application. Separating themselves from other bearing types they are free from the normal rigidity of installed standard bearings.
Self-aligning bearings are a fully assembled double row set of balls accommodating misalignment during assembly and operation. The bearing’s outer ring has a concave raceway and an inner ring with a cylindrical or tapered bore. This type of bearing is available as open or with seals.
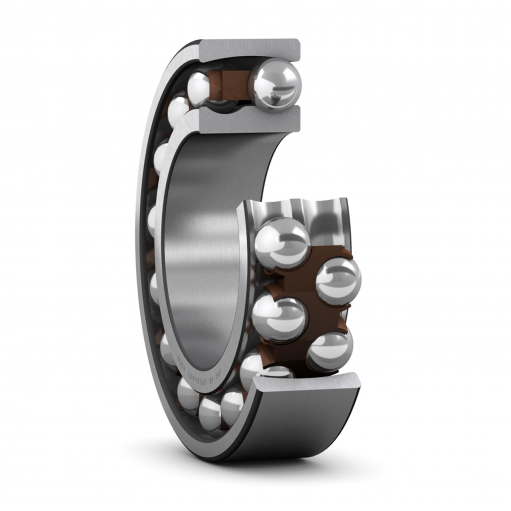
In applications with shaft deflection the angular misalignment feature allows for continued smooth operation as it is self adjusting. Self-aligning bearings are perfect for applications where shaft and or housing alignment is problematic.
Due to the outer rings spherical raceway and its center of curvature working along the axis of the inner ring, balls and cage free rotation occurs. Normally pressed steel cages are used but some manufacturers use polyamide or other materials. Due to the small contact angle self-aligning ball bearings have a low axial load capacity. Permissible dynamic misalignment is approximately 3 to 7 degrees under normal loads.
The main feature and benefit of self-aligning bearings include the ability to accommodate static and dynamic misalignment. Self-aligning bearings are excellent in high-speed circumstances and demonstrate excellent performance in these applications. Because self-aligning ball bearings generate less friction than any other type of rolling bearing this enables them to run cooler even at high speeds. With lower heat generation, the bearing temperature is lower leading to extended bearing life and longer maintenance intervals.
Loose conformity between balls and outer ring lowers friction and therefore frictional heat. Self-aligning ball bearings also have low minimum load requirements. Additionally they can reduce noise and vibration levels which is why they are often used in fans.
Precision self-aligning ball bearings are specified across a wide spectrum of applications, from automotive systems to heavy-duty industrial machinery.
SKF self-aligning ball bearings for the textile industry have the following features:
- Self-aligning up to a maximum of 3 degrees;
- No risk of sliding during start-ups and light- load conditions;
- Very low friction offers minimum operating temperature combined with high speed capability;
- SKF sealed versions provide robust protection in harsh environments;
- SKF E design bearings offer optimized internal geometry for maximum load capacity.
Textile Applications
- Spinning machines;
- Fabric processing machines.
SKF self-aligning bearings are designed to handle misalignment, contamination and high speeds. In spinning and fabric processing machines, ring frame shaft and guide roller bearings are exposed to dynamic misalignment. Surrounded by steam, water and chemicals many fabric widths force varying loads on roller shafts and bearings. These conditions will cause unplanned stops and breakdowns that negatively affect fabric quality.
SKF self-aligning ball bearings are ideally suited for textile processing as well as general industrial applications. SKF self-aligning ball bearings can accommodate a maximum of up to 3 degrees of misalignment without affecting performance. The SKF self-aligning bearings can easily manage uneven loading across the roller shaft width while maintaining low friction.
As I mentioned these bearings generate less frictional heat and the SKF self-aligning ball bearings will accommodate higher speeds as compared to other types of self-aligning rolling bearings. With very low minimum load requirement SKF has virtually eliminated sliding during start-up and light-load conditions. With the reduced risk of bearing damage comes improved reliability which in turn extends bearing service life and reduces maintenance costs.
Pacific International Bearing Sales offers SKF and FAG self aligning ball bearings from stock.

FAG self-aligning ball bearings are double row, self-retaining units composed of outer rings with a concave raceway, inner rings with a cylindrical or tapered bore and ball and cage. FAG self-aligning ball bearings are available in open and sealed designs.
Applications
Self-aligning bearing units are particularly recommended for their suitability in the following applications and industries:
- Handling and transport;
- Agricultural and agri-food machines;
- Textile machines;
- Fitness equipment;
- Car washes;
- Sawmills;
- Woodworking machines;
- Air conditioning and ventilation;
- Packaging, paper and cellulose processing;
- Gearboxes/speed reducers.
The versatility of self-aligning ball bearings translates into multiple use applications across various sectors:
- Automotive Industry. These bearings are used in automotive components such as steering systems, suspension assemblies, and gearbox applications, where misalignments and varying loads are prevalent.
- Mining and Construction. Self-aligning ball bearings find use in heavy-duty machinery employed in mining, construction, and excavation, where they endure challenging conditions and heavy loads.
- Textile Machinery. The ability to accommodate shaft misalignments makes these bearings suitable for textile machinery components, ensuring smooth operation even in high-speed spinning and weaving processes.
- Material Handling. Conveyor systems and material handling equipment benefit from the operational versatility and load-bearing capabilities of self-aligning ball bearings.
- Agriculture. In agricultural machinery like tractors and combines, where uneven terrains and abrupt movements are common, these bearings contribute to reliable performance and reduced maintenance requirements.
Characteristics of Electric Motor Bearings
Self-aligning ball bearings are specified for their unique ability to accommodate misalignment, making them a preferred choice for various electric motor applications.
Self Aligning bearings can support both radial and light axial loads. Their ability to accommodate misalignment makes them suitable for applications where shaft deflection or mounting errors are likely, ensuring reliable operation even in less-than-ideal conditions.
Self Aligning bearings are designed to operate at high speeds with minimal friction. The internal design allows smooth operation, which is essential for electric motors used in high-speed applications such as fans and compressors. The self-aligning feature helps maintain low friction and operational stability even when the shaft is misaligned.
The self-aligning feature helps to minimize noise and vibration caused by misalignment, making them ideal for applications where low noise levels are required, such as appliances and medical equipment. Precision machining and optimized internal geometry contribute to their low noise and vibration performance.
Self-aligning bearings can operate effectively over a wide range of temperatures. They are designed to handle the heat generated by electric motors and can operate in both low and high-temperature environments. The use of heat-resistant materials and proper lubrication ensures their performance and prevents thermal degradation.
Installation, Maintenance, and Troubleshooting Self-Aligning Ball Bearings
Following proper procedures for installation, maintenance, and monitoring of self-aligning ball bearings is important to ensure successful operation and long life. Neglecting these aspects can lead to premature failures, unexpected downtime, and compromised machinery efficiency. Therefore, adhering to established best practices is imperative to maximize the benefits of these bearings.
The optimization of lubrication is a fundamental consideration in enhancing bearing performance. Proper lubrication reduces friction, heat generation, and wear. The selection of lubricant, its viscosity, and replenishment intervals should be grounded in comprehensive tribological analyses. Inadequate lubrication alone is identified as a leading cause of approximately 36% of bearing failures.
Embracing advanced monitoring techniques, such as vibration analysis and thermography, facilitates early anomaly detection. This proactive approach has been proven to curtail maintenance costs by up to 50% and increase machinery uptime by almost 30%. By analyzing vibration patterns and temperature variations, incipient issues can be identified and addressed before they escalate into major problems.
Mitigating contamination is crucial to prolonging bearing life. Effective sealing mechanisms guard against the infiltration of contaminants and moisture, which can significantly accelerate wear rates. Furthermore, periodic visual inspections play a pivotal role in detecting wear, damage, or lubrication irregularities. Regular inspections have the potential to extend bearing service life by up to 2.5 times.
Conclusion
Self-aligning ball bearings are designed to accommodate angular misalignment between shafts and housing while still maintaining smooth operation. The fundamental design comprises two rows of balls, enabling them to operate with lower frictional resistance compared to other bearing types, resulting in reduced energy consumption and heat generation. The curvature of the inner and outer rings allows for the absorption of misalignment-induced stresses, enhancing the bearing’s longevity and reliability.
The use of self-aligning ball bearings in industrial applications is proven to enhance operational efficiency and extend bearing and machinery life. These bearings have been extensively utilized in various sectors including automotive, aerospace, and manufacturing due to their ability to sustain radial and axial loads simultaneously. Moreover, self-aligning ball bearings exhibit a self-correcting mechanism when subjected to shaft deflections or housing misalignments, mitigating the risk of catastrophic failure. This feature is attributed to the geometry of the bearing’s raceways and the distribution of contact points between the balls and raceways.
Advancements in bearing materials led to the development of self-aligning ball bearings with enhanced fatigue and corrosion resistance. The utilization of specialized steels and advanced heat treatment processes has further improved the bearing’s performance under extreme operating conditions. Using computational methods, such as finite element analysis, has provided deeper insights into the stress distribution and load-bearing capabilities of self-aligning ball bearings, aiding in their optimal integration into complex mechanical systems.
Still have questions or want to discuss something? Please Contact us at [email protected].