Loads affecting bearings include force exerted by the weight of the object the bearings support, transmission force of devices such as gears and belts, loads generated in equipment during operation, etc. Rarely can these kinds of loads be determined by simple calculations. As the load is not always constant and the load fluctuates in many cases, it is difficult to determine the frequency and magnitude of the fluctuation.
Radial vs. Axial Loads on Bearings – What’s the Difference?
Bearings play an important role in machinery operation by supporting shafts and guiding, rotating, or oscillating around shafts while minimizing friction. To ensure the optimal performance and life of machinery components, you must understand the forces affecting bearings as either pure radial, pure axial, or a combined radial and axial load.
Radial loads act perpendicular to the shaft. Most standard single-row radial bearings are selected for their use in applications that have primarily radial loads.
Radial Load | Axial Load |
Force acts perpendicular to the shaft’s axis. | Force acts parallel to the shaft’s axis (also known as a thrust load). |
Handled primarily by standard single-row radial bearings (designed mainly for radial forces). | Handled by thrust bearings (designed specifically for axial forces). |
Common in supporting rotating shafts – for example, the weight of gears or tension from belts creates radial forces on bearings. | Common in applications with load along the shaft – for example, a jack screw or helical gear can impose an axial (thrust) force through the bearing. |
Bearing catalogs base load ratings on radial loads, since most applications involve primarily radial force. | Axial loads often must be converted to an equivalent radial load for bearing selection, or require specialized thrust bearings if dominant. |
Axial loads act parallel to the shaft’s axis. Thrust bearings are selected for applications with only axial loads.
It is essential to consult with your supplier or look up the load ratings in manufacturers catalogs to determine the most suitable bearing. Accurate calculations of these forces are essential in choosing the right bearing type and ensuring its efficiency and life.
- Dynamic Load Capacity is defined as the constant stationary radial load at which a rolling bearing can theoretically last with a basic rating life of one million revolutions.
- Static Load Capacity: Shown in manufacturers catalogs as the maximum load a bearing can withstand without any permanent deformation while stationary. Exceeding the manufacturers catalog specifications may lead to material fatigue and eventual bearing failure. This specification is typically designated as the symbol C0 and is measured in units of force, such as Newtons (N).
A basic fatigue life rating known as L10 is a bearing’s basic fatigue life rating and is calculated using the number of rotations in which 90% of all bearings in a specific group achieve or exceed a calculated time without failure (probability of failure: 10%).
Find your bearing’s dynamic capacity in the catalog, estimate the radial load and RPM, and you can calculate your own L10 bearing life. The L10 life calculation indicates the life of the bearing in your operating conditions with 90% accuracy.
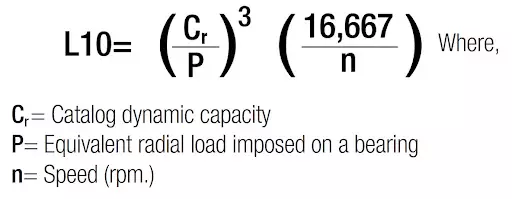
Therefore, loads are normally obtained by multiplying theoretical values by various coefficients developed over time.
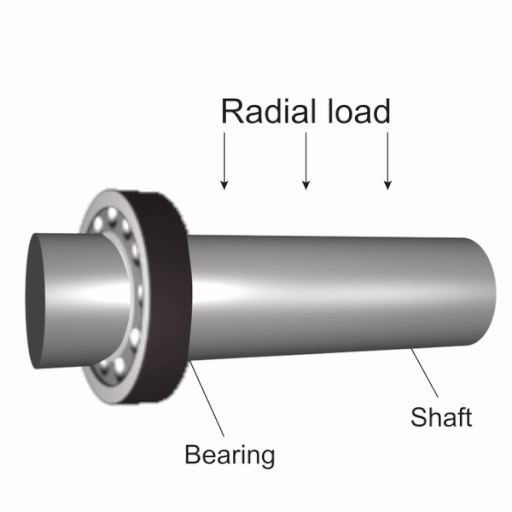
There is a lot of math involved, but you can find this information on many manufacturers’ sites.
How to Calculate Bearing Loads
The Computation of Bearing Loads is simplified as follows:
- R= Radial load – loads that are perpendicular to the shaft
- T= Thrust load – loads that are parallel to the axis of the bearing
- C= Combined load is a result of calculating both Radial and Thrust loads using the combined load calculations
To calculate the dynamic equivalent radial load (composed of both radial and axial forces) for a single row deep groove ball bearing, it is as follows:
P= XFr + YFa
Symbol | Actual axial (thrust) load on the bearing |
---|---|
P | Dynamic equivalent radial load |
Fr | The factor defining when axial load needs consideration (from the catalog) |
Fa | Actual radial load on the bearing |
X | Radial load factor (from bearing catalog) |
Y | Thrust load factor (from bearing catalog) |
e | Factor defining when axial load needs consideration (from catalog) |
The static equivalent radial load on single-row deep groove bearings subject to both radial and axial (thrust) loads is computed as follows:
Po=0.6 Fr +0.5 Fa
- Po=Static equivalent load
- Fr=Radial load
- Fa=Axial load
Kaydon bearing load scenarios
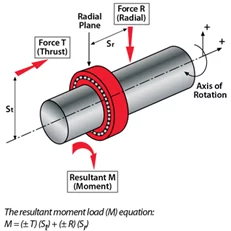
Common Sources of Loads are:
- Weight- shafts, gears, pulleys, or other machine parts supported by bearings
- Centrifugal Force – out of balance conditions-eccentrics, or as in wheel bearings while turning curves
- Tension – required to transmit power, as in timing or drive belts
- Torque Reaction – producing loads due to the twisting effect of power input, on bearings supporting the drive pinion or worm gear, etc.
Effect of Bearing Location on Load Distribution
A shaft is ordinarily supported by two bearings:
With (1) Load (L) applied between the two bearings perpendicular to the shaft
Or (2) Load applied parallel to the shaft, or both bearings will be designed based on the magnitude of load, the distance between bearing centers, and the point of application.
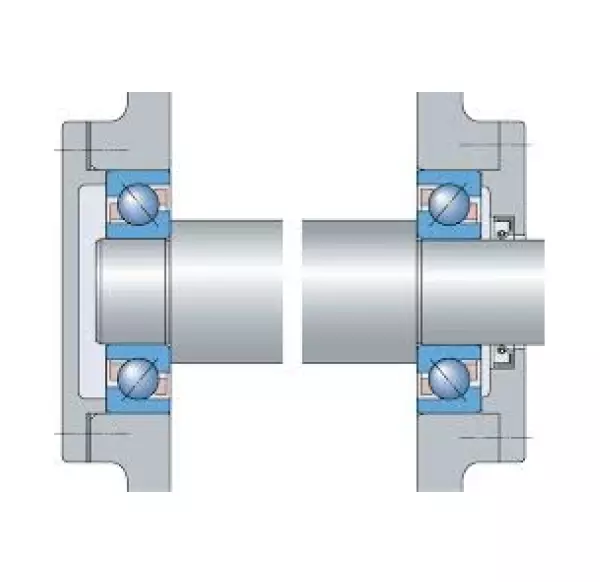
The first step in calculating bearing loads is therefore the computation of (L) from available data and the determination of bearing center distances. In the majority of cases, the applied load is the result of mechanical forces so large in comparison to the actual weight of the parts that the latter may be ignored.
In many cases, the heavy rotating parts likely constitute a large part of the load.
Torque from Horsepower input. Most bearing load calculations require the determination of torque or twisting moment due to the input of horsepower at a known speed.
Power transmission losses are present depending on the efficiencies of the elements involved. However, in the methods of calculations, the efficiency of 100% is used in order to keep the solutions as simple and direct as possible. Contact Us for further assistance.
Frequently Asked Questions
Q: What is the difference between radial load and axial load on a bearing?
A: Radial load is a force perpendicular to the shaft (sideways load on the bearing), while axial load (thrust load) is a force parallel to the shaft (pushing along the axis). Many applications involve both simultaneously.
Q: How do I calculate the load on a bearing?
A: To calculate a bearing’s load, first determine all external forces on it (weight, belt/gear forces, etc.), separate them into radial and axial components, then use the bearing’s equivalent load formula (P = X·Fr + Y·Fa) to find the combined effect. This tells you the effective load to compare against the bearing’s capacity.
Q: What is the dynamic load capacity in bearings?
A: It’s the constant radial load a bearing can theoretically endure for 1e6 revolutions (the baseline life). It indicates the bearing’s load rating under dynamic conditions.
Q: What is L10 bearing life?
A: L10 life is the number of revolutions (or hours at a given speed) that 90% of identical bearings will complete without failure under a given load. It’s a standard measure to estimate bearing longevity.