Precision bearings are necessary to ensure high performance in robotic systems. This article discusses various precision bearing types as they might be applied in robotic applications.
What is a precision bearing?
Precision bearings have specific high tolerances and are designed to support rotational or linear movement, reducing friction and handling high loads and speeds with extreme accuracy.
High precision bearings are different from standard bearings due to tighter tolerances and more controlled runouts. In addition to closer tolerances, the use of materials such as ceramics and highly specialized steel allows higher precision bearings the ability to operate at higher speeds, carry more load, and do so with minimal noise and vibration.
The demand for precision movements in robotics is essential for overall accurate performance. Misalignments and vibration can lead to significant errors — making precision bearing selection so very important in this application.
Super high precision bearings are manufactured to exacting standards for:
- Ultra-high Rotational Speeds.
- Exceptional Accuracy and Stability.
- Extremely tight tolerances, ensure consistent and reliable performance. High accuracy is vital in applications where precision is non-negotiable, such as surgical robots or precision measuring instruments.
- Low Noise and Vibration. Super precision bearings are engineered to minimize noise and vibration levels, a critical feature in sensitive applications like high-speed imaging equipment or semiconductor manufacturing.
Super high precision ball bearings can sustain higher rotational speeds than standard precision bearings, which is crucial in applications like high-speed spindle operations in CNC machinery or robotics.
Precision Bearing Products
Pacific International Bearings Sales offers a wide range of bearings catered specifically for robotic applications.
Examples of bearing types use in robotics:
Precision Cylindrical Roller Bearings
Key Features: These bearings are known for their high radial load capacity and moderate thrust capabilities. They are typically designed with precision in terms of roller and raceway contact.
Applications: Commonly used in machine tool spindles, these bearings are ideal for high-speed, high-precision applications due to their ability to maintain rigidity and accuracy under heavy radial loads.
Precision Angular Contact Ball Bearings
Key Features: These bearings have raceways in the inner and outer rings that are displaced relative to each other in the direction of the bearing axis. This design enables them to handle combined loads (both radial and axial) and work at high speeds.
Applications: Widely used in precision applications such as high-speed spindles in machining centers, robotics, and high-precision machinery.
Super Precision (Spindle) Bearings
Key Features: Designed for ultra-high-speed and precision applications, these bearings offer superior accuracy and are manufactured to incredibly tight tolerances. They often feature unique designs to minimize friction and heat generation.
Applications: Ideal for machine tool spindles, high-frequency motors, and other high-speed precision applications.
High Precision Tapered Roller Bearings
Key Features: These bearings are designed to handle large radial and thrust loads. The tapered design allows for the bearing to handle a combination of forces.
Applications: Common in precision rotating assemblies in industries like aerospace, where load handling and performance are crucial.
Precision Spherical Roller Bearings
Key Features: Characterized by barrel-shaped rollers, these bearings are designed to manage high radial loads and moderate axial loads while compensating for misalignments.
Learn more – PIB Sales online shop.
Applications: Used in applications where there are severe misalignment issues or where shaft deflection is expected, such as in heavy-duty machinery.
Precision Needle Roller Bearings
Key Features: These are compact bearings with high load capacity and high rigidity. They are characterized by cylindrical rollers with small diameters to their length.
Applications: Ideal for applications with limited radial space and high load requirements, such as in automotive and industrial machinery.
Spherical Plain Bearings
Key Features: Spherical plain bearings accommodate a wide range of motion and can handle both radial and axial loads. They are designed to provide high wear resistance and low maintenance.
Applications: Often used in applications requiring oscillating or rotating movements, such as articulated joints in robotic systems.
Kaydon Reali Slim bearings
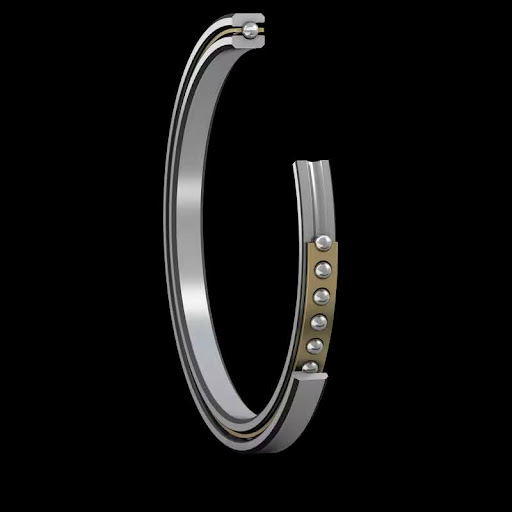
Kaydon is the premier bearing manufacturer of thin section bearings widely used in Robotic applications. Kaydon bearings are designed to solve highly demanding robotic applications.
Reali-Slim® thin section bearings
Kaydon thin section bearings are designed to save weight, use less space, reduce friction, increase design flexibility, and provide high running accuracy.
Kaydon bearings are widely used in aerospace, robotics, semiconductor, industrial machinery, machine tools, and medical devices Here is a list of popular Kaydon bearings used in robotics applications.
To buy Kaydon bearings go to:
Kaydon products
Custom-Specialized Robotics Bearings and Components
Schaeffler Bearing Company has the most extensive portfolio of bearings and components for robotics. Schaeffler offers a precision strain wave gear series for classical and lightweight robots, with a torque sensor integrated into the strain wave gearing. Schaeffler also offers the PSC series (the “P” stands for “precise,” the “S” for “silent,” and the “C” for “constant,” marking a constant level of precision) of precision robotics. These bearings are often custom-designed for specific robotic applications, emphasizing precision, reliability, and reduced maintenance.
Applications: Used in various parts of robotic systems, including arms, joints, and rotating platforms, where precision and reliability are critical.
Read the article Custom Bearings and Special dimension bearings
FAQ
Q: What are the key factors to consider when selecting bearings for robotic applications?
A: When selecting bearings for robotics, consider factors like load capacity, precision, speed requirements, environmental conditions, and space constraints. The choice of bearing directly affects the robot’s performance, durability, and maintenance needs.
Q: How do precision bearings improve the performance of robots?
A: Precision bearings enhance robot performance by providing high accuracy, reduced friction, and stability, crucial for tasks requiring meticulous control and repeatability. They ensure smooth and precise motion, which is essential in robotics.
Q: What makes super precision bearings different from standard bearings?
A: Super precision bearings are designed for ultra-high-speed and precision applications, with tighter tolerances, superior accuracy, and the ability to handle higher loads and speeds. They minimize noise and vibration, which is critical in high-precision robotic applications.
Q: Can precision bearings operate in extreme environments?
A: Yes, certain precision bearings are designed to operate in extreme environments. They can be engineered to withstand high temperatures, corrosive substances, and other challenging conditions, making them suitable for a wide range of robotic applications.
Q: Are there specific types of bearings recommended for robotic arm applications?
A: For robotic arms, angular contact ball bearings and precision cylindrical roller bearings are commonly recommended due to their ability to handle both radial and axial loads efficiently and provide high levels of precision and rigidity.
Q: How does bearing size impact a robot’s design and functionality?
A: Bearing size can significantly impact a robot’s design and functionality. Larger bearings typically handle higher loads but may require more space, while compact bearings are suited for smaller robots or those with limited space but might have lower load capacities.
Q: What is the importance of maintenance for precision bearings in robotics?
A: Regular maintenance of precision bearings is crucial in robotics to ensure optimal performance and longevity. Proper maintenance involves regular lubrication, cleaning, and inspection for wear or damage, which helps prevent failures and prolongs the bearing’s life.
When choosing bearings for robotic applications where high precision is required there are many choices for precision and materials to obtain the best results. PIB offers not only bearings but through its relationship with Schaeffler Bearing and other manufacturers like Kaydon, RBC, SKF, and INA, Pacific International Bearing offers much more than just rolling bearings. PIB is your strategic partner for robotic system components, precision gearboxes, pivot bearing supports, drive motors, and sensors.
For more information go to [email protected] or visit www.pibsales.com