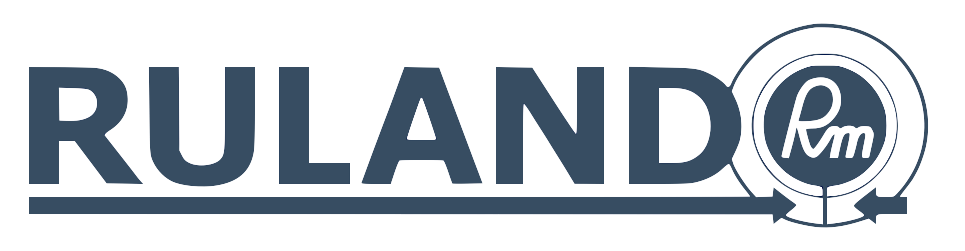
Oldham couplings from Ruland Manufacturing are three-piece precision couplings consisting of two metallic hubs and a center disk insert. This unique design provides a zero-backlash transmission when using an acetal (plastic) disk, meaning no play or lost motion – a critical feature for precise conveyor indexing and positioning.
Overview: Oldham Couplings for Conveyor Applications
Oldham couplings from Ruland Manufacturing have a balanced construction that minimizes vibration at high speeds, making them ideal for motors driving conveyor rollers. Oldham couplings excel at handling parallel misalignment between shafts, a common scenario in conveyor systems due to frame tolerances or thermal expansion.
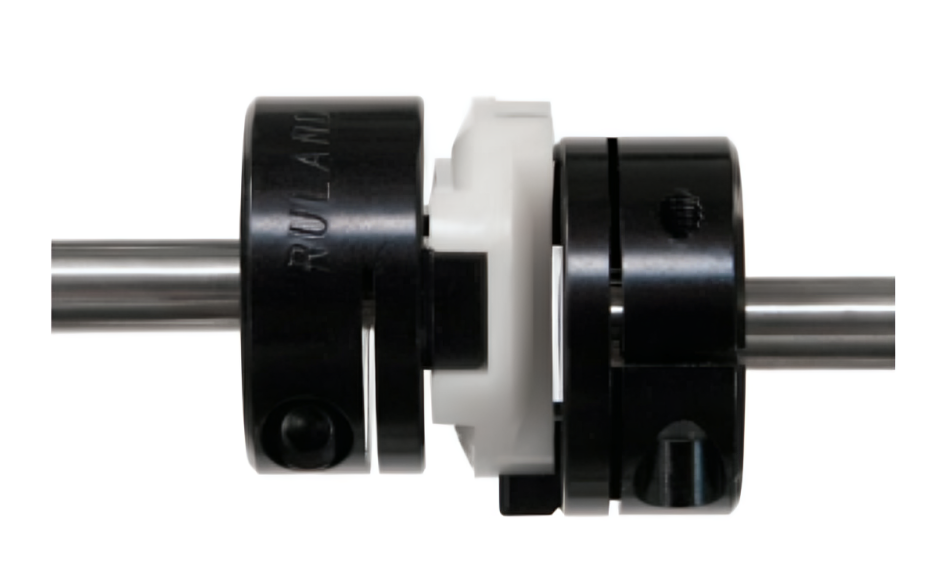
They can accommodate relatively large parallel offsets (up to ~10% of the coupling’s outer diameter) without imposing high loads on bearings. This protects conveyor motors and bearings from premature wear. Additionally, Ruland’s Oldham design makes maintenance straightforward – the couplings easily disassemble, allowing quick removal of conveyor rollers for cleaning or replacement. Overall, Ruland’s Oldham couplings are a versatile, reliable solution for industrial and packaging conveyors that require precise motion control and easy maintenance.
Technical Benefits of Ruland Oldham Couplings in Conveyor Systems
Ruland’s Oldham couplings offer several technical advantages that provide clear value in conveyor applications:
- Zero backlash & accurate motion
With an acetal center disk, Oldham couplings operate with virtually zero backlash. This means conveyors that rely on accurate indexing (for example, in packaging or sorting) benefit from precise, repeatable motion without lag or slop. The constant velocity transmission of Oldham couplings ensures timing between a conveyor drive motor and roller is maintained without oscillation or wind-up.
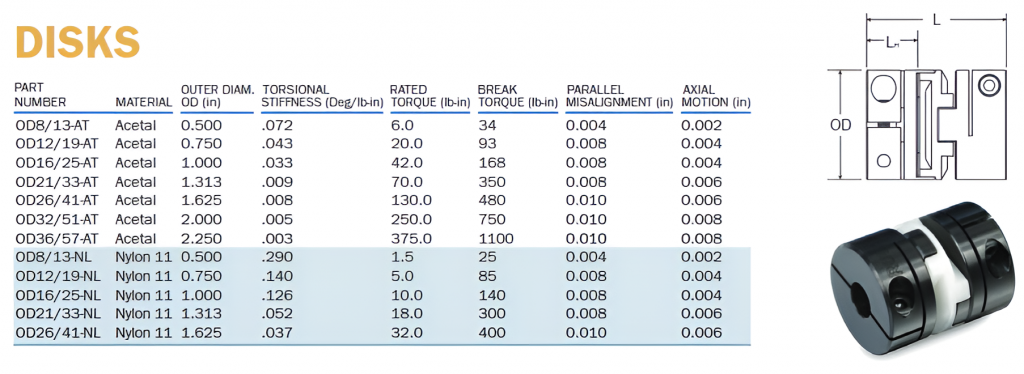
- High misalignment tolerance & low bearing stress
Oldham couplings are especially suited for parallel misalignment, where the two shafts are offset laterally. They can tolerate much more misalignment than most other coupling types – often up to 0.010 inches or more in larger sizes (roughly 5–10% of the coupling diameter). Because the disk “floats” between the hubs and slides to accommodate offset, the coupling imposes minimal reaction forces.
This results in low bearing loads, protecting conveyor shaft bearings and motor mounts from excessive stress. Small angular misalignments (up to about 0.5°) and a limited amount of axial motion are also handled by the Oldham’s flexible design, which is beneficial for conveyors with slight shaft angle errors or thermal expansion in shafts.
- Vibration damping and shock absorption
The center disk is available in multiple materials, allowing the user to tailor the coupling’s response to vibration. An acetal (hard plastic) disk provides high torsional stiffness for best accuracy, while a nylon disk is softer and excellent for damping vibrations and absorbing shock. In conveyor systems that start and stop frequently or handle irregular loads, a nylon disk can reduce shock transmitted to the motor, contributing to smoother operation and longer component life. The Oldham’s inherently balanced, three-piece design also means it runs with reduced vibration even at speeds up to 6,000 RPM (well above typical conveyor motor speeds).
- Electrical isolation & fail-safe protection
Because the disk insert is non-metallic (plastic), Ruland Oldham couplings electrically isolate the two hubs. This is an advantage in conveyor setups where you want to prevent electrical currents from passing from the motor to the driven shaft (for instance, to protect sensitive sensors or eliminate grounding loops).
Moreover, the plastic disk serves as a mechanical fuse: if the torque exceeds the coupling’s capacity or a jam occurs, the disk will shear cleanly and disengage power transmission. This fail-safe action can prevent damage to more expensive conveyor components (gearboxes, motors) in the event of an overload. Replacing the disk is quick and much cheaper than replacing an entire coupling or motor shaft – in most cases, a fresh insert restores the coupling to full performance immediately.
- Easy maintenance & versatile assembly
Oldham couplings facilitate easy disassembly, which is a significant benefit for conveyors that require routine roller maintenance or quick changeovers. The two hubs can be separated by sliding the disk out, allowing operators to remove conveyor rollers or motors without completely uninstalling the hubs from their shafts. In addition, Ruland’s Oldham hubs are designed with a proprietary machining process that yields an exceptionally smooth hub-to-disk interface.
This precision results in longer coupling life and reduced downtime since the disk and hubs wear more slowly and uniformly. Overall, the coupling’s modular nature (two hubs + one disk) makes it easy to mix and match components: users can combine clamp-style and set-screw-style hubs, use different bore sizes (even mix inch and metric bores), or accommodate keyed shafts by selecting the appropriate hub types.
Oldham Coupling Part Numbers and Specifications
Ruland manufactures Oldham coupling hubs in a range of sizes and configurations to suit various conveyor system requirements. Hubs are typically made from high-strength aluminum with a black anodized finish (for low inertia and corrosion resistance), but stainless steel hubs are available for washdown or food processing environments. Hub styles include clamp type (for easy installation and even holding pressure) and set screw type (for compactness or when a shaft keyway is used).
Keyed versions of each style are offered for shafts with keyways (e.g. part numbers beginning with “OCC” for clamp keyed, “OSC” for set screw keyed), while standard non-keyed versions begin with “OCT” (clamp, no key) or “OST” (set screw, no key). All hub part numbers include the coupling series (indicating the outer diameter), the bore size, and a material code (e.g., “-A” for aluminum).
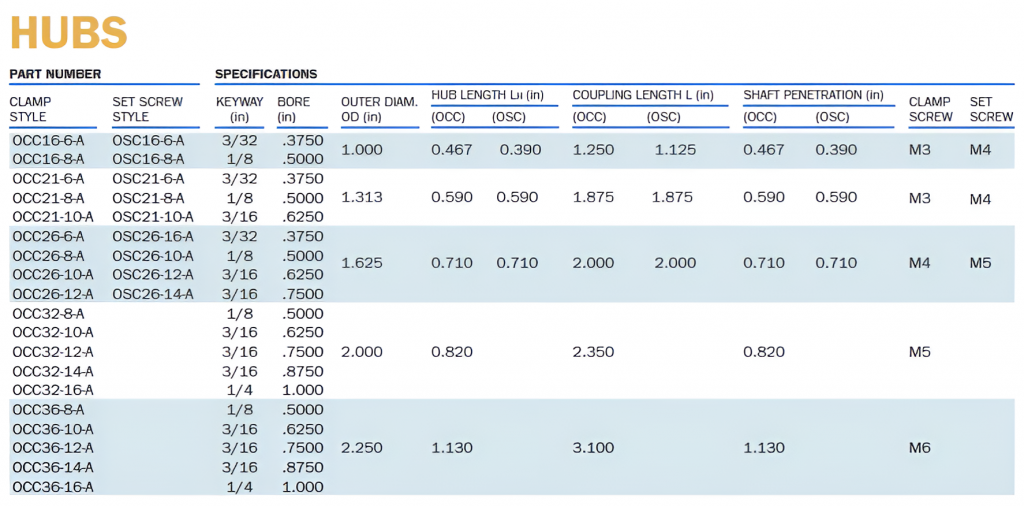
A complete Oldham coupling assembly consists of two hubs and one disk insert. For proper function, both hubs should be the same series (same outer diameter) so that they mate with the corresponding disk. The disk part number will indicate the same outer diameter. Below is an overview of Ruland’s standard inch-dimension Oldham coupling hubs (aluminum, without keyway), showing available bore size ranges for each coupling size:
For each coupling size, Ruland provides matching disk inserts in multiple materials. The disk part number is designated by “OD” followed by the coupling OD in fractional inch (or a paired metric size), plus a material code. The standard material options are: acetal (code “AT”) for high torsional stiffness and zero-backlash operation, nylon (code “NL”) for vibration damping and shock absorption, and PEEK (code “PEK”) for high temperature and low outgassing applications.
All disk materials are plastic (thermoplastic), which inherently provides electrical isolation between the hubs. Table 2 below summarizes the key performance specifications of the disk inserts for each coupling size.
Coupling OD (inch) | Disk Part Number (Acetal) | Rated Torque (lb·in, Acetal) | Disk Part Number (Nylon) | Rated Torque (lb·in, Nylon) | Max Parallel Misalignment‡ (in) |
0.500″ | OD8/13-AT | 6.0 lb·in | OD8/13-NL | 1.5 lb·in | 0.004″ |
0.750″ | OD12/19-AT | 20.0 lb·in | OD12/19-NL | 5.0 lb·in | 0.008″ |
1.000″ | OD16/25-AT | 42.0 lb·in | OD16/25-NL | 10.0 lb·in | 0.008″ |
1.313″ | OD21/33-AT | 70.0 lb·in | OD21/33-NL | 18.0 lb·in | 0.008″ |
1.625″ | OD26/41-AT | 130.0 lb·in | OD26/41-NL | 32.0 lb·in | 0.010″ |
2.000″ | OD32/51-AT | 250.0 lb·in | (not offered in nylon) | – | 0.010″ |
2.250″ | OD36/57-AT | 375.0 lb·in | (not offered in nylon) | – | 0.010″ |
Oldham coupling disk inserts and their approximate rated torque capacities. “Rated” torque is the recommended continuous torque limit for each disk material. (The disks typically shear at roughly 4–6× this torque as a safety measure.) Acetal disks provide higher torque capacity and zero backlash operation; nylon disks have lower torque capacity but add compliance for shock loads and noise reduction. PEEK disks (not shown in table) have torque ratings similar to acetal disks of the same size, but are formulated for use in high-temperature environments (up to ~300°F) and cleanrooms. ‡ Max parallel misalignment is the maximum offset of shaft axes that the coupling can accommodate (values are from Ruland’s specifications for each size; angular misalignment up to 0.5° is also tolerance.
We see that the torque capacities of Ruland Oldham couplings cover a broad range – from ~6 lb·in for the smallest size (suitable for light-duty conveyor or encoder drives) up to ~130 lb·in (acetal) for mid-size couplings and even 375 lb·in for the largest standard size. This range can cover everything from small motorized conveyor belts in packaging machines to larger material-handling conveyors.
Axial motion (end-play) capacity is also provided by the coupling (typically a few thousandths of an inch, as seen in the table for each size), which can accommodate thermal expansion or slight spacing variations between conveyor components. All Ruland Oldham couplings are designed for speeds up to at least 4,500 RPM (with many up to 6,000 RPM), well above the regime of most conveyor drives.
In summary, Ruland’s Oldham coupling part numbering and specs allow engineers and procurement professionals to easily select the right coupling for their conveyor system. One can choose the appropriate size based on required torque and shaft diameters, then pick hub styles (clamp or set screw, keyed or keyless) and disk material to match the application’s needs (precision vs damping, standard vs high temperature).
The modular system means nearly any combination is possible – for example, a designer could use one clamp hub and one set-screw hub in the same coupling to interface a keyed motor shaft to an unkeyed roller shaft, mixing inch and metric bores if necessary. This flexibility and the clearly defined part number system streamline the specification and purchasing process for conveyor couplings.
Competitive Advantages of Ruland Oldham Couplings vs. Other Couplings
When comparing coupling solutions for conveyor drive systems, Ruland’s Oldham couplings have distinct advantages over other common coupling types:
Oldham vs. Jaw Couplings
Jaw couplings (elastomer “spider” couplings) are widely used in industrial power transmission due to their simplicity and low cost. However, standard jaw couplings can introduce backlash and do not handle parallel misalignment as effectively. Ruland Oldham couplings, in contrast, are zero-backlash when equipped with an acetal disk, which is crucial for accurate conveyor positioning. In terms of misalignment, a jaw coupling’s elastomer spider mainly compensates for angular misalignment and a small amount of parallel offset, but larger parallel misalignments will significantly compress the spider and increase bearing loads. Oldham couplings excel in parallel misalignment scenarios, sliding without substantial restorative force.
Moreover, when a jaw coupling’s spider fails or wears out, the metal hubs can contact with each other – often resulting in sudden failure or damage. In Ruland’s Oldham design, if the disk insert fails, the hubs decouple (no metal-to-metal contact), acting as a mechanical fuse that protects the rest of the machine. Replacing an Oldham disk is also simpler in many cases (just sliding out the old disk and inserting a new one) compared to replacing a jaw spider, which may require moving one or both hubs off the shafts.
Oldham vs. Beam Couplings
Beam couplings (helical one-piece couplings) are another option often seen in light-duty conveyor or encoder drives. Beam couplings are zero-backlash and flexible, but they achieve misalignment accommodation by bending, which can introduce significant bearing loads under offset conditions.
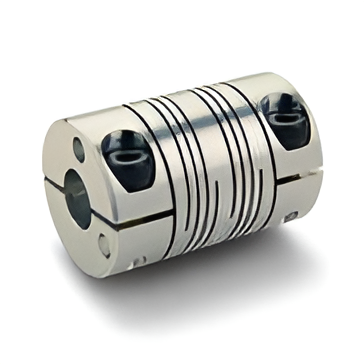
They typically handle only modest parallel misalignment (a few thousandths of an inch) before the restoring forces climb sharply. Oldham couplings provide a far greater parallel misalignment capacity (as noted, up to 0.010″ or more) with minimal bearing stress, making them better suited for applications where shafts are not perfectly colinear.
Beam couplings also have lower torque capacity for a given size and can act like a spring (torsionally soft), whereas Oldham couplings with acetal disks have a higher torsional stiffness for precise motion control. In short, beam couplings might suffice for very small conveyors or instrumentation, but for higher loads or misalignment, Oldham couplings offer more robust performance.
Oldham vs. Disc Couplings
Disc couplings (flexible metal disc pack couplings) provide zero backlash and high torsional rigidity, often used in servomotor applications. Compared to disc couplings, Oldham couplings have the advantage in misalignment capability and ease of maintenance. A steel disc pack coupling tolerates only minimal parallel misalignment (it primarily flexes in bending for angular offset), whereas an Oldham can handle substantially more offset by design.
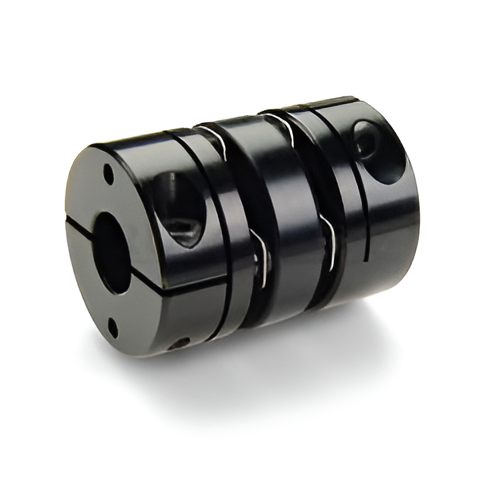
If a disc coupling is misaligned beyond its small limit, the thin metal discs can fatigue and crack, requiring full replacement of the coupling or disc pack. Oldham couplings have a forgiving nature – the plastic element wears gradually and can be replaced at a low cost during scheduled maintenance without replacing the hubs.
Additionally, Oldham couplings introduce some damping due to the plastic element (especially with nylon), which can be beneficial in reducing resonance in conveyor drives. Disc couplings, being all-metal, have no damping (which can lead to vibration issues in some setups). While disc couplings might handle higher speeds or torques in certain high-end servo conveyors, Ruland’s Oldham couplings cover a wide range of medium to high torque needs and do so with more misalignment tolerance, often at a more economical price point.
Oldham vs. Rigid Couplings
Rigid couplings simply clamp two shafts together with no allowance for misalignment. These are generally not recommended for motor-to-roller connections in conveyors (except in the rare case of perfect alignment) because any misalignment will cause binding, excessive wear, or bending of shafts.
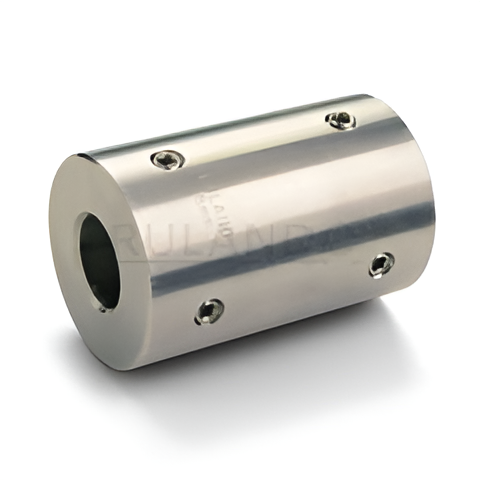
The Oldham coupling’s flexible disk eliminates these issues by compensating for misalignment, greatly reducing maintenance headaches and the need for precision alignment during installation. In essence, using a rigid coupling on a conveyor drive requires near-perfect alignment; using an Oldham coupling provides forgiveness for alignment errors and dynamic movement while still transmitting torque accurately.
Ruland’s Oldham couplings combine many of the best attributes needed for conveyor drive applications: the precision of a zero-backlash coupling, the flexibility to handle misalignment like a beam or jaw coupling (but with much lower stress), and a fail-safe element that protects your equipment. This blend of features often makes Oldham couplings the preferred choice for engineers looking to maximize reliability and performance in conveyor systems.
How to Purchase Ruland Oldham Couplings through PIB Sales
As an engineering or procurement professional, once you’ve identified the suitable Oldham coupling for your conveyor system, the next step is to source it efficiently. PIB Sales is a trusted supplier of Ruland Manufacturing products and can help you secure the exact Oldham coupling components you need. We recommend the following process to streamline your purchase:
Contact PIB Sales with your application details – our experts can verify the coupling size, hub style, bore dimensions, and disk material that best fit your conveyor requirements. Whether you need a standard aluminum Oldham coupling for a packaging conveyor or a stainless steel version with a PEEK insert for a washdown food conveyor, PIB Sales will ensure you get the correct Ruland part numbers.
PIB Sales will provide a prompt quote, including pricing and lead times. Ruland’s couplings are high-quality components made in the USA, and common sizes/styles are typically in stock for fast shipment. PIB maintains a large inventory, minimizing wait times for our customers. Any customization (such as special bore sizes or keyways) can be discussed and arranged during this stage.
Once you place your order, PIB Sales will coordinate the fulfillment. Thanks to our efficient logistics, you can expect quick delivery so that your conveyor downtime is minimized. We also offer support with any documentation needed (spec sheets, RoHS compliance info, etc.) for your records.
Contact PIB Sales today to request a quote or to discuss your application with our engineering team. We are ready to assist you in selecting and purchasing the ideal Oldham coupling solution. Contact us at [email protected] .