What Are Open Bearings?
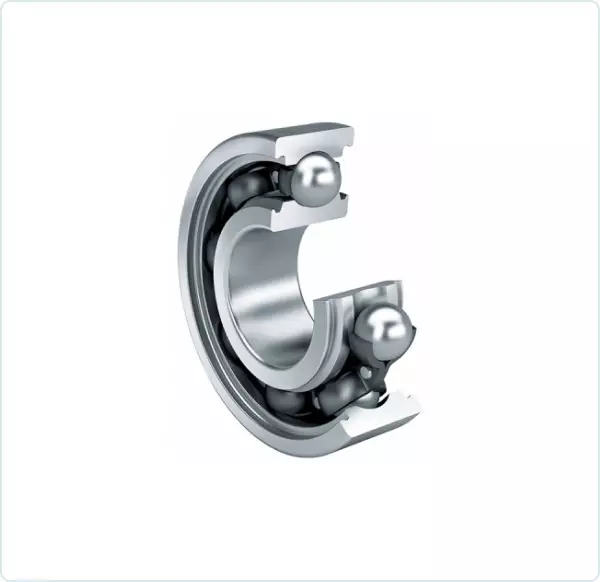
An open bearing is a rolling bearing with no built-in seals or shields, leaving all internal components exposed. Open bearings are typically used in clean, well-lubricated environments – for example, inside gearboxes or machinery where the bearing is continuously bathed in oil. Because they lack any enclosure, open bearings rely on the machine’s lubrication system and cannot prevent contaminants from entering on their own.
What Are Shielded Bearings?
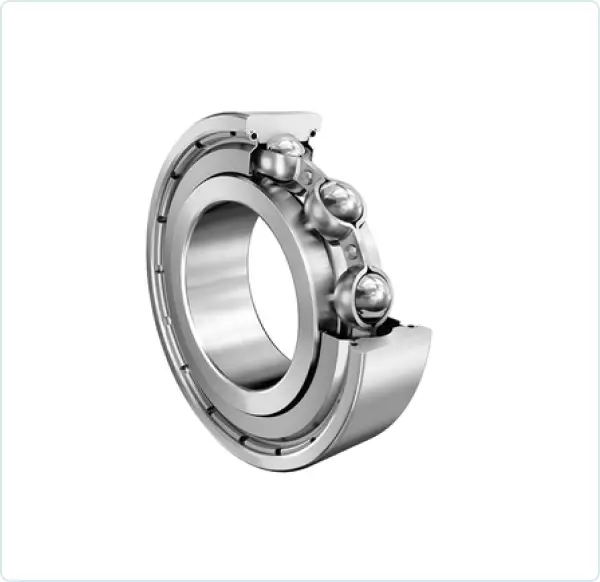
A shielded bearing is a bearing that uses metal shields on one or both sides to enclose the internal components partially. The metal shield sits in a groove of the outer ring and does not contact the inner ring, leaving a small gap. This design keeps out larger particles like dust and debris while still allowing low-friction operation. Shielded bearings are commonly used in moderately clean environments where some protection is needed but low starting and running torque is a priority – for example, in electric motors, fans, and appliances.
What Are Sealed Bearings?
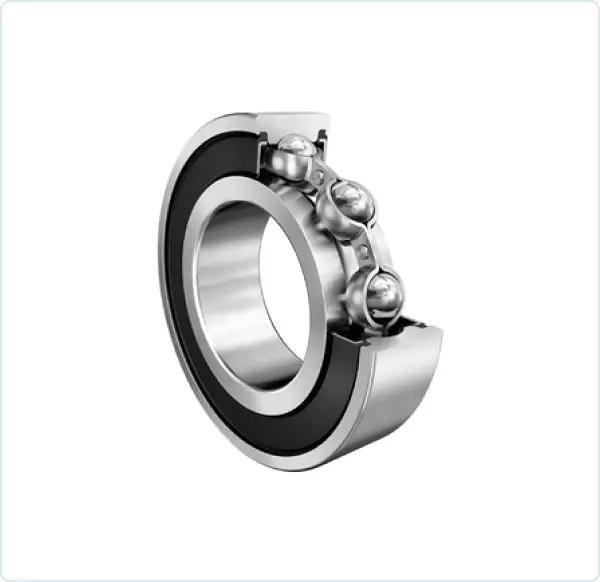
A sealed bearing is a bearing that has integrated seals (usually rubber or polymer) on one or both sides, fully enclosing the inner workings. The seals make light contact with the inner ring, creating a barrier that keeps lubricant in and contaminants out. Sealed bearings typically come pre-lubricated with grease and are effectively maintenance-free. This makes them ideal for dirty or wet environments, or any application where you need to protect the bearing from contamination and cannot frequently service it.
Sealed Bearings
Bearings with shields or seals filled with grease are widely used. Grease has the advantage over oil in that it’s more easily retained and takes longer to be compromised than oil.
Sealed bearings have the advantage of being lubricated for life, are suitable for normal and light loads with moderate to low speeds. Sealed bearings generally have a low production cost and maintain no need for relubricated or greased.
As such these bearings are used widely in electric motors, fan motors, and automation equipment.
Types of Bearing Seals: Contact vs. Non-Contact
In sealed bearings, manufacturers utilize two main types of seal designs: non-contact seals (or shields) and contact seals. Each type balances protection and friction differently:
- Non-Contact (Shield-Type): These have a small gap between the seal/shield and the inner ring – no physical contact. This design avoids added friction, allowing lower torque and heat, but it only provides moderate contaminant protection. (Metal shields labeled “Z” or “ZZ” are common non-contact enclosures.)
- Contact Seal: This seal touches the inner ring to form a tight barrier. Contact seals provide maximum protection against dust, water, and other contaminants, and they retain lubricant best. However, the trade-off is a slight increase in friction and operating temperature due to the contact. (Rubber seals labeled “RS” or “2RS” are typical contact seals.)
When selecting a seal type, consider the application’s speed, allowable friction, and environment. For high-speed or low-torque applications in cleaner settings, a non-contact shield may be preferable. In dirty or exposed conditions where protection is critical, a contact seal is the better choice.
What Are the Advantages of Sealed Bearings?
Key advantages of sealed bearings include:
- Contamination Protection: Sealed bearings excel at keeping out dirt, dust, and moisture. The integrated seals act as barriers, significantly reducing contamination ingress compared to open or even shielded bearings.
- Lubrication Retention: The seals lock grease inside the bearing. This means the lubricant remains in place for the life of the bearing, ensuring consistent lubrication and performance without regular re-greasing.
- Extended Bearing Life: By preventing contaminant entry and keeping lubrication where it’s needed, sealed bearings often last longer than open or shielded bearings in the same conditions. Less dirt and optimal lubrication translate to slower wear and fewer failures.
- Reduced Maintenance: Sealed bearings are generally maintenance-free. Users don’t need to periodically add grease; the factory-filled lubricant typically lasts for the bearing’s service life. This lowers maintenance schedules and labor.
Versatility: Because of their self-contained protection, sealed bearings work well in a wide range of applications, especially in harsh or outdoor environments. From agricultural equipment to wheel hubs, they are chosen when reliability in dirty conditions is required.
Bearing Shields vs. Seals – What’s the Difference?
Bearing shields and seals serve a similar purpose – they both protect the bearing’s internals from contamination and help retain lubricant – but they are not the same thing. The differences lie in their materials, design, and performance:
- Construction: A shield is usually a thin metal disc that sits in a groove on the outer ring and does not touch the inner ring. A seal is typically made of rubber or polymer and makes light contact with the inner ring.
- Protection Level: Because seals form a tighter barrier, they offer a higher level of protection against fine dust and liquids (even humidity or water splash) than shields. Shields mainly block larger particles and dust but won’t fully stop water or fine debris.
- Friction: Seals do contact the inner ring, so a sealed bearing has slightly more friction (and running torque) than a shielded bearing. Shields are non-contact, adding virtually no friction – which is why shielded bearings spin more freely.
- Lubrication & Maintenance: Sealed bearings are usually pre-lubricated at the factory and meant to run without additional lubrication (the seal keeps grease in). Shielded bearings can also come pre-greased, but because they aren’t fully sealed, grease can eventually leak or dry out, meaning periodic re-greasing might be needed for long-term use.
In short, a shield is a looser fitting metal barrier, whereas a seal is a tighter fitting rubber barrier. This fundamental difference is why sealed bearings tend to protect better but also have slightly more rolling resistance than shielded bearings.
Sealed vs. Shielded Bearings: Which Is Better?
When choosing between a sealed and a shielded bearing, “better” depends on your application requirements. Neither type is universally superior; each has trade-offs: A sealed bearing is better if you need maximum protection and minimal maintenance, whereas a shielded bearing is better if low friction and high-speed performance are critical. In practice:
- Use sealed bearings for environments exposed to dirt or moisture, or where you cannot frequently service the bearing. For example, in outdoor machinery or sealed-for-life installations, the sealed bearing’s superior protection and grease retention translate to longer life and reliability.
- Use shielded bearings for relatively clean, indoor, or high-speed applications where you want the bearing to run as freely as possible. In precision equipment, electric motors, or appliances, the lower drag of shields can be beneficial, provided heavy contamination isn’t present.
In summary, sealed bearings provide more protection while shielded bearings allow slightly better efficiency. The “better” choice comes down to whether protecting against contamination (sealed) or minimizing friction (shielded) is more important for your situation.
Comparison of Open, Shielded and Sealed Bearings
Feature | Open Bearing (no enclosure) | Shielded Bearing (metal shield) | Sealed Bearing (rubber seal) |
Enclosure Type | None – bearing is open/exposed. | Thin metal shield on sides; no contact with inner ring. | Flexible seal (rubber/polymer) on sides; light contact with inner ring. |
Contaminant Protection | Low: No built-in protection from dust or moisture. Suited only for very clean or lubricated environments. | Moderate: Shields block large debris and dust, but fine particles or liquids can still enter through the gap. | High: Seals provide a tight barrier against dust, dirt, and even water splashes, greatly limiting contaminant ingress. |
Lubrication Retention | None: Relies on external or continuous lubrication (e.g. oil bath). Grease can escape easily. | Partial: Grease is better retained than in open bearings, but some can leak out over time since shields aren’t airtight. | Excellent: Grease is sealed inside for the life of the bearing. Little to no leakage, allowing long-term lubrication with no external re-greasing. |
Friction & Torque | Lowest friction: No seals or shields means nothing additional contacting the races – ideal for minimizing drag. | Low friction: Non-contact shields add virtually no friction, so startup and running torque remain low (close to an open bearing). | Slight friction increase: Contact seals rub the inner ring slightly, which increases friction and starting torque a bit (and can raise operating temperature marginally). |
Maintenance Needs | High: Requires regular lubrication and cleaning since it’s exposed (e.g. frequent oil changes or grease application in use). | Moderate: May require occasional re-lubrication over time, especially in long-term service, because some grease may escape and contaminants can enter through gaps. | Minimal: Generally maintenance-free. Sealed bearings are typically lubed for life; you usually do not re-grease them during their service life. |
Typical Applications | Internally lubricated systems with low contamination: gearboxes, engines, transmissions (oil-bath environments). Not suitable for dirty or wet conditions. | Applications balancing low friction with some protection: electric motors, fans, household appliances – mostly clean environments but want to keep out dust. | Dirty, outdoor, or hard-to-service environments: automotive wheel hubs, agricultural machinery, conveyors – anywhere you need maximum protection and long life with no maintenance. |
Frequently Asked Questions
Q: When should I use a sealed bearing instead of a shielded bearing?
A: Use a sealed bearing when your environment is dirty, dusty, or exposed to moisture, or if you want a maintenance-free solution (no re-lubrication). In contrast, use a shielded bearing in relatively clean, dry conditions or high-speed applications where low friction is more important than maximum sealing.
Q: What are open bearings used for?
A: Open bearings are used in applications that supply continuous lubrication and are free of outside contaminants. A common use is inside gearboxes or engines where the bearing is bathed in oil. They’re chosen for their simplicity and low friction, but they are unsuitable for dirty or wet environments because they have no built-in protection.
Q: Do sealed bearings need maintenance or re-greasing?
A: Generally, sealed bearings do not require re-greasing during their service life. They come pre-lubricated from the factory and the seals keep the grease inside. Unless a sealed bearing is damaged or used past its intended lifetime, you typically don’t need to open it or add lubricant.
Q: What do “2RS” and “ZZ” mean in bearing part numbers?
A: These codes indicate the type of enclosure: “2RS” means two rubber seals (one on each side of the bearing), essentially a sealed bearing. “ZZ” means two metal shields, which is a shielded bearing. So, for example, a bearing number ending in 2RS is fully sealed, whereas “ZZ” denotes it’s shielded on both sides. (Similarly, a single “Z” or “RS” would indicate a shield or seal on one side only.)
Q: Why do some bearings have only one seal or one shield?
A: Some applications only need protection on one side. For instance, a bearing might be open on the inside (toward an internal oil source) and sealed on the outside (facing external dirt). Using one seal or shield reduces friction compared to two, and it can lower cost, while still protecting the more exposed side of the bearing. This configuration is designated in part numbers by a single suffix (e.g., “RS” or “Z” for a one-sided enclosure).