Drones and unmanned aerial vehicles (UAVs) rely on precision engineering in every moving part, and bearings are among the most critical components. Bearings support rotating elements and minimize friction, enabling drone propellers, motors, gimbals, and actuators to operate smoothly and efficiently. As the global drone market grows (with revenues around $4.4 billion in 2025), engineers are paying close attention to bearing design to boost performance. From tiny racing quadcopters to large industrial UAVs, the right bearings improve propulsion efficiency, flight stability, weight reduction, and even the quality of aerial imaging.
Why High-Quality Bearings Matter in Drone Performance
Bearings in drones do much more than reduce friction – they fundamentally impact a drone’s efficiency, stability, and longevity. Below are key ways bearings contribute to drone performance:
- Ensuring Propulsion Efficiency: In brushless drone motors, high-precision ball bearings support the rotor shaft, enabling smooth, frictionless rotation for optimal thrust. Quality bearings reduce power losses as the motors spin at tens of thousands of RPM, translating battery energy into lift. They also minimize wobble and vibration in the motor bell, so more energy is produced as useful thrust instead of noise or heat. Low-friction bearings mean motors run cooler and more efficiently, crucial for maximizing flight time on limited battery capacity.
- Enhancing Flight Stability & Control: Stable flight depends on vibration-free rotation of propellers and precise movement of control mechanisms. Precision bearings dampen vibration and noise, preventing oscillations that could destabilize the drone. For example, the bearings in propeller hubs and rotor shafts ensure even, balanced spinning of propellers, which improves the drone’s overall balance and responsiveness. In the control linkages of camera gimbals or flight actuators, tight-tolerance bearings eliminate slop, so the drone responds predictably to inputs. The result is a smoother flight with less sensor noise and better autopilot accuracy.
- Weight Reduction for Longer Flights: Every gram matters in aerial vehicles. Modern drone bearings are often specialized for low weight and compact size, without sacrificing strength. Thin-section bearings and hybrid ceramic bearings help reduce overall drone weight, directly improving flight time and maneuverability. A lighter bearing (and thus lighter drone) requires less lift to stay airborne, meaning the motors can draw less power or carry additional payload. Designers choose slim-profile bearings (discussed below) in place of standard bearings to save precious weight and space in drones’ tightly packed frames.
- Protecting Camera Image Quality: Drones used for photography, videography, or sensors carry sensitive cameras on stabilized gimbals. Bearings in these gimbals must allow butter-smooth rotation with minimal friction or “stiction.” Any jerky motion or vibration can blur images or footage. Precision miniature bearings in gimbal joints isolate the camera from motor vibrations and enable steady, fluid movement, resulting in sharp images and stable video. In essence, high-quality bearings are a prerequisite for professional-grade aerial imaging – they keep the camera level and stable despite the drone’s motion.
- Durability in Demanding Conditions: Drones often operate in harsh environments – high speeds, rapid maneuvers, temperature extremes, dust, moisture, and shock from takeoff/landing. Bearings designed for drones prioritize robustness and reliability. They use materials and lubricants that resist corrosion and wear. For instance, stainless steel or ceramic hybrid bearings won’t rust when drones spray crops or fly in humid climates. Bearings with secure seals keep out dust or water. By handling high RPMs, dynamic loads, and shocks without failing, quality bearings reduce the chance of mid-flight breakdowns and costly crashes. This durability gives drones longer service lives and safer operation.
In short, bearings might be small components, but they have an outsized impact on a drone’s propulsion efficiency, stability, weight, and data collection capability. Next, we’ll examine the common types of bearings used in drones and why each is chosen.
Common Bearing Types Used in Drones
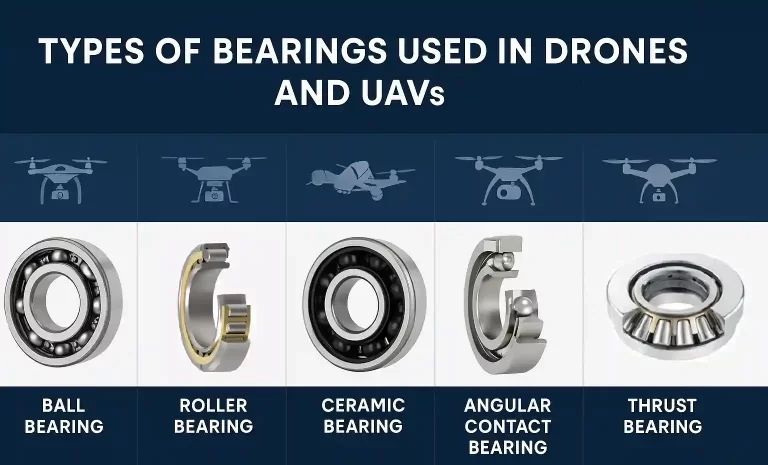
Modern drones utilize a range of bearing designs, each suited to particular functions and load conditions. Ball bearings are by far the most prevalent, but other types like rollers and thrust bearings appear in specialized roles. Below, we outline the main bearing types in drones, along with their applications and features.
Deep Groove Ball Bearings (Radial Ball Bearings)
Deep groove ball bearings are the workhorses of drone mechanisms. They have an inner and outer ring with a single row of steel balls running in deep raceway grooves. This simple yet robust design handles radial loads (forces perpendicular to the shaft) and moderate axial loads (along the shaft) in either direction. In drones, deep groove ball bearings are most commonly found in motor shafts, propeller assemblies, and even in some gimbal pivots.
Key advantages of deep groove bearings include low friction, high rotational speed capability, and ease of maintenance. Drone brushless motors, which can spin at extremely high RPM, rely on these bearings to minimize friction and heat as the rotor turns. A well-made ball bearing keeps the motor running smoothly, improving power transfer and efficiency. Deep groove bearings also contribute to drone longevity by sustaining the high-frequency vibrations of motors without rapid wear. For instance, a tiny stainless steel bearing like SMR115 (5 mm × 11 mm × 4 mm) can have a limiting speed over 50,000 RPM – a testament to the precision engineering that drone motors demand. In propeller hubs, pairs of deep groove bearings keep the prop shaft centered and spinning uniformly, which reduces flight vibrations. Overall, this bearing type’s versatility, high-speed performance, and compact size make it indispensable in virtually all drones, from hobby quadcopters to industrial UAVs.
Angular Contact Ball Bearings
Angular contact ball bearings are designed to support significant axial (thrust) loads in one direction, in addition to radial loads. They have raceways in the inner and outer rings that are offset (angled) relative to each other, so that the bearing can sustain a force along the axis. In drone applications, angular contact bearings are used where there are pronounced axial forces or combined loads – for example, in the main rotor shaft of heavier drones or in thrust-bearing positions of multirotor hubs. High-speed drones that perform aggressive maneuvers may also use angular contact bearings to better handle the stress from sudden directional changes.
The advantage of these bearings is their stiffness and load-bearing capacity in the axial direction. Unlike standard deep groove bearings, which can only take mild axial loads, an angular contact bearing (especially when used in pairs back-to-back) can safely support the upward or downward thrust from a propeller or rotor. This makes them valuable for drones carrying heavy payloads or drones with coaxial rotor arrangements. Angular contact bearings in drones improve stability and prevent excessive shaft flex under load. For example, a large quadcopter designed for crop-spraying might employ angular contact bearings in its motor mounts to handle the extra weight and forces. These bearings must be mounted correctly (with the proper orientation of the contact angle) and often in matching sets to distribute loads. When used appropriately, angular contact bearings provide both high-speed capability and reinforcement against axial stress, ensuring the drone’s rotating assemblies remain precise under demanding conditions.
Thin-Section Bearings (Reali-Slim® Type)
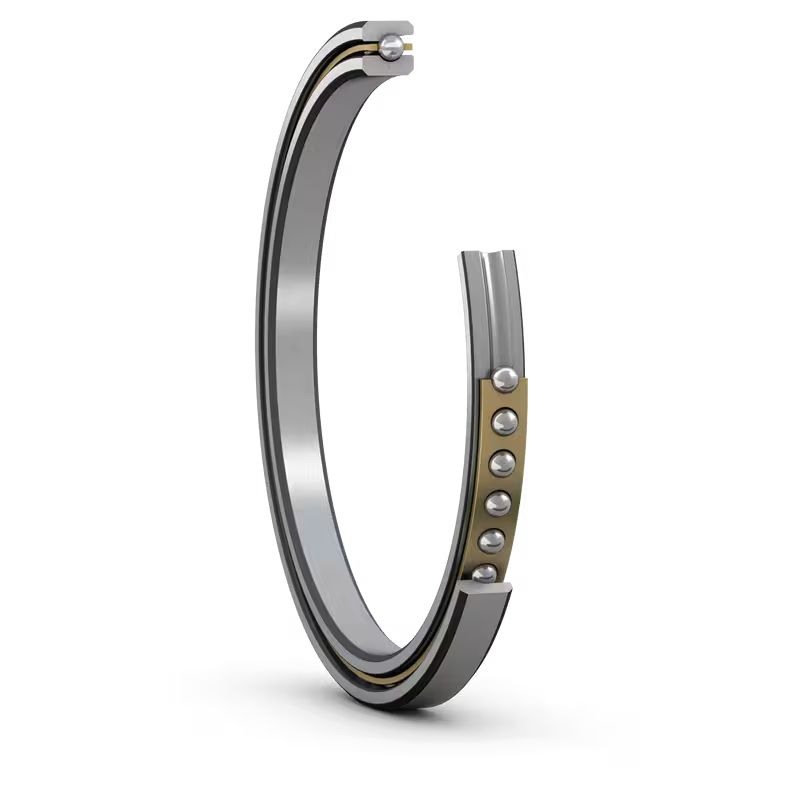
Drones that require minimal weight and space often turn to thin-section bearings – also known by trademarks like Reali-Slim®.
Thin-section bearings are a special type of radial ball bearing where the cross-sectional profile (thickness of the bearing) is very small relative to the bore diameter. For example, the bearing KA020CP0 has a 2.0-inch bore, 2.5 inch outer diameter, but only a 0.25 inch cross-section. This slim profile means the bearing adds very little bulk or mass to a design. In drones, thin-section bearings find use in areas such as camera gimbals, pan-tilt mechanisms, LIDAR scanners, or lightweight frames, where standard bearings would be too bulky. They can even serve as the main rotor or tilt mechanism bearings in compact UAVs where weight savings are critical.
The primary benefit of thin-section bearings is weight reduction and space efficiency. By using a thinner ring and ball set, these bearings cut down on material and mass – sometimes weighing less than half of an equivalent standard bearing. They also have lower inertia, which improves the responsiveness of moving parts (important for camera stabilization systems). Despite their slim build, quality thin-section bearings can still handle respectable loads and offer good accuracy. For instance, Kaydon-type thin bearings with brass cages and steel races are designed for demanding applications like aerospace gimbals and robotics. PIB regularly supplies thin-section bearings like the KA series, which are ideal for drones needing a large diameter bearing without the added weight. One consideration: because of their thin rings, these bearings must be handled and mounted carefully to avoid distortion. When properly integrated, thin-section bearings contribute to longer flight times and more agile drone movements by shaving off unnecessary weight.
Hybrid Ceramic Ball Bearings
Hybrid ceramic bearings combine traditional metal races with ceramic balls, typically made of silicon nitride. This design yields a bearing that is lighter and can perform under conditions where all-steel bearings might falter. In racing drones and UAVs where maximum motor RPM and minimal friction are desired, hybrid ceramic ball bearings are a popular upgrade. The ceramic balls have several advantages: they are extremely smooth and hard (up to 7 times harder than steel), and much lighter – about 58–60% lighter than steel balls. This reduces the overall rotating mass, allowing motors to spin faster with less centrifugal force. The lower weight and ultra-smooth surface of ceramic balls mean lower friction and heat generation, which is critical for high-speed operation. Drones configured for racing or fast aerial maneuvers benefit from these traits, as hybrid bearings can tolerate very high RPM without overheating or binding.
Another benefit is that ceramic balls don’t corrode and are not electrically conductive. In drone applications, this means hybrid bearings can survive wet or humid conditions better (no rust on the balls), and they can be used in electric motor setups where electrical insulation of the bearing is a plus. Hybrid ceramic bearings are also very durable in the sense that they resist wear – the hard ceramic doesn’t deform easily, so bearings maintain their precision for a long time. However, they can be brittle and are more expensive, so they’re used selectively: typically in premium drone motors, generator/alternator units in UAVs, or long-life components where the cost is justified. Many drone enthusiasts report smoother motor acceleration and a small increase in flight time by switching to hybrid ceramic motor bearings, thanks to the reduced friction and weight. Pacific International Bearing Sales (PIB) offers hybrid ceramic options (often stainless steel races with Si<sub>3</sub>N<sub>4</sub> balls) for customers looking to upgrade drone motors or solve performance issues like overheating bearings. It’s an example of how material science in bearings directly contributes to UAV performance.
Other Bearings: Roller & Thrust Types
While ball bearings handle the majority of drone needs, certain drones employ specialty bearings:
- Roller Bearings (Tapered & Cylindrical): These bearings use cylindrical rolling elements instead of balls, trading higher friction for much greater load capacity. Tapered roller bearings can support very high radial and axial loads, so they appear in large UAV or eVTOL (electric helicopter) rotor shafts, or heavy payload drone hubs where deep groove balls would wear out quickly. Cylindrical rollers might be used in drone gearboxes or drive train components that see heavy radial forces. The downside is weight – rollers are generally heavier and larger. But for drones designed to carry heavy cargo or perform tasks like crop spraying with significant force on the airframe, roller bearings ensure durability and stiffness.
- Thrust Bearings: These are designed purely for axial loads (forces along the shaft). In drones, thrust bearings might be used in vertical shaft support (e.g., supporting a vertical lift rotor or in a coaxial rotor system to take the upward thrust) or in gimbal assemblies to bear the weight of camera equipment. Thrust ball bearings or needle thrust bearings resist motion in the axial direction, keeping components like rotors from shifting under lift forces. For example, a small thrust bearing can prevent a drone’s propeller hub from sliding downward when the prop produces lift. Thrust bearings thus contribute to stability and prevent undue wear on other parts.
Each type of bearing plays a role in drone engineering. Often, drone designs will use a combination – deep groove ball bearings for general use, maybe an angular contact pair for a main shaft, a thin-section for the gimbal, and perhaps a tapered roller in a high-load joint. The goal is always to maximize performance while minimizing weight and size. The table below summarizes common bearing types found in drones:
Bearing Type | Typical Drone Applications | Features & Benefits |
Deep Groove Ball Bearing (single-row) | – Drone motors (rotor shaft support)- Propeller hubs- Small gimbal pivots | Versatile, low-friction bearing for high-speed rotation. Supports radial and moderate axial loads in either direction. Compact and lightweight. Enables smooth motor operation and reduces heat build-up. The most common bearing type in drones is due to its broad capability. |
Angular Contact Ball Bearing (single or paired) | – Heavy-lift drone rotor shafts- Thrust-heavy propeller mounts- Drone wheel or joint bearings (for axial stiffness) | Oriented for combined loads with a high axial component. Installed often in back-to-back pairs for stability. High contact-angle design gives greater thrust load capacity and rigidity. Used when drones carry substantial weight or endure high-G maneuvers. |
Thin-Section Ball Bearing (deep groove, thin profile) | – Camera gimbals and pan-tilt units- Folding arm joints- UAV gear where space/weight are limited | Ultra-slim, lightweight bearing. A large diameter-to-width ratio dramatically saves weight. Allows compact designs without sacrificing bore size. Lower torque and inertia for improved efficiency. Ideal for precision instruments (cameras, sensors) where every gram counts. |
Tapered/Cylindrical Roller | – Large UAV main rotor or propeller shafts- Gearboxes and drive systems- Drones with heavy payload mounts | High load capacity bearings for heavy-duty use. Rollers increase contact area, supporting heavy radial loads and shock. Tapered types handle axial thrust as well. More robust but heavier; used in drones with significant loads (e.g., delivery drones) to ensure longevity. |
Thrust Bearing (ball or roller) | – Vertical shafts (coaxial rotors, lift fans)- Gimbal rotation axes (axial load from camera weight) | Dedicated axial load support. Keeps components from moving along the shaft under thrust. Prevents component separation and wear under propeller lift forces. Often combined with radial bearings in a stack. Ensures stability in multi-rotor hubs and smooth gimbal tilt/yaw motions. |
Hybrid Ceramic Ball (steel/ceramic mix) | – High-performance racing drone motors- High-temperature or high-rpm parts- Long-endurance UAV systems | Steel races with ceramic balls for extreme performance. Ceramic elements are ~60% lighter than steel, vastly reducing spinning mass and friction. Offer higher RPM limits, run cooler, and resist corrosion. Perfect for maximizing motor efficiency and lifespan. Higher cost, so used in specialty builds. |
Bearing Material Options and Their Benefits
Selecting the right materials for a drone’s bearings is as important as choosing the type. Materials affect a bearing’s strength, weight, corrosion resistance, and friction – all of which influence drone performance. Below are common bearing materials and constructions used in UAV applications, along with their engineering benefits:
- Chrome Steel (AISI 52100): The standard material for most bearing rings and balls. Chrome steel is a high-carbon alloy steel that offers excellent hardness and fatigue life, making it capable of handling high loads and speeds. Its smooth finish and consistency yield low-noise operation. In drones, chrome steel bearings are used in motors and props where maximum strength is needed under high RPM. They perform best in normal environments; however, they are not corrosion-resistant, so if exposed to moisture (e.g., drones used in crop spraying or marine environments,) they require protective coatings or regular maintenance. Chrome steel’s popularity comes from its high load capacity-to-cost ratio – it’s strong and economical.
- Stainless Steel (AISI 440C or similar): Stainless steel bearings trade a bit of hardness for corrosion resistance. 440C stainless steel can be heat-treated to a high hardness (though slightly lower than 52100), and it contains chromium that forms a protective oxide layer against rust. For drones operating outdoors, in agriculture (spraying chemicals), or in high-humidity climates, stainless steel bearings are preferred to prevent rust and pitting. They ensure longevity where chrome steel might corrode. Engineering benefits include good toughness and temperature tolerance. Stainless bearings are often used for miniature bearings (e.g. in micro-drones or camera gimbals) and any application where the bearing might encounter water or condensation. They are slightly heavier than chrome steel and have marginally lower load ratings, but the corrosion resistance can be vital for reliability.
- Hybrid Ceramic Construction: As discussed earlier, hybrid bearings use steel (usually chrome or stainless) for the races and ceramic (Si₃N₄) for the balls. This combination yields a bearing that leverages the strengths of both materials: ceramic balls are extremely hard, smooth, and light, while steel rings provide toughness and ductility. Engineering benefits include higher speed capability (ceramic balls can tolerate ~30–50% higher surface speeds) and much lower weight/inertia, improving dynamic response. Hybrids also run with less lubrication – ceramic doesn’t gall or micro-weld to steel, which reduces adhesive wear and friction. They are also electrically insulating, which can protect drone motor windings from stray currents via the bearings. The downside is cost and the slight brittleness of ceramics (they can crack under severe shock loads). Overall, hybrids are chosen for high-performance and longevity – e.g., a professional drone’s brushless gimbal motors might use hybrid bearings to remain ultra-smooth over many hours of operation.
- Full Ceramic Bearings: In some specialized cases, bearings are made entirely of ceramic (rings and balls of Si₃N₄ or ZrO₂). Full ceramics are extremely lightweight and can operate in environments where metal bearings fail (very high temperatures, no lubrication, acidic exposure). They have a minimal magnetic signature and never rust. However, in drone use, they are rare due to expense and brittleness. One might find full ceramic miniature bearings in niche applications like very high-altitude drones or where non-magnetic properties are needed (certain scientific instruments). Generally, hybrids suffice for most needs, and full ceramics are used only when necessary.
- Polymers and Composites: Some small drone mechanisms (like tiny toy drones or very light servo actuators) might use plastic bushings or polymer bearings. These eliminate the need for lubrication and are extremely light. For example, an igus® polymer bushing could be used in a hinge that doesn’t spin fast but must be maintenance-free. The benefit is that they don’t corrode and add almost no weight; the trade-off is much lower load capacity and higher friction at speed. They are only suitable for low-stress, low-speed joints. In high-end drones, polymer bearings are uncommon except perhaps in hinges for folding arms or dampers.
The choice of material often comes down to environmental conditions and performance requirements. Many drone builders start with chrome steel bearings for their strength, then upgrade to stainless or hybrid ceramic as needed for corrosion resistance or better efficiency. The table below summarizes bearing material options and their benefits in drone engineering:
Material / Construction | Benefits | Use in Drones |
Chrome Steel (52100 alloy) | Highest load capacity and hardness; low wear.Smooth surface for low friction and noise.Economical and widely available. | The default choice for most high-stress parts (motors, props).Use in dry environments; needs proper lubrication.Not rust-proof – avoid exposure to water or chemicals. |
Stainless Steel (440C, etc.) | Corrosion resistant – won’t rust in humidity or rain.Good hardness (near 52100 when hardened).Withstands moderate/high temperatures. | Preferred for outdoor and agricultural drones, marine UAVs.Miniature bearings in gimbals and flight controllers (for long life without rust).Slightly lower load rating than chrome steel, but much better durability in corrosive environments. |
Hybrid Ceramic (Steel + Si₃N₄ balls) | Lower rotational mass – ceramic balls ~60% lighter.Very high hardness and polish -> minimal friction, lower heat.No electrical conductivity between races.Excellent wear and corrosion resistance. | High-performance drone motors (racing drones, high-end UAVs) for efficiency and speed.Cases where lubrication is minimal or high temperature (ceramic tolerates heat).Increases cost; used where performance gains justify it. |
Full Ceramic (Si₃N₄ or ZrO₂) | Ultra-lightweight & non-magnetic.Can run with zero lubricant (good for vacuum or very clean environments).Impervious to corrosion, can handle extreme temperatures. | Rarely used in drones (costly).Potentially in specialized aerospace drones or research UAVs requiring non-metallic components.Suitable for low-load, high-temp situations – otherwise use hybrid for better toughness. |
Polymers / Composites (plastic) | No maintenance (self-lubricating).Very light and corrosion-proof.It can dampen vibrations due to material elasticity. | Toy drones or micro mechanisms with tiny loads.Hinge points or folding arms that need a simple, light bushing.Not for precision or high-speed parts due to higher friction and wear. |
Performance Parameters for Drone Bearings
Designing or selecting a bearing for a UAV involves meeting certain performance criteria. Key parameters include rotational speed, load capacity, weight, friction, and more. These factors determine whether a given bearing will adequately support the drone’s operation without failure. Below, we highlight a few critical performance parameters and why they matter for drone bearings:
- Maximum RPM (Speed Rating): Drone motors, especially in multirotors, spin at very high speeds to generate lift. Bearings must be rated for these speeds. If a bearing’s speed limit is exceeded, it can overheat or suffer lubricant failure. For example, small racing drones have motors that may spin 30,000–50,000 RPM, so their bearings (often ABEC-5 or ABEC-7 rated) are built to handle extremely high RPM with minimal friction. Quality miniature bearings like the SMR115 can reach ~53,000 RPM limits thanks to precision manufacturing. Using a bearing with a comfortable speed overhead ensures smooth power delivery and prevents overheating at full throttle.
- Load Capacity (Radial & Axial): Load capacity is the amount of force a bearing can sustain without undue wear or deformation. Drones experience radial loads (from the weight of rotors, centrifugal forces, etc.) and axial loads (thrust from propellers, payload weight). Bearings must handle both. A propeller shaft bearing, for instance, needs sufficient radial load capacity to support the spinning prop and axial capacity to take the thrust lifting the drone. If a drone will carry heavy payloads or perform high-G maneuvers, engineers will check that the selected bearing’s dynamic load rating exceeds the expected forces with a safety margin. Exceeding load ratings leads to early fatigue or brinelling of the bearing. Large UAVs might require bearings with dynamic capacities in the thousands of Newtons. Ensuring the bearing can handle shock loads and continuous forces is vital for safety. Using high-load bearings (like tapered rollers for heavy drones) adds weight, so there is a trade-off – part of the engineering challenge is choosing a bearing just robust enough but not overbuilt.
- Weight and Form Factor: Bearing mass directly contributes to the drone’s weight budget. A lighter bearing helps achieve longer flight times and better agility. This is why thin-section bearings and hybrids are popular – they cut down mass significantly. For example, replacing a standard bearing with a thin-section or using ceramic balls can save several grams per bearing (ceramic balls are significantly lighter than steel). In a drone with a dozen bearings, these savings add up. Engineers look at the bearing’s dimensions (OD, width) to ensure it fits in the design without wasteful material. A bearing’s weight-saving potential is often expressed qualitatively (e.g., “30% lighter than standard”) since it depends on the specific sizes. The goal is to minimize dead weight while meeting strength needs – hence the use of compact designs like 6700-series thin bearings (which have very low profiles, e.g,. 4 mm thick for a 15 mm bore in a 6702 bearing). Lower weight bearings contribute to a higher power-to-weight ratio for the drone.
- Friction (Torque) and Efficiency: The internal friction of a bearing (often measured as a torque or coefficient of friction) affects how much energy is lost as heat. Low-friction bearings allow more of the motor’s power to convert to thrust. Factors influencing friction include the quality of surfaces, lubricant type, seals, and preload. Drones benefit from bearings with polished raceways and optimal clearances (often C3 clearance for high-speed small bearings) to keep friction low. For precision camera gimbals, low starting friction (static friction) is crucial so that even a small command can move the camera – specialized bearings or cross-roller designs might be used for near-zero backlash and friction. Engineers may refer to frictional torque charts in bearing datasheets to pick a bearing that won’t drag on the motors. Proper lubrication is also key: lightly oiled bearings might give the least friction for racing drones, whereas greased bearings might be chosen for longevity in industrial drones, accepting a minor friction increase. The bottom line is that minimizing friction maximizes flight efficiency and reduces heat that can degrade components over time.
- Precision and Clearance: The manufacturing precision (tolerance class) of a bearing, along with its internal clearance, determines how smoothly and accurately it runs. High precision (ABEC-5/7 or ISO P5/P4) bearings have tighter tolerances on roundness and alignment, which results in less vibration at high speeds. They also often have a better surface finish. Drones with high-speed rotors or sensitive instruments might require precision-grade bearings to avoid imbalance and noise. Internal clearance (like C3, C4, etc.) defines the play between rings. Too loose and the rotor may wobble; too tight and friction increases or the bearing may seize when hot. For drone motors, a slightly higher clearance (C3) is commonly used to account for thermal expansion at high RPM, ensuring the bearing doesn’t preload itself when the motor heats up. Precision also affects repeatability – a high-grade bearing in a gimbal will help the camera return exactly to center with minimal hysteresis. So, selecting the right grade and clearance is essential for smooth, jitter-free operation.
- Environmental Resilience: Drone bearings must often be tailored to the environment: if the UAV will experience dust or sand (desert operation), sealed bearings with appropriate shields and possibly ceramic elements (for grit tolerance) are chosen. For cold weather or high-altitude (thin air) use, lubricants and materials must be rated for the temperature range so bearings don’t seize or lose lubrication. In summary, speed, load, weight, friction, precision, and environment are all taken into account. The following table focuses on a few of these performance parameters, illustrating their importance:
Parameter | Importance of Drone Applications | Example / Implication |
Max Speed (RPM) | Must exceed the rotational speed of drone motors and rotors without overheating or losing lubrication. High-speed capability ensures smooth power transmission and prevents bearing failure at full throttle. | Racing drone motors can spin >30,000 RPM; bearings are chosen to handle ~50,000 RPM safely. E.g., a miniature SMR115 bearing is rated for ~53,000 RPM, enabling high KV motors to run reliably. |
Load Capacity (Dynamic & Static) | Bearing must support forces from propeller thrust, weight of payload, and maneuvering loads. Adequate load margin prevents permanent deformation and fatigue. Both radial and axial capacities are considered for drone multi-axis loads. | A delivery drone’s rotor bearings might see >1000 N of combined load during lift and turns. Selecting a tapered roller bearing with a high dynamic load rating provides durability. Insufficient capacity could lead to early bearing failure (vibration, roughness) after a few flights. |
Weight (Mass) | Lighter bearings contribute to a lighter drone, improving flight time and agility. Low-profile designs also save space. Weight reduction in bearings is often achieved with smaller cross-sections or lighter materials. | Using a thin-section bearing instead of a standard bearing can cut bearing weight by ~50%. Hybrid ceramic bearings further reduce rotating mass (ceramic balls ~60% lighter than steel). A lighter drivetrain means the drone can carry more payload or fly longer on the same battery. |
Friction & Vibration (Bearing torque, runout) | Low internal friction reduces energy loss (longer battery life) and heat. Minimal vibration from bearings is critical for stability and sensor performance. High precision and proper lubrication keep friction and vibration low. | Precision ABEC-7 bearings in a gimbal have extremely low friction, allowing smooth camera motion with minimal motor effort. Low-vibration bearings prevent transmission of motor buzz to the IMU (inertial measurement unit), thus improving flight controller accuracy. Conversely, a rough bearing could introduce oscillations that destabilize a drone’s flight. |
Bearing Part Number | Type & Size | Drone Application | Key Features |
SMR115 (SMR115-2RS) | Miniature Deep Groove Ball Bearing– 5 mm × 11 mm × 4 mm (ID×OD×W)Stainless Steel, double sealed | Small drone motors, micro-gimbals, FPV racing drones (motor or axle positions). Often used in pairs in brushless motors of size 11xx to 18xx. | High-speed miniature bearing (up to ~53k RPM) with corrosion-resistant steel construction. Low-friction seals keep dust out during low-altitude flight. Common upgrade for tiny whoop and micro drone motors due to durability and smoothness. |
6702-2RS (61702 series) | Thin-Section Deep Groove Ball Bearing– 15 mm × 21 mm × 4 mmSteel, double sealed | Medium-sized drone motors (e.g., 22xx to 28xx motors), rotor shafts in lightweight drones, or gimbal yaw bearings where a slim form factor is needed. Fits in tight hubs and arm joints. | Ultra-thin profile bearing (4 mm width) significantly reduces weight and space. Despite its slim size, it supports typical motor radial loads with a proper rating. Rubber seals protect against dirt – useful for drones in dusty environments. Available in chrome steel or stainless. Often chosen for its weight-saving potential in racing and long-endurance drones. |
KA020CP0 (Kaydon Reali-Slim) | Thin-Section Reali-Slim Ball Bearing– 2.000″ ID × 2.500″ OD × 0.250″ width(≈50.8 mm × 63.5 mm × 6.35 mm)Open, radial contact, ABEC-1 | Larger UAV gimbals (e.g., heavy camera turret rotation), drone arm pivots on professional rigs, or multi-rotor hubs on big drones. Ideal for weight-critical designs that need relatively large diameter support. | Extremely lightweight for its size – 1/4″ cross-section saves space. Open brass cage design for low friction. Handles ~1.5 kN dynamic load, suitable for moderate loads in UAVs. Aids in weight reduction for better flight efficiency. PIB supplies these high-quality Kaydon bearings (Kaydon is an SKF brand) as an authorized distributor, ensuring genuine performance. |
6806-2RS Hybrid | Hybrid Ceramic Deep Groove Ball Bearing– 30 mm × 42 mm × 7 mmSteel races (52100), Si₃N₄ ceramic balls, sealed | Drone drive motors in high-end UAVs or eVTOL, generator/alternator bearings, and high-speed rotor shafts, where low friction and long life are paramount. Also considered in custom racing drone builds for oversized motors. | Hybrid ceramic construction: 6 mm ceramic balls reduce rotating mass and prevent heat buildup. Sealed for life with high-speed grease. Supports high RPM with minimal wear – ideal for endurance and racing. Greater cost, but dramatically lowers maintenance frequency. PIB can provide hybrid versions of many standard sizes (including 68xx and 69xx series) for clients seeking ultimate performance. |
NMB RTX BB (Example)** | Precision Angular Contact Bearing (pair)– 8 mm × 22 mm × 7 mm (single)Matched pair arrangement | Thrust-hungry positions: e.g, dual bearing support for a large drone’s main rotor or tilt-rotor mechanism. Also used in some drone gearboxes or propeller shaft supports requiring high stiffness. | Matched angular contact pair preloaded for zero end-play. Provides stiff, precise rotation under axial thrust. Common in aerospace mechanisms – e.g., NMB’s RTX series is used in gimbal and actuator assemblies. PIB, as a partner of MinebeaMitsumi (NMB), delivers these high-precision bearings with full factory support. |
Conclusion
By carefully selecting bearing types, materials, and designs optimized for propulsion efficiency, stability, weight savings, and precision, drone engineers can unlock better performance and reliability. Pacific International Bearing Sales, Inc. is proud to support this industry with both products and engineering know-how. PIB’s role as an authorized distributor and technical partner means that drone manufacturers and hobbyists alike have access to the best bearings from around the world, plus guidance on using them to full effect.
As UAV technology continues to advance, with higher speeds and heavier payloads on the horizon, bearings will remain a pivotal component to innovate. Whether it’s a ceramic hybrid bearing enabling a new top speed or an ultra-thin bearing making a new micro-drone possible, PIB is here to help integrate these solutions. We understand that in drones, every bit of efficiency counts, and a small component like a bearing can make a big difference. With the right bearings in place, drones can fly longer, smoother, and more reliably, achieving new heights in performance.
Please contact us at [email protected] or visit us at www.pibsales.com for your next drone project and let our expertise in precision bearings keep your ideas airborne. From selecting the optimal bearing to ensuring on-time supply, we’ll make sure the critical components in your UAV are rock-solid, so you can focus on flying with confidence.