Modern industrial automation – encompassing robotics, advanced machinery, and mechatronic systems – rely on precision bearing technologies as critical building blocks. From the robotic arms assembling products to the conveyor systems moving materials, bearings enable smooth, reliable motion by reducing friction and supporting loads. Leading manufacturers like SKF note that integrated bearing systems and linear components “contribute to better performing and more reliable machine operations” across a wide spectrum of automated applications. Pacific International Bearing Sales Inc. (PIB), as a trusted distributor of major brands (IKO, Ruland, SKF, Schaeffler Group’s INA/FAG, etc.), play a key role in delivering these high-performance solutions to engineers and machine builders. In this article, we explore how precision bearings support modern machine automation, robotics, and mechatronic systems and highlight design advantages that make today’s automation systems efficient, flexible, and precise.
Bearings in Robotics and Mechatronic Systems
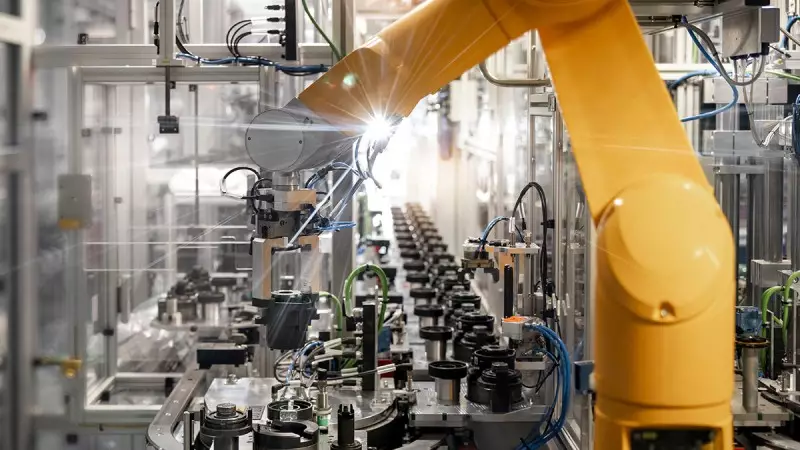
Industrial robots and complex mechatronic assemblies depend on a variety of bearings at every joint and moving interface. High-quality ball and roller bearings are the unsung heroes inside robot arms, providing the accuracy, rigidity, and long life needed for repeatable motion. For over two decades, major robot OEMs have relied on advanced bearing solutions to achieve “powerful performance, unrivaled reliability and extended lifetime”, allowing 24/7 operation in fields from automotive manufacturing to semiconductor fabrication. In multi-axis robots, each axis may use different bearing types: deep groove ball bearings, angular contact bearings, needle or tapered roller bearings, and even specialized harmonic drive bearings, all chosen to handle specific loads and precision requirements. For example, NSK recently developed a new “wave” bearing for strain wave (harmonic) gearboxes used in collaborative and service robots – an innovation that boosts precision in compact robot joints.
Robotic systems also make heavy use of crossed roller bearings and slewing ring bearings for rotational joints that demand high stiffness and accuracy. Crossed roller bearings contain cylindrical rollers arranged orthogonally, enabling a single compact bearing to carry loads in all directions with minimal deflection – ideal for robot wrists or rotary tables. IKO (one of PIB’s key partners) produces crossed roller bearings and needle bearings widely used in robotics and industrial machines. Slewing ring bearings (large-diameter turntable bearings) support heavy rotating masses such as a robot’s base or arm turret. These robust components allow precise positioning of heavy loads; in fact, slewing rings are “a perfect fit for robotics, aerospace, heavy equipment, and industrial machinery”, where they provide smooth, controlled rotation under substantial loads. Whether it’s an articulated robot or a gantry system, the right bearing choice ensures the robotic motion is precise, repeatable, and maintenance-friendly.
Bearings in Linear Actuators and Motion Systems
Linear motion is at the heart of many automated systems – from Cartesian robots and machine tools to packaging lines. Bearings enable linear actuators (electric cylinders, slides, etc.) to move with minimal friction and high accuracy. Linear bearings and guide rails provide the tracks on which automation equipment can carry out smooth, quiet linear motion. Precision profile rail guides with recirculating ball or roller elements support heavy loads while keeping linear travel accurate to a few microns. These guides often include features like long-life seals and integrated lubrication units that ensure “long-term, maintenance-free operation”, critical for keeping production lines running without unexpected downtime. In pick-and-place machines or semiconductor handlers, for instance, linear guide bearings maintain alignment and stiffness so that each movement is repeatably precise.
Another cornerstone of linear actuators is the ball screw, which is a screw-nut mechanism using ball bearings to convert rotary motion to linear motion with high efficiency. Ball screws (and their higher load counterpart, roller screws) allow servo motors to drive linear axes with minimal backlash and energy loss. SKF’s automation portfolio highlights such components – “ball and roller screws, actuators, rail guides” – as building blocks that accelerate OEM development and ensure robust performance in automated machinery. For example, electromechanical actuators using ball screws can replace pneumatic cylinders to offer finer position control and greater energy efficiency. In SKF’s experience, modern electromechanical linear actuators in automated welding systems “offer outstanding energy efficiency” and eliminate downtime through built-in lubrication, while sealed bearings in their construction provide added reliability. Whether in a high-speed packaging line or a CNC machine, linear bearings and ball screws work together to deliver fast, precise, and energy-efficient motion.
Bearings in Rotating Machinery
Virtually every rotating element in an automated machine is supported by bearings. Electric motors, gearboxes, spindles, and rotary tables all rely on precision bearings to carry shafts and loads at speed. In automated factories, motors and gear drives may run continuously, so bearing selection directly impacts performance and equipment life. Deep groove ball bearings are commonly used in electric motors and pumps for their low friction and quiet operation, while angular contact and tapered roller bearings are chosen for handling higher loads or combined axial-radial forces (such as in gearboxes or spindle heads). The Schaeffler Group (parent of INA and FAG) and its affiliates produce specialized bearings for such needs – for instance, KBC (a Schaeffler brand) is known for electric motor quality (EMQ) deep groove ball bearings and tapered roller bearings that ensure durability and low vibration in motor applications. These high-grade bearings minimize energy loss and heat generation, contributing to more efficient and long-lived motors and drives.
Precision rotating machinery often also employs crossed roller bearings or angular contact ball bearings in pairs for accurate positioning. For example, a rotary indexing table on an assembly machine might use a crossed roller ring to achieve zero play and high rigidity, enabling exact indexing at high speed. In high-speed machinery, low-noise and well-balanced bearings are important – many automation-grade bearings are manufactured to tighter tolerances (ABEC-5/7 or P5/P4 class) to support precision motion. Proper lubrication and sealing are equally crucial in rotating machines; many industrial bearings come pre-lubricated or sealed for life, reducing maintenance needs. To connect rotating components, designers also rely on couplings – PIB supplies Ruland’s precision shaft collars and couplings, engineered for critical motion control applications to ensure “dependable performance and exact alignment”. These couplings, while not bearings themselves, complement the bearing systems by transmitting torque smoothly between motors, gearboxes, and driven elements without backlash, thereby protecting the bearings from misalignment stresses. In sum, quality bearings in rotating machinery guarantee the smooth, efficient transfer of power and motion that automated systems demand.
Bearings in Automated Material Handling Systems
Automated material handling – including conveyor systems, automated guided vehicles (AGVs), robotic forklifts, and gantry cranes – puts heavy demands on bearings for both load capacity and reliability. Conveyor rollers and pulley shafts, for example, are commonly mounted on pillow block bearings, which are housings with integrated bearings that make it easy to bolt into machinery frames. These pillow block (or flange) units often utilize spherical roller or deep groove bearings that can handle misalignment and keep conveyors running smoothly at high throughput. In warehouse automation, where miles of conveyor and sorter systems run nonstop, using high-quality mounted bearings with proper seals and lubrication is key to avoiding costly downtime.
Large-scale material handling equipment and robotics frequently employ slewing ring bearings for rotational movement. Slewing rings (some exceeding a meter in diameter) support and rotate platforms such as robotic crane arms, turret mechanisms, or even the chassis of mobile robots that swivel. They are built to carry very high axial and radial loads. A typical slewing ring features either balls or crossed rollers and may incorporate gear teeth for driving the rotation. These bearings provide an optimal solution when “significant load-carrying, heavy-duty applications” must also achieve precise positioning – for example, the swivel base of a heavy robotic picker or the turntable of a palletizing machine. Because material handling systems often operate in varied conditions (dust, impact loads, continuous duty), robust bearing designs with protections like triple-lip seals and grease reservoirs are favored.
A case in point from NSK’s experience involves an autonomous mobile robot for warehouse order fulfillment. The drive gearbox in this robot was initially using a standard ball bearing, but under the high torque and shock loads of lifting storage racks, it was not meeting the required lifespan. NSK’s engineers determined that switching to a tapered roller bearing for the gear output shaft would better handle the heavy loads “to fulfill the life requirements specified by the end user”. The tapered roller bearing’s higher load capacity and stiffness ensured the AGV could run reliably with zero unplanned downtime in the material handling system. This example underscores how selecting the right bearing type (in this case, upgrading to a heavy-duty bearing) is critical for dependable automation in logistics and material transport. With expert guidance, designers can choose bearings that maximize uptime even under 24/7 operation and challenging loads.
Common Bearing Types in Automation
Modern automation systems draw on a wide range of bearing styles, each suited to specific motion tasks. Key bearing types and related motion components commonly used include:
- Linear Bearings and Guides: These include linear ball bearings (bushing-style bearings that run on shafts) and profile rail guides with recirculating balls or rollers. They enable precise, low-friction linear motion in actuators and gantries, ensuring smooth travel for robot arms or slides. Many linear guides are designed for quiet operation and can be equipped with long-life lubrication systems for maintenance-free use.
- Ball Screws: A ball screw assembly uses a nut with recirculating ball bearings rolling along a threaded shaft. It converts rotary motion from a motor into linear movement with high efficiency and accuracy. Ball screws are widely used in CNC machines, electric linear actuators, and any automation requiring precise linear positioning. They offer much higher efficiency than traditional lead screws, which contributes to energy-efficient machine designs. Standard rolled or ground ball screws from brands like NSK and SKF come in various diameters and lead to support different thrust loads and speeds.
- Slewing Ring Bearings: Also known as turntable bearings, slewing rings are large-diameter bearings often incorporating internal or external gears. They can support heavy axial, radial, and moment loads. Slewing rings are used in robotics (for base rotations or large arm joints), as well as in cranes, turret assemblies, and heavy material handlers. Their ability to carry tons of load while enabling rotation makes them ideal for heavy-duty, slow-turning applications where positioning accuracy is important. For instance, a slewing ring might allow a robot to rotate a car body in an assembly station or enable an automated crane to swivel smoothly.
- Crossed Roller Bearings: These compact bearings contain cylindrical rollers arranged perpendicular to each other in an alternating pattern. The design gives crossed roller bearings extremely high rigidity and the capacity to carry forces from all directions (radial, axial, and moment) in a single unit. They are commonly used in robotic joints, indexing tables, and precision rotary stages – wherever space is limited but high stiffness and accuracy are required. A crossed roller bearing can replace multiple conventional bearings in a machine design, contributing to a more compact footprint and higher precision in motion control systems.
- Pillow Block and Mounted Bearings: Pillow block bearings are bearings housed in a solid base (often cast iron or cast aluminum) that can be easily mounted to frames or chassis. They simplify the installation of shafts for conveyors, rollers, gearboxes, or other rotating shafts in automation equipment. Inside a pillow block is typically a deep groove ball bearing or spherical roller bearing that may allow a bit of self-alignment. Pillow blocks are favored in material handling and general machinery for their ease of use – they come pre-assembled and often pre-lubricated. By securing rotating shafts in the correct position, pillow blocks help maintain alignment and reduce vibration in high-speed conveyor lines and drive systems.
Each of these bearing types plays a specialized role in automation. A given system often combines several kinds – for example, a robotic linear module might use a ball screw (with thrust bearings to support it) plus linear guide bearings to carry the load, and a coupling to connect the motor, all working in concert.
Design Advantages of Precision Bearings in Automation
Modern precision bearing technologies confer numerous design advantages that help automation systems achieve exceptional performance:
- High Stiffness and Load Capacity: Advanced bearings (like crossed rollers or large slewing rings) provide high rigidity, which minimizes deflection under load. This is crucial for maintaining accuracy in robot arms or gantry systems that handle heavy payloads. High load capacity extends service life by preventing premature wear when bearings are subjected to continuous or shock loads.
- Compact Footprint: Many specialized bearings condense functionality into a small package. For example, thin-section bearings and integrated bearing units allow machine designers to save space and weight. A crossed roller bearing in a robot joint can handle multi-directional loads in one slim unit, reducing the need for multiple bearings and keeping robot wrists and actuators lightweight and compact.
- Low Noise and Smooth Operation: Precision bearings are finely machined and often incorporate optimized raceway geometry and ball/roller complements to run quietly. In automation equipment (especially in medical or laboratory automation, or collaborative robots working near people), low noise and smooth motion are important quality factors. The use of high-quality lubricants and proper seals also contributes to quieter operation by reducing friction and preventing contamination.
- Long Service Life and Reliability: Industrial-grade bearings are engineered for durability, using high-purity steels, heat treatments, and precise geometries that distribute loads evenly. Many can easily exceed tens of thousands of hours of operation with minimal maintenance. For instance, the use of sealed and pre-lubricated bearings means the internal components are protected from dust and debris and are lubricated for life, achieving longevity even in harsh environments. Reliable bearings translate directly into higher machine uptime and lower maintenance costs, as machines can run continuously without frequent bearing replacements.
- Maintenance-Free or Low-Maintenance Designs: Automation designers increasingly opt for bearing solutions that require little to no periodic maintenance. Innovations such as NSK’s optional K1 lubrication units on linear guides provide a built-in oil supply that ensures long-term operation without re-greasing. Self-lubricating bearing materials (e.g., certain polymer bushings) and sealed-for-life bearings remove the need for manual lubrication. Additionally, automated lubrication systems (like those offered by SKF) can continuously lubricate bearings in critical equipment, “eliminating downtime for re-lubrication” and extending component life. By reducing maintenance demands, these features make automation systems more flexible (machines can run longer between service intervals) and more cost-effective over their lifespan.
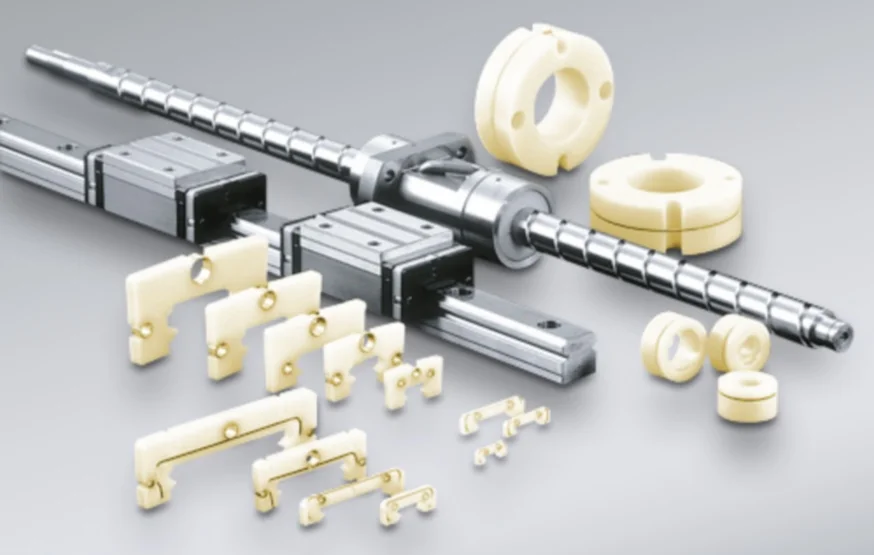
Collectively, these design advantages enable more energy-efficient, precise, and flexible motion control in industrial automation. High stiffness and precision mean robotic motions can be finely controlled with minimal error, while low friction and proper lubrication mean motors consume less energy to overcome resistance, improving overall energy efficiency of the system. Maintenance-free bearings allow production lines to be reconfigured or run for long stretches without intervention, adding flexibility to operations. In short, advanced bearing technology empowers engineers to create automated machines that are faster, more accurate, and more reliable than ever before
Please contact us at [email protected] or call us at 1-800-228-8895.