Grease and oil or dry lubricant are critical in maintaining the functionality and longevity of bearings.
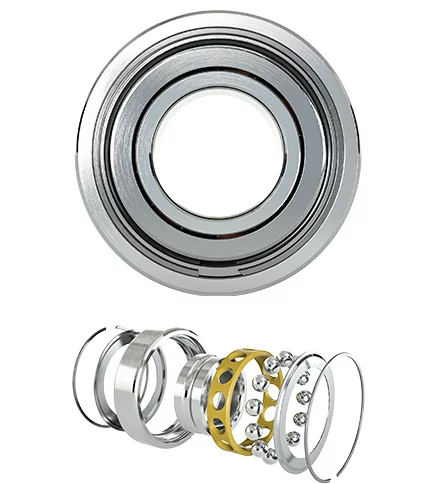
Without proper lubrication, bearings will have increased friction and wear, leading to overheating and premature failure. Lubrication reduces friction and wear by penetrating around the bearing’s rolling elements and raceways, which are the components that allow the bearing to rotate smoothly.
Understanding the importance of lubrication and selecting the appropriate lubricant for each specific bearing application is essential. Proper lubrication helps maintain optimal performance and minimizes maintenance costs.
In this article, we will delve into the various aspects of lubrication for bearings and provide valuable insights into prolonging bearing life.
Structure of Bearings
Before we dive into the details of lubrication, it is important to understand the basic structure of bearings. Bearings consist of an inner and outer ring, ball or roller separator cage, seals or shields, and lubrication. The rolling elements are responsible for carrying the load and allowing the bearing to rotate with minimal friction. Rolling elements in bearings are usually steel or ceramic.
Bearings come in various shapes and sizes, and their structures can vary depending on the intended application. Modern bearings usually have cages separating the rolling element, but some bearings use no separator. Proper lubrication helps to reduce friction and wear between these components, minimizing the risk of failure and extending the lifespan of the bearing.
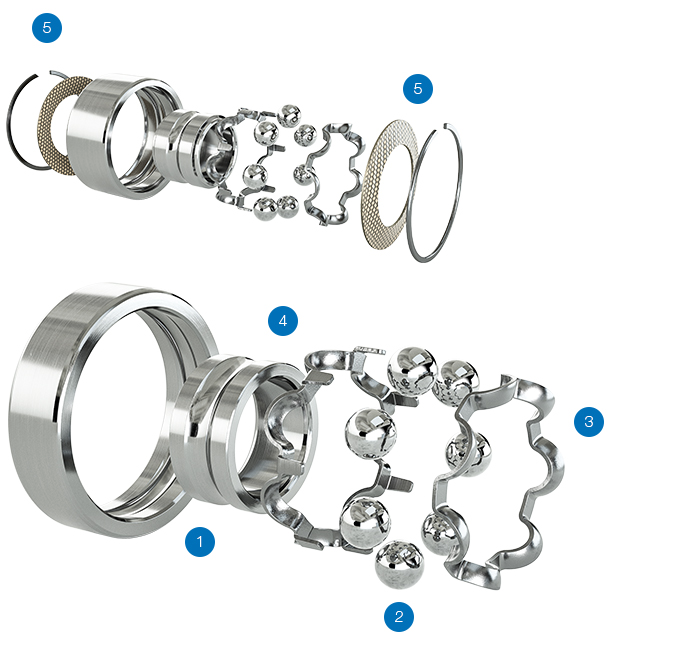
Lubrication Methods for Bearings
Lubrication methods vary depending upon the application, but generally, bearings are greased, oiled, use a solid film, or are air lubricated. The choice of lubrication method depends on a range of factors, including the application, bearing location, the load and speed, and the operating conditions.
Grease lubrication
Grease is a semi-solid lubricant that consists of oil, thickener, and additives. It is easy to handle, reduces friction and wear, and provides sealing properties. Grease lubrication is suitable for applications with low to moderate speeds and moderate loads.
Oil lubrication
Oil lubrication is applied as thin film to the bearing surface. It provides excellent lubricity and cooling properties, making it suitable for high-speed and high-load applications. Oil lubrication can be done through splash, mist, or circulation methods.
Circulating oil lubrication
With this method, the oil required to lubricate the bearings is collected in a sump. From this sump the oil is conveyed from pipes and pumps to the various bearing positions and is highly effective when heat dissipation is required. The oil sump must be adjusted for heat dissipation requirements before using this method. Additional oil coolers can be built into the oil circuit if necessary. In any case, the oil sump must be large enough so that most of the bearing is lubricated. Before the oil is circulated in the lubrication system, it must be filtered to prevent any contaminants from entering the bearings.
Solid film lubrication
Solid film lubrication involves the deposition of a solid lubricant film onto the bearing surface. The solid lubricant reduces friction and wear, improves surface finish, and provides a protective barrier against contaminants. Solid film lubrication is suitable for applications with low to moderate speeds and loads.
Air lubrication
Air lubrication involves compressed air to reduce friction and wear between the bearing and its mating surface. Air lubrication is suitable for high-speed and low-load applications, such as in aerodynamic bearings.
Oil Mist Lubrication
This method is also suitable for bearings operating at high and very high speeds but requires a compressed air system. In oil mist lubrication, the lubricating oil is evaporated into tiny droplets using an atomizer. The air/oil mixture is then fed into the bearing position, where a continuous flow lubricates and cools the bearing.
Factors Affecting Lubrication Performance
The performance of lubrication in bearings depends on several factors, including load and speed, temperature, contamination, and lubricant selection.
1. Load and speed
The load and speed of the bearing affect the thickness and distribution of the lubricant film. Higher loads and speeds require thicker and more uniform lubricant films to prevent metal-to-metal contact and reduce wear.
2. Temperature
The operating temperature affects the viscosity and flow properties of the lubricant. Elevated temperatures can cause the lubricant to break down, resulting in poor lubrication and increased wear.
3. Contamination
Contaminants such as dust, dirt, and water can reduce the effectiveness of lubrication and increase wear. Proper sealing and filtration systems can prevent contamination and prolong bearing life.
4. Lubricant selection
The choice of lubricant depends on the operating conditions, such as temperature, load, and speed. The lubricant should have the right viscosity, additives, and compatibility with the bearing materials.
Impact of Lubrication on Bearing Performance
Proper lubrication is critical for maintaining the performance and longevity of bearings. The benefits of good lubrication include improved wear resistance, reduced friction and heat generation, and extended bearing life.
- Improved wear resistance
Lubrication reduces wear by providing a protective barrier between the bearing and its mating surface. It also helps to distribute the load and reduce stress concentrations on the bearing surface.
- Reduced friction and heat generation
Lubrication reduces friction by providing a low-friction barrier between the bearing and its mating surface. It also helps to dissipate heat and prevent overheating and premature failure.
- Extended bearing life
Proper lubrication helps to extend the life of bearings by reducing wear, friction, and heat generation. It also prevents contamination and helps to distribute loads evenly across the bearing surface. Regular maintenance and monitoring of lubrication performance can help to detect issues early and prevent costly bearing failures.
Conclusion
In conclusion, lubrication is a critical aspect of bearing performance and longevity. The choice of lubrication method and lubricant depends on several factors, including the application, load, speed, and temperature. Proper lubrication helps to reduce wear, friction, and heat generation, while extending bearing life. It is essential to monitor lubrication performance regularly and address any issues promptly to prevent bearing failures and costly downtime.
Contact us for assistance in selecting the proper lubrication for your application.