C-3 versus standard clearance is simply that C-3 is looser having more play than a standard fit bearing. Each application determines the fit clearance so the designer will determine tolerances and fits . The performance of a bearing in most applications is based on a bearing reaching zero clearance after installation.
Below is an explanation for the different fit types and clearance used in conjunction with how fits are determined.
Bearing Interference, Slip, and Transition Fits Explained.
What is meant by an interference, slip, or transition fits for bearings?
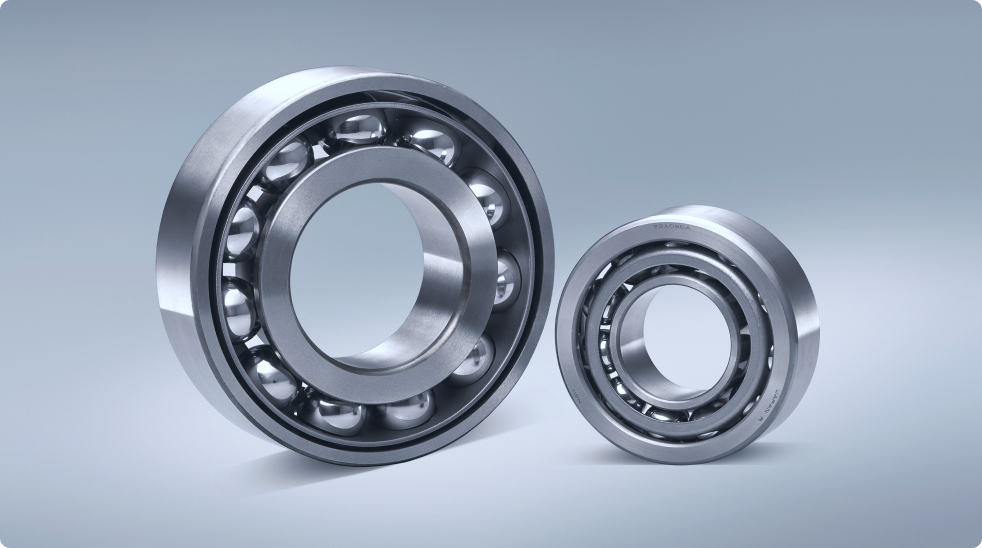
Bearings need to be able to operate in any environment and are precisely designed to fit on shafts and into housings to function efficiently.
Establishing accurate shaft and housing fits is essential to achieving the best possible bearing performance. Many issues occur in applications where fits are too loose or tight. Improper fits can cause excessive wear, poor bearing rotation, excessive vibration, noise, unwanted pre-load, overheating, and reduced radial play.
Once the design of the bearing has been established it must be fitted properly during mounting.
Now let’s talk about the difference between interference, slip and transition fits.
A slip fit is something that can be as easy to understand as pulling on a pair of socks. There is slight resistance when slipping the bearing bore over the shaft or the outer race into the housing.
An interference fit would be something like trying to pull a soaking wet sock on.
There is resistance between your foot and the sock. When tolerance differences are tight between the outer race and the housing or the inner race and the shaft, force is required to push the parts together.
A transition fit is somewhere between the slip and interference fit, as if the sock is drying out.
In general, bearings can be mounted by using a press or interference fit.
As a rule, the rotating ring of the bearing requires an interference fit using the housing or the shaft. The fixed ring is usually a loose fit with the mating part.
Bearings are manufactured with a certain amount of radial and axial play, also known as clearance. This free space in the bearing is where the ball in the raceways can move up, down, or sideways.
How do you get rid of this free space?
The fits reduce this play or leave it as designed depending upon the operating conditions and the objective of the design engineer, whatever meets the best operation for the application. In addition to the fitting of the bearings into the housing or onto the shaft, a preload can be applied to the axis of the bearing to limit the side movement or axial play.
All manufacturers make recommendations for shaft and housing fits dependent upon the type of bearing specified. Pressing a bearing into its location may require special tooling and must be done to avoid damage to the bearing balls, races, and cage. View this SKF’s instructional video on installing bearings, as it demonstrates numerous ways to mount bearings.
There are many steps involved in the bearing selection process.
Before you arrive at picking the fits in a bearing you must follow these steps to get there. First you must determine the performance requirements and operating conditions. Only after selecting the bearing type, size, and lubrication and understanding operating temperature and speed can help correctly identify the fits needed.
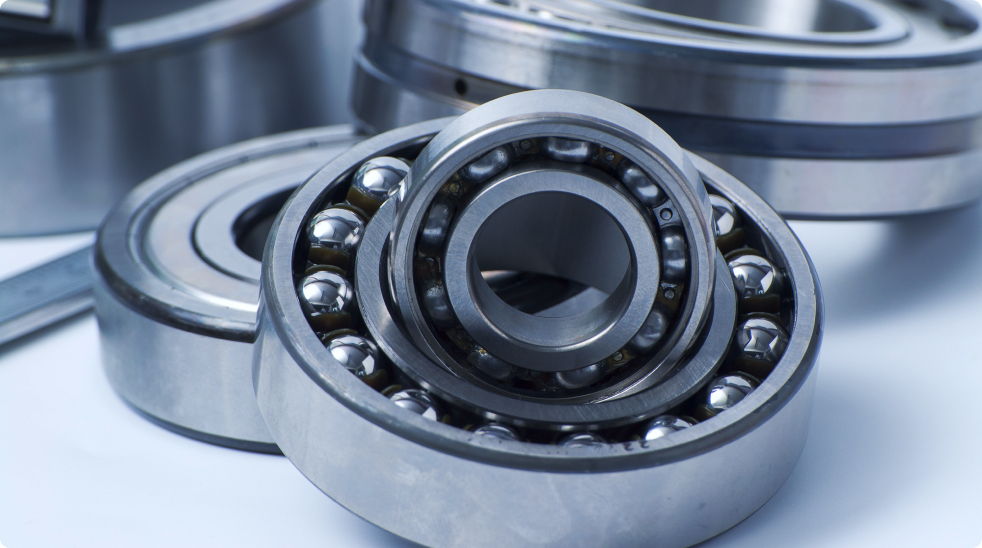
In this step, bearing seats are especially important in determining performance. Bearing seats support the bearing’s circumference across the entire width of the raceway.
Bearing manufacturers such as SKF make recommendations and set requirements for designing bearing interfaces. I recommend visiting any one of these fantastic manufacturing sites for fit charts. Below is one such example for selecting fits from SKF.
When selecting fits, it is best to follow the recommendations of the manufacturer. While many of the applications are covered, you will still need to adjust to your specific use case.
Some common considerations for selecting fits are as follows:
- Conditions of rotation
- Magnitude of load
- Temperature differences
- Precision requirements
- Design and material of the shaft and housing
- Ease of mounting and dismounting
- Axial displacement of the bearing in the non-locating position
Dimensional tolerances for bearing seats are dictated by the required fit.
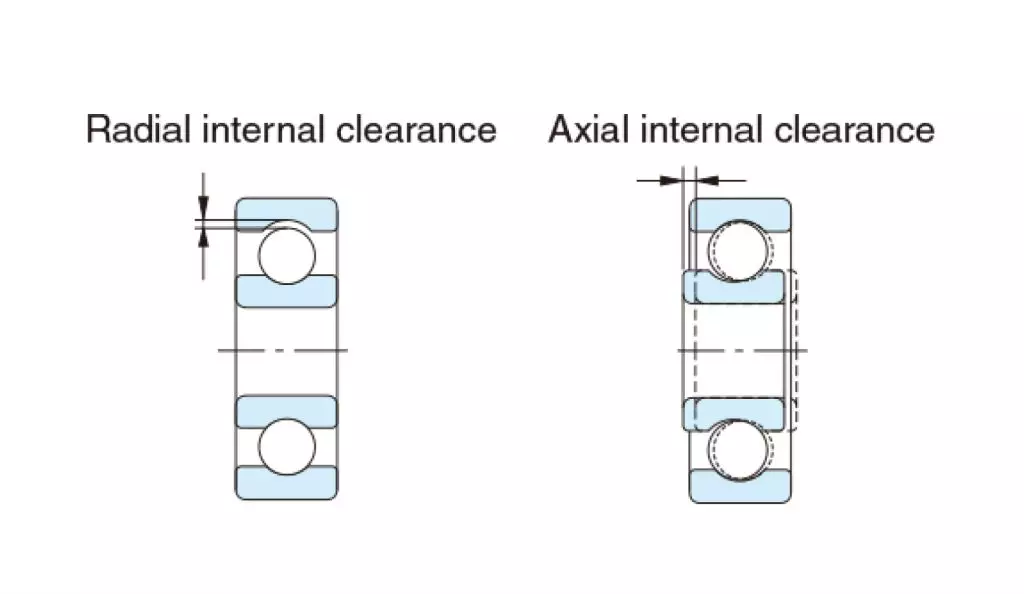
The application’s requirements will determine the bearing tolerance class needed. In this link to SKF, the tables provide information about bearing tolerances, seat tolerances, and resultant fits. You can use these tables to determine fit values. You can also use other manufacturers’ tables to estimate the engineering aspect for determining fits for your specific application. SKF, INA, FAG and others are focused on larger, more industrial bearings whereas NMB and NHBB are focused on smaller, lighter, and narrower width bearings. Care must always be given when fitting up bearings but particular care must be taken with small or miniature bearings, as they can easily be damaged due to their smaller cross sections.