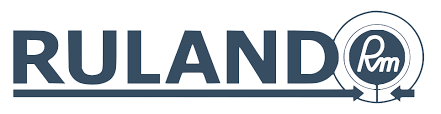
Modern high-tech applications demand motion components that deliver extreme precision and reliability. In industries like test & measurement instrumentation, automated inspection systems, semiconductor fabrication, and medical devices, even the slightest mechanical “play” can lead to positioning errors or inconsistent results. This is why Ruland backlash-free couplings (also known as zero-backlash couplings) have become essential in advanced motion control. They ensure that when a motor turns, its counterpart turns exactly in step with no lost motion or slop. For example, if a servo motor shaft rotates 90°, a zero-backlash coupling guarantees the driven shaft also rotates 90° with no play between components. By eliminating backlash, these couplings provide the precise, repeatable performance that high-tech servo systems require for accuracy and high-speed responsiveness.
Overview: Zero-Backlash Couplings in Advanced Motion Control
Advanced technology applications typically run at high speeds and require tight tolerances – conditions under which conventional couplings can introduce vibration, misalignment forces, or backlash. Ruland Zero-backlash couplings are specifically designed to address these issues, making them invaluable in applications from liquid handling robots and packaging automation to solar panel assembly and laboratory instruments. Ruland couplings feature balanced designs that minimize vibration at high rotational speeds, so systems like precision conveyors or scanning devices operate more smoothly. Equally important, most backlash-free coupling designs can accommodate misalignment between shafts without generating large reaction forces. Small misalignments are inevitable in complex machinery (due to frame machining tolerances or thermal expansion of components), and if not handled, they can cause bearing overload or wear. Backlash-free couplings such as the Oldham style excel at handling parallel misalignment in particular – they allow a significant offset between shafts while imparting only light reaction loads on bearings. This flexibility protects sensitive motor and driven components, reducing wear and maintenance needs in the long run. In short, zero-backlash couplings enable engineers to build highly precise motion systems that are also robust to alignment inaccuracies and high-speed operation.
Another key design consideration is torsional stiffness (rigidity). High torsional rigidity means the coupling twists very little under load, which is critical for motion accuracy during rapid moves. For instance, a scanning-type motion system (such as continuous imaging or laser scanning equipment) must maintain accuracy even while moving, which “necessitates a coupling with high torsional rigidity” to prevent any wind-up or lag. All-metal coupling styles like disc-pack couplings are known for their exceptionally high torsional rigidity and zero backlash, making them popular in many servo motor-driven axes. However, such rigid designs tolerate only very small misalignments. In practice, engineers often choose a coupling type that balances torsional rigidity with needed misalignment flexibility and damping. Ruland Manufacturing addresses this by offering six types of zero-backlash couplings – including rigid, beam, bellows, disc, curved jaw, and Oldham styles – each suited to different performance needs. This wide selection allows designers in high-tech industries to pick a coupling that best fits their application’s mix of precision, speed, misalignment, and torque requirements.
Why choose Ruland’s zero-backlash couplings for high-tech applications? Ruland’s couplings are specifically engineered for precision motion control. Some notable advantages include:
Balanced, high-speed design: Ruland couplings are precision machined for balance, which reduces vibration at high RPM. This is crucial for applications like high-speed inspection cameras or printing systems where smooth operation improves accuracy and longevity.
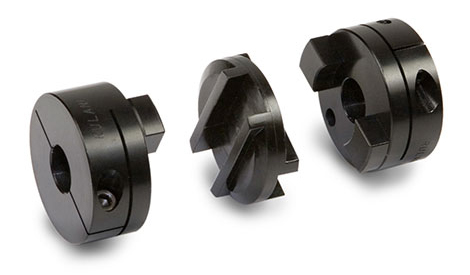
Wide range of coupling styles: Ruland is unique in manufacturing six different zero-backlash coupling types, from flexible beam and Oldham couplings to rigid and bellows couplings. This means an engineer can find a perfect fit, whether the priority is misalignment accommodation, ultra-high torsional rigidity, minimal inertia, or a combination of these.
Custom and special designs: Beyond standard offerings, Ruland can provide special designs on request – for instance, custom bore sizes or geometry tweaks – to meet unusual requirements often encountered in cutting-edge equipment.
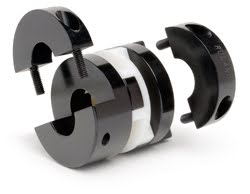
Quality manufacturing and fast availability: All couplings are carefully made in Ruland’s Marlborough, MA facility to strict quality standards and are RoHS3 and REACH compliant. Tight in-house control means these high-quality components are in stock for immediate delivery in most sizes, minimizing downtime for project development or maintenance.
Backlash-free couplings play a vital role in high-tech applications, so choosing the right type is important. Below, we look at two popular Ruland coupling styles – Oldham and beam couplings – and how their design benefits demanding applications.
Oldham Couplings: Zero Backlash with Misalignment Flexibility
Oldham couplings are a three-piece coupling design that provides zero-backlash torque transmission while allowing considerable misalignment between shafts. Each Oldham coupling consists of two metallic hubs (typically aluminum or stainless steel) with drive tenons that interlock with a middle floating disk (often made of plastic). When assembled, the disk slides between the hubs’ tenons to transmit torque. This clever arrangement yields several engineering benefits:
- High Parallel Misalignment Capacity: Oldham couplings excel at handling parallel shaft offsets far beyond what most other coupling types can tolerate. The floating disk can slide to compensate for misalignment without significant resistance, allowing offsets on the order of 5–10% of the coupling diameter in many cases. Because the disk glides rather than bends, the coupling imposes only minimal reaction forces on the shafts. As a result, bearings and motor mounts see very light loads, avoiding the excess wear that misalignment usually causes. This makes Oldham couplings invaluable in equipment where precision alignment is hard to maintain, for example, indexing tables or conveyor drives, where frames or shafts may shift over time.
- Zero Backlash & Constant Velocity: With a properly fitted center disk (usually an acetal plastic disk for high precision), an Oldham coupling transmits motion with zero backlash, meaning no lost motion or “wind-up.” The two halves are always positively engaged through the disk, so there is no play as the direction of rotation changes. This ensures precise, repeatable positioning – a critical feature in applications like packaging machines and medical dosing devices that require accurate start-stop indexing. Additionally, Oldham couplings transmit motion at constant velocity (no oscillation), so stepper or servo-driven systems maintain synchronicity between motor and load during dynamic moves.
- Vibration Damping & Shock Protection: The center disk can be made from different materials (most commonly acetal or nylon), allowing the user to tune the coupling’s torsional softness. An acetal disk is relatively stiff (high torsional rigidity) and gives the coupling crisp, accurate motion. A nylon disk, on the other hand, is more compliant and can absorb vibrations and shocks. In high-tech systems that experience frequent start-stop cycles or sudden load changes, such as pick-and-place robots or syringe pumps, a nylon Oldham insert can dampen impact loads, smooth operation, and protect the motor. Importantly, Oldham’s three-piece design is inherently balanced and can run at speeds up to ~6,000 RPM without vibration issues, well above the range of most servo motors in practice.
- Electrical Isolation & Fail-Safe Safety: Because the torque-transmitting disk is non-metallic, Oldham couplings electrically isolate the two hubs. This is a valuable feature in many high-tech and medical devices – it prevents stray currents from traveling between the motor and driven component, which can protect sensitive sensors or eliminate ground loop problems. Moreover, the plastic disk serves as a built-in mechanical fuse: if the system jams or an overload occurs above the coupling’s torque limit, the disk will shear off cleanly, disengaging the drive. This fail-safe mechanism can save expensive components like motors or gearboxes from damage in a crash scenario. Replacing a sheared disk is quick and inexpensive, essentially restoring the coupling to full function on the spot.
- Easy Maintenance & Modular Customization: Oldham couplings are prized for how easy they are to install and service. The two hubs are not permanently joined; they are held together only by the center disk. This means you can separate the hubs by simply sliding out the disk – convenient for maintenance tasks like replacing a motor or servicing a linear stage, since you don’t have to remove the hubs from each shaft. The design is also highly customizable: Ruland offers Oldham hubs in many materials (lightweight anodized aluminum is standard, with stainless steel available for higher torque or corrosive environments) and in both clamp-style and set screw-style attachments. You can mix or match hub types, bore sizes, and even combine inch and metric bores or keyed and keyless hubs in one coupling. Customers have over 25,000 possible standard hub/disk combinations to choose from when specifying a Ruland Oldham coupling. This modular approach makes it easy to tailor the coupling to your machine’s shafts without special machining. Many engineers also value that Oldham couplings from Ruland are low inertia (thanks to aluminum hubs and a lightweight plastic disk) and economically priced, making them a cost-effective choice for both misalignment-critical and general-purpose applications.
With these characteristics, Ruland Oldham couplings have found homes in a wide array of high-tech applications. They are used in precision conveyors, automated printing and labeling machines, lab automation equipment, and even some robotic systems – anywhere that parallel misalignment might be present or easy servicing and zero-backlash operation is needed. Their torque capacities cover a broad range: for instance, standard Ruland Oldham couplings can handle from as low as ~6 lb·in up to about 130 lb·in continuously in mid-range sizes, and up to 375 lb·in for the largest sizes with an acetal disk(~42 N·m). This range means a properly selected Oldham coupling can connect everything from a tiny stepper motor in a microscope stage to a larger servo motor in a semiconductor wafer handler. The combination of zero-backlash precision, misalignment forgiveness, and safety makes Oldham couplings a versatile solution for advanced motion control.
Beam Couplings: Lightweight, Zero-Backlash Couplers for Compact Systems
Example of Ruland zero-backlash beam couplings (multiple-beam helical design) in various sizes. These one-piece couplings have spiral cuts that allow flexibility while maintaining torsional stiffness. Smaller four-beam versions are often used for encoders and instrument drives, while larger six-beam versions can connect servo motors to lead screws.
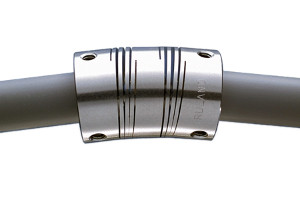
Another common backlash-free coupling used in high-tech machinery is the helical beam coupling (often just called a beam coupling). Unlike the three-piece Oldham design, a beam coupling is made from a single continuous piece of metal (typically aluminum or stainless steel) with a series of spiral cuts machined through it. The helical cut pattern turns the solid metal into a spring-like form that can twist and bend slightly. Beam couplings are zero-backlash by design – the one-piece construction means no free play – and their elasticity allows them to accommodate misalignment by flexing. Ruland manufactures beam couplings in two main configurations: four-beam couplings for smaller shafts and lighter torques (commonly used for encoders and light instrumentation), and six-beam couplings with longer bodies for higher torque transmission, such as connecting servo motors to lead screws. The beam couplings’ ability to bend in multiple directions lets them handle all forms of misalignment (angular, axial, and a small amount of parallel) in a single compact unit.
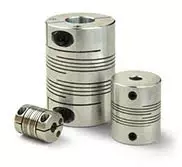
Despite being elastic, modern beam couplings can be engineered to be fairly stiff torsionally. Ruland’s proprietary multi-beam designs, for example, have higher torque capacity and torsional stiffness than commodity single-slit couplings. The six-beam “F-series” couplings feature two sets of three helical cuts, which effectively makes them stronger and more rigid under twist while still flexible for misalignment. This gives greater accuracy and repeatability in motion control, which is why these couplings are promoted for robotics and servo-driven systems. At the same time, beam couplings introduce a gentle restoring force when flexed, so it’s best to use them for moderate misalignments (on the order of a few thousandths of an inch). They excel in scenarios where alignment is good but not perfect, and you want to avoid the complexity of a multi-piece coupling. One caveat: if over-stretched by too much offset, beam couplings will exert increasing force on shafts (like a spring), potentially raising bearing loads. In practice, keeping misalignment within recommended limits (and choosing a longer or multiple-beam version for greater compliance) makes this a non-issue for most applications.
The simplicity of beam couplings brings several advantages aligned with high-tech requirements. They have very low inertia, being made of a single aluminum piece, which means they don’t add burden to the motor during high-acceleration moves. This is beneficial for fast reciprocating motions (for example, in pick-and-place machines or rapid scanning devices) because the coupling won’t significantly slow the system’s response. Beam couplings are also maintenance-free; with no moving parts or wear components, they can operate indefinitely without attention. They are frequently used in sensitive systems like encoders, tachometers, and measuring instruments, where their lightweight and zero backlash ensure the signal fidelity is maintained. Ruland’s beam couplings, in particular, are designed for high RPM operation – their balanced one-piece construction allows them to run up to ~6,000 RPM smoothly. This makes them suitable for high-speed applications such as centrifuges or spindle drives in which other flexible couplings might introduce vibration.
Ruland offers beam couplings in a variety of sizes and materials to suit different needs. Standard bore diameters range from 3/32″ up to 3/4″ (2 mm to 19 mm), covering very small shafts (think micro motors in optical equipment) through to medium-sized motor shafts. Aluminum beam couplings provide the lowest inertia and are common in most setups, while stainless steel beam couplings are available when higher torque capacity or temperature resistance is required. Designers can choose between clamp-style hubs or set screw hubs on the ends, and even mix inch-to-metric bore combinations in the same coupling to join dissimilar shafts. Notably, Ruland’s beam couplings also incorporate an anti-vibration hardware feature on clamp screws (a nylon patch to prevent loosening) in some models, which is an extra assurance for long-term reliability in vibrating environments.
Beam couplings are commonly found in highly automated systems that demand both precision and compactness.
For example, in surgical robots and laboratory automation equipment, beam couplings are used to connect servo motors to lead screws or linear actuators, where their combination of torsional stiffness and flexibility is well-suited to the fine motions required. In pick-and-place gantries or semiconductor wafer handling arms, they can accommodate slight misalignments between the motor and slide without backlash. And in devices like 3D printers or CNC engraving machines, beam couplings precisely transmit motor rotation to lead screws or drive shafts, ensuring printed layers or machined features align perfectly. While beam couplings might not handle as much misalignment or torque as an Oldham or disc coupling of comparable size, their one-piece simplicity, zero backlash, and adequate compliance make them a go-to solution for many medium-duty, high-speed positioning systems in the high-tech arena.
How to Choose Zero-Backlash Couplings
As an engineering or procurement professional working on high-tech equipment, once you’ve determined the ideal coupling type and size for your application – be it an Oldham coupling for misalignment forgiveness or a beam coupling for a small precision motor, or any other Ruland zero-backlash style – the next step is to source it efficiently. PIB Sales is a trusted distributor of Ruland Manufacturing products and makes it easy to get the exact coupling components you need. We maintain a large inventory of Ruland’s zero-backlash couplings and can typically offer fast shipment on common sizes and styles, since these high-quality components are made in the USA and stocked for quick fulfillment.
To streamline your purchasing process, reach out to PIB Sales with your application details or requirements. Our sales and engineering support teams will help verify the appropriate coupling selection – ensuring you have the right size, hub style (clamping or set screw, keyed or keyless), and disk or spider material if applicable, to match your design’s needs. Whether you require a standard aluminum Oldham coupling for a precision indexing table, a stainless steel beam coupling for a cleanroom robot, or even a specialty bellows or disc coupling for a high-torque servo axis, PIB Sales will assist you in identifying the correct Ruland part numbers and options. We then provide a prompt quote with competitive pricing and lead times. Most standard Ruland couplings are in stock at our facility, so you can expect minimal lead time – often your order will ship out immediately or within a very short time frame. Any custom requests (such as non-standard bore diameters or special tolerances) can also be discussed and arranged through our team in coordination with Ruland’s engineers.
Once you place your order, PIB’s shipping department will ensure your Ruland couplings are delivered promptly so you can keep your project on schedule. We will supply documentation you may request, such as product specification sheets or compliance certifications.
Contact PIB Sales today to request a quote or to discuss your motion control application with our knowledgeable staff. We are ready to assist [email protected] in selecting the ideal backlash-free coupling solution from Ruland’s lineup, ensuring your application achieves precision, performance, and reliability.