Grease for Ball and Roller Bearings can be standard or a specialized lubricant formulated to ensure the reliable operation and longevity of ball and roller bearings. Lubrication plays a critical role in reducing friction, protecting against wear and corrosion, and maintaining the efficiency of various machinery and equipment across multiple industries. In this article, we will detail considerations for selecting the right grease, applications, various types, and other factors that influence performance and compatibility with bearings.
Introduction to Bearing Grease Selection
Selecting the right grease for ball and roller bearings is important for smooth operation and maintaining the longevity of machinery. Whether you’re working with heavy-duty industrial equipment or precision machines, the type of grease you choose can significantly impact performance and reliability. Missteps in grease selection or application can lead to excessive wear, overheating, or even failure of the bearing.
Why Proper Lubrication Matters for Bearings
Lubrication isn’t just a maintenance step — it’s the life force of a bearing. When done right, grease minimizes friction, reduces wear, and protects the bearing from contaminants like dirt and moisture. Proper lubrication also helps control temperature by dissipating heat generated through friction. All these factors combine to enhance the efficiency and lifespan of the bearing.
Now, let’s consider some key performance metrics affected by lubrication:
- Friction Reduction: Proper grease creates a thin film between moving surfaces, reducing friction and preventing metal-to-metal contact.
- Load Distribution: The right grease ensures that the load is evenly distributed across bearing components, reducing stress points.
- Corrosion Protection: Bearings exposed to moisture or chemicals need a grease that shields against rust and corrosion.
- Heat Dissipation: High-speed bearings can overheat without the right type of grease to regulate temperature.
Improper lubrication, on the other hand, can lead to significant issues like overheating, contamination, and even bearing seizure. Here are some common pitfalls to avoid:
- Over-lubrication: Adding too much grease can cause churning, leading to excessive heat and reduced bearing performance.
- Under-lubrication: Too little grease results in insufficient film formation, increasing friction and wear.
- Using Incompatible Greases: Mixing grease types can result in chemical reactions that deteriorate the lubricant, compromising the bearing.
Every application has its own unique set of requirements, and choosing the right lubricant should be based on the specific needs of your bearings. For a more detailed look into optimizing lubrication for bearings, visit our Understanding the Importance of Lubrication guide.
Types of Greases for Ball and Roller Bearings
The selection of grease for ball and roller bearings is not a one-size-fits-all decision. It requires an understanding of the specific application. Greases having unique properties can be applied so as to maximize bearing life and performance. Below are some examples of grease types.
Lithium Grease
Lithium grease is the most commonly used lubricant for ball and roller bearings due to its excellent versatility. It has a good resistance to high temperatures and remains stable under varying conditions, making it suitable for a wide range of applications, from automotive to industrial machinery. Its water resistance also makes it ideal for use in environments where moisture is present.
Calcium Sulfonate Grease
Known for its superior corrosion protection and high load-bearing capacity, calcium sulfonate grease excels in marine applications and heavy-duty industrial settings. This grease type stands out for its ability to perform under extreme pressures and in the presence of water, resisting washout and maintaining its protective qualities.
Polyurea Grease
Polyurea grease offers exceptional high-temperature stability and oxidation resistance, which is critical for high-speed bearings in electric motors and automotive applications. Its long service life and minimal bleeding make it a preferred choice for sealed-for-life bearings, where re-lubrication is not feasible.
Synthetic Grease
Formulated with synthetic oils, this type of grease is tailored for extreme temperature conditions, both high and low. Synthetic grease is particularly beneficial in aerospace, cold storage, and high-temperature industrial applications due to its broad operating temperature range. Its enhanced lubricity and chemical stability ensure reliable performance in the most demanding conditions.
Selecting right Grease for Bearings
Selecting the right grease for a bearing requires addressing several factors to ensure peak performance and longer life.

Specify a lubricator that provides the right quantity of grease all the time. Automatic lubrication can cycle or sequence to avoid over-lubrication. Too much lubrication can occur easily when lubricating manually and can lead to bearing failure. Schaeffler has the perfect solution and can be purchased directly from Pacific International Bearing Sales Inc. Contact us at [email protected]
Understanding Grease Consistency and Its Impact
The consistency of grease, essentially its thickness, is quantified using the National Lubricating Grease Institute (NLGI) grading system. This system ranges from 000 (highly fluid) to 6 (extremely stiff). For bearings, the selection often centers around three grades:
NLGI 2 | This is your go-to grade for general bearing applications, offering a versatile balance between fluidity for ease of application and stiffness for staying in place under operational conditions. |
NLGI 1 | Optimal for bearings operating in colder environments or those that see limited movement, this grade ensures adequate lubrication without becoming too stiff. |
NLGI 3 | For bearings in high-temperature environments or subjected to significant vibrations, a stiffer grease maintains its protective layer without breaking down. |
The Role of Oil Viscosity
Base oil viscosity is the backbone of grease’s lubricating performance, determining the thickness of the lubricating film under operational conditions. It’s pivotal to select a grease whose base oil viscosity is appropriate for the bearing’s operational speed and load conditions. Adjustments may be necessary:
- For viscosities below 20 mm²/s at 40°C (104°F), consider a slight increase to ensure a robust lubrication film.
- In the 20 to 250 mm²/s range, standard recommendations generally suffice without alterations.
- Above 250 mm²/s, specialized advice may be warranted to tailor grease selection to specific application demands.
Extreme Pressure additives are essential for bearings operating under high load or shock conditions. These additives form a protective layer on the bearing surfaces, preventing metal-to-metal contact and the resultant wear. However, their use must be balanced against the potential for adverse reactions with bearing materials, particularly at elevated temperatures.
Requirements
Beyond the basics, several application-specific considerations may influence grease selection:
Wide Temperature Operation – bearings functioning across a broad temperature range benefit from greases with a mineral base and lithium complex, ensuring consistent performance from sub-zero to elevated temperatures.
High-Speed and High-Temperature Conditions – synthetic base oils are preferred for stability at extreme temperatures and resistance to breakdown, crucial for bearings in demanding applications.
Severe Loads and Vibratory Conditions – greases fortified with EP additives and robust thickeners, like lithium soap, offer enhanced protection against wear and deformation under heavy loads or in vibrating machinery.
Optimal Grease Application Techniques – the right amount of grease is paramount.
Over-greasing can lead to excessive heat buildup due to the churning of grease, while under-greasing leaves bearings vulnerable to premature wear and failure. A general rule of thumb is to fill the bearing’s free volume (the space between the balls and races) to about one-third full for optimal performance. For sealed bearings, manufacturers often pre-fill the correct amount, eliminating the guesswork.
To calculate the optimal amount of grease required for a bearing, the following formula can be applied:
Grease Quantity (g)=Bearing Outside Diameter (mm) + Bearing Width (mm) / 2×Bearing Factor
The bearing factor is determined by the bearing type and its size, which can usually be found in the manufacturer’s catalog or technical guidelines.
The re-lubrication frequency depends on the bearing size, speed, and operating conditions. A common method is to use calculation tools or charts provided by bearing and grease manufacturers, which consider these factors to recommend intervals. Always monitor the bearing’s condition and environmental influences, as these may necessitate adjustments to the re-lubrication schedule.
After the initial grease fill, the re-lubrication intervals depend on various factors, including the bearing size, type, speed, and operating conditions. While specific formulas can vary based on bearing design and application, a typical formula to estimate the re-lubrication interval might look like this:

Where:
- f = A factor based on the type of bearing and grease used (consult manufacturer’s guidelines)
- B = A base number from bearing specifications or empirical data
- n = Rotational speed in rpm
- dm = Mean diameter of the bearing in mm, which is the average of the bearing’s inside (d) and outside (D) diameters ( dm=0.5× (d+D)
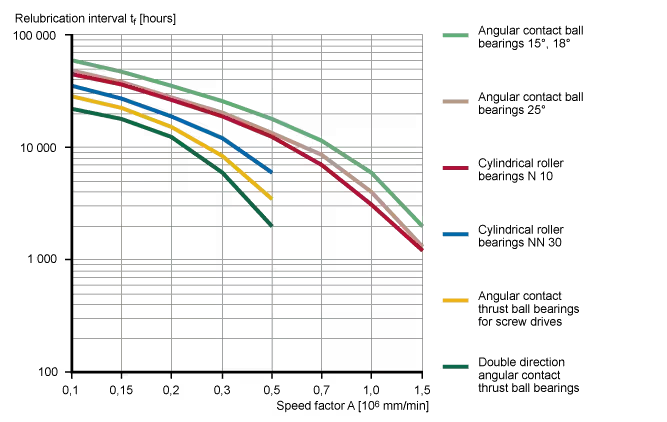
Proper grease application involves more than just adding grease. Follow these steps for effective lubrication:
- Ensure the grease gun and area around the bearing are clean to avoid introducing contaminants that can damage the bearing.
- Check that the new grease is compatible with any residual grease in the bearing or housing to prevent degradation of lubricating properties.
- Use a grease gun for precise application, aiming the grease directly into the bearing or onto the grease nipple, if present. For manual application, wear gloves and apply the grease evenly around the bearing elements.
- Slowly rotate the bearing as you apply grease to ensure even distribution within the bearing. This helps in achieving a uniform coating over all rolling elements and races.
Grease Lifespan and Performance
The foundation of maximizing grease lifespan begins with proper storage. Grease should be stored in a cool, dry place away from direct sunlight and extreme temperatures, which can degrade its quality. Containers should be sealed tightly to prevent contamination and oxidation. Ideally, store grease in its original packaging until it’s ready to be used, and always use older stocks first (FIFO – First In, First Out principle).
Monitoring the condition of the grease can help identify contamination, separation, or degradation before they impact bearing performance. Techniques such as visual inspections, sampling, and analysis can provide valuable insights into the grease’s condition and the need for replacement.
Grease lifespan is closely linked to operating temperatures. High temperatures can accelerate the degradation and evaporation of the base oil, reducing the grease’s lubricating properties. Ensuring that machinery operates within recommended temperature ranges can help preserve grease life. In cases where high temperatures are unavoidable, selecting a grease with a high dropping point and good thermal stability is crucial.
Implementing a lubrication analysis program can significantly extend grease life and enhance bearing performance. Regular analysis of grease samples can detect changes in viscosity, contamination levels, and wear particles, providing early warning signs of potential issues. This proactive approach allows for timely interventions, such as cleaning or re-lubrication, to maintain optimal lubrication conditions.
Common Mistakes in Bearing Lubrication
Lubricating bearings might seem straightforward, but even small missteps can lead to major issues. From breakdowns in equipment to shortened bearing life, improper lubrication is one of the leading causes of bearing failure. Let’s explore some frequent mistakes and the ways they impact bearing performance.
Using the Wrong Grease Type
Not all greases are suitable for every bearing application. Many people make the mistake of selecting a grease without considering key factors like operating temperature, load, or speed. Using the wrong grease type can cause a range of problems, such as poor lubrication, increased wear, and even complete bearing failure. Think of it like choosing the wrong fuel for a car—it won’t run properly and can even cause damage.
For example, using a grease meant for high-speed applications in heavy-load conditions often results in film failure, leading to increased friction and overheating. It’s essential to check for compatibility with your bearing’s operating environment before settling on a grease. You can find more details on how to choose the right grease type by reading this detailed guide.
Mixing Incompatible Greases
Greases are crafted with unique formulations, including different thickening agents, oils, and additive packages. Mixing two incompatible greases can lead to a chemical reaction or breakdown, creating a compound with completely different properties. This often leads to poor lubrication performance, contamination, and even hardening or softening of the grease, which compromises the bearing’s functionality.
Think of it this way: combining incompatible greases is like mixing oil and water—it doesn’t work. In industrial applications, using multiple grease types should be carefully planned or entirely avoided. If it’s necessary to switch to a new grease, cleaning the old grease out thoroughly before applying the new one is crucial. For further understanding of bearing lubrication strategies, visit our lubrication guide.
Applying Too Much or Too Little Grease
Striking the right balance in the amount of grease applied is critical. Here are some common scenarios and their consequences:
- Over-Greasing: While it may seem logical to add more grease for better performance, over-greasing often causes excessive heat and friction within the bearing. This happens because the extra grease creates churning, increasing resistance and degrading the grease more quickly. One practical example includes overheating bearings in motor applications due to grease overflow.
- Under-Greasing: On the flip side, insufficient grease prevents a complete lubricating film from forming, leading to direct metal-to-metal contact. This causes higher friction, wear, and ultimately, bearing failure. In applications with high-speed rotations, under-greasing becomes particularly problematic, accelerating wear and tear.
To avoid these issues, stick to manufacturer guidelines for lubrication amounts. Regular maintenance checks are also a smart way to ensure the correct grease levels. For tips on proper bearing maintenance, check out our maintenance guide.
Mistakes in lubrication are easy to make, but they’re also avoidable with knowledge and the right approach. Always consider the specific needs of your bearing application, and align your lubrication practices to match.
FREQUENTLY ASKED QUESTIONS
Selecting the right grease for ball and roller bearings can feel overwhelming. With so many options, specifications, and factors to consider, it’s no surprise that questions abound. To help clear up any confusion, here are responses to some of the most frequently asked questions about bearing grease selection.
Q: What Type of Grease Should I Use for My Bearings?
A: The type of grease you choose depends on several factors, including operating temperature, speed, and load. A good starting point for most applications is a lithium-based grease because of its versatility and resistance to water and corrosion. It works well in a wide range of conditions and is widely available. For more specialized needs, high-temperature greases or those with extreme pressure (EP) additives may be required. Explore our guide on high-temperature bearings for more details.
Q: How Often Should Bearings Be Greased?
A: The frequency of lubrication depends on the application and the operating environment. Bearings in high-speed machinery or heavy-load conditions may require more frequent re-lubrication compared to slower, lighter applications. It’s important to follow the manufacturer’s specifications and inspect bearings regularly. For guidelines on optimizing maintenance schedules, refer to our bearing maintenance guide.
Q: Can I Mix Different Types of Greases?
A: Mixing greases is not recommended. Different greases have unique chemical compositions and thickening agents, and mixing them can lead to chemical incompatibility. This often results in performance degradation, grease hardening, or even bearing failure. If you need to switch greases, thoroughly clean the bearings to remove any residue of the old grease. Learn more about this topic in our section on common lubrication mistakes.
Q: What Happens if I Use the Wrong Grease?
A: Using the wrong grease can cause inadequate lubrication, overheating, or bearing wear. For example, a grease intended for high-speed applications might break down under heavy loads, while a thick grease might cause excessive resistance in high-speed machinery. Always check the grease specifications and ensure compatibility with your bearing’s operating conditions. For additional tips, visit our comprehensive guide on grease selection.
Q: How Do I Know if My Bearings Are Properly Lubricated?
A: There are some signs to watch for when determining if your bearings are lubricated correctly:
- Excessive Noise: Dry bearings often sound louder due to insufficient lubrication.
- Excess Heat: Overheating can indicate too much or too little grease.
- Grease Leaks: Leakage may mean over-lubrication or failing seals.
If you notice any of these issues, it’s time to inspect and relubricate your bearings. Learn how to address these challenges in our troubleshooting guide.
Q: What Is NLGI Grade, and Why Does It Matter?
A: The NLGI (National Lubricating Grease Institute) grade measures the consistency of a grease, ranging from 000 (fluid-like) to 6 (solid-like). Bearings typically require NLGI Grade 2 grease, as it provides a balanced consistency suitable for most applications. Think of it as choosing between peanut butter and jelly—both may be spreadable, but each has its place. If you’re unsure which grade you need, check your bearing manufacturer’s recommendations.
Proper grease selection might feel like an art, but with the right information at your fingertips, it becomes a science. These FAQs cover the basics, but always consult technical data sheets or industry experts for complex applications. For additional insights, review our bearing lubrication resources.
Conclusion
In conclusion, selecting the right grease for ball and roller bearings is a critical maintenance decision that demands careful consideration of bearing type, operating conditions, and the specific features of various grease formulations. By understanding and applying the principles outlined in this guide, you can maximize the life and performance of your bearings, ensuring smooth operation and reduced downtime.
Consistent maintenance and regular monitoring are a key to the longevity of your lubrication system. Should you require specialized advice, assistance in selecting the perfect grease for your needs, or need to replenish your maintenance supplies, PIB Sales is here to help.
Visit the PIB Sales online shop for a comprehensive selection of top-quality ball and roller bearings or contact us for expert guidance tailored to your unique requirements.