Pacific International Bearing Sales provides components for modern robotic devices like Schaeffler’s plug-and-play linear modules. These range extenders are intended to give much longer working ranges for robots, with options for a triple toothed belt drive or a ball screw drive based on the application. Cobots may easily build X-Z axis systems using two linear modules from Schaeffler’s broad modular systems. This extended travel distance in two axes frequently enables the use of smaller and lighter robots, increasing adaptability and efficiency in a variety of applications.
We highlight such advancements because they represent the future of robotics, pushing the boundaries of what robots can achieve with greater precision and adaptability.
Range Extenders in Robotics Overview
A plug-and-play ready range extender is a type of range extender that is designed to easily integrate into existing robotic systems. This plug-and-play functionality means that the extender can be easily connected and configured without extensive setup or programming, allowing for immediate use. These extenders come equipped with all necessary components, including servo motors, controllers, and installation kits, making the installation process simple and fast.
Features of the Plug-and-Play Ready Range Extender
Drive Options
Range extenders are available with two primary drive options, each tailored to different operational needs:
Triple toothed belt drive:
– Capable of achieving speeds up to 5 meters per second, ideal for tasks requiring rapid movements and extensive coverage.
– Designed for durability, the triple toothed belt drive minimizes maintenance needs, reducing downtime and operational costs.
– Ensures smooth, consistent operation, making it suitable for high-speed automation tasks.
Ball screw drive:
– Offers exceptional accuracy with a precision of ±0.01 mm, essential for applications requiring high precision and repeatability.
– Handles loads up to 200 kg, providing the necessary strength for heavy-duty applications.
– Minimizes backlash and ensures precise positioning, crucial for detailed and intricate tasks.
Modular System
The linear modules used in range extenders are part of a comprehensive modular system that allows for easy customization and scalability. By combining two linear modules, users can create X-Z axis systems, particularly beneficial for collaborative robots (cobots). This modularity ensures that the system can be tailored to specific needs, offering a flexible solution adaptable to evolving operational demands. The modular design also simplifies upgrades and reconfigurations, making it easy to integrate new components and technologies.
The following table summarizes the technical specifications for plug-and-play linear modules:
Feature | Triple toothed belt drive | Ball screw drive |
Speed | Up to 5 m/s | Up to 2 m/s |
Precision | ±0.05 mm | ±0.01 mm |
Load Capacity | Up to 100 kg | Up to 200 kg |
Travel Distance | Customizable up to 10 meters | Customizable up to 5 meters |
Maintenance | Low maintenance | Requires regular lubrication |
Benefits of using the plug-and-play ready range extender
1) Significantly increases the operational range of robots, crucial for tasks requiring large workspaces or long-distance travel. This capability enhances productivity and efficiency in large-scale manufacturing environments, warehouses, and agricultural fields by allowing robots to cover more ground without relocation.
2) The ability to choose between different drive options and the modular system provides a high degree of versatility. This flexibility allows robots to adapt to various applications, from industrial automation to healthcare and agriculture. Users can configure the range extender to meet specific operational requirements, ensuring the robotic system remains up-to-date with the latest technological advancements.
3) Extending the travel distance in two axes often allows for the use of smaller and lighter robots, reducing overall system costs and enhancing operational efficiency. Smaller robots consume less power and require less maintenance, contributing to lower operational costs. Additionally, fewer robots are needed to cover a given area, streamlining workflows and reducing redundancy.
4) The plug-and-play design ensures easy integration into existing robotic systems, reducing setup time and minimizing disruptions to ongoing operations. The user-friendly design requires minimal technical training for installation or configuration, facilitating quicker deployment and rapid benefits from the enhanced capabilities.
5) Integrating high-quality bearings ensures smooth and efficient operation, enhancing the longevity and reliability of the extender. High-quality bearings reduce friction and wear, ensuring consistent performance over time. This reliability is crucial in high-stakes environments where downtime can lead to significant losses. The precision provided by these bearings also improves the accuracy of robotic movements, essential for tasks requiring meticulous detail and consistency.
Key Performance Factors of a Range Extender for Cobots
A range extender designed for cobots must meet stringent performance criteria to ensure precise motion control, load stability, and long-term reliability in dynamic automation environments. As cobots continue to be adopted in high-mix, low-volume production, logistics automation, and precision assembly, the requirements for modular and scalable linear motion systems have evolved. A well-engineered range extender must incorporate advanced mechatronic integration, optimal force distribution, and high-durability components to maximize operational efficiency.
1. Mechatronic integration and system synchronization
One of the critical performance aspects of a range extender for cobots is its seamless integration with existing robotic controllers and motion planners. Unlike traditional linear motion systems, a cobot-compatible range extender must synchronize dynamically with real-time force feedback and trajectory adjustments.
- EtherCAT, PROFINET, and Modbus compatibility enable direct communication with major industrial robot controllers, ensuring precise motion coordination.
- Embedded absolute encoders allow for real-time position tracking, improving repeatability in pick-and-place and assembly applications.
- Adaptive control algorithms adjust acceleration profiles based on payload variation, preventing sudden force spikes that could impact collaborative workspaces.
By leveraging closed-loop servo control combined with sensor-driven motion adjustments, the range extender ensures smooth transitions between operational phases while maintaining compliance with ISO/TS 15066 safety standards for cobots.
2. Structural rigidity and vibration damping
Cobots frequently operate in applications requiring high-speed, high-precision movements with variable loads. To maintain accuracy over extended travel distances, the range extender must exhibit high mechanical stiffness while effectively absorbing vibrational energy.
- Extruded aluminum profiles with integrated damping channels reduce deflection under dynamic loads, maintaining motion accuracy across the entire stroke length.
- Vibration isolation mounts and passive damping elements minimize oscillations that could affect the precision of end-effector operations.
- Preloaded guideways with linear recirculating ball bearing assemblies (INA KUVE Series) enhance motion stability by ensuring consistent contact pressure across rolling elements.
The ability to maintain rigid structural integrity while mitigating micro-vibrations is essential for applications such as precision dispensing, automated inspection, and fine-pitch electronic assembly.
3. Load optimization and force distribution
A range extender must efficiently distribute forces across its entire motion range, ensuring that payload weight shifts do not introduce excessive mechanical stress.
- Cross-roller bearing systems (INA RUS Series) provide high radial and axial load capacity, ensuring even weight distribution when the cobot extends to its maximum reach.
- Ball screw actuators with dual-guideway support improve force resistance, making them ideal for applications requiring heavy payload stability (up to 200 kg).
- Load-adaptive servo actuation automatically adjusts torque output based on real-time force feedback, improving motion consistency across variable payload scenarios.
Proper load balancing not only extends the lifespan of mechanical components but also enhances the safety and responsiveness of the range extender in dynamic environments.
4. Energy efficiency and thermal management
To ensure continuous-duty operation in high-cycle industrial applications, a range extender must be designed for low energy consumption and efficient heat dissipation.
- High-efficiency servo motors with regenerative braking minimize energy loss in high-speed motion sequences.
- Low-friction linear bearing arrangements (INA KUVE35-B, RUE45-E) reduce power consumption by optimizing rolling resistance in extended linear travel.
- Passive cooling systems integrated into the actuator housing dissipate excess heat, preventing thermal expansion issues that could affect motion accuracy.
A well-optimized thermal management system ensures consistent actuator performance, even in high-temperature operating environments such as automated welding cells or CNC tool handling stations.
5. Predictive maintenance
Cobots are expected to operate in high-availability manufacturing setups, where unplanned downtime can result in significant productivity losses. The range extender must incorporate predictive maintenance features to monitor component wear and prevent mechanical failures before they occur.
- Integrated condition monitoring sensors track bearing wear and lubrication levels, providing early warning signals for maintenance scheduling.
- Self-lubricating bearing elements (FAG 6205-2RSR, INA ZKLN2052-2RS-XL) extend service intervals, reducing manual intervention.
- Automated fault diagnostics detect anomalies in motor response and actuator travel, preventing premature component failures.
By leveraging IIoT-enabled condition monitoring, the system can optimize maintenance schedules based on real-time operational data, ensuring that the range extender remains fully functional with minimal downtime.
Schaeffler Plug-and-Play Ready Range Extender
Schaeffler offers advanced plug-and-play-ready linear actuators designed to serve as range extenders, significantly enhancing the operational reach of robotic systems. These actuators are comprehensive solutions, supplied with essential components such as a servo motor, servo controller, and cable track solution. Additionally, they come with versatile installation kits for either floor or ceiling mounting, providing flexibility in various deployment scenarios.
Schaeffler’s linear actuators are part of a wide-ranging modular system, enabling the creation of X-Z axis configurations by combining two actuators. This modularity allows for the realization of complex motion systems, particularly beneficial for collaborative robots (cobots). The extended range of travel in two axes often permits the use of smaller and lighter robots, thereby reducing system costs and enhancing overall efficiency.
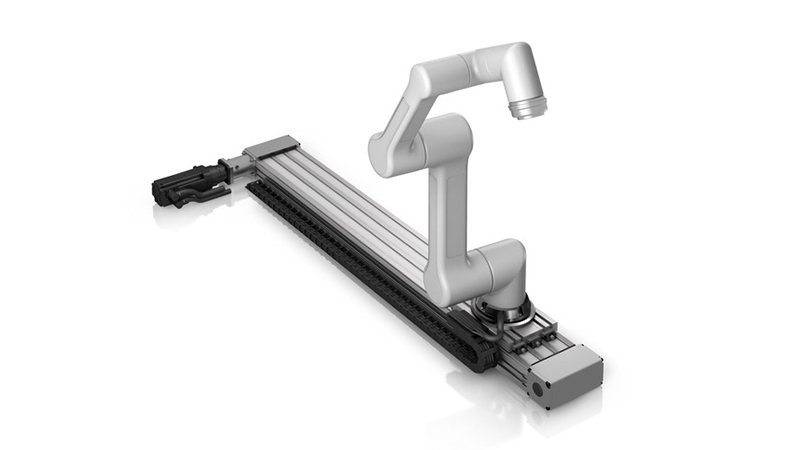
Technically, the actuators provide customizable travel distances, with the belt drive extending up to 10 meters and the ball screw drive up to 5 meters. This adaptability ensures that the range extenders can be tailored to operational needs, whether in industrial automation, precision assembly, or other demanding environments.
Furthermore, the plug-and-play design of these range extenders simplifies integration into existing robotic systems. This ease of deployment minimizes setup time and operational disruptions, allowing for a swift enhancement of robotic capabilities. High-quality bearings incorporated into the actuators ensure smooth and efficient operation, contributing to the reliability and longevity of the system.
Optimizing Robotic Workspaces with Modular Range Extenders
To further enhance the flexibility and efficiency of robotic workspaces, Schaeffler has developed advanced range extender configurations that allow for dynamic, high-speed motion with precise load distribution. These solutions optimize linear movement, reduce mechanical stress, and extend robotic reach without requiring additional floor space.
Schaeffler’s range extenders are designed with adaptive load balancing, ensuring that robotic arms maintain consistent force distribution across extended travel distances. This is particularly beneficial in high-speed automation processes, where mechanical vibration and deflection must be minimized.
Key performance advancements include:
- Kinematic Compensation Mechanisms – Ensuring stable motion dynamics by adjusting acceleration profiles based on payload weight.
- Active Damping Integration – Reducing oscillations and maintaining sub-micron positioning accuracy in high-speed applications.
- High-Rigidity Guideways (INA RUE35-E, RUE45-E) – Enabling precise linear motion with minimal wear over extended operating cycles.
- Optimized Gearbox Pairing (FAG NUP2306-E-TVP2, NUP2310-E-TVP2) – Ensuring smooth torque transmission and consistent velocity profiles.
These features contribute to more stable robotic movement, reduced wear on mechanical components, and improved overall efficiency in dynamic environments such as automated pick-and-place operations and logistics handling systems.
For extended-range robotic workspaces, precision motion components must be optimized for high-cycle durability and minimal energy loss. Schaeffler incorporates specialized bearing solutions from its Schaeffler Bearings Catalog, engineered for continuous operation under variable load conditions.
- INA ZKLN Series Axial Angular Contact Bearings (ZKLN1545-2RS-XL, ZKLN2052-2RS-XL) – Ideal for applications where high axial and radial loads are present in extended linear travel.
- FAG Cylindrical Roller Bearings (NU2222-E-XL-TVP2, NJ2215-E-M1A-C3) – Designed for high-speed motion with optimized load-carrying capacity in belt-driven actuator systems.
- Schaeffler TPI 252 Track Roller Bearings – Used in high-load rail-guided linear actuators, offering increased contact surface for load distribution.
- Deep Groove Ball Bearings (6205-2RSR, 6010-2Z) – Supporting secondary drive components in modular range extenders to reduce rolling resistance.
These bearings ensure low-friction movement, reduced thermal expansion, and extended service intervals, making them ideal for robotic applications requiring extreme precision and reliability.
To further optimize industrial workspaces, Schaeffler’s range extender solutions integrate multi-zone control algorithms, allowing robots to:
- Operate at variable speeds based on workspace segmentation, improving cycle time efficiency.
- Adapt travel path constraints dynamically, reducing unnecessary movements and optimizing power consumption.
- Synchronize with multiple robotic units, ensuring collision-free operation in multi-robot environments.
This multi-zone approach is particularly effective in logistics automation, CNC machining centers, and semiconductor production, where precise travel coordination is required to maximize throughput.
By leveraging Schaeffler’s advanced modular range extenders, manufacturers can expand robotic workspaces efficiently while maintaining precision, durability, and adaptability, ensuring future-ready automation solutions for high-performance industries.
The right bearings make all the difference! Find high-quality, reliable options at Pacific International Bearings Sales and keep your robotics running smoothly.
Implementation and Integration
Implementing and integrating a ready range extender for robotics entails various steps to ensure performance and operation, including the selection of appropriate components, precise configuration, and careful calibration to fit with the specific requirements of the application.
System Integration
Integrating the range extender into an existing robotic system involves several steps, including mechanical mounting, electrical connections, and software configuration. The integration process should ensure that the extender is securely attached and aligned with the robot’s operational axis.
Integration step | Description | Considerations |
Mechanical mounting | Securely attach the range extender to the robot’s frame | Ensure alignment and stability to prevent operational issues |
Electrical connections | Connect the servo motor and controller to the robot’s power supply and control system | Verify voltage compatibility and signal integrity |
Software configuration | Update the robot’s software to recognize and control the range extender | Ensure firmware compatibility and proper parameter settings |
Calibration and Testing
Once the range extender is physically integrated, calibration and testing are essential to ensure precise operation. This involves setting the correct parameters in the robot’s control software and performing test runs to verify performance.
Calibration step | Description | Considerations |
Parameter setting | Configure speed, acceleration, and precision parameters | Match settings to application requirements |
Test runs | Conduct operational tests to verify movement and accuracy | Check for any discrepancies or issues in performance |
Adjustment | Make necessary adjustments based on test results | Fine-tune parameters for optimal performance |
Operational Integration
After successful calibration, the range extender is ready for operational integration. This phase involves synchronizing the extender’s movements with the robot’s tasks to ensure smooth and efficient operations. Continuous monitoring and periodic maintenance are crucial to maintain performance and longevity.
Operational step | Description | Considerations |
Synchronization | Align the extender’s movements with the robot’s operational tasks | Match settings to application requirements |
Monitoring | Continuously monitor performance during operations | Identify and address any issues promptly |
Maintenance | Perform regular maintenance to ensure longevity and reliability | Ensure seamless coordination to avoid operational delays |
The implementation and integration of a ready range extender for robotics necessitates thorough planning and execution. By carefully selecting components, assuring flawless mechanical and electrical integration, and executing comprehensive calibration and testing, the range extender can greatly improve the operational capabilities of robots. Continuous monitoring and maintenance will assure long-term performance, increasing efficiency and productivity across a variety of applications.
Applications and Use Cases
The plug-and-play range extender considerably increases the operational range and diversity of robotic systems, making it suitable for a wide range of industries and use cases.
In industrial automation, the range extender serves to optimize manufacturing operations. Robots with range extenders can cover bigger areas, making jobs like material handling, assembly, and quality inspection more efficient. This lowers the need for many robotic units while streamlining operations.
In the healthcare sector, range extenders enhance the capabilities of medical robots. These robots can perform a variety of tasks, from delivering medications and supplies within a hospital to assisting in surgeries with extended precision and reach. The extended range also supports telemedicine applications, allowing robots to interact with patients over greater distances.
In logistics and warehousing, range extenders allow robots to traverse and operate over large regions, improving products storage, retrieval, and transportation. This application improves inventory management, lowers operating expenses, and boosts overall efficiency.
Range extenders are used in research and development to enable robots to execute a variety of experimental activities requiring precision and longer reach. This adaptability is critical for conducting experiments, creating prototypes, and testing new technologies in controlled situations.
In the construction business, range extenders improve the capabilities of robots used for building, inspection, and maintenance. Robots’ longer reach enables them to access hard-to-reach regions and do jobs that would be difficult or risky for human workers.
Visit the Pacific International Bearings website to browse and order bearings for your advanced robotic systems. Please contact us for questions or assistance.