Pacific International Bearing Inc. offers Schaeffler’s advanced products, including precision strain wave gears, renowned for their exceptional performance in robotic joints. Schaeffler Technologies, a leader in this field, has made significant strides with its precision strain wave gears, particularly the high torque RT1 and standard torque RT2 series. These components are integral to the seamless operation of robotic joints, enhancing their accuracy and lifespan. The integration of sensors within these gears further amplifies their performance by providing real-time feedback and control.
Strain wave gears from Schaeffler are well-known for their small size, high torque density, and low backlash, which makes them the perfect option for robotic applications such as medical equipment and industrial robots. Torque sensors, particularly those with cutting-edge Sensotect coating technology, allow for accurate force and torque measurement, which enhances the dynamic behavior and control of robotic systems.
Technical Principles of Strain Wave Gears
The precision strain wave gears in Schaeffler’s RT series consist of three primary components: the Wave Generator, the Flexspline, and the Circular Spline. The Wave Generator, an elliptical drive element equipped with a pre-mounted thin section bearing, induces the deformation of the Flexspline, a flexible, torsionally rigid component with external teeth. The Circular Spline, a rigid ring gear, surrounds the Flexspline and engages with its teeth.
The Flexspline is designed in two variants: HAT and CUP. In the HAT variant, the base of the Flexspline extends outward, creating a large passage opening suitable for large hollow shafts. The CUP variant, with an inward-extending base, is optimized for compact drive systems. Depending on the version, additional components such as output bearings, input shafts, and housings are incorporated for straightforward integration into various applications.
Component | Description |
Wave generator | Elliptical drive element with a thin section bearing |
Flexspline | Flexible component with external teeth |
Circular spline | Rigid ring gear with internal teeth |
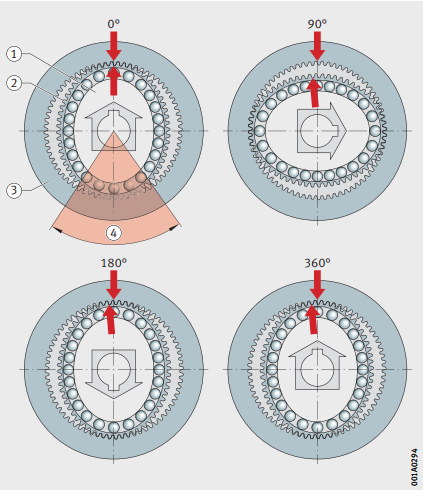
- 1 – Wave generator
- 2 – Flexspline
- 3 – Circular spline
- 4 – Tooth engagement area
The Flexspline takes on the wave generator’s elliptical shape after installation. The Flexspline experiences circumferential deformation as a result of the Wave Generator’s rotation. There are two sizable, symmetrical tooth engagement zones where the external teeth of the Flexspline and the interior teeth of the circular spline meet. The Flexspline and Circular Spline move about one another by two teeth per input revolution since the Flexspline has two fewer teeth than the Circular Spline.
Phase | Description |
0° | The wave generator starts rotating, flex spline deforms |
90° | Maximum engagement of teeth |
180° | Flexspline moves two teeth relative to the circular spline |
360° | Completes one cycle, flex spline shifts by two teeth |
The RT series includes High Torque RT1 and Standard Torque RT2, characterized by their compact design, high torque density, and minimal backlash. The High Torque RT1 series achieves up to 30% higher torque and 40% longer service life compared to the RT2 series. The RT1 series also features the RT1-T variant, integrating a torque sensor without introducing additional elasticity into the drive train.
Lubricants significantly influence the performance and service life of strain wave gears. Approved lubricants ensure optimal operation, with the lubricant temperature and service life being key factors. For example, the RT1 series recommends a lubricant change if temperatures exceed +35°C, while the RT2 series allows up to +40°C.
Strain Wave Gear Series Overview
Overview of series
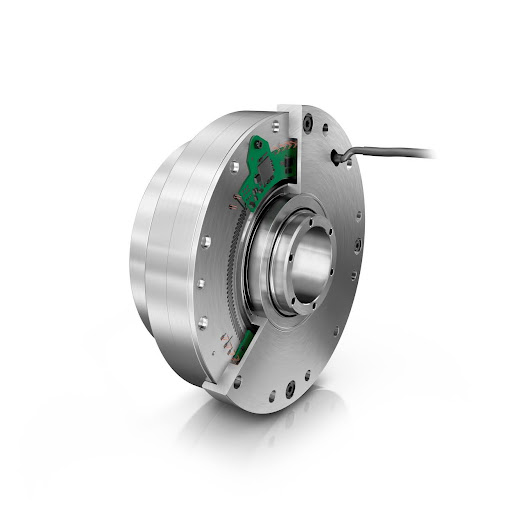
The High Torque RT1 series offers sizes ranging from 14 to 32, with gear reduction ratios of 50, 80, 100, 120, and 160. These gears deliver a maximum torque between 23 Nm and 484 Nm. The RT1 series is available in two variants: HAT, where the Flexspline runs outward, allowing for large hollow shafts, and CUP, where the Flexspline runs inward, making it ideal for compact drive systems. The versions within this series include a сomponent Set (CS), a basic unit with heavy-duty output bearing for a hollow shaft motor (BHS), a иasic гnit for the motor shaft (BMS), and a fully pre-mounted and sealed unit (UHS). The RT1 series is known for its high torque density and extended service life, making it suitable for heavy-duty applications.
The Standard Torque RT2 series also comes in sizes 14 to 32 with gear reduction ratios of 50, 80, 100, 120, and 160. It provides a maximum torque range from 18 Nm to 372 Nm. Similar to the RT1, the RT2 series has HAT and CUP variants. The versions available are Component Set (CS), Basic Unit with heavy-duty output bearing for hollow shaft motor (BHS), Basic Unit for motor shaft (BMS), and a fully pre-mounted and sealed unit (UHS). The RT2 series is characterized by its extensive portfolio of sizes and gear ratios, making it versatile for various applications.
The sensorised high torque RT1-T series is available in sizes 14, 17, 25, and 32, with gear reduction ratios of 100 and 160. The maximum torque ranges from 36 Nm to 484 Nm. This series features the HAT variant, and the available version is the Unit with an integrated torque sensor (UHS-T). The RT1-T series integrates a torque sensor for precise measurement, offering high sensitivity without introducing additional elasticity into the drive train.
Series | Sizes | Gear Reduction Ratios | Maximum Torque (Nm) | Variants | Versions | Key Features |
RT1 (High Torque) | 14, 17, 20, 25, 32 | 50, 80, 100, 120, 160 | 23 to 484 | HAT, CUP | CS, BHS, BMS, UHS | High torque density, long service life |
RT2 (Standard Torque) | 14, 17, 20, 25, 32 | 50, 80, 100, 120, 160 | 18 to 372 | HAT, CUP | CS, BHS, BMS, UHS | Versatile sizes and ratios, robust design |
RT1-T (Sensorised High Torque) | 14, 17, 25, 32 | 100, 160 | 36 to 484 | HAT | UHS-T | Integrated torque sensor, high sensitivity |
Schaeffler’s precision strain wave gears are designed to ensure optimal performance and reliability in various industries, including robotics, medical equipment, industrial machinery, and machine tools. The high torque RT1 series is ideal for applications demanding high torque and durability. The Standard Torque RT2 series offers versatility with its wide range of sizes and ratios. The sensorised RT1-T series is perfect for applications requiring precise torque measurement and high sensitivity.
For more information and to explore Schaeffler’s complete portfolio of precision strain wave gears, contact Pacific International Bearing Inc., your trusted supplier of high-quality bearings and drive components.
Integration of Sensors in Strain Wave Gears
Schaeffler’s sensorised precision strain wave gears utilize an integrated torque sensor that is embedded within the Flexspline. This integration allows for accurate torque measurement without the need for additional elastic elements, thus maintaining the torsional rigidity of the system at 100%.
The torque sensor is coated with sensotect, a sensory coating applied via Physical Vapor Deposition (PVD) technology followed by laser structuring directly onto the component surface. This advanced coating enables continuous measurement of force and torque on both two-dimensional and three-dimensional geometries, providing high sensitivity and minimal deviation in hysteresis and linearity
The sensor system in Schaeffler’s strain wave gears comprises three main components: a precise strain wave gear, a torque sensor, and an electronic sensor system that captures the torque signal directly from the Flexspline. The electronic control and signal processing system is also directly integrated into the Flexspline, minimizing the length of connecting cables and enhancing signal integrity. The signals from all strain gauges are processed by a neural network running a multilayer perceptron AI, ensuring accurate and reliable data.
Integrating sensors into strain wave gears significantly enhances the performance and sensitivity of robotic joints. The sensotect coating, with a thickness of just 10 μm, offers excellent long-term stability and is unaffected by temperature variations. This technology is particularly advantageous for collaborative robots (cobots), which traditionally face challenges related to greater elasticity and vibration compared to larger industrial robots.
The torque sensor in Schaeffler’s precision strain wave gears is designed to meet functional safety requirements up to ISO 13849 category 3 PL c. It features a redundant multi-channel design and various safety functions, including cyclic redundancy checks, life counters, and wire break detection. These features ensure the system’s reliability and safety in critical applications.
Performance and Applications
Performance Characteristics
1. Load ratings and torque capacity
The strain wave gears are designed to handle significant loads and deliver high torque capacity. The basic radial dynamic load rating ranges from 3,900 N to 13,300 N, while the basic radial static load rating spans from 7,800 N to 35,000 N. The axial dynamic load rating varies from 5,500 N to 18,800 N, and the axial static load rating ranges from 19,600 N to 88,000 N. These ratings ensure that the gears can withstand substantial forces, making them suitable for demanding applications.
2. Dynamic and static tilting moments
The permissible dynamic tilting moment (Mdyn max) ranges from 41 Nm to 313 Nm, while the permissible static tilting moment (M0) varies from 75 Nm to 778 Nm. These parameters indicate the gears’ ability to handle tilting loads in both dynamic and static states, ensuring stability and precision in robotic joints.
Applications
Schaeffler’s strain wave gears are widely used in industrial robotics, where precision, reliability, and durability are paramount. The high torque capacity and minimal backlash make these gears suitable for tasks that require exact positioning and repetitive motions, such as assembly lines, welding, and material handling.
1. Collaborative robots (Cobots), designed to work alongside humans, benefit greatly from the integration of sensor technology in strain wave gears. The sensors enable active vibration compensation and real-time feedback, which are crucial for maintaining safety and efficiency in collaborative environments. The ability to measure and adjust to force and torque changes ensures smoother and more precise operations.
2. In medical robotics, the precision and sensitivity of strain wave gears are critical. Applications such as surgical robots and diagnostic devices require exact control and minimal deviation, which are achievable with Schaeffler’s sensorised precision strain wave gears. The high sensitivity and integrated torque measurement provide the accuracy needed for delicate medical procedures.
3. AGVs used in logistics and manufacturing also leverage the high performance of Schaeffler’s strain wave gears. The gears’ ability to handle substantial loads and deliver high torque ensures efficient and reliable operation of these vehicles, enhancing productivity in automated environments.
Visit the Pacific International Bearings website to browse and order bearings for your advanced robotic systems. Please contact us for questions or assistance.