As robotics continue to advance, the significance of high precision components is higher than ever for accuracy and overall performance. Bearings play a vital role in enabling the smooth and precise movement of robotic joints, as robots cannot do any of the picking or lateral movements without bearings.
The choice of bearings significantly influences the efficiency, reliability, and longevity of robotic systems. There is now a fundamental distinction when identifying classical industrial robots typically used for welding, painting, and handling heavy components and lightweight robots used in assembly with lighter loads up to 50 lbs. Lighter-weight robots maximize payload and reduce inertia, which improves response. This is only possible with the use of thin section bearings.
Thin Section Bearings for Industrial Robots
Kaydon Reali-Slim® bearings are a good starting point to begin your search for robotic application bearings. As robotic designs continue to grow, many design engineers are specifying Kaydon. Kaydon robotic bearings offer compact and lightweight bearings to increase payloads and minimize power requirements.
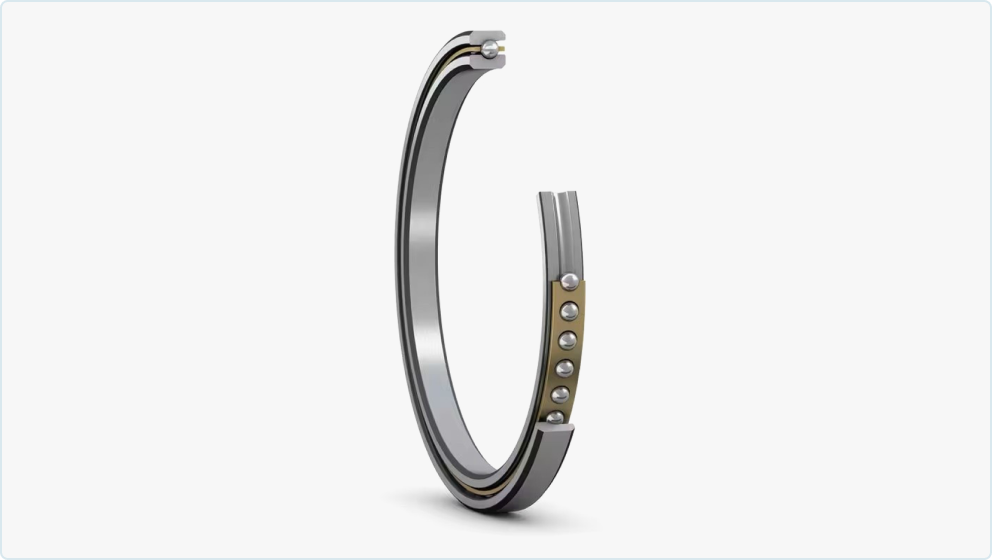
RBC Bearings is another world class bearing manufacturer that offers a full line of thin section bearing types for demanding robotics applications. Today’s improved robotic designs rely on compact designs, light weights, and small cross section bearings. Thin section bearings are the best solution for robotic designs.
The various series of thin section bearings keep the same cross section dimension even though the bore increases. This type of design allows for hollow shaft designs where other components like air, electric, or hydraulic lines can be used for passage. Other designs like the four-point contact thin section RBC bearing can replace a pair of bearings for a more compact design and steady performance.
Bearings and Components for Robotics
Schaeffler Corporation is the best in the industry, offering many components and bearings for robotics.
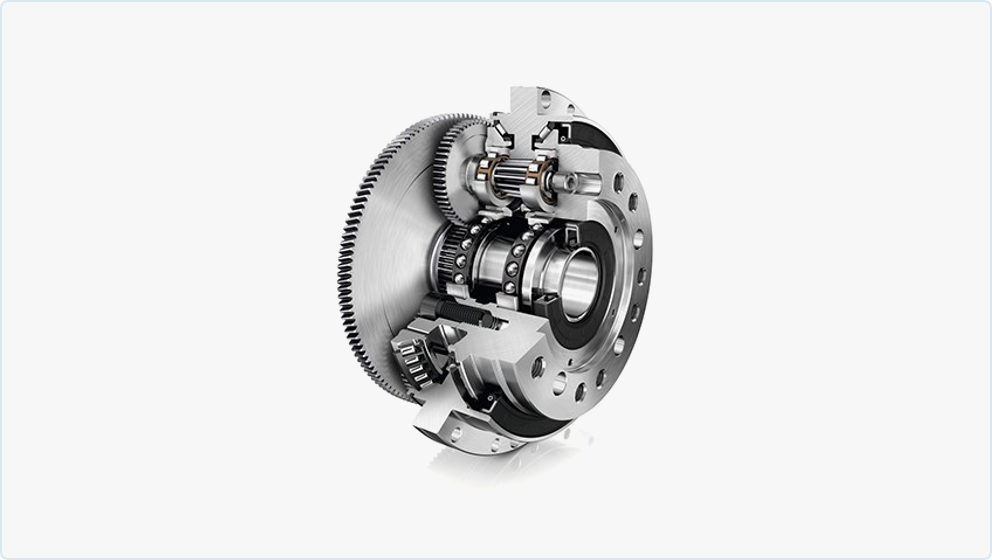
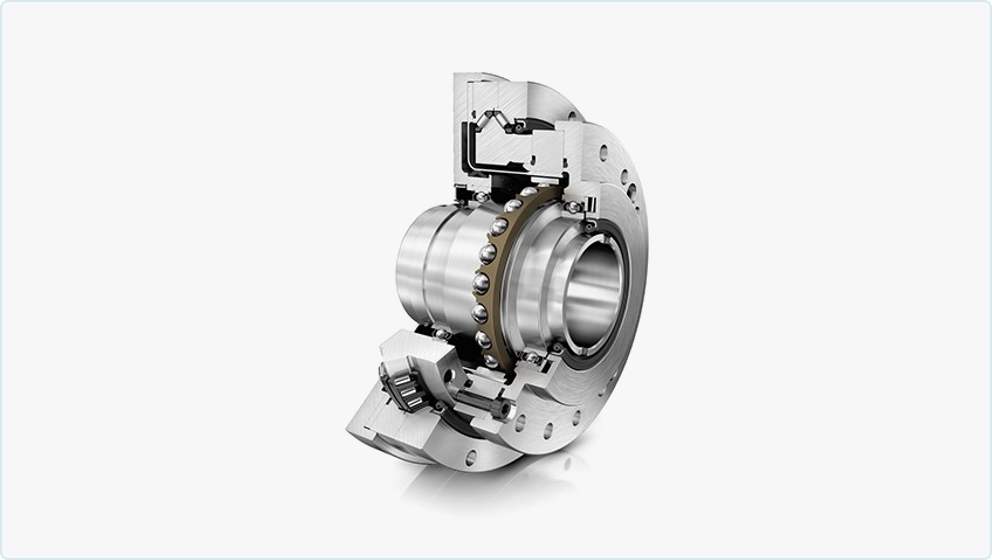
Schaeffler Bearing Company has the most extensive portfolio of bearings and components for robotics. Schaeffler offers a precision strain wave gear series for classical and lightweight robots, with a torque sensor integrated into the strain wave gearing. Schaeffler also offers the PSC series (the “P” stands for “precise,” the “S” for “silent,” and the “C” for “constant,” marking a constant level of precision) of precision planetary gear units for industrial robotics.
Schaeffler offers two precision strain wave gears series for classical and industrial lightweight robots. In addition, Schaeffler offers the PSC series of precision planetary gear units for industrial robots. The Schaeffler offering includes a wide range of robotic linear solutions including applications in reach extension or in gripping systems.
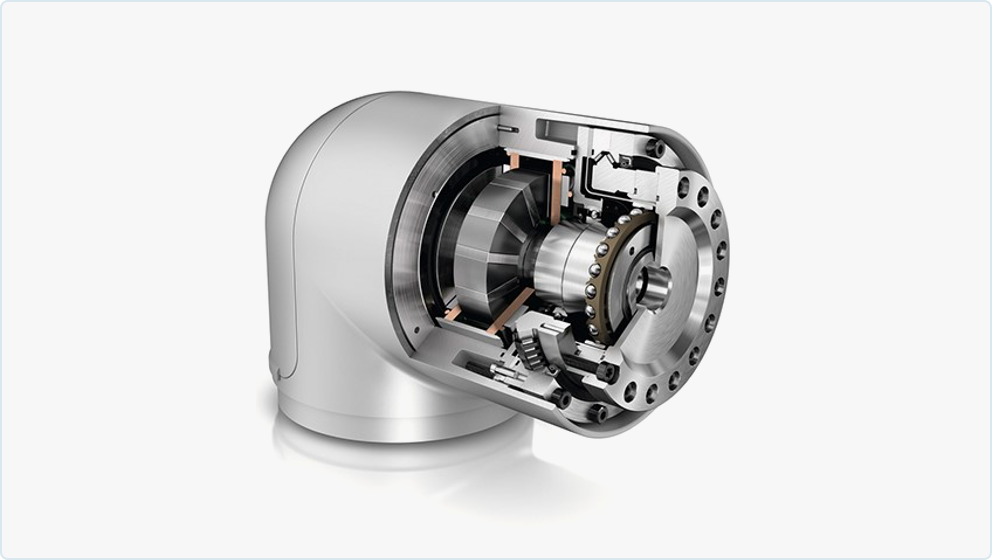
INA standard and high-torque series components are available as pre-assembled and articulated arm units.
The motor, strain wave gear, output bearing support, and an optional integral torque sensor create a perfectly tuned mechatronic unit. You can expect extremely high torque density, accuracy, and long service life when specifying this unit.
Crossed roller bearings are ideal for high-rigidity joint bearings. Short spacers are used in the INA XSU series to separate the cylindrical rollers, reducing friction and running noise.
INA SGL angular contact roller bearings are widely accepted by precision gearbox manufacturers as INA angular contact roller bearings are extremely rigid. With their compact cross section, the angular contact roller bearing is exceptionally accurate for use in robotic joints. For robotic applications they are mainly used in servo drives, robotic joints, and as output bearings in planetary gearboxes.
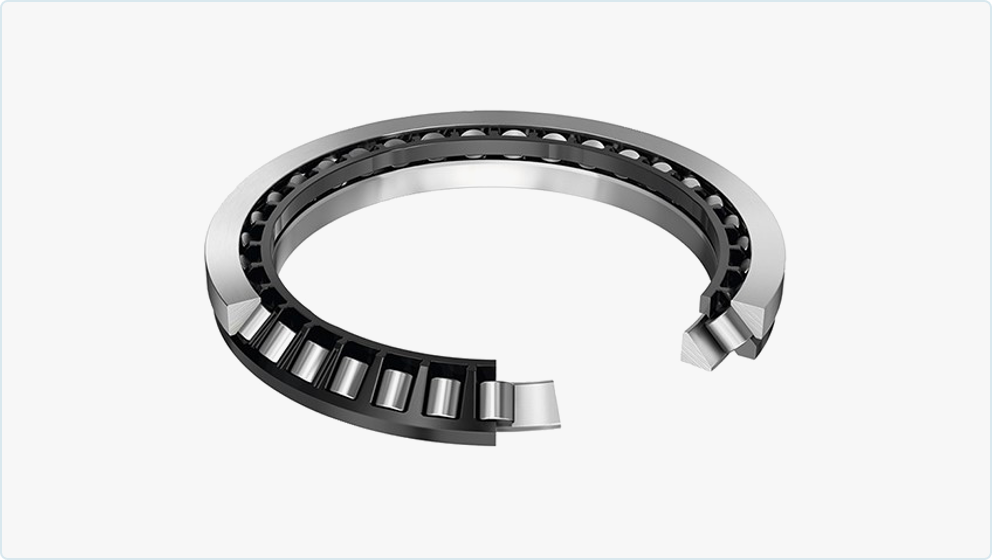
INA offers an alternative to the crossed roller bearing when the robotics application requires more tilting rigidity. INA XZU series angular contact needle roller bearings have identical external dimensions to crossed roller bearings.
They are also conveniently interchangeable with each other. Two separate raceways provide a support distance which increases rigidity while the cages precisely guide the rollers, reducing friction and allowing room for more lubrication, as necessary.
INA’s state-of-the-art monorail guidance systems are ideally suited for many industrial robotic applications. The raceways are manufactured in an “X” arrangement, offering high-speed variants up to 10 m/s without use of expensive special materials, and have six-row recirculating ball bearing and guideway assemblies.
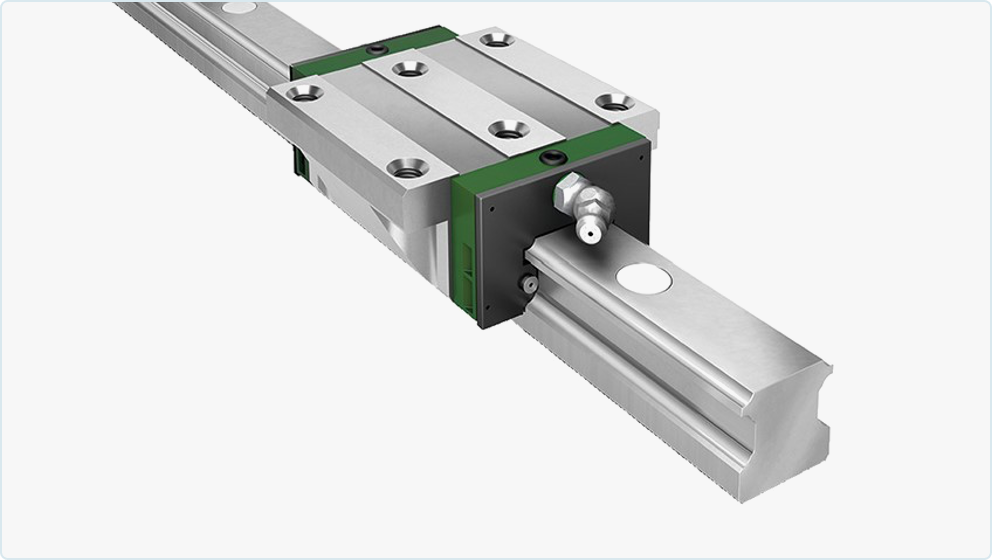
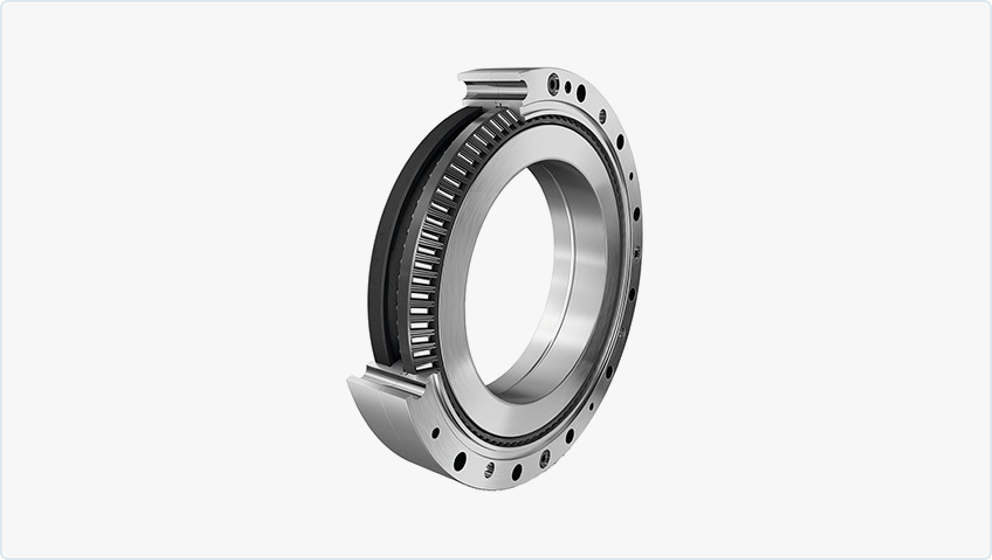
Through Schaeffler Bearing and other manufacturers like Kaydon, RBC, SKF, and INA, Pacific International Bearing offers much more than just rolling bearings. PIB is your strategic partner for robotic system components, precision gearboxes, pivot bearing supports, drive motors, and sensors.
Standard vs. Customized Bearings in Robotics
Standard bearings, which are those with set dimensions, tolerances, and load capacities, are the industry’s workhorses. Standard catalog bearings are proven in performance and have immediate availability. Manufacturers such as Kaydon, SKF, FAG, INA, TPI, NMB, and NSK have established part numbers that have become the standard for the bearing industry.
Standard bearing catalog series like 6000, 6200, and 6300 are reliable and likely can be used right out of the box in robotic applications. Buy this series of bearings now at https://pibsales.com/?s=tpi&tab=Products
Kaydon Reali Slim series of bearings featuring SAA15XL0, JHA17CL0, KAA17AG0, and KO5008CP0 are examples of part numbers available from Pacific International Bearing Sales Inc.
Kaydon bearings are widely used for applications where precise positioning and lightweight designs are important, including:
- Aerospace
- Machine tools
- Medical industry
- Robotics
- Semiconductor manufacturing industry
- Astronomy, telescopes/observatory equipment
- CT scanners
- Fixturing and work holding equipment
- Food processing equipment
- Glassworking equipment
- Luggage scanners
- Optical sights
- Packaging equipment
- Radar, satellite and communications equipment
- Textile machinery
- Tube and pipe-cutting machines

Customized Bearings are sometimes required in robotic applications where standard catalog bearings may be modified to meet the specific need. A speedy and efficient solution for special applications is to utilize existing product designs.
Many customizations involve ring material changes, lubrication enhancements, internal clearance, and ball material changes. Custom bearings may incorporate unique materials, non-standard dimensions, and specialized coatings or seals to cope with unusual loads, speeds, or environmental conditions.
Rarely does a completely new design for bearings appear or is even technically possible. Consult with your expert bearing distributor who can offer many options and explore possibilities with various manufacturers. Not all manufacturers are eager to offer changes, especially in low volume. Customization is very possible for many types of bearings utilizing the knowledge and resources from distributors like Pacific International Bearing Sales Inc.
Customization allows for the incorporation of special materials like High-temperature alloys or ceramic elements for operation in extreme environments.
The decision to opt for standard or customized bearings in robotics includes these factors:
- Volume: If the application is common and the volume is high, standard bearings often provide a cost-effective solution.
- Performance: When the robotic application requires ultra-precision, or must operate under extreme conditions, customized bearings may be the only viable option.
- Innovation: In cutting-edge robotics, where standard solutions are difficult then custom bearings should be considered.
Other types and designs are available in robotics
Plain bearings, also known as sleeve bearings or bushings, offer simplicity and cost-effectiveness for certain robotic applications. They consist of a shaft and a bearing surface, which could be made of various materials such as metal, plastic, or composite.
Key types of plain bearings used in robotics include:
- Journal Bearings
Journal bearings support shafts by providing a low-friction surface between the rotating shaft and the bearing housing. They excel in applications requiring smooth rotation and low-noise levels such as robotic joints, articulated arms, and rotary tables.
- Thrust Bearings
Thrust bearings are designed to withstand axial loads, ensuring the efficient transmission of axial forces within robotic systems. They are commonly used in robotic actuators, gearboxes, and applications where axial forces are prevalent.
- Magnetic Bearings
Magnetic bearings employ electromagnetic forces to levitate and control the position of a rotating shaft without any physical contact. They offer several advantages, including high-precision, maintenance-free operation, and reduced friction and wear. Magnetic bearings find applications in precision robotic systems, such as robotic surgery, semiconductor manufacturing, and high-speed robotics.
- Hybrid Bearings
Hybrid bearings combine the benefits of different bearing types, offering improved performance and versatility. They often integrate ceramic rolling elements with steel races, enhancing stiffness, durability, and corrosion resistance. Hybrid bearings are suitable for various robotic applications that require a balance between high-speeds, heavy loads, and long service life.
Material Selection for Robotic Bearings
52100 Chrome Steel has long been the standard bearing material for bearings. This bearing steel combines hardness, long life, and cost-effectiveness. AISI 52100 chrome steel is particularly good for its wear resistance and load-carrying capacity, suitable for the rigors of robotic operation. 6000, 6200 and 6300 series bearings are standard catalog deep groove ball bearings all manufactured from AISI 52100 steel. Purchase these various series bearings from Pacific International Bearing.
Hybrid Ceramic bearings, made from materials such as silicon nitride (Si3N4), represent a leap forward for applications demanding high speed, precision, and stiffness. These bearings are lighter, harder, and offer superior wear resistance compared to their steel counterparts. They are less susceptible to thermal expansion, which is crucial for maintaining accuracy in high-speed operations. A notable part is NSK’s 7205CTYNSULP4, a bearing that utilizes ceramic balls to achieve a higher degree of precision and speed, ideal for precision arms and positioning stages in robotics.
Advancements in polymers have given rise to plastic and composite bearings, which offer exceptional corrosion resistance and lower weight. These materials are beneficial in environments where exposure to corrosive substances or the need for X-ray transparency is a concern. For instance, Igus’ iglide® J series, such as the JFM-1012-10, is a polymer bearing that is self-lubricating, maintenance-free, and can operate quietly, which is particularly advantageous for medical or laboratory robots.
Other Hybrid bearings, which utilize ceramic balls with steel races, offer a combination of the benefits of both steel and ceramic bearings. These hybrids provide the durability of steel with the reduced weight and thermal resistance of ceramic, making them suitable for high-speed applications that also require load-bearing capacity. The SKF 6310-2RS1/HC5C3WT is an example of a hybrid bearing used in electric motors and generators, which can be found in robotic drives.
Conclusion
Selecting the right bearing for a robot is a critical step in ensuring optimal performance, reliability, and longevity. By considering load capacity, speed, precision requirements, environmental factors, maintenance requirements, and various bearing types, engineers can make informed decisions.
Do you still have questions, or are there specifics you need to discuss? Reach out to the experts at PIB Sales for personalized assistance that addresses your unique requirements. Contact PIB Sales today, and empower your robotic systems with the precision they deserve.