Modern robotics and automation systems rely on high-performance bearings to achieve precise motion, support heavy loads, and maintain reliability under continuous operation. Bearings are concealed inside robotic arms, linear actuators, and rotating joints – they minimize friction between moving parts and ensure smooth, controlled movement. From industrial robot arms performing repetitive assembly tasks to automated gantry systems shuttling components, the correct choice of bearing enables these machines to operate with accuracy and longevity. In this article, we consider how different types of bearings are used in robotics and automation, focusing on crossed roller bearings, linear motion bearings, and spherical plain bearings. We look at each bearing type and its specifications, comparing performance and suitability in various applications.
Engineers and system designers must carefully select bearings that meet the demanding requirements of robotics: high load capacity, precision, stiffness, and compact form factors. For instance, an articulating robot arm might use a high-rigidity crossed roller bearing in its base or wrist joint to support complex multi-axis loads, while its linear axes utilize recirculating ball linear guides for accurate positioning. Meanwhile, spherical plain bearings might be found at pivot points where an actuator or linkage needs to allow angular misalignment without binding. By understanding the role of each bearing type and reviewing their specifications, robotics engineers and procurement specialists can make informed decisions to optimize performance and reliability. Pacific International Bearing Sales Inc. offers robotic and automation application-specific type bearings and can be purchased at www.pibsales.com.
Crossed Roller Bearings in Robotic Systems
IKO Crossed roller bearings offered through PIB are a specialized type of rotary bearing uniquely suited for robotics and automation. Internally, they contain cylindrical rollers arranged in an alternating cross pattern (each roller oriented 90° to the next) between inner and outer rings. This configuration results in line contact between rollers and raceways (as opposed to point contact in ball bearings), which dramatically increases rigidity and load capacity. A single crossed roller bearing can sustain large axial, radial, and moment loads simultaneously – i.e., forces from any direction – without sacrificing rotational accuracy. This all-in-one load-bearing ability is extremely valuable in robot joints, where complex multi-axis forces are common (for example, a robotic wrist might experience radial loads from holding a payload, axial thrust along the joint axis, and bending moments during movement).
High Rigidity and Precision: IKO Crossed roller bearings exhibit very high stiffness and minimal elastic deformation under load. Because multiple rollers share the load with a greater contact area, deflection is much lower than in conventional ball bearings. This yields greater rotational precision and repeatability, key for robotic applications where positioning accuracy is paramount. Many crossed roller bearings are also available in preloaded versions (zero internal clearance) and high precision grades to further boost positioning accuracy and eliminate any play. In humanoid and collaborative robots, these bearings help achieve smooth, precise joint motions without backlash or wobble.
Compact, Space-Saving Design: The crossed roller configuration also allows for a very compact form factor relative to the loads handled. Crossed roller bearings are often designed as thin-section rings that can fit into space-constrained assemblies like robotic wrists or rotating end-effectors. For example, IKO’s CRBH series crossed roller bearings have a “high rigidity, slim” profile with integrated inner and outer rings. The IKO CRBH7013AUU is a representative model: it is a sealed crossed roller ring of 70 mm inner diameter, 100 mm outer diameter, and only 13 mm in width. Despite its slim size, this bearing can support a dynamic load of about 20.1 kN (and static load ~27.7 kN) according to its specifications. Such a bearing is ideal for a robot’s joint where space is tight but high loads and moments must be withstood. (By comparison, a standard ball bearing of similar outer diameter would likely be much thicker and still not handle moment loads as effectively.) Many crossed roller designs like the CRBH series also feature built-in mounting holes on both rings, simplifying installation onto robot linkages or frames without requiring separate housings.
Example – Robotic Arm Joint: Consider a 6-axis industrial robot’s shoulder or elbow joint. This joint must support the arm’s weight, the payload, and dynamic forces as the arm moves. Crossed roller bearings are frequently used here for their combination of load capacity and stiffness. The crossed roller can replace what might otherwise require a pair of angular contact bearings to handle axial and radial loads, streamlining the design. With an IKO CRBH7013AUU in the joint, the robot gains a compact pivot that can handle heavy off-center loads with minimal flex. For smaller robotic joints or precision rotary tables, a correspondingly smaller crossed roller bearing model can be used (for instance, the IKO CRBH5013AUU with 50 mm bore, 80 mm OD, 13 mm width has about 17.3 kN dynamic capacity). In all cases, crossed rollers provide greater rotational accuracy and repeatability under load, which translates to more precise robot motion and positioning.
Longevity and Efficiency: An additional benefit of automation is that crossed roller bearings often have lower friction torque and a small difference between static and dynamic friction. This means the force needed to start moving is nearly the same as that to keep moving, resulting in very smooth motion without stick-slip. The low friction and uniform roller contact reduce wear and heat generation, promoting longer life and even quiet operation in sensitive environments. Many crossed roller bearings include separators or cages to prevent the rollers from rubbing, further lowering friction and noise. All these features make crossed roller bearings a robust solution for robotics, where long maintenance-free service is expected.
In summary, IKO crossed roller bearings play a critical role in robotics by enabling precise, heavy-duty rotational joints in a single compact unit. Their high rigidity, ability to handle combined loads, and built-in mounting ease have made them a staple in robot shoulder joints, swiveling bases, wrist axes, and even some precision linear stages (as part of a crossed roller slide). Engineers designing an automation system should consider crossed roller bearings whenever a rotary motion must be both load-bearing and extremely accurate.
Linear Motion Bearings in Automation
While robots often evoke images of rotating arms, many automated systems also incorporate linear motion – for example, a gantry robot that moves an end effector in X, Y, Z axes, or a pick-and-place machine that slides components into position. Linear motion bearings are what make these precise straight-line movements possible. They come in several forms, with the most common in robotics being profiled rail guides with recirculating ball or roller elements (often just called linear guides or linear rails). Another type is the linear bushing (ball bushings on a round shaft), though these are more common in light-duty or simple setups. In advanced automation, profile rail guides dominate due to their higher load capacity, stiffness, and accuracy.
Profile Rail Linear Guides: A typical linear guide consists of a steel rail with a precise profile (usually square or rectangular) and a mating bearing block (carriage) that rides on it. Inside the carriage, rows of steel balls circulate in raceways, allowing the block to glide smoothly along the rail. The balls contact the rail at four points (two points per raceway in an X-arrangement), which gives these bearings high rigidity in all directions despite their compact size. For example, the IKO Linear Way L series (designation LWL) includes miniature guides as small as 1 cm wide. The IKO LWL15B is a miniature linear carriage designed for a 15 mm wide rail – its block has an assembly height of only ~16 mm and a length of around 42 mm. Despite being small, a single LWL15B carriage can support roughly 4.98 kN dynamic load and 6.49 kN static load on its rail. This is quite impressive for such a tiny bearing, and multiple carriages can be used on one rail to increase load capacity and stability if needed.
These linear guides provide smooth, low-friction translation with high precision. Because the balls roll, friction is minimal, allowing for fast movements and high efficiency (often >90% energy efficiency for linear motion systems). They also have very little play; preloaded carriages can eliminate clearance so that the linear axis has no perceivable slop, which is essential for accuracy and repeatability. Precision and accuracy are indeed key advantages – linear guides enable robotic and CNC axes to position tooling or parts within microns of the target. The rigidity of a profiled rail system ensures that even under load, deflection is tiny, so a robot’s end effector follows a straight and true path. This is why linear guides are heavily used in CNC machines, 3D printers, pick-and-place machines, and Cartesian robots.
High-Speed Automation: Linear bearings also support the high speeds often needed in automation. Ball-bearing linear guides can operate at several meters per second travel speeds with proper lubrication, facilitating rapid pick-and-place cycles in assembly lines. Their smooth rolling motion means minimal wear even at high duty cycles. For instance, in a PCB assembly robot or an automated warehouse shuttle, the linear guide rails allow the mechanism to zip back and forth reliably all day long. Compared to a plain sliding bearing, the rolling element design of linear guides reduces friction and wear, which translates to longer life and less maintenance downtime.
Scalability: Linear motion bearing systems come in many sizes to fit different applications. Miniature guides (e.g., 7 mm, 9 mm, 12 mm rail width) are used in small-scale robots, lab automation devices, or semiconductor equipment where loads are lower but space is at a premium. For example, an IKO LWL9B carriage on a 9 mm rail has a dynamic load capacity of about 1.81 kN – sufficient for micro-robotics or slides in imaging equipment. On the other end, large profile rails (45 mm, 55 mm width or more) can carry extremely heavy loads (tens of kilonewtons) and are used in gantry robots that lift heavy parts or in machine tools. Manufacturers like THK, NSK, IKO, and others offer a range of sizes; typically, as rail size increases, the ball circuits and carriage beef up to handle higher forces. For instance, a 30 mm or 45 mm linear guide might handle 20–50 kN per carriage, suitable for heavy automotive or aerospace automation systems. Pacific International Bearing Sales Inc. offers not only IKO but also other brands like CPC and THK linear bearing products. Contact us for your specific needs at www.pibsales.com.
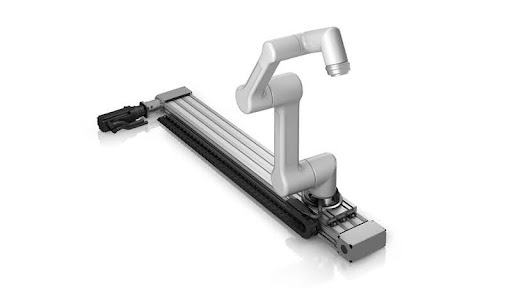
Application Examples: In robotics and automation, linear bearings find use wherever controlled linear travel is needed: a Cartesian robot (also known as a linear robot) uses orthogonal linear axes (X, Y, Z) with guides on each axis for pick-and-place or CNC routing tasks. SCARA robots often have a vertical linear axis in addition to rotary joints – that vertical motion is guided by a linear bushing or rail. Collaborative robots (cobots) that slide along a rail to service multiple stations rely on a linear guide for that track motion. Even in delta or parallel robots, linear bearings can appear in the prismatic joints of the linkage. Essentially, linear guides provide the backbone for precision straight-line movement in automation, ensuring each motion is repeatable and exactly to spec.
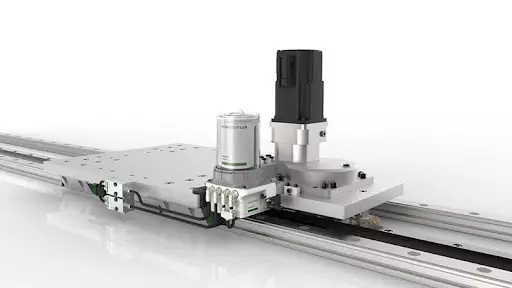
Linear Bushing Bearings: It’s worth noting that some systems use round shaft linear bushings – these are typically cylindrical bushings with recirculating balls that run on a hardened steel shaft. For example, an LM10UU is a common 10 mm inner diameter ball bushing. These are simpler to install for light-duty tasks (like small 3D printers or basic handling devices) and can be lower cost, but they generally cannot match profile rail guides in load capacity or accuracy (they tend to allow a bit of play and can flex under load). In high-end robotics, profile rails are thus more prevalent. However, spherical-plain-lined bushings or polymer bushings are sometimes used in custom linear slide designs if the motion must endure misalignment or shock (for instance, in a very dirty environment where recirculating balls might fail, a Teflon-lined sleeve bearing on a rod could be chosen at the expense of some precision).
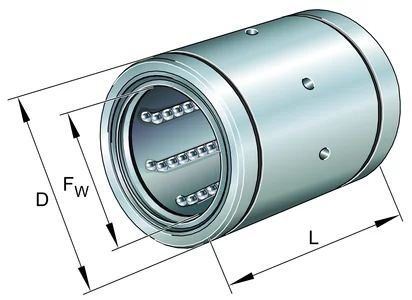
In summary, linear motion bearings such as recirculating ball guides are crucial for automation systems that require accurate and smooth linear movement. They enable robotic gantries, actuators, and slides to position parts with high accuracy and speed. When selecting a linear bearing, engineers consider factors like load (both mass and any moments), desired precision, stroke length, and environmental conditions. Properly sized linear guides, like the LWL15B with its 15 mm rail supporting ~5 kN, will ensure a robot axis can carry its loads without deflection. With lubrication and seals to keep contaminants out, these bearings will operate reliably over millions of cycles – a must for 24/7 automated production lines.
Spherical Plain Bearings in Robotics
Not all motions in robotics are purely rotary or linear – many involve complex angular movements, pivots, and linkages. Spherical plain bearings (SPBs) are designed to facilitate rotation and angulation between two connected parts. Structurally, a spherical plain bearing consists of an inner ring with a convex spherical outer surface and an outer ring with a matching concave spherical inner surface. This “ball-and-socket” construction allows the inner ring to tilt and rotate within the outer ring. Essentially, spherical plain bearings behave like rugged universal joints or bushings that can oscillate and accommodate misalignment. They are sometimes called spherical bushings or ball joints (not to be confused with automotive ball joints, though the principle is similar).
In robotics and automation, spherical plain bearings are particularly valuable in joints that experience misalignment or tilting motion. For example, consider the end of a hydraulic or pneumatic cylinder that pivots as it extends – a spherical bearing at the attachment point allows the cylinder to swivel a few degrees without binding. In robotic arms, SPBs can be used in parallel linkage mechanisms or in joints that don’t rotate a full 360° but need to pivot within a limited range. They are also common in the legs of walking robots or motion simulators, where the joints have to handle high forces at varying angles. Automation equipment like conveyor articulations, grippers, and tooling mounts also employs spherical bearings to handle any alignment inconsistencies.
High Load Capacity and Misalignment: One of the standout features of spherical plain bearings is their ability to support very high radial loads in a compact form, while also allowing significant angular misalignment. They are generally categorized by inner diameter size, and their load ratings scale steeply with size. For instance, an IKO GE10E spherical plain bearing (10 mm bore, 19 mm OD, 9 mm width) can tolerate about 9.41 kN dynamic load (radial) and an impressive 56.5 kN static load in the radial direction. It can also allow roughly ±6° to 7° of angular motion (12° total tilt). Such a part might be used in a small actuator or robot linkage. On the other hand, a much larger SKF GE50ES (50 mm bore, 75 mm OD) has a dynamic capacity of around 156 kN and a static capacity of 780 kN – suitable for heavy industrial robot joints or machinery pivots. These numbers show that spherical plain bearings are built for heavy-duty applications, often in slow or oscillatory joints where traditional rolling bearings might not have enough capacity or would experience edge loading due to misalignment.
Applications in Robotics: Spherical plain bearings truly shine in situations requiring multi-axis flexibility. They are crucial in applications demanding three-dimensional motion and large misalignment angles, essentially acting as the “shoulder” in many robotic linkages. For example, a delta robot’s moving platform is connected to a fixed base via several link rods – at each end of those rods, a spherical joint (either a plain bearing or a rod-end bearing which contains a spherical plain) allows the rod to swivel freely as the geometry changes. This is what gives the delta robot its fluid movement. Another example: humanoid robots and animatronics often use spherical bearings in their hip, knee, or ankle joints combined with linear actuators – the SPB accommodates the slight angular changes as the actuator moves, enabling more organic, human-like limb motion. To achieve smooth, organic movements (rather than jerky motions), designers seek bearings with minimal friction torque and nearly zero clearance, so there is no stick-slip or backlash in the joint. Spherical plain bearings, especially the modern self-lubricating types, can meet this need by providing a snug fit and low friction, ensuring the robot’s movements are as fluid as possible.
[Insert image: Spherical plain bearing used in a robotic linkage (pivot connection illustration)]
Metal-on-Metal vs. Self-Lubricating: There are two primary categories of spherical plain bearings: metal-to-metal (usually steel-on-steel) and self-lubricating (which typically have a PTFE-based liner between the inner and outer ring). Each has its merits in robotics:
- Steel-on-Steel (metal-to-metal): These traditional SPBs can handle alternating and shock loads very well and generally have a long service life under heavy loads. However, they require periodic lubrication to avoid galling or excessive wear, and they cannot be preloaded at assembly (they have some internal clearance by design). That means initially there may be a small amount of play, and under load they have higher friction. In a robot, a metal-to-metal SPB might be chosen for extremely high load joints or where operating conditions are harsh (e.g., a robotic excavator or large industrial arm), but the slight backlash and maintenance needs are a trade-off.
- Self-Lubricating (PTFE-lined): These bearings have a composite or fabric liner (often PTFE-based) bonded to one of the rings, providing a maintenance-free sliding surface. They excel under constant loads and can even be preloaded to achieve minimal or zero clearance in the joint. They also exhibit low friction under load and can dampen small vibrations due to the slight compliance of the liner. This makes them ideal for precision robots – for example, a self-lubricating spherical bearing can be installed with a slight interference to eliminate play, giving a very tight, precise joint. The downside is they are typically more expensive, and the liners can be susceptible to permanent deformation under very heavy impact (so they’re not favored for high-impact or shock-vibratory conditions). In many robotic applications, the benefits outweigh the cons, and we see self-lubricating SPBs used in everything from aerospace mechanisms to surgical robots where maintenance lubrication is impractical.
In summary, spherical plain bearings serve the critical function of allowing angular motion under heavy loads. They are often the best (or only) choice when a joint must pivot in multiple directions or when alignment between parts can’t be perfectly maintained. By selecting the right type (steel-on-steel for brute strength vs. self-lubricating for precision) and size, engineers can design robotic systems that move freely as intended but remain robust against the forces encountered. These bearings complement the more rigid rotary and linear bearings in a machine, adding compliance where needed to prevent binding and ensure smooth operation across complex motions.
Comparison of Bearing Types for Robotics
Each bearing type brings its strengths to a robotic system. The table below summarizes key specifications of the example bearings discussed above and their typical applications in automation and robotics:
Bearing Type | Example (Part Number) | Key Dimensions | Load Capacity (Dynamic/Static) | Typical Applications in Robotics & Automation |
Crossed Roller Bearing | IKO CRBH7013AUU (High-Rigidity Crossed Roller) | 70 mm bore × 100 mm OD × 13 mm width | 20.1 kN / 27.7 kN | Precision rotary joints requiring high stiffness and multi-axis load support (e.g. robot arm shoulder, slewing base, or wrist rotation axes). |
Linear Guide (Ball Type) | IKO LWL15B (Miniature Linear Way block) | 15 mm rail width, ~16 mm carriage height; ~42 mm carriage length | 4.98 kN / 6.49 kN per carriage | Precision rotary joints requiring high stiffness and multi-axis load support (e.g., robot arm shoulder, slewing base, or wrist rotation axes). |
Spherical Plain Bearing | IKO GE10E (Radial Spherical Plain) | 10 mm bore × 19 mm OD × 9 mm width | 9.41 kN / 56.5 kN (radial) | Pivot joints and linkages with misalignment – e.g., actuator ends, robotic link pivots, or suspension-like joints. Ideal where angular motion or alignment flexibility is needed under high loads. |
Table: Comparison of different bearing types commonly used in robotics, with example part specifications. Each type serves distinct motion needs: crossed rollers for high-precision rotation, linear guides for translational motion, and spherical plains for angular alignment.
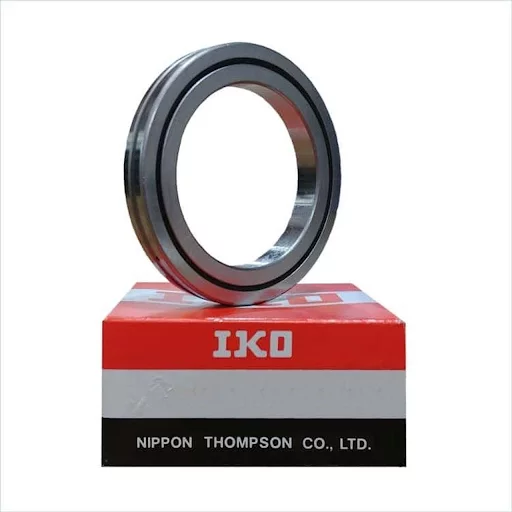
As shown, a crossed roller like CRBH7013AUU handles heavy loads in a compact rotary form, making it perfect for joints that see complex forces.
The linear guide example LWL15B, though much smaller in size, can carry nearly 5 kN while guiding linear motion – multiple carriages can be employed for even higher loads or to increase stability for moments. The spherical plain bearing GE10E illustrates how even a small pivot can sustain extreme static loads (56.5 kN) – a testament to the heavy-duty nature of SPBs in accommodating shock or intermittent loads in pivoting connections.
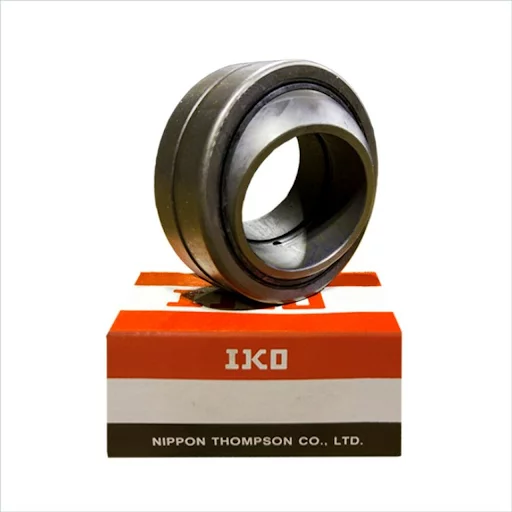
When choosing the right bearing for a given robotic application, engineers should consider the type of motion (rotary, continuous vs. linear vs. oscillating), the degrees of freedom required, load directions and magnitudes, space constraints, and precision needed. Often, the solution is a combination: crossed roller bearings or angular contact bearings for main rotary axes, linear guides for sliding axes, and spherical bearings or rod ends for link pivots. Each must be sized with appropriate safety margins and integrated properly (with correct mounting and preload if applicable) to ensure the overall system performs reliably. Fortunately, suppliers like PIB Sales carry a broad range of these bearing types – from miniature crossed rollers and linear guides for small robots to large spherical bearings for industrial machinery – and can guide optimal selection.
Ready to Get Moving? – Order from PIB Sales
Designing a robotic or automation system involves many decisions. PIB Sales offers a one-stop solution for all the bearing types discussed above and more, backed by expert guidance to help you choose the best option for your needs. We stock high-quality bearings from leading manufacturers (including IKO, SKF, THK, RBC, and others) and understand the critical performance factors for robotics applications.
To make procurement easy, PIB Sales provides multiple convenient ways to get your bearings:
- Many standard bearings (as well as related components like shaft couplings from Ruland) are available for immediate purchase through our website’s online store. Simply use the search function to find the part number or browse by category. You can add items to your cart and check out online for fast, tracked delivery.
- Have a list of bearings or a request for a quote? Send us an email at [email protected] with your requirements. Our sales engineers will promptly review your needs and reply with pricing, availability, and any technical input to ensure you get the right parts. This option is great for complex inquiries or volume orders where you might need custom pricing.
- Give us a call at 800-228-8895 (Mon–Fri, 8:00 am–4:30 pm PST) to speak directly with a PIB Sales representative.
Whether you choose to order online for convenience or reach out to us for personalized support, PIB is committed to ensuring you get the right bearing at the right time. We understand the demands of robotics and automation projects – deadlines, technical specs, performance stakes – and we strive to be a reliable partner in your supply chain.