Internal bearing clearance is the free space between the inner and outer raceways of a bearing. It is also known as radial internal clearance or axial internal clearance.
The internal clearance of a bearing affects its performance and can be specified by the bearing manufacturer based on the intended application. Generally, a larger internal clearance will allow for greater angular misalignment between the inner and outer raceways, while a smaller internal clearance will provide greater axial stiffness and better load distribution.
There are four standard designations for internal clearance for single row radial ball bearings: they are C2, CN, C3, and C4. CN and C3 are by far the most commonly used standard clearances. CN means Clearance Normal. The appropriate internal clearance for a given application will depend on factors such as the operating temperature, speed, load, and desired level of performance.
The radial internal clearance is typically expressed in micrometers (μm) or in thousandths of an inch (mil). It is often designated by the letter “C” followed by a number that represents the clearance value. For example, “C3” indicates a clearance of 3 μm or 0.00012 inches.
The axial internal clearance is typically expressed in micrometers (μm) or in thousandths of an inch (mil). It is often designated by the letter “K” followed by a number that represents the clearance value. For example, “K5” indicates a clearance of 5 μm or 0.0002 inches.
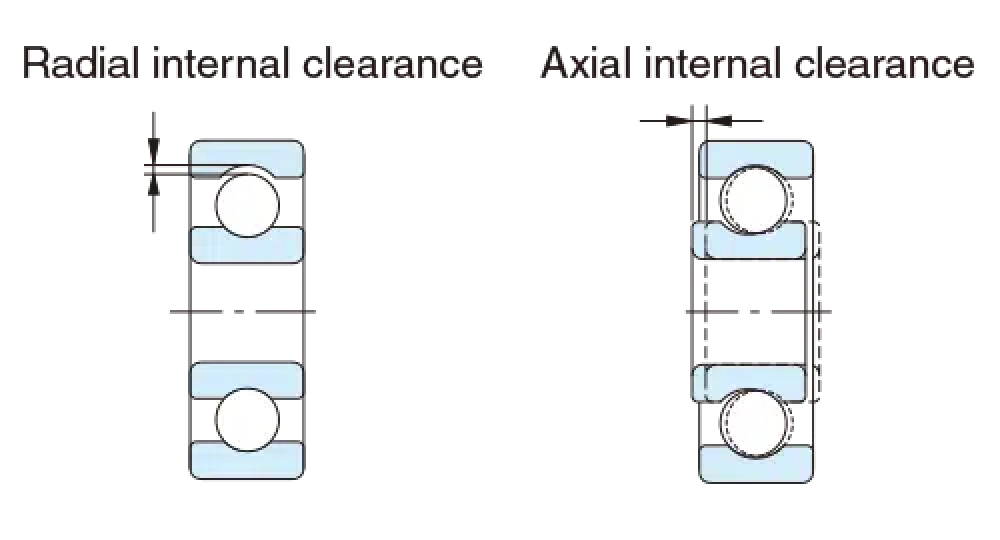
It is important to note that internal clearance can change due to varying temperatures, load, and wear. Regular maintenance and monitoring of bearing performance are important to ensure optimal operation and prevent failure.
Radial internal clearance
Radial internal clearance is an important parameter in the design and operation of bearings.
The radial internal clearance affects the performance of the bearing in several ways. If the clearance is too small, the bearing may experience excessive friction and heat buildup, leading to premature wear and failure. On the other hand, if the clearance is too large, the bearing may exhibit excessive play, which can cause vibration, noise, and reduced precision.
The radial internal clearance can be adjusted during the assembly of a bearing by controlling the amount of interference between the bearing components. The amount of clearance required depends on the application and the expected operating conditions of the bearing. Bearings used in high-speed applications may require tighter clearances to minimize the risk of vibration and noise. Bearings used in high-temperature applications may require larger clearances to accommodate thermal expansion.
Axial internal clearance
Axial internal clearance is another important parameter in the design and operation of bearings. It refers to the amount of internal space between the rolling elements (such as balls or rollers) and the axial components of a bearing, such as the housing or the shaft.
The axial internal clearance affects the ability of the bearing to handle axial loads, which are forces acting parallel to the axis of rotation. If the clearance is too small, the bearing may be unable to accommodate axial loads, leading to premature wear and failure. On the other hand, if the clearance is too large, the bearing may exhibit excessive play, which can cause vibration, noise, and reduced precision.
The axial internal clearance can be adjusted during the assembly of a bearing by controlling the amount of interference between the bearing components. The amount of clearance required depends on the application and the expected operating conditions of the bearing. For example, bearings used in high-thrust applications may require tighter clearances to minimize the risk of axial play, while bearings used in applications with alternating axial loads may require larger clearances to accommodate the changes in load.
Selection methods for bearing internal clearance
The type of bearing, application,operating environment, and manufacturer’s suggestions all play a role in the selection of bearing internal clearance.
Manufacturer’s recommendation
The bearing manufacturer provides a range of internal clearance values for different types of bearings. The recommended value is based on the application, operating conditions, and expected bearing performance. It is always advisable to follow the manufacturer’s recommendations for selecting internal clearance.
Application requirements
The application requirements, such as speed, load, and temperature can affect the bearing internal clearance. For example, a high-speed application may require a tighter internal clearance to reduce the risk of vibration and noise, while a low-speed application may require a looser clearance for proper lubrication.
Bearing mounting method
The method of mounting the bearing can affect the internal clearance. For example, if a bearing is mounted with an interference fit, it may require a looser internal clearance to prevent excessive preload.
Operating temperature
The operating temperature may affect the bearing internal clearance selection. As the temperature increases, the bearing components expand, and the internal clearance may be reduced. Therefore, it is essential to consider the operating temperature while selecting the internal clearance.
Tolerance fit
The tolerance fit between the bearing components can also affect the internal clearance. A looser tolerance fit may require a tighter internal clearance, while a tighter tolerance fit may require a looser internal clearance
Calculation of the operational clearance
Operational clearance, also known as running clearance, is the amount of space between the rolling elements of a bearing and the inner and outer rings of the bearing when it is in operation. The operational clearance is an important parameter to consider when selecting bearings because it affects the bearing’s load capacity, stiffness, and running accuracy.
The operational clearance is typically calculated using the following formula:
C = (D – d) – 2(e + f)
Where:
- C = operational clearance
- D = outer diameter of the bearing
- d = inner diameter of the bearing
- e = maximum radial internal clearance of the bearing (the space between the rolling elements and the inner ring)
- f = maximum axial internal clearance of the bearing (the space between the rolling elements and the outer ring)
The maximum radial internal clearance and maximum axial internal clearance are specified by the bearing manufacturer and can be found in their product catalogs. These values are typically given in microns (μm) or, in some cases, in thousandths of an inch.
It is important to note that the operational clearance should not be confused with the initial internal clearance, which is the space between the rolling elements and the inner and outer rings when the bearing is not in operation. The initial internal clearance is important for proper bearing installation and can affect the bearing’s performance, but it is not the same as the operational clearance.
Once the operational clearance is calculated, it should be compared to the application requirements to ensure that the bearing can handle the anticipated loads and operating conditions. If the calculated operational clearance is too small, the bearing may experience excessive heat generation, premature wear, or other problems. If the operational clearance is too large, the bearing may exhibit reduced stiffness and running accuracy, which can affect the performance of the machine or equipment it is installed in.
Still have a question or need to discuss something? Contact us to get help.