Calculating the life expectancy of bearings is an important step in any design.
Selecting the correct bearing will be determined by its life calculation. It’s not just a matter of selecting the right bearing, but also understanding how long it will be in service. Calculating bearing life enables engineers to predict its useful life. Engineers can be confident that the bearings selected will remain in service providing the optimal performance.
Rating life of bearings calculations
Bearings are crucial components in machinery and equipment that require rotational motion. Bearings are incorporated into rotating parts to reduce friction. The expected life of a bearing under particular operating circumstances can be determined by doing life calculations.
The basic principle of bearing life calculations is to conclude that 90% of the bearings will meet or exceed the calculated life while 10 % may not.
The bearing life formula is expressed mathematically as follows.
L10 = (C/P)^p x 10^6
where:
- L10 is the calculated bearing life in hours;
- C is the dynamic load capacity of the bearing in Newtons;
- P is the applied load on the bearing in Newtons;
- p is the exponent of the bearing life formula, which is typically 3 for ball bearings and 10/3 for roller bearings.
To use this formula, the dynamic load capacity and applied load on the bearing must be known. Once these values are determined, they can be used in the bearing life formula to calculate the expected life of the bearing. It is important to note that this formula provides an estimate of the bearing life, and other factors such as lubrication, contamination, and operating temperature can affect the actual life of the bearing.
Effective service life
The operating conditions, loads , speeds, and lubrication and bearing precision affect the effective service life of a bearing.
In general, a bearing’s useful service life is the amount of time during which it can continue to function properly without suffering excessive wear or damage. The number of hours of operation, rotations, or cycles that a bearing operates is used to express the bearing’s effective service life.
One way to estimate the effective service life of a bearing is to use the basic rating life calculation taking into account the load and speeds present. The basic rating life is the number of revolutions or operating hours that a group of identical bearings can last before failure. A failed bearing is evident when material fatigue occurs on one or both of the rings or rolling elements .
Regular maintenance and proper lubrication can help to extend the effective service life of a bearing and prevent premature failure.
Life factor
Bearing life is a key factor to consider when selecting the right bearing for an application. Depending upon the application, the bearing may be exposed to different loads, temperatures, and speeds. This means that different bearings will provide different levels of life expectancy. It is important to consider the expected life of a bearing before making a selection to ensure it will meet the requirements of the application.
Speed factor calculating
The speed factor is an important consideration when calculating the expected life of a bearing. The speed factor is a function of the bearing’s operating speed.
The basic dynamic load rating (C) of a bearing is the load that a bearing can theoretically last for one million revolutions without experiencing fatigue failure. This rating is determined by the size and design of the bearing and is provided by the bearing manufacturer.
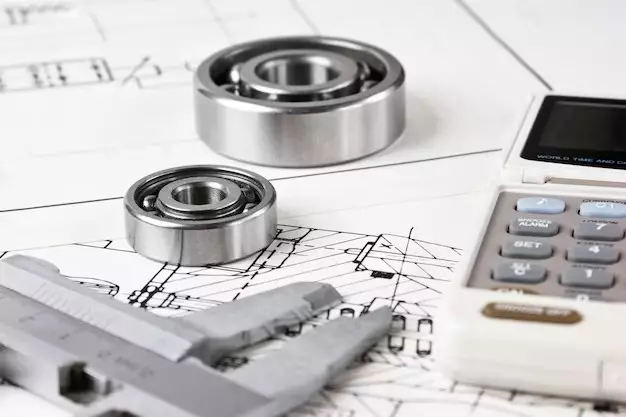
The speed factor (n x dm) is the product of the bearing’s operating speed (n) and the mean diameter of the bearing (dm). The mean diameter is calculated as the average of the bearing’s inner and outer diameters. The speed factor is expressed in units of mm/min.
The speed factor is used to calculate the bearing’s equivalent dynamic load rating (P). The equivalent dynamic load rating is the load that a bearing can theoretically withstand for a million revolutions at the given operating speed. The equivalent dynamic load rating is calculated using the following equation:
P = XFr + YFa
Where X and Y are coefficients that depend on the bearing type and size, Fr is the radial load, and Fa is the axial load. The equivalent dynamic load rating is then compared to the basic dynamic load rating to determine the expected life of the bearing.
Required service life
Generally speaking, the service life of a bearing can be defined as the number of revolutions or hours of operation that a bearing can perform before it requires replacement or maintenance.
Further definition of the factors for calculating life are as follows:
- Load. The load capacity of the bearing must be sufficient for the application. The higher the load, the shorter the service life of the bearing.
- Speed. The speed at which the bearing will operate also affects its service life. The higher the speed, the shorter the service life of the bearing.
- Lubrication. Proper lubrication is essential for maximizing the service life of bearings. Insufficient or incorrect lubrication can significantly reduce the service life of a bearing.
- Operating conditions. Operating conditions, such as temperature, humidity, and exposure to contaminants, will impact the service life of bearings.
- Maintenance. Regular maintenance, including inspections and re-lubrication, can help extend the service life of bearings.
Scale of bearing life
The scale of bearing life refers to the expected duration of time that a bearing can operate effectively before it needs to be replaced due to wear or failure. Bearing life is typically measured in terms of the number of revolutions or hours of operation before the bearing fails.
The industry standard for measuring bearing life is the L10 life, which is defined as the number of revolutions or hours of operation that 90% of a large population of bearings will complete before failure, assuming they are all operating under the same conditions. This means that 10% of the bearings in the population may fail earlier than the L10 life, while 90% will last as long or longer.
L10 life is a useful guideline for estimating the expected life of a bearing, but actual results may vary.
Still have a question or need to discuss something? Contact us to get help.