Machine tool spindles have two primary functions. The first is to rotate the tool for drilling, milling, grinding or turning a work piece. The second is to transmit torque and speed to the cutting area.
The vast majority of machine tools are designed with motorized spindles. Motorized spindles consist of at least two sets of ball and cylindrical roller bearings. The bearing sets have the greatest influence on the lifetime of the spindle. Generally the motor is arranged between the two bearing sets.
Understanding the factors considered for bearing selection in machine tool spindle applications is important for achieving reliable results. Load capacity, speed requirements, rigidity, lubrication, environmental conditions, and noise levels are primary considerations guiding engineers in proper bearing design.
Navigating the bearing set selection process requires precise analysis of the operating conditions. By identifying machine tool requirements, calculating loads and speeds, and utilizing life calculation methods, engineers can determine the optimal bearing set for the application.
In this article we discuss standard applications and bearing types commonly specified in machine tool spindles. We will also explore the best practices for selection, handling, storage and installation guidelines. And finally we will discuss how to evaluate, inspect and monitor bearing operation to ensure peak performance.
Applications
- Spindle units are a vital component in machining operations. Spindle designs range from belt-driven to motor-integrated spindles. Spindle units are used in a variety of machines from high-speed milling to high-capacity turning.
- Screw drives, linear guides and rotary tables are integral in determining machined parts quality. Having high-position accuracy and stiffness are an important key for successful operation.
- Ball screws are high-accuracy and high-efficiency mechanical devices. Ball screws are widely used to drive the axis of a machine tool. Machine tools require screw drives that can position a work piece or machine component with precision in a quick and efficient manner. Rotary tables are positioning devices used in metalworking. Rotary tables enable drill or cut work at precise intervals around a fixed axis. Rotary tables have wide uses for manufacturing and inspection.
- SKF IMx – Optimize communication between CNC control and condition monitoring systems for excellent performance. For many types of machine tool processing operators they want a high level of quality, uptime and long lasting solutions. It is possible to incorporate data from a machine’s CNC system directly into the SKF IMx condition monitoring technology. With SKF’s technology it is possible for end users to predict spindle health using vibration, temperature, speed and process data. Uploading data into SKF @ptitude will give users valuable insight through better diagnostics and prognostic information. SKF can provide support with more in depth analysis. This approach allows for a move from a time based to condition based maintenance approach which reduces the total life cycle cost.
Please contact Pacific International Bearing Sales SKF ACBB specialized distributor for assistance.
Types of Machine Tool Spindle Bearings

Pacific International Bearings is an authorized stocking distributor of SKF manufactured super-precision angular contact ball bearings. SKF Spindle bearings offer a range of shaft diameters from 6 to 360 mm. Spindle bearing requirements vary, and as a result, the SKF assortment of super-precision angular contact ball bearings includes four ISO dimension series.
SKF angular contact bearings have the following features and benefits:
- High-load carrying capacity
- The lower shoulder enables a large number of balls to be incorporated in the bearing, giving it a relatively high load carrying capacity
- Good running properties
- Rapid accelerations and decelerations are possible
- Easy mounting of universally matchable bearings
- No adjustment is needed for correct internal clearance or preload.
Single Row Angular contact ball bearings are designed with inner and outer rings, a cage, and a set of balls that enable contact with the raceways at specific angles.SKF single row angular contact ball bearings can accommodate axial loads in one direction only.
Advantages:
- Angular contact ball bearings are highly suitable for high-speed operations with reduced friction;
- ACBB bearings offer excellent rigidity, minimizing deflection during machining processes, resulting in enhanced precision;
- Angular contact ball bearings have a compact structure, making them ideal for machines with limited space requirements.
Double Direction Angular Contact Thrust Ball Bearings specified in Machine Tool Spindle

SKF double direction angular contact thrust ball bearings provide a method to locate spindle shafts axially in both directions. Double Direction bearings are mounted in combination with cylindrical roller bearings. This bearing combination simplifies machining of the housing bore. Either a straight or tapered bore allows for use of the NN 30 K or N 10 K series Cylindrical Roller bearing
Double direction angular contact thrust ball bearings shown here mounted for use with a corresponding cylindrical roller bearing.
Double direction angular contact thrust ball bearings have the same nominal bore size and outside diameter as the cylindrical roller bearings.
The outside diameter tolerance of the housing washers, combined with the housing bore diameter and tolerances for super-precision cylindrical roller bearings will determine the correct radial clearance in the housing bore. The clearance will stop radial loads from acting on the thrust bearing provided that its outer ring is not axially clamped in the housing.
Cylindrical Roller Bearings

Single Row Cylindrical roller bearings are available in many designs, different series and various sizes.
Features and benefits of using Cylindrical Roller bearings in machine tool spindles:
Lower Friction
Cylindrical roller bearings are precisely designed and manufactured resulting in low friction (Roller end / flange contact area) The open flange design along with the roller end design support lubricant film formation which results in lower friction providing for a higher axial load capability.
Long service life is essential for bearings used in machine tools
The logarithmic roller profile lessens edge stresses at the roller/raceway contact and sensitivity to misalignment and shaft deflection.

Enhanced operational reliability as the surface finish on the contact surfaces of the rollers and raceways supports the formation of a hydrodynamic lubricant film.
Separable components of SKF cylindrical roller bearings are interchangeable. This helps with mounting, dismounting and maintenance inspections.

The cage designs are suitable for high speeds, rapid accelerations and peak loads.
Cylindrical roller bearings are designed to handle primarily radial loads. Cylindrical roller bearings are composed of inner and outer rings and with cylindrical rollers held in place by a cage. These bearings provide a protracted contact surface area for efficient load distribution.
Advantages:
- High Radial Load Capacity: Cylindrical roller bearings excel in applications demanding substantial radial load-carrying capabilities, making them suitable for heavy-duty machining operations
- Low Friction: These bearings exhibit low friction during operation, resulting in improved efficiency and reduced heat generation
- Suitable for High-Speed Applications: With proper design and lubrication, cylindrical roller bearings can achieve high-speed capabilities
Pacific International Bearing Sales Inc offers NSK ACBB Precision bearings.
NSK’s line of high-precision bearings is broad. The 7000, 7200 and 7900 series of angular contact ball bearings are popular series specified to support spindle operations with remarkable accuracy. The 7000, 7200 and 7900 NSK series bearings are specifically engineered to accommodate high loads and high speeds while minimizing heat generation, and ensuring sustained precision and reliability.
NSK 7000,7200 and 7900 series bearings are of high quality and are a value option for other brands made in Europe. NSK offers the 7000 series for light duty, the 7200 series for medium duty and the 7900 series for extra light duty.
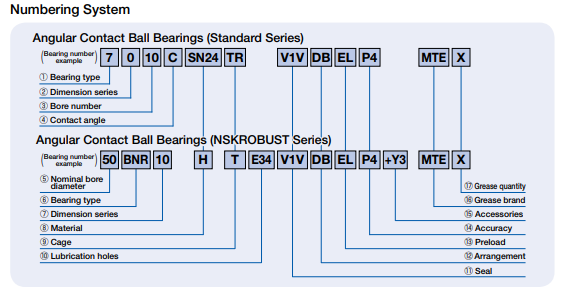
The first four digits identify the bearing part number. In the above chart 7010 is the basic part number where the last two digits multiplied by 5 identify the bearing bore to be 50mm. A 7012 would have a 60mm bore and a 7014 would have a 70mm bore and so on. The breakdown of the bearing part number system for NSK is like most bearing manufacturers having an alpha numeric system to identify the bearing type, contact angle, material, cage, lubrication, preload and how the bearings are arranged.
Pacific International Bearing offers NSK High Precision Cylindrical Roller bearings for sale.
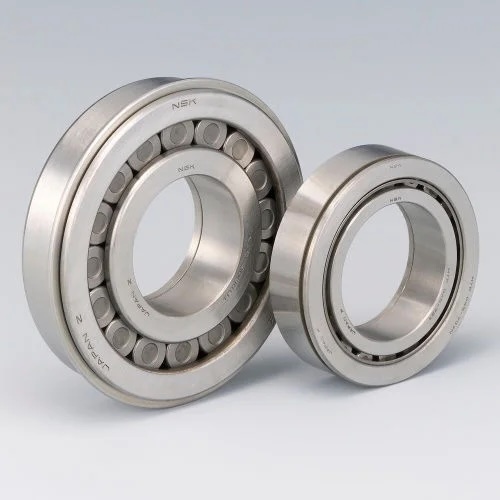
NSK NN and NNU series cylindrical roller bearings are specified to handle higher loads as well for rigidity. The NSK NN3012MBKR and NNU4924MBKR are cylindrical roller bearings designed with double rows of rollers to provide increased load-carrying capacity and further rigidity. This design makes them particularly suitable for machine tool main spindle applications where high radial stiffness and precise runout are critical.
NSK’s dedication to innovation is exemplified in their ROBUST™ series of spindle bearings. These bearings, with part numbers like the ROBUST™ 100BNR10HTYNDUELP4Y, are for extreme speeds, precision, and durability. The “BNR” indicates an 18-degree contact angle, and the combination of “TYN” and “DUELP4Y” signifies the use of NSK’s exclusive polyamide cage and a universal bearing arrangement with medium preload, respectively.
NSK’s preloaded bearings, identified with part numbers ending in “DU,” “TR,” or “TYN,” are specifically set up to deliver optimal performance by ensuring the correct amount of preload. NSK’s detailed manufacturing process results in bearings that offer high rigidity and precision, minimizing thermal expansion and improving the accuracy of high-speed spindle operations.
Magnetic Bearings
In machine tool spindles, magnetic bearings provide contactless support, allowing the spindle to rotate with virtually no friction. This is achieved through an advanced system of controlled magnetic fields that precisely maintain the spindle’s position. The absence of physical contact translates to a significant reduction in wear and the elimination of lubrication requirements, factors that contribute to the longevity and maintenance-free operation of the spindle.
Instead of standard part numbers, magnetic bearing systems for machine tool spindles are often defined by their key performance attributes and the sophistication of their control systems. Terms like ‘radial magnetic bearing (RMB)’ or ‘axial magnetic bearing (AMB)’ denote their orientation and positioning within the spindle assembly.
Manufacturers such as SKF and Waukesha Bearings may use proprietary nomenclature to denote their magnetic bearing systems. A system designed by SKF could be listed as ‘SKF S2M Magnetic Bearing’, indicating a complete solution customized for high-speed spindle applications.
A magnetic bearing assembly for machine tool spindles is often part of a tailored system that includes the necessary sensors and control units required for seamless operation. For instance, a complete magnetic bearing setup designed for a specific spindle application might be referred to as a system, such as ‘MAGSYS-5000’, highlighting the integrated nature of these advanced support systems.
Tapered Roller Bearings

Tapered Roller bearings are designed to accommodate combined loads acting simultaneously. Combined loads are both radial and axial forces. The projection lines of the raceways meet at a common point on the bearing axis providing a true rolling action. Tapered roller bearings are designed in such a way to provide low frictional moments during operation.
The axial load carrying capacity of tapered roller bearings increases with increasing contact angle. The size of the contact angle is usually between 10° and 30° for tapered roller bearings. A single row tapered roller bearing is normally adjusted against a second tapered roller bearing. By applying a preload, a rigid bearing application can be achieved.
Tapered roller bearings typically have a running-in period, during which a conventional design tapered roller bearing creates friction and wear.
However PIB distributes SKF tapered roller bearing designs that significantly reduce friction, frictional heat and wear if the bearings are mounted and lubricated. The inner ring with roller and cage assembly (cone) can be mounted separately from the outer ring (cup). The separable components are interchangeable. This assists in mounting, dismounting and maintenance inspections. Tapered roller bearings are designed to handle both radial and axial loads. They consist of inner and outer rings with tapered rollers and spacers, maintaining proper roller orientation to optimize load distribution.
Advantages:
- Tapered roller bearings are capable of handling both radial and axial loads making them versatile for various machine tool applications.
- These bearings provide excellent rigidity and stability, ensuring precise machining performance.
- Tapered roller bearings are known for their ability to outperform in demanding applications
Visit the PIB Sales shop today to browse our tapered roller bearings offerings and make a purchase.
Hybrid Bearings

MRC Hybrid ceramic ball bearings combine AISI 52100 steel rings matched with silicon nitride (ceramic) balls. As an excellent electrical insulator, hybrid bearings have a very high-speed capacity and a longer service life than standard bearings.
When electrical current goes across bearings, a washboard pattern shows on the raceways, along with a blueish gray appearance. Typical results include bearing surface damage and failure of the lubricant. The insulating properties of ceramic material does away with these failure modes.Extending the service life of a bearing saves money and time. The initial cost of a hybrid bearing may be higher than a standard steel bearing, but the difference is quickly recovered in maintenance savings. Because of the properties of ceramics, a hybrid bearing’s service life may be over 10 times that of a standard steel bearing.
MRC hybrid bearings run cooler and will be able to operate with thinner lubricant films than standard bearings. Lighter weight ceramic balls and dissimilar materials reduce the risk of false brinelling damage when specifying Hybrid bearings. As ceramic balls are 40% as dense as steel balls, the centrifugal load they generate is less and the internal bearing friction is lower. With lower density and friction the bearing is operating much cooler during operation.
Solid particle contaminants finding their way into bearings can create dents in raceway rolling surfaces and raised edges around those dents. This can cause noise and premature wear as the steel balls roll over those surfaces. Harder ceramic balls smooth the surface roughness with no material removal extending life of the bearing. Hybrid bearings combining ceramic and steel materials offer unique advantages for machine tool applications.
Advantages:
- Hybrid bearings exhibit superior high-speed capabilities, reducing heat generation during operation and enabling faster machining processes
- The ceramic material enhances the bearing’s resistance to corrosion and wear, leading to prolonged service life
- Hybrid bearings provide lower friction, contributing to enhanced efficiency and overall machine performance
- Their unique characteristics make them best suited for specific applications requiring high-speed performance and corrosion resistance.
By carefully considering the machine tool spindles requirements and operating conditions, engineers can optimize machine tool performance.
Factors Affecting Bearing Selection
- Load Capacity and Speed Requirements
Load capacity is a fundamental consideration in bearing selection, as it directly determines the bearing’s ability to support applied loads without experiencing premature failure. Engineers need to evaluate both static and dynamic load conditions to identify the maximum loads the bearing may encounter during operation.
The dynamic load rating (C) is a key parameter provided by bearing manufacturers, representing the load at which 90% of a group of identical bearings can operate without fatigue failure after one million revolutions. By calculating the equivalent dynamic bearing load (P), which accounts for various load components like radial and axial loads, engineers can assess the bearing’s performance under real-life conditions.
Operating speed is equally important, as excessive rotational speeds can lead to significant issues, such as overheating and increased wear rates. The bearing’s limiting speed (n_limit) defines the maximum rotational speed it can withstand without encountering detrimental effects. Engineers must ensure that the bearing’s dynamic load rating and limiting speed align with the specific requirements of the application to avoid premature failure and ensure optimal performance.
- Rigidity and Precision
Rigidity is crucial in high speed machine tool spindles where accurate positioning and minimal deflection are essential. High-rigidity bearings ensure the shaft and component remain in its intended position, ensuring precision and repeatability.
Two essential measures of rigidity are axial stiffness (K_a) and radial stiffness (K_r). Axial stiffness reflects the bearing’s resistance to axial deflection when subjected to axial loads, while radial stiffness denotes the resistance to radial deflection under radial loads. Bearings with high stiffness values are favored for applications requiring precise positioning, such as CNC machines, robotics, and optical equipment.
In precision engineering, low runout and axial runout are essential to minimize eccentricities during rotation. Bearings with tight dimensional tolerances, such as those conforming to ABEC 7 or higher, ensure low runout and axial runout values, contributing to enhanced precision and smoother operations in high-performance machine tool spindles.
- Environmental Conditions
Environmental factors significantly influence bearing selection, as harsh conditions can lead to premature wear and failure. Factors such as humidity, dust, aggressive chemicals, or abrasive particles can compromise bearing performance and longevity. To address these challenges, engineers may opt for bearings with additional protective features:
- Sealed or shielded bearings offer an effective defense against contaminants, preventing external particles from infiltrating the bearing and reducing maintenance needs.
- In corrosive environments, bearings made from stainless steel, ceramic, or other corrosion-resistant materials are preferred to mitigate the effects of chemical exposure.
- Additionally, specialized coatings, such as Physical Vapor Deposition (PVD) or Diamond-Like Carbon (DLC), provide an extra layer of protection against corrosive agents, further extending bearing life and reliability.
Bearing Selection Process
The selection of bearings is a critical process in engineering design, particularly in machine tools and mechanical systems where precise motion, load-bearing capacity, and longevity are essential.
1. Identifying Machine Tool Requirements
The first step in the bearing selection process is to clearly define the machine tool’s operational requirements. This involves understanding factors such as the type of load (radial, axial, or combination), operating speed, temperature, and environmental conditions. The nature of the application influences the choice between various bearing types, including deep groove ball bearings, cylindrical roller bearings, angular contact bearings, and others.
2. Load and Speed Calculations
Accurate load and speed calculations are pivotal in determining the appropriate bearing size and type. The applied loads can vary due to forces generated during operation or external factors such as vibration. Engineering standards, such as ISO 281:2007 for calculating dynamic load ratings, provide a basis for estimating the bearing’s capacity to handle loads while considering factors like load distribution and operating conditions. Calculations must also account for rotational speed, as higher speeds can affect bearing performance and durability.
3. Life Calculation Methods
The life expectancy of a bearing is crucial for predicting maintenance intervals and overall system reliability. The bearing’s rated life, defined as the number of revolutions or operating hours until 90% of a group of identical bearings have failed, can be calculated using industry-standard formulas, including ISO 281 and ASTM F2812. These calculations consider factors like load, speed, material, lubrication, and operating conditions to estimate the bearing’s operational lifespan.
4. Lubrication Selection
Proper lubrication is fundamental to bearing longevity and optimal performance. The lubricant’s role is to reduce friction, dissipate heat, and protect against wear and corrosion. The selection of lubricant type (oil or grease) and properties (viscosity, additives, etc.) depends on factors such as speed, temperature, load, and sealing mechanisms. Industry standards like ISO 281:2007 provide guidelines for determining lubrication requirements based on operating conditions.
5. Preload and Clearance Considerations
Achieving the right amount of preload and clearance is essential in minimizing unwanted internal movement of the bearing elements. Preload is an intentional axial force applied to eliminate rolling element clearance, ensuring higher stiffness and accuracy in precision applications. Conversely, controlled clearance is necessary in applications where thermal expansion or load variations are expected. Selecting the appropriate preload or clearance level involves balancing stiffness, thermal effects, and operational demands.
Conclusion
Machine tool spindles can only operate with high-quality precision bearings. Contacting and working with qualified authorized distributors is a good first step in the process. The selection and replacement of precision bearings used in machine tool spindles is critical and must be exact. Missing details for lubrication, clearance, precision grades, contact angles etc. can all result in the cause of premature failure.
Selecting the right machine tool ball bearing is necessaryl for achieving the precision and efficiency required in today’s advanced manufacturing processes. Understanding each bearing type and the specific needs of your machinery is important in ensuring optimal equipment performance and life.
If you’re ready to take the next step in enhancing your machine tool bearing performance, look no further than PIB Sales. At Pacific International Bearing Sales, we are dedicated to providing quality ball bearings. Our bearings are designed to deliver superior precision and performance, ensuring that your machinery operates at its best.
We invite you to explore our selection and find the perfect match for your requirements at the PIB Sales shop. Our extensive inventory is backed by expert guidance and customer service, ensuring that you not only receive a product but also a partnership that contributes to the success of your operations.
Still have a question or need to discuss something? Contact us to get help.