Full ceramic bearings are made of ceramic rings and balls with a non-metallic retainer and seals. Full ceramic bearings are excellent for high-speeds, low friction, and offer exceptional resistance to corrosion and elevated temperatures. However, one very important difference is that load ratings are lower for an all-ceramic bearing as compared to an all-steel bearing or Hybrid bearing. So be careful when sizing full ceramic bearings into your application. Hybrid ceramic bearings will generally have an 85% static load rating capacity using steel ratings tables.
Check with the manufacturer for Full Ceramic Dynamic and Static ratings for the size bearing you are designing into your application.
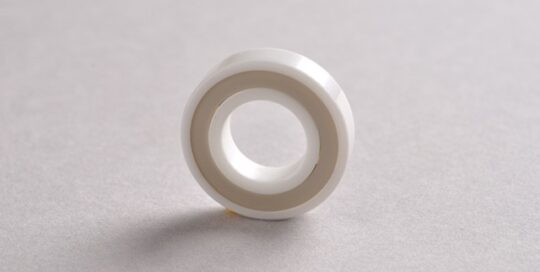
Ceramic bearing rings, balls, and cages made from ceramic may be used in applications where conventional bearings are not suited. Ceramic bearings are non-magnetic and are self-insulating. Ceramic bearings have a longer service life and are highly heat resistant. The cage can be made of non-metallic material, resin, or composite material depending on the intended use. In this article, we will explore the different types of full ceramic bearings, their advantages, applications, challenges, and their future prospects.
- NSK full ceramic bearings data
- Koyo full ceramic bearings data
Materials for Full Ceramic Bearings
Silicon Nitride (Si3N4)
Silicon nitride is a chemical compound of the elements silicon and nitrogen. Si3N4 is the most thermodynamically stable and commercially important of the silicon nitrides. Silicon nitride ceramic bearings are the most popular type of full ceramic bearings due to their excellent properties. Full ceramic bearings exhibit high strength against fractures and are resistant to wear and corrosion. Silicon nitride bearings are commonly used in high-speed applications such as dental drills, machine spindles, and turbochargers.
Zirconia (ZrO2)
Zirconia ceramic bearings have high strength, hardness, and toughness. They are also resistant to wear, corrosion, and high temperatures. Zirconia bearings are used in various applications, including pumps, valves, and chemical processing equipment.
Alumina
Alumina ceramic bearings have excellent thermal and chemical stability, high strength, and hardness. ZrO2 is commonly used in harsh environments such as vacuum environments, high-temperature furnaces, and chemical processing equipment.
Advantages of Full Ceramic Bearings
Silicon nitride balls are harder than steel and lighter, which reduces contact with the bearing raceway. Specifying ceramic balls instead of steel balls results in 80% less friction, three to ten times longer life, 80% higher speed, and 60% less weight. Full ceramic bearings that can operate with little to no lubrication are superior for corrosion resistance and will operate in significantly higher temperatures than steel bearings.
- High Speed Capabilities
Full ceramic bearings have lower friction and heat generation as compared to metal bearings, allowing them to run at higher speeds without the risk of damage or failure. Applications include machine tool spindles, turbochargers, gas turbines, centrifuges, spindle motors, dental handpieces, polygonal mirror scanning motors, and twine spindles.
- Low Friction
Full ceramic bearings have lower friction and heat generation than metal bearings, which results in reduced wear and longer bearing life.
- Corrosion Resistance
Ceramic bearings are inherently resistant to corrosion, making them ideal for use in harsh environments where traditional metal bearings would quickly degrade. Applications include semiconductor equipment, plating equipment, composite fiber equipment, and optical film equipment.
- Non-Magnetic Properties
Ceramic bearings are non-magnetic, making them ideal for use in applications where magnetic interference can be a problem such as in medical equipment. Applications include electric motors, superconduction equipment, and atomic power insulation.
- High Temperature Resistance
Ceramic bearings can withstand elevated temperatures, making them ideal for use in high-temperature applications such as jet engines and gas turbines. Other applications include heat treatment furnaces, heat rollers, and chemical fiber instruments.
- Increased Durability
Ceramic bearings have higher hardness and resistance to wear than traditional metal bearings, resulting in longer bearing life and reduced maintenance costs.
- Lightweight
Ceramic bearings are lighter than traditional metal bearings, which can reduce the overall weight of a machine or equipment, resulting in improved performance and efficiency.
Other Applications for Full Ceramic Bearings
Full ceramic bearings are used in a wide range of other applications, including:
- Chemical processing equipment such as pumps, valves, and bearings in harsh environments;
- Medical equipment such as MRI machines and surgical tools;
- High-temperature furnaces and kilns;
- High-speed machinery and equipment such as machine tool spindles, dental drills, and turbochargers;
- Aerospace and defense applications such as jet engines and missile guidance systems.
Challenges of Full Ceramic Bearings
One of the biggest challenges specifying full ceramic bearings is the higher cost of the material as compared to steel bearings. Ceramic materials are more expensive to produce than steel, which can make full ceramic bearings more costly. Another consideration is possible lower load ratings for similar sized steel bearings. Please check with your distributor to obtain the load ratings. This is a particularly important exercise when investigating the use of Full Ceramic bearings in any application.
Conclusion
Full ceramic bearings offer several advantages over traditional metal bearings, including high-speed capabilities, low friction, corrosion resistance, and increased durability. They are used in a wide range of applications, from high-speed machinery to harsh environments such as chemical processing equipment and high-temperature furnaces.
While there are challenges associated with the use of full ceramic bearings, such as cost and load ratings, ongoing research and development are likely to lead to improved manufacturing techniques and more widespread use of these bearings in the future.