In this article, I will discuss different bearing designs used in Turbomolecular pumps. The working principle of a Turbomolecular pump and the leading Bearing brands. I will add a list of turbomolecular bearing part numbers and where you can buy them. Pacific International Bearing (PIB) represents the highest quality turbomolecular pump bearings from manufacturers who have extensive knowledge and years of experience.
Bearings specified for use in Turbomolecular Pumps must survive in a very difficult environment. Turbomolecular pumps are commonly found in semiconductor, chemical analysis and SEM (Scanning Electron Microscope) equipment. Bearings in these environments must work in the 10-6 to 10-9mm Bar region.
Turbomolecular Bearings in vacuum conditions must be reliable, offer high-speed capabilities and last. Minimum life requirements exceed 30,000 hours of life, having only a small application of lubricant. To achieve the required high-speed rotation, somewhere in the range of 30,000 to 90,000 RPM, the bearings must have low friction, exceptional stability, and resistance to wear.
In operation, bearings must have low vibration and noise characteristics. Those manufacturers capable of designing and manufacturing turbomolecular bearings use special surface finish and harmonic standards during manufacturing. In many cases, bearings can be designed to have an infinite fatigue life.
What Are Turbomolecular Pump Bearings?
Turbo Molecular Pumps operate where gas molecules move in very specific biased directions when hit by a solid surface. The moving pump blade due to its interaction with the gas molecules can be guided in a predictable direction. Ultra high operating pressures are present and range between 103 and 10-11 mbar, with pumping speeds of between 10 and 4,000 l/s. Bearings must operate with no downstream contamination and no lubrication loss.
In this difficult environment, the bearing rings must be of the highest precision and have controlled harmonic amplitudes for the raceways. The bearings must have a very high if not exceptional surface finish. In addition to supporting the rotor, TMP bearings need to maintain precise alignment between the rotor and the stator. If this precision is not maintained then catastrophic failure is likely. Bearings applied in TMP applications must maintain precision performance while subjected to high temperatures and corrosive environments many times without the benefit of conventional lubrication.
Manufacturers such as Barden Bearing manufacture bearings specifically designed for use in Turbomolecular pumps and will manufacture special custom designed bearings for customers. Requirements for turbomolecular bearings include special low outgassing lubrication and are available from Pacific International Bearing in the normal bore size range from 4mm-12mm.
Turbomolecular bearings can be manufactured from Cronidur 30 stainless steel material which has greater corrosion resistance and is longer wearing than 440C stainless steel.
Leading Manufacturers like Barden Bearing commonly use AMS5898 high-nitrogen steel for optimum performance and reliability.
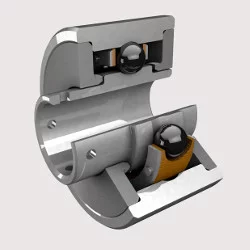
The use of AMS5898 material ensures excellent performance when paired with a ceramic ball rolling element. This design is employed to provide high performance and meet the demands for exceptional corrosion resistance and high-speed requirements. To meet the requirement for higher pumping speeds Barden turbomolecular bearings use high-speed ceramic small ball technology.
Barden offers shielded angular contact bearings to guard against contamination. Barden also offers these bearings in open and sealed versions as required by each application. The Barden part numbering system includes a “TMP Standard” having a special internal finish which provides for even more quieter running and therefore higher reliability and extended life.
Schaeffler Bearing has an outstanding reputation as a quality manufacturer of turbomolecular bearings
As Compressors and vacuum pumps function in many areas of commerce and industry Schaefller offer FAG, INA, and Barden product lines for almost every need. ln Schaeffler’s large portfolio of bearings they can conquer almost every application requirement. Schaeffler offers bearings for every purpose and has the largest range of bearings in X-life quality. The Barden product line is particularly suited for turbomolecular bearing applications.
Schaeffler products used in applications for compressors
1. Compression of compressed air, both mobile and stationary, for example in factory automation, materials handling, construction machinery, etc;
2. Refrigeration compression for industrial and commercial cooling and central air-conditioning systems;
3. Process gas compression in process engineering, the chemical industry or biotechnology;
4. Compression in the oil and gas industry, whether upstream, midstream or downstream.
Schaeffler products used in Application for Vacuum Pumps
1. Generation of negative pressure in packaging technology, as in the food and pharmaceutical industries;
2. High-purity vacuum, dry-running vacuum pumps applied in the manufacturing of silicon wafers;
3. Vacuum as an important component in the chemical industry;
4. Simulation and component testing in the aerospace industry.

The challenge for turbo molecular pump bearings includes:
- Long life expectancy;
- Absolute reliability;
- High speeds;
- Low noise level;
- Low vibration;
- Cleanliness.
Significant performance can be achieved through bearing design optimization. In some cases, the use of enclosed bearings with seals and or shields are needed to protect against contamination and to increase life. Choosing ceramic balls (Si3N4) for higher speeds and negligible friction is essential for optimizing bearing dynamics. Using an Integrated tribological concept for lubricant, preservation, surface quality, and materials yields satisfactory results according to Barden Bearing. Some companies like GMN use their own GMN TXM cage resulting in lower vibrations and quiet operation.
GMN Bearing Company offers Spindle ball bearings for Turbomolecular Pump applications and are available in Open or shielded with Silicon nitride balls with a Vacuum of up to 10-3 mbar and with Speed characteristics up to 1,1 x 106 mm/min.
- Service life > 30.000 h
- Cages: oil impregnated hard tissue cage or TXM cage
- Special design (dimensions, design, cage)
- Optimized grease reservoir

- Open or covered
- Silicon nitride spheres (Si3N4)
- Vacuum to 10-3 mbar
- Characteristic RPM up to 0,8 x 106 mm/min
- Oil lubrication
- Service life > 30.000 h

Why Bearing Quality Matters in Turbomolecular Pumps
The quality of bearings inside a turbomolecular pump is directly tied to how well the pump performs, how long it lasts, and how reliable it is during day-to-day operation. A high-quality bearing gives you a pump that runs smoother, with less vibration and noise. This is especially important in labs, semiconductor manufacturing, or any process where even a small amount of vibration can cause a drop in performance or product quality.
Inferior bearings tend to wear out fast. They can’t hold tolerances, leading to wobble or drift in the rotor. As a result:
- The pump may lose its ability to maintain a high vacuum.
- Operating temperature can climb due to low quality, misapplied or improperly designed bearings creating friction and heat.
- The lifespan of the pump drops, with a higher risk of unplanned breakdowns.
- Service intervals become shorter, adding to downtime and expense.
Premium bearings, like precision ceramic hybrids or top-grade steel types, hold up under the stress of non stop rotation. They stay quiet, resist heat, and keep the shaft centered. Clean-room assembly and strict quality checks are a must since even a speck of dust or a tiny defect can start a chain reaction that fails.
Quality bearings also mean a lower total cost of ownership. You spend less on emergency repairs, replacement parts, and maintenance labor. More importantly, your vacuum process stays on track, free from sudden interruptions. In short, the quality of turbomolecular pump bearings is a strong predictor of equipment uptime, pump output, and production consistency.
Vacuum Technology
GMN develops complete designs in collaboration with the industry for special bearings, in particular for turbomolecular pumps (TMP).
Emergency Touchdown Bearings
Barden Bearing has also developed Emergency Touchdown support bearings for when a magnetic bearing system fails. Many industrial applications such as turbo blowers, turbo compressors, and turbomolecular pumps may employ a magnetic bearing system and so it is possible to back it up with mechanical Barden emergency touchdown support bearings.

If a complete electronics failure occurs, Barden mechanical Touchdown bearings protect the system from a total crash. In this application, the bearing needs to accelerate from zero to 2.7 or higher ndm instantly, even if the TD bearing sat idle for years. In this case, the bearing system must instantly and accurately control the rotor and the extremely high radial, axial and shock loads. The initial shock load is high due to the gyroscopic forces generated.
Barden bearings have been developed for this application using ceramic balls and a full ball complement design. Barden uses AMS5898 material to create a reliable exceptional performance and corrosion resistant TD bearing. The Barden bearing design is optimized for the maximum number of touchdowns.
Of course, you can specify and use Barden’s full complement hybrid ceramic bearings in numerous other applications.
Magnetic Bearings
As I mentioned earlier, Magnetic bearings are also used in Turbomolecular pump applications. Magnetic bearings have represented a significant technological advancement in TMP bearing design. These bearings operate without any physical contact by suspending the rotor using magnetic fields generated by electromagnets. This lack of contact means that there is no wear and tear, enabling the pump to operate more cleanly and with less maintenance. Magnetic bearings can be controlled actively by adjusting the electromagnetic fields to maintain the rotor position, a feature provided by brands such as Calnetix Technologies. This level of control can compensate for imbalances and external vibrations, contributing to the pump’s overall efficiency and stability.
Radial Ball Bearings
Ball bearings are the most conventional type of bearings used in TMPs. They typically consist of steel or ceramic balls contained within inner and outer raceways. In TMP applications, angular contact ball bearings are also widely used due to their ability to handle both radial and axial loads simultaneously, a crucial factor for the stability of the rotor at high speeds.
Part Number | Dimensions | Ball Type |
PIB34TPH | 4mm 13mm 5mm | Ceramic |
YC1340TPHW6 | 4mm 13mm 6mm | Ceramic |
PIB34EXT | 4mm 13mm 5mm | Ceramic |
SS684C14/20 | 5mm 11mm 3mm | Steel |
YCA1650C-GHY72 | 5mm 16mm 5mm | Ceramic |
YCA1750SSW75 YCA1750SSW85 YCA1835SSW85 PIB250A | 5mm 17mm 7.5mm 5mm 17mm 8.5mm 5mm 18.3mm 8.5mm 6mm 19mm 8mm | Ceramic Ceramic Ceramic Ceramic |
DDL-1360 SS686C3NGVFB YCA1960C-GHY72 PIB70A | 6mm 13mm13.5mm 6mm 13mm 3.5mm 6mm 19mm 6mm 6.1mm 19mm 8mm | Steel Steel Ceramic Ceramic |
HYSV607P4D15 | 7mm 19mm 6mm | Ceramic |
HYSV607P4T4HB | 7mm 19mm 6mm | Ceramic |
PIB36TPH/NG | 7mm 19mm 7mm | Ceramic |
YCA2070SSW9 SV608P4D15 HYSV608P4D15 | 7mm 20mm 9mm 8mm 22mm 7mm 8mm 22mm 7mm | Ceramic Steel Ceramic |
CER-2280ZZSD602 | 8mm 22mm 10.31mm | Ceramic |
C38STX363 | 8mm 22mm 10.31mm | Ceramic |
CER-2290ZZSD600 | 9mm 22mm 10.31mm | Ceramic |
PIB1900V | 10mm 22mm 6mm | Ceramic |
This listing is for bearings already designed into popular turbomolecular pumps.
Types of Bearings Used in Turbomolecular Pumps
Selecting the right bearing type for a turbomolecular pump shapes its performance, reliability, and maintenance cycle. The material of the bearing, its method of supporting the rotor, and the way it manages friction all play a role. Each option has its own strengths. We’ll break down the main types so you know what to expect from each.
Ceramic vs. Steel Bearings
Steel bearings have long been the standard choice for turbomolecular pumps. They use high-purity bearing steel and are known for their toughness and shock resistance. Steel bearings manage moderate speeds and loads well. However, at the very high speeds seen in turbomolecular pumps, steel suffers from friction and heat build-up. Regular lubrication becomes essential. Contaminants can shorten lifespan quickly.
Ceramic bearings, usually made from silicon nitride, push performance further. They weigh less than steel, which reduces centrifugal force at top speed. Ceramics run cooler, resist wear, and won’t rust. These properties make them a popular option for pumps running almost nonstop or in harsh settings.
Typical advantages of ceramic over steel bearings:
- Lower friction: Less energy lost to heat, smoother rotation.
- Greater lifespan: Resist wear, especially with poor lubrication or variable loads.
- Corrosion resistance: Handle moisture and aggressive gases better.
- Reduced maintenance: Less frequent lubrication required.
Steel bearings still win out for lower-cost or less-demanding jobs, but ceramics are the choice for speed, long life, and harsh process gases.
Magnetic Bearings vs. Mechanical Bearings
Mechanical bearings—such as ball or roller types—physically support the shaft. They handle weight and keep everything centered. This contact results in gradual wear over time. They need periodic checks and lubrication, and can generate dust particles if they degrade.
Magnetic bearings take a different approach. They float the shaft on a cushion of controlled magnetic fields. No physical contact means no classic wear, and almost no maintenance. These systems run quietly and can keep the shaft perfectly centered, even as temperature or load shifts.
Here are the main practical differences:
- Wear: Magnetic bearings don’t wear in the traditional sense. Ball bearings wear out and eventually fail from mechanical stress.
- Maintenance: Mechanical bearings require regular service. Magnetic types have a much longer maintenance interval.
- Noise and vibration: Magnetic bearings are quieter, with less vibration—helpful for sensitive lab work.
- Complexity and cost: Magnetic systems are more complex and expensive, often reserved for the most demanding installations.
Choose magnetic bearings for the absolute best reliability, clean operation, and lowest maintenance, especially in process-critical areas. Mechanical bearings still see wide use when budgets are tight or conditions are less extreme.
Hybrid Bearings: Benefits and Applications
Hybrid bearings offer a middle ground. They combine a steel bearing race with ceramic rolling elements (balls or rollers). This blend captures some of the best traits from each material.
Hybrid bearings excel in:
- Performance: They operate at higher speeds than full steel bearings.
- Reliability: The ceramic balls resist wear and won’t seize if lubrication runs low, while the steel races maintain mechanical strength.
- Reduced heat: They generate less heat at top speed, which limits thermal growth and distortion.
- Lifespan: They outlast standard steel types, cutting replacement costs.
In turbomolecular pumps, hybrid bearings are common where the pump runs fast but must also take mechanical shocks—like startups or shutdowns. They perform well in clean-room environments, semiconductor production, and other applications where both uptime and purity are important. While pure ceramic bearings are best for some scenarios, hybrids balance price, performance, and lifespan for most demanding vacuum systems.
Key Factors in Choosing Turbomolecular Pump Bearings
Selecting the right bearings for a turbomolecular pump requires more than picking a type or brand. Each application demands performance across different areas, from high speeds to long operating cycles. When you know the key factors, you avoid costly breakdowns and raise productivity. Here’s how speed, vibration, heat, and maintenance needs affect your decision.
High-Speed Performance and Tolerance
Speed is a constant challenge in turbomolecular pumps. Bearings must hold tight tolerances to keep the shaft stable at rotational speeds of up to 90,000 RPM. Even a small error at these speeds can throw the rotor out of balance.
Precision-machined bearings limit runout and shaft movement. This reduces the risk of contact between moving parts, cutting down on wear and the chance of sudden failure. Ceramics and hybrid designs excel here because they offer lower friction, produce less heat, and can run at higher speeds without distortion.
Look for bearings with strict manufacturing controls:
- Low roundness deviation
- Minimal surface roughness
- Exact internal geometry
These qualities keep the rotor steady, even with temperature swings and long shifts. The bearings must also handle sudden changes in speed without damage.
Vibration and Noise Considerations
Bearings play a direct role in how much vibration and noise the pump creates. Excess vibration affects both the system and the finished product—especially in sensitive lab settings or microchip production.
Properly chosen bearings cut down on rotor wobble. Hybrid and magnetic bearings stand out for low vibration profiles because their smooth surfaces and light rolling elements dampen movement. Quieter pumps also produce less strain on nearby equipment and operators.
Several features help reduce vibration:
- Tight clearances
- Balanced bearing assemblies
- High-grade surface finishes
With less vibration, pumps last longer and keep other components from coming loose over time.
Heat Resistance and Lifespan
Turbomolecular pumps generate significant heat, especially at top speeds. Bearings exposed to high temperatures can break down, lose lubrication performance, and warp.
Materials like silicon nitride in ceramic or hybrid bearings stand up to heat better than plain steel. These materials maintain shape and surface hardness when temperatures rise, so they resist wear longer.
Heat-resistant bearings provide:
- Consistent performance during long runs
- Better resistance to lubrication breakdown
- Longer replacement intervals
A bearing’s lifespan directly links to its ability to resist heat. Keeping bearings cool with proper materials and, if needed, added cooling features, guards against early failure.
Maintenance Requirements and Downtime Impact
Maintenance is more than a schedule—it’s a direct cost, both in labor and lost productivity. Some bearing types, like magnetic and certain ceramics, require far less upkeep than standard steel options.
Consider maintenance needs when planning your budget:
- Frequency of lubrication
- Inspection intervals
- Ease of bearing replacement
Bearing that last longer and need less service means pumps spend more time running and less time waiting on repairs. Every hour of downtime cuts into output. For critical systems, use bearings with proven longevity and reduced service intervals, even if upfront costs are higher. The saving shows up through fewer unplanned shutdowns and less waste from inconsistent vacuum performance.
Making smart choices on bearings protects both the pump and your bottom line.
Frequently Asked Questions
How long do turbomolecular pump bearings last?
Service life depends on the type of bearing, pump speed, operating conditions, and maintenance schedule. Standard ball bearings, when used in clean, well-controlled applications, can last between 20,000 and 60,000 hours. That matches about two to seven years in regular use.
Ceramic and hybrid bearings often last longer than all-steel ones. They have higher wear resistance and better heat tolerance. Magnetic bearings have the highest life expectancy of all, sometimes running well beyond 100,000 hours, since there is no contact or wear.
A few factors can reduce the lifespan:
- High particulate loads or exposure to corrosive gases
- Overheating or poor lubrication (for lubricated bearings)
- Shaft misalignment or excess vibration
- Skipped or improper service intervals
Always check the manufacturer’s guidelines and look for early signs of trouble. Routine inspection and support keep most issues from turning into costly failures.
What are the signs of bearing failure in vacuum pumps?
Early detection can prevent catastrophic damage. There are several common symptoms that signal bearing problems:
- Increased noise or unusual sounds: New or louder grinding, clicking, or humming often means damage to the balls or races.
- Higher vibration levels: Excess vibration tells you there may be pitting, flat spots, or loss of smooth rotation.
- Rise in temperature: Bearings create more heat when they begin to fail. Surface temperature checks can pick up early warning signs.
- Changes in vacuum quality: As bearings degrade, the pump may struggle to hold the same vacuum level or take longer to reach set points.
- Lubricant leaks or dust buildup: For mechanically lubricated types, leaking oil or the presence of fine debris near the bearing area may show internal damage.
Technicians should use vibration monitoring, temperature measurements, and sound checks to spot problems early. Scheduled shutdowns for inspection give a chance to confirm concerns before the bearing fails completely.
Are magnetic bearings better than ceramic bearings?
Magnetic and ceramic bearings each bring clear advantages, depending on your needs.
Magnetic bearings use an active magnetic field to support the pump shaft. There is no physical contact. The benefits are:
- Nearly zero wear, so bearing life is much longer.
- No need for lubrication, which means less maintenance.
- Lower vibration and noise levels—helpful for sensitive tasks.
- Clean operation since no particles are shed from wear.
Ceramic bearings (like silicon nitride balls) do have contact points, but they’re much harder and lighter than steel. Their main strengths are:
- Higher speed tolerance compared to steel.
- Great resistance to corrosion and high heat.
- Lower friction than all-steel options.
If you need the absolute minimum in particulate generation, lowest possible vibration, or the longest maintenance intervals, magnetic bearings are the top pick. They do cost more and use more complex electronics. For most demanding vacuum work, ceramics (or ceramic hybrids) balance reliability, speed, and cost.
Match the bearing to the process risk, budget, and downtime tolerance. For high-purity or long-life installs, magnetic types often win. For most daily lab or process use, ceramic remains a solid, practical choice.
The Bottom Line
Choosing the right turbomolecular pump bearing sets the foundation for system reliability and service life. Material and bearing type must match the demands of your application—speed, load, thermal limits, vibration, and maintenance. As highlighted, ceramic, hybrid, steel, and magnetic bearings each bring distinct advantages when applied intentionally.
Take time to evaluate your process and weigh long-term costs against up-front investment. The right bearing decision reduces breakdowns, extends maintenance intervals, and protects product quality. Review manufacturer specifications closely and stay proactive with regular inspections. For more information contact us at [email protected].