Understanding friction torque in bearings will help engineers in selecting the correct design for their application. In this article, we will explore factors affecting friction torque in bearings, frictional losses in bearings, and the numerous factors used to reduce friction torque.
What is Friction Torque?
In mechanics, the contact resistance that occurs between mating surfaces when moving is called friction torque. The rotation of the bearing’s mating components, outer rings, inner ring, retainers, seals and shields, and the rolling element all are part of the friction factor. The rotational force is measured in pounds, feet, or newton meters. In golf, a good example of friction torque is when a golf ball hits the ground. This effect is due to the friction torque applied to the golf ball from the friction between the golf ball and the ground.
In the context of mechanical systems, friction torque plays a significant role in determining the efficiency and performance of rotating machinery. It can be encountered in various forms, such as static friction torque, which needs to be overcome to start the rotation of an object, and dynamic or kinetic friction torque, which is experienced when an object is already in motion.
Understanding and managing friction torque is essential for engineers and designers for several reasons:
- Energy Efficiency: High friction torque can lead to increased energy consumption as more power is required to overcome the resistance to motion. Reducing friction torque can significantly enhance the energy efficiency of mechanical systems.
- Wear and Tear: Friction inevitably leads to wear, affecting the longevity and reliability of mechanical components. By minimizing friction torque, the rate of wear can be reduced, extending the life of parts and reducing maintenance costs.
- Noise Reduction: Friction torque can also be a source of noise in mechanical systems. Reducing it can contribute to quieter operation, which is particularly important in consumer products and in environments where noise is a concern.
Applications of principles that reduce friction torque, such as the use of lubricants, selection of materials with lower coefficients of friction, and precision engineering of component surfaces, are widespread. These strategies are crucial in automotive engineering, aerospace design, manufacturing equipment, and even in everyday household appliances.
Factors Affecting Friction Torque in Bearings
Bearings play a critical role in various industries, including industrial, medical, automotive, and aerospace. A bearing’s performance is measured by the ability to minimize friction and withstand loads while operating at various speeds. Friction torque is an essential parameter that determines the power loss from bearings.
Bearing Design: How bearing geometry impacts friction torque
The bearing’s geometry plays a crucial role in determining the friction torque. The contact angle, raceway curvature, and ball diameter significantly impact the bearing’s performance. Smaller contact angles result in higher radial loads, but higher friction torque. In contrast, larger contact angles reduce the radial loads but lead to lower friction torque. Raceway curvature also affects the friction torque, with tighter radii resulting in higher friction torque. Similarly, smaller ball diameters lead to higher friction torque.
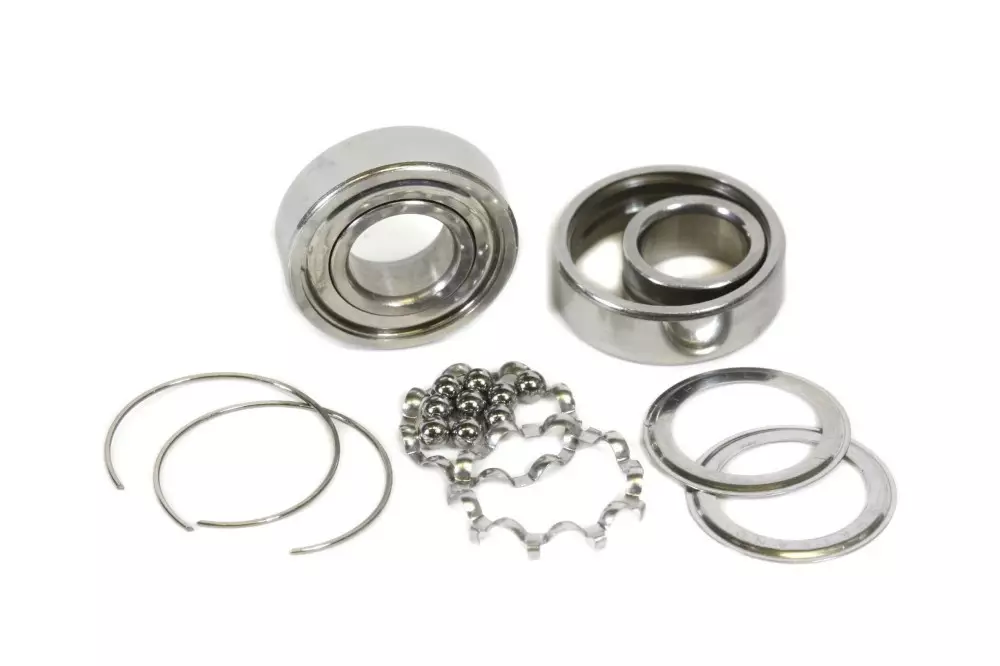
For example, reducing the contact area between the bearing surfaces can decrease frictional losses, resulting in lower friction torque. Engineers can also optimize the geometry of the bearing elements by increasing the number of rolling elements, reducing the diameter of the bearing, or using a more precise manufacturing process to reduce roughness and irregularities.
Bearing Materials: How material selection impacts friction torque
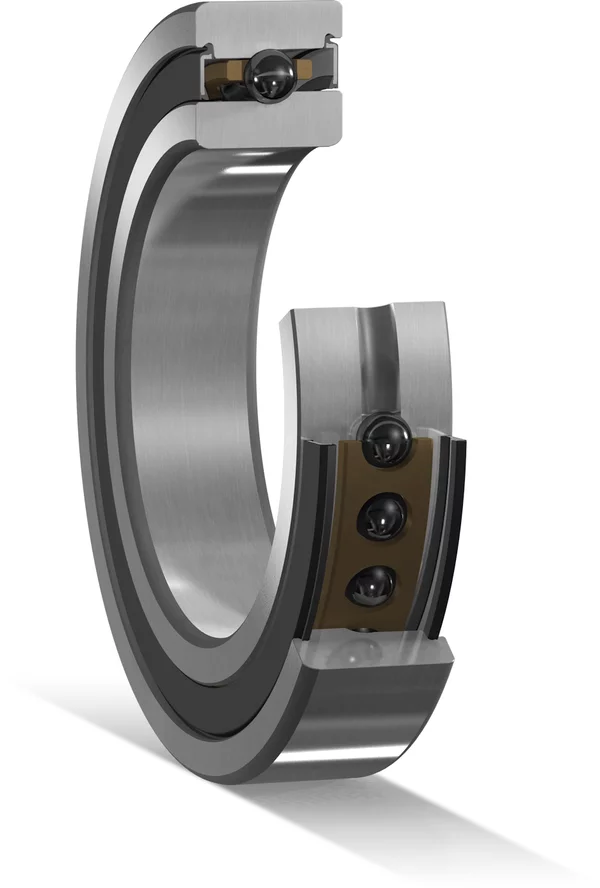
The materials used in a bearing should be selected based on their ability to withstand high loads and reduce friction. Generally, bearings are manufactured from AISI 52100 steel. Smaller bearings, however, may use 440C stainless Steel as standard. Hybrid bearings that use steel races and ceramic balls are an excellent choice for reducing friction and increasing speed.
Full ceramic bearings are another option for reducing friction and are increasingly used in various applications.
Combining materials like ceramics, Cronidur 30, 440C, and AISI 52100 steel with phenolic, steel, polyamide cages, and internal clearance all has significant effects on torque values.
Bearing Lubrication: The role of lubrication in reducing friction torque
Lubrication is essential for reducing friction torque in bearings. Proper lubrication ensures that the bearing surfaces remain separated, reducing friction and wear. The lubricant’s viscosity, temperature, and composition affect the bearing’s performance. High-viscosity lubricants are suitable for heavy loads, while low-viscosity lubricants are ideal for high speeds. Temperature also plays a critical role, as elevated temperatures can degrade the lubricant and reduce its effectiveness.
Bearing Load and Speed: How load and speed impact friction torque
The bearing load and speed are critical factors affecting friction torque. As the load and speed of the bearing increases, the friction torque also increases, leading to higher energy losses. The contact pressure between the bearing surfaces also increases with increasing load, leading to higher frictional losses. Understanding the load and speed requirements is crucial for selecting the appropriate bearing design and material for optimal performance. The bearing’s load capacity and speed ratings must be considered to avoid premature failure due to excessive loads or speed.
Frictional Losses in Bearings
There are two types of friction that engineers need to consider: static friction and dynamic friction.
Static friction is the force that must be overcome to initiate motion between two surfaces. This is also known as the “breakaway” force and is typically higher than the force required to maintain motion. Dynamic friction is the force required to maintain motion between two surfaces once motion has been initiated.
How to measure and calculate frictional losses
Measuring and calculating frictional losses in bearings involves several methods, including torque measurement, power consumption analysis, and temperature rise analysis.
Torque measurement is the most common method used to measure frictional losses in bearings. It involves measuring the amount of torque required to rotate the bearing under a specified load and speed. The difference between the input torque and the output torque represents the frictional losses. This method is relatively simple and straightforward, but it requires specialized equipment, such as a torque sensor and a dynamometer.
Power consumption analysis is another method used to measure frictional losses. It involves measuring the electrical power consumed by the motor that drives the bearing. The power consumed is proportional to the frictional losses in the bearing. This method is suitable for measuring frictional losses in larger bearings, such as those used in heavy machinery and industrial applications.
Power loss due to friction can be calculated using the following formula:
P = T × ω
where:
- P = power loss due to friction
- T = frictional torque
- ω = angular velocity
Temperature rise analysis is another method used to measure frictional losses in bearings. It involves measuring the temperature rise of the bearing during operation. The amount of temperature rise is proportional to the amount of energy lost due to friction. This method requires specialized equipment, such as infrared cameras and temperature sensors.
Temperature rises due to friction can be calculated using the following formula:
ΔT = P × Rth
where:
- ΔT = temperature rise due to friction
- P = power loss due to friction
- Rth = thermal resistance
Once the frictional losses have been measured, engineers can use various calculations to analyze the data. One common calculation is to calculate the friction coefficient, which is the ratio of the frictional force to the normal force.
Friction coefficient can be calculated using the following formula:
μ = Ff/Fn
where:
- μ = friction coefficient
- Ff = frictional force
- Fn = normal force
The friction coefficient can be used to compare the performance of different bearings and lubricants.
Another calculation is to calculate the energy lost due to friction, which is the product of the frictional force and the distance traveled.
Energy lost due to friction can be calculated using the following formula:
E = Ff × d
where:
- E = energy lost due to friction
- Ff = frictional force
- d = distance traveled
This calculation can help engineers estimate the amount of energy that can be saved by reducing frictional losses.
Bearing Maintenance for Reducing Friction Torque
Regular maintenance is essential for reducing friction torque and maximizing the service life of bearings. Here are some of the best practices for bearing maintenance:
Proper lubrication and cleaning. Proper lubrication and cleaning are crucial for maintaining optimal bearing performance. Lubrication reduces friction and wear, while cleaning removes contaminants that can damage the bearing surfaces. Early detection of bearing wear and tear.
Proper lubrication management includes:
- Selection of the Right Lubricant: Choosing a lubricant with the appropriate viscosity and properties for the specific application and operating conditions.
- Regular Lubrication Schedule: Adhering to a lubrication schedule that matches the manufacturer’s recommendations and the environmental conditions of the application.
- Lubrication Techniques: Applying lubricants correctly to avoid over-lubrication or under-lubrication, both of which can lead to increased friction and wear.
Early detection of bearing wear and tear is critical for preventing catastrophic failures and minimizing downtime. Regular inspections can identify potential issues before they become major problems. Bearing replacement. Bearings should be replaced as soon as signs of wear and tear are detected. Continued use of worn bearings can lead to increased friction, heat, and wear, which can ultimately result in bearing failure.
This includes:
- Visual Inspection: Looking for signs of wear, corrosion, or damage to the bearing surfaces.
- Measurement and Analysis: Measuring clearances and tolerances to assess wear and fit.
- Timely Replacement: Replacing bearings at the first sign of significant wear or damage to prevent further issues.
In addition to these practices, it is important to follow manufacturer-recommended maintenance procedures and schedules to ensure the best possible performance from your bearings. Proper maintenance can help reduce friction torque and improve the overall performance and service life of bearings.
Regular maintenance should include lubrication of bearings with the correct lubricant in the appropriate amounts. Over-lubrication can lead to higher torque due to increased friction and under-lubrication can lead to increased wear and eventual failure. Cleaning of bearings is also important as contaminants can lead to increased wear and torque.
It is also important to use the correct tools and techniques during bearing installation and removal to prevent damage to the bearing surfaces. Additionally, keeping records of bearing installation and maintenance can help identify potential issues and aid in troubleshooting in the future.
By following these practices for bearing maintenance, it is possible to reduce friction torque and ensure optimal performance and longevity of bearings.
Conclusion
In conclusion, understanding the factors that affect friction torque in bearings is critical for optimizing bearing performance and minimizing wear and tear. Bearing design, materials, lubrication, load, and speed all play a significant role in determining the level of friction torque experienced by the bearing.
To minimize frictional losses and improve bearing performance, it is important to select the right bearing for the application, ensuring that the bearing design and materials are appropriate for the load and speed conditions. Proper lubrication and cleaning, as well as early detection of wear and tear, are essential for maintaining optimal performance and reducing friction torque.
Regular maintenance, including proper lubrication, cleaning, and inspection, can help reduce friction torque and improve the service life of bearings. By following manufacturer-recommended procedures and schedules, using the correct tools and techniques, and keeping records of maintenance, it is possible to ensure the best possible performance from bearings.
PIB Sales offers an online bearing shop. Here, you can find a wide selection of bearings suitable for various applications, alongside expert advice to ensure you select the perfect product for your needs. Visit our online shop today to enhance your machinery’s performance.