Precision ball bearings are often needed in vacuum environments and will need special consideration for lubrication. Many applications like space exploration, semiconductor manufacturing, and high-precision scientific instruments will have special lubrication requirements. Traditional greases and oils are not useful in extreme applications especially where the absence of air and the presence of high or cryogenic temperatures can degrade normal lubrication quickly. One popular solution is the use of Dry Film Lubricants (DFLs).
In this article, we will explore the various types of Dry film lubricants, and their typical applications.
What is a dry film lubricant?
DFLs are specialized lubricants designed to withstand the vacuum’s harshness, offering a friction-reducing layer between contact surfaces without relying on liquid or grease. These lubricants are composed of materials like PTFE (Polytetrafluoroethylene), MoS2 (Molybdenum Disulfide), and Graphite—each selected for their ability to maintain performance under extreme conditions. Their application not only extends the life of bearings but also enhances their performance, ensuring reliability in environments where failure is not an option.
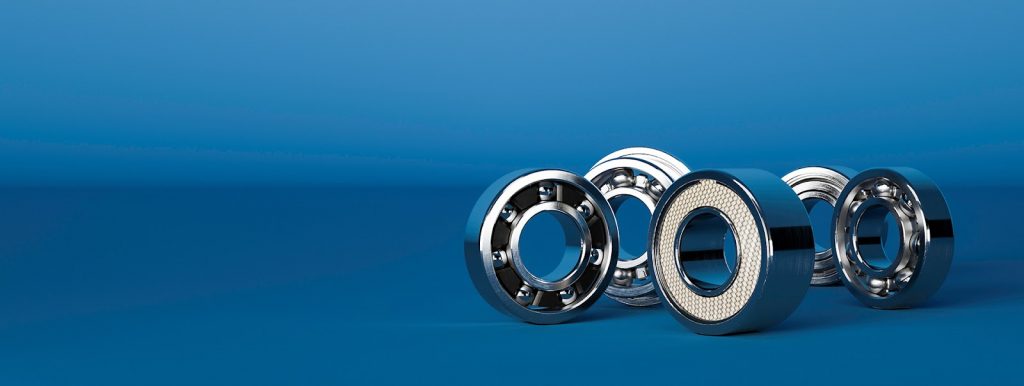
Dry film lubricants can be applied without seals or shields or with only one seal installed.
Dry Film Lubricants applications
The application of dry lubricants is not a one-size-fits-all solution but rather a strategic choice . Applications typically involve environments where liquid or grease lubricants would either evaporate due to high temperatures or become contaminated by external factors, compromising the integrity and performance of the bearing. Often dry lubricants are the go-to option in situations requiring minimal maintenance, as they do not attract dust or debris, ensuring the long-term cleanliness and functionality of the machinery.
Where are Dry Film Lubricants Used?
- Aerospace and Space Exploration: Protecting equipment in the vacuum of space where liquid lubricants cannot survive.
- Food Processing Equipment: Providing non-toxic, clean lubrication solutions where hygiene and safety are paramount.
- Cleanrooms and Laboratories: Applications where the slightest contamination could compromise research or product quality.
- Automotive and Mechanical Systems: Especially in components exposed to extreme conditions, such as brakes and clutch assemblies.
Dry Film Lubricants are used in vacuum environments, such as those found in space exploration, where traditional lubricants cannot survive. Additionally, their application extends to the semiconductor manufacturing industry, where contamination from liquid lubricants can lead to catastrophic failures. Through their ability to maintain performance under these challenging conditions, dry film lubricants have become an indispensable solution in ensuring the reliability and efficiency of bearings and the machinery they support.
Contact PIB Sales experts at [email protected] to explore more about dry film lubricants suitable for your specific industry needs.
Benefits of Using Dry Film Lubricants
Looking for optimal performance and longer bearing life dry film lubricants are the best choice especially when operating within vacuum environments. These specialized lubricants not only overcome the limitations of traditional lubrication but also have inherent advantages that enhance the operation and provide longer life when applied in such extreme conditions.
What Friction Related Problems are Dry Lubricants Used to Solve?
Friction affects mechanical efficiency and component longevity. Dry Film lubricants are a perfect solution many times meeting or exceeding lubricity concerns.
- Wear and Tear Reduced
By providing a solid lubricant layer between moving parts, dry lubricants significantly reduce the contact, thereby minimizing wear and extending the life of the bearing. - Temperature Resistance
In vacuum environments where temperature extremes are common, dry lubricants maintain their structural integrity and lubricating properties, unlike conventional lubricants that may vaporize or degrade. - Elimination of Contamination
Without the need for liquid or grease, which can attract and accumulate dust and other particulates, dry lubricants ensure that bearings remain free from contaminants that could impede their function. - Reduced Maintenance Requirements
The long-lasting nature of dry film lubricants means bearings require less frequent maintenance, reducing downtime and operational costs.
Choosing the Right Dry Film Lubricant for Your Vacuum Application
Selecting the appropriate dry film lubricant for bearings in vacuum applications is a process that requires consideration of a few key factors.
- Evaluate the Material Compatibility
Ensure that the DFL is compatible with the materials of your bearings. For instance, certain dry lubricants work better with specific metal alloys or ceramics.
- Consider the Temperature Range
Assess the operational temperature range of your application. You’ll need a DFL that performs well within those limits. For example, if your bearings will be exposed to extreme heat, a lubricant with a temperature range of -300° to +1200°F would be suitable.
- Assess Environmental Conditions.
Take into account any special conditions such as exposure to corrosive substances, extreme pressures, or radiation. Select a DFL that can withstand these conditions without breaking down.
- Understand the Application’s Load requirements
Dry lubricants have varying capacities when used under various loads. Understand the loads your bearings will encounter and choose a lubricant that can maintain its integrity under those stresses.
- Check for Industry Standards and Certifications
Some applications may require lubricants that meet specific industry standards or certifications, like MIL-specifications for aerospace applications.
- Evaluate Wear Life
Look at the expected wear life of the DFLs. Some may offer a longer wear life than others, reducing the need for reapplication and maintenance.
- Determine the Ease of Application and Reapplication
Consider how the DFL is applied and how often reapplication is needed. Some lubricants might require special preparation, such as a phosphate coating, for effective use.
Types of DFL
Table summarizing the main types of dry film lubricants, their compositions, typical applications, and advantages:
Type | Applications | Advantages | Temperature Range |
Graphite | High temperature environments, automotive brakes, aerospace, nuclear reactors | Operates at high temperatures, good thermal conductivity, reduces wear | -200°C to 3500°C in inert atmosphere |
Molybdenum Disulfide (MoS2) | Automotive parts, aircraft components, industrial machinery | Excellent load-carrying capacity, works in vacuum or inert atmospheres, reduces friction | -185°C to 450°C in air, up to 1100°C in vacuum or inert atmosphere |
Polytetrafluoroethylene (PTFE, Teflon) | Coatings for non-stick cookware, seals, bearings, aerospace components | Low friction coefficient, chemically inert, operates over a wide range of temperatures | -200°C to 260°C |
Tungsten Disulfide (WS2) | Precision gears, bearings, automotive, space vehicles | Similar to MoS2, but with better performance at extreme conditions, good thermal stability | -273°C to 650°C in air, higher in vacuum or inert atmosphere |
Boron Nitride | Electrical insulators, thermal spray coatings, aerospace | High thermal conductivity, electrical insulation, lubricates over a wide temperature | -30°C to 900°C in air, up to 2000°C in inert atmosphere |
Calcium Fluoride (CaF2) | Optical components, welding, metallurgical processes | Operates at high temperatures, low water solubility, good for high-vacuum applications | Up to 800°C |
Silver | Electrical contacts, bearings, high-temperature applications | Good electrical conductivity, anti-galling properties, thermal conductivity | -50°C to 800°C |
The choice of dry lubricant is crucial, with each material offering distinct properties suited to different applications. The most commonly used in vacuum environments include:
- PTFE (Polytetrafluoroethylene): Renowned for its exceptionally low coefficient of friction, PTFE is a versatile lubricant that excels in a wide range of temperatures and provides excellent chemical resistance.
- MoS2 (Molybdenum Disulfide): With its ability to withstand high pressures and its effectiveness in reducing friction, MoS2 is particularly suited for applications where load-bearing capacity is a critical factor.
- Graphite: Ideal for high-temperature environments, graphite maintains its lubricity even when exposed to extreme heat, making it indispensable in applications where thermal resilience is paramount.
Contact Pacific International Bearing
Looking to enhance the performance of your bearings in vacuum applications with the right dry film lubricant? Contact us today to explore PIB Sales solutions and find out how we can help you find the best solution for Dry Film lubrication.