Ball and roller bearings are widely specified because rolling friction is less than that of sliding friction. Rolling resistance is influenced by the elastic properties of the bearing material and the shape and condition of its surfaces. Further characteristics influencing rolling resistance include the magnitude of the perpendicular force as well as the magnitude and direction of the tangential force. Also, the speeds, temperature, and lubricant are all fundamental considerations.
In bearing applications, combined forces and motion are fundamental to machine performance. Bearings are designed to support radial loads, which act perpendicular to the shaft, and axial loads, which act parallel to the shaft. These forces generate internal stresses on the rolling elements and raceways, leading to contact pressure and potential deformation. Motion within bearings is primarily rotational, characterized by the rolling motion of balls or rollers along the raceways.
The dynamic interaction between these forces and motions directly impacts bearing life, operational temperature, vibration levels, and overall system stability.
In selecting the correct bearing for your application it is necessary to understand the forces (loads) acting on the bearing, the speeds involved, and the relative size of the shaft and housing as a starting point.
Often the application will dictate to some degree the size of the bearing based on adjacent components and mating parts. For more information contact us at [email protected]
Overview of Bearing Forces
Understanding the forces acting on bearings will help in selecting the appropriate type and size for any application. The primary forces affecting bearings are radial, axial, combined, dynamic, and static loads. Each of these forces has distinct characteristics and impacts on bearing performance, requiring consideration for the final design. Below is a breakdown of these forces, along with a comparison of dynamic and static loads, guidelines on measurement, and selection metrics.
Radial vs. axial forces
Radial forces act perpendicular to the bearing’s shaft axis. These forces are commonly encountered in rotating machinery where the weight of the supported structure, centrifugal forces from rotating masses, or forces from external equipment like gears and pulleys act on the bearing. For instance, in a typical electric motor, the radial load arises from the rotor’s weight and electromagnetic forces. Radial load capacity is a critical factor, as bearings must be capable of sustaining the expected radial forces without excessive deformation or wear.
Axial forces, also known as thrust forces, act parallel to the shaft axis. These are typical in applications like thrust bearings in automotive transmissions, where the load direction is along the length of the shaft. Axial forces require bearings that can handle the load from one or both directions. For example, angular contact ball bearings and thrust bearings are specifically designed to accommodate axial forces, with single-direction thrust bearings suited for one-way loads and double-direction thrust bearings managing loads in both directions.
Combined loads
In many practical applications, bearings are subjected to combined loads, where both radial and axial forces act simultaneously. For example, a gearbox shaft might experience radial forces from gear meshing and axial forces due to helical gears.
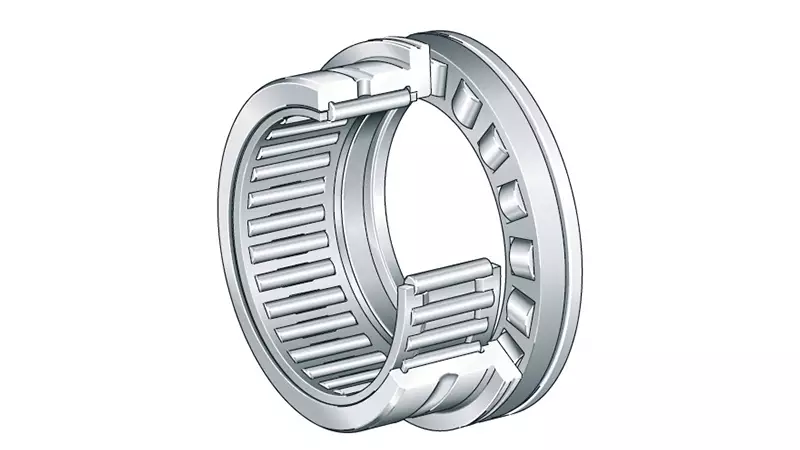
Bearings designed to handle combined loads, such as tapered roller bearings and angular contact ball bearings, are essential in these scenarios. The combined load capacity must be carefully evaluated, often requiring the use of load rating formulas and equivalent dynamic load calculations to determine the appropriate bearing.
Needle roller/axial cylindrical roller bearings can support axial forces in one direction as well as high radial forces.
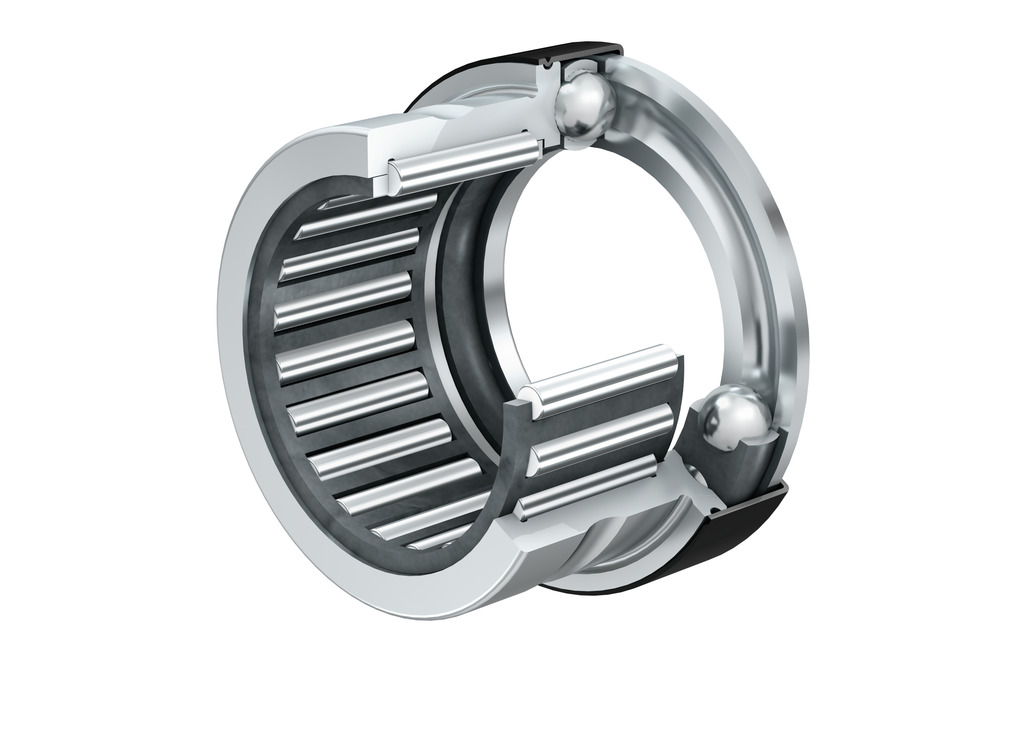
Needle roller/axial deep groove ball bearings can support axial forces in one direction as well as high radial forces.
Dynamic vs. static loads
Dynamic loads occur when a bearing is in motion, such as in rotating shafts or reciprocating machinery. The magnitude of dynamic loads fluctuates, which can cause varying stress levels on the bearing components. Dynamic load ratings are critical for determining a bearing’s suitability for high-speed or variable load applications. The dynamic load rating (C) is a key metric that represents the load a bearing can endure for a specified number of revolutions (typically one million cycles) without fatigue. This rating helps predict bearing life under operational conditions.
Static loads are applied to a bearing when it is stationary or at low speeds where motion is minimal. These loads can cause permanent deformation of the rolling elements and raceways if they exceed certain limits. The static load rating (C0) indicates the maximum static load a bearing can withstand without excessive deformation. Static load ratings are crucial when selecting bearings for applications where high loads occur intermittently or during startup and shutdown phases.
Parameter | Dynamic loads | Static loads |
Definition | Loads occurring during motion | Loads acting when the bearing is stationary |
Rating | Dynamic Load Rating (C) | Static Load Rating (C0) |
Impact on bearing life | Directly influences fatigue and operational life | Can cause permanent deformation |
Measurement | Measured in Newtons (N) or pounds (lbs) | Measured in Newtons (N) or pounds (lbs) |
Critical in | High-speed, variable load applications | Applications with intermittent or start-stop conditions |
Key Consideration | Bearing fatigue life | Maximum permissible deformation |
When evaluating bearing forces, several things are used to understand how bearings will perform under specific load conditions. These metrics are standardized throughout the bearing industry and are used to compare the capabilities of bearings when subjected to different forces, such as radial, axial, combined, dynamic, and static loads. The following table summarizes these key metrics, their standard measurements, and how they specifically relate to the forces acting on bearings.
Metric | Definition | Standard Measurement | Relevance to Bearing Forces |
Dynamic Load Rating (C) | The load a bearing can sustain for 1 million revolutions under dynamic conditions without fatigue. | Newtons (N) or pounds (lbs) | Critical for assessing the bearing’s capability to handle varying and fluctuating forces during operation. Higher C values are preferable for dynamic load conditions. |
Static Load Rating (C0) | The maximum load a bearing can handle at rest without permanent deformation. | Newtons (N) or pounds (lbs) | Essential for understanding the bearing’s ability to resist forces when stationary, crucial for applications where high static forces are present. |
Fatigue Life (L10) | Expected life at which 90% of bearings will operate without failure under a specified load. | Millions of revolutions | Directly influenced by the magnitude and direction of forces; used to predict the bearing’s durability under operational forces. |
Equivalent Dynamic Load (P) | A calculated value that combines both radial and axial forces into a single representative load. | Newtons (N) or pounds (lbs) | Essential for evaluating combined load conditions, ensuring the selected bearing can handle the cumulative effect of both radial and axial forces. |
Temperature Range | Operating temperature limits of the bearing. | Degrees Celsius (°C) or Fahrenheit (°F) | Influenced by the heat generated from internal forces; bearings must be selected to withstand operational temperatures affected by force-induced friction. |
Lubrication Type | Specifies the lubrication required to manage forces and reduce friction within the bearing. | Oil, grease, or solid lubricant | Proper lubrication minimizes the effects of forces, reducing wear and heat generation caused by friction between bearing components. |
How to Choose Bearings Considering Bearing Forces
Selecting bearings in relation to the forces they will encounter involves a detailed assessment of the operational conditions and matching these with the relevant metrics:
Load ratings (C and C0)
Start by analyzing the specific forces the bearing will be subjected to. For dynamic operating forces, the dynamic load rating (C) should be a priority to ensure that the bearing can handle the expected loads over its service life. For static conditions, where forces are applied to the bearing when it is not in motion, the static load rating (C0) should be the primary consideration to prevent deformation.
Equivalent dynamic load (P)
In applications where bearings are subjected to both radial and axial forces, calculate the equivalent dynamic load (P) to understand the cumulative effect of these forces. This value helps in selecting a bearing that can adequately handle the combined forces without compromising performance.
Fatigue life (L10)
Evaluate the L10 life of bearings to predict how long they will last under the specific forces encountered in the application. A higher L10 rating indicates a bearing that can withstand operating forces for a longer period of time, reducing the frequency of maintenance and replacement.
Temperature range and lubrication
Consider the impact of forces on heat generation within the bearing. Excessive forces can increase friction and, subsequently, the operating temperature. Bearings should be selected with appropriate lubrication types and temperature ratings to mitigate the effects of force-induced heat.
Force distribution and application-specific factors
Finally, assess the distribution of forces within the bearing assembly. Uneven force distribution can lead to premature failure. Bearings should be chosen based on their ability to evenly distribute forces and handle specific application demands, such as low noise, vibration tolerance, or resistance to environmental contaminants.
At PIB Sales, we can help in guiding you through the selection process, ensuring that the bearing selected meets your application requirements. If you have any questions or need help selecting bearings, please contact us at [email protected].
Mechanics of Motion in Bearings
Bearings are designed to accommodate various types of motion — rotational, linear, and oscillatory — each with unique mechanical characteristics that influence the bearing’s performance and longevity. Understanding these mechanics is essential for selecting the appropriate bearing type and ensuring optimal performance under different operational conditions.
Types of motion in bearings
Rotational motion is the most common type of motion in bearings, where the bearing allows shafts or other components to rotate about a fixed axis. This motion is characterized by the rolling of balls or rollers along the raceways, which significantly reduces friction. Key factors influencing rotational motion include the internal design of the bearing, the precision of the rolling elements, and the type of lubrication. Common bearings that handle rotational motion include deep groove ball bearings, cylindrical roller bearings, and angular contact ball bearings. The mechanics of rotary motion are influenced by factors such as load distribution, misalignment tolerance, and operating speed.
Linear motion occurs in applications where the bearing supports movement along a straight line, such as in guideways or linear actuators. Linear bearings, such as ball bushings or linear guides, are designed to provide low-friction, precise motion along a single axis. In linear motion, the rolling elements typically move in a path along a track or guide with minimal contact friction. The mechanics of linear motion in bearings include load distribution along the linear path, maintaining alignment, and minimizing friction to prevent stick-slip phenomena that can cause irregular motion.
Oscillating motion refers to repetitive back and forth motion within a bearing, commonly found in applications such as rocker arms or pivots. Bearings that support oscillating motion, such as spherical plain bearings or needle roller bearings, are designed to handle the frequent directional changes and angular displacements typical of this motion. Oscillating motion can place unique stresses on the bearing, including micro-slip and fretting wear, requiring careful consideration of materials and lubrication to mitigate these effects.
Key factors affecting motion in bearings
- Friction between the rolling elements and raceways is a critical factor in the mechanics of motion. Bearings are designed to minimize friction through the use of rolling elements, precise manufacturing tolerances, and appropriate lubrication. However, any residual friction generates heat, which can affect the bearing’s performance and lifespan. The mechanics of motion aim to balance these forces, optimizing the bearing’s efficiency and reducing energy losses.
- The distribution of loads across the bearing’s rolling elements is crucial for maintaining smooth motion. Uneven load distribution can cause localized stress concentrations, leading to premature wear or failure. Proper alignment, correct installation, and appropriate bearing selection are essential to ensure even load distribution, enhancing the mechanics of motion within the bearing.
- Bearings are rated for specific speed ranges, and exceeding these limits can lead to increased friction, heat, and potential bearing damage. The mechanics of motion must consider the operating speed and any acceleration forces that may act on the bearing. High-speed applications require bearings with low friction and high precision to maintain smooth operation without excessive heat generation.
- Lubrication provides a thin film between the rolling elements and raceways to reduce friction, wear, and heat. The type, viscosity, and quantity of lubrication must be carefully selected based on the bearing type, motion characteristics, and operating conditions. Insufficient or inappropriate lubrication can lead to increased friction, while over-lubrication can cause excessive drag, impacting the motion mechanics.
Selection tips:
1) Select bearings that offer low friction, high load capacity, and precise tolerances to support smooth rotation. Deep groove ball bearings and cylindrical roller bearings are typically suitable for high-speed rotational applications.
2) Choose linear bearings or guides that minimize friction and support the required precision and load capacity. Ball bushings and profile rail guides are commonly used in applications requiring precise linear movement.
3) Use bearings that can handle frequent direction changes and angular displacements, such as spherical plain bearings or needle roller bearings, which are designed to accommodate oscillatory stresses and minimize wear.
By fully understanding the mechanics of motion in bearings, engineers can optimize bearing selection and ensure that the selected bearings provide the desired performance.
Choosing the Right Bearing
At PIB Sales, we understand that the choice of bearing must be closely aligned with the forces acting on it and the specific type of motion it supports. Here, we provide a selection scheme using examples from our range of bearings, illustrating how different bearings are suited to various force and motion requirements.
Bearing selection based on forces
For radial loads:
- Radial ball bearings are ideal for applications where the primary force is radial. They offer low friction and can handle moderate radial loads at high speeds. Common uses include electric motors, fans, and pumps.
- Cylindrical roller bearings are suitable for applications with heavy radial loads and high-speed conditions. Their design allows them to carry large radial forces while minimizing friction.
For Axial (Thrust) loads:
- Thrust ball bearings are specifically designed to handle high axial loads, thrust ball bearings are perfect for applications like automotive steering and machine tool spindles where axial forces dominate.
- Angular contact ball bearings are designed to handle axial loads with high precision, making them suitable for high-speed applications requiring both axial load support and high accuracy.
Bearing Selection Based on Motion
For rotational motion:
- Deep groove ball bearings are widely used for applications with high-speed rotational motion and low friction requirements. They are versatile and can handle moderate radial and axial loads, making them suitable for electric motors and household appliances.
- Spherical roller bearings are suitable for heavy-duty applications where rotational motion is coupled with misalignment issues, such as in conveyor systems or heavy machinery.
For linear motion:
- Linear ball bearings and linear guides & carriages are designed specifically for linear motion applications. They provide smooth, low-friction movement along a track or guide, making them ideal for CNC machines, 3D printers, and other precision positioning systems.
For oscillatory motion:
- Spherical plain bearings are perfect for applications involving oscillatory or pivoting motion, such as in hydraulic cylinders and suspension components. They can accommodate misalignment and high load capacities, which are typical of oscillatory movements.
PIB Sales offers a comprehensive catalog that provides all the essential information about the various types of bearings, helping you make informed decisions and select the bearings that best fit your needs. If you have any questions or need further assistance, contact us. Our team is always available to help you find the perfect solution.