Miniature Angular Contact Bearings are designed to handle both axial and radial loads in high-speed applications where space and weight are critical. They are used in a wide range of industries, including aerospace, medical devices, robotics, and machine tools. This article explains the design and working principles of miniature angular contact bearings or spindle bearings and their applications.
Generally, miniature Angular Contact or Spindle bearings fall between 3mm inner diameter and 25mm inner diameter. Spindle bearings are single-row angular contact bearings with a nominal contact angle of 15° (C) or 25° (E). They can be subjected to both radial and (in one direction) axial loads. The direction of the axial load is shown by a “V” marking on the outer ring. Miniature spindle ball bearings are suitable for applications requiring precision while carrying high load combined with high speed.
Miniature Angular Contact spindle ball bearings are characterized by the following properties:
- Manufactured quality of P4 (ABEC7) or better;
- Rings made of corrosion resistant Cronidur 30 high-grade steel, 440C Stainless or 52100 Chromium steel;
- Steel or ceramic balls;
- Solid retainer made from fiber-reinforced phenolic resin, peak, or other strong materials;
- 15° (C) or 25° (E) contact angles as standard;
- Optionally, bearings can be paired with three predefined preload classes (L, M, or S) or to a customer specific preload value;
- Oil or grease lubrication;
- Open and shielded versions available;
- Cleanroom assembly, lubrication, and packaging.
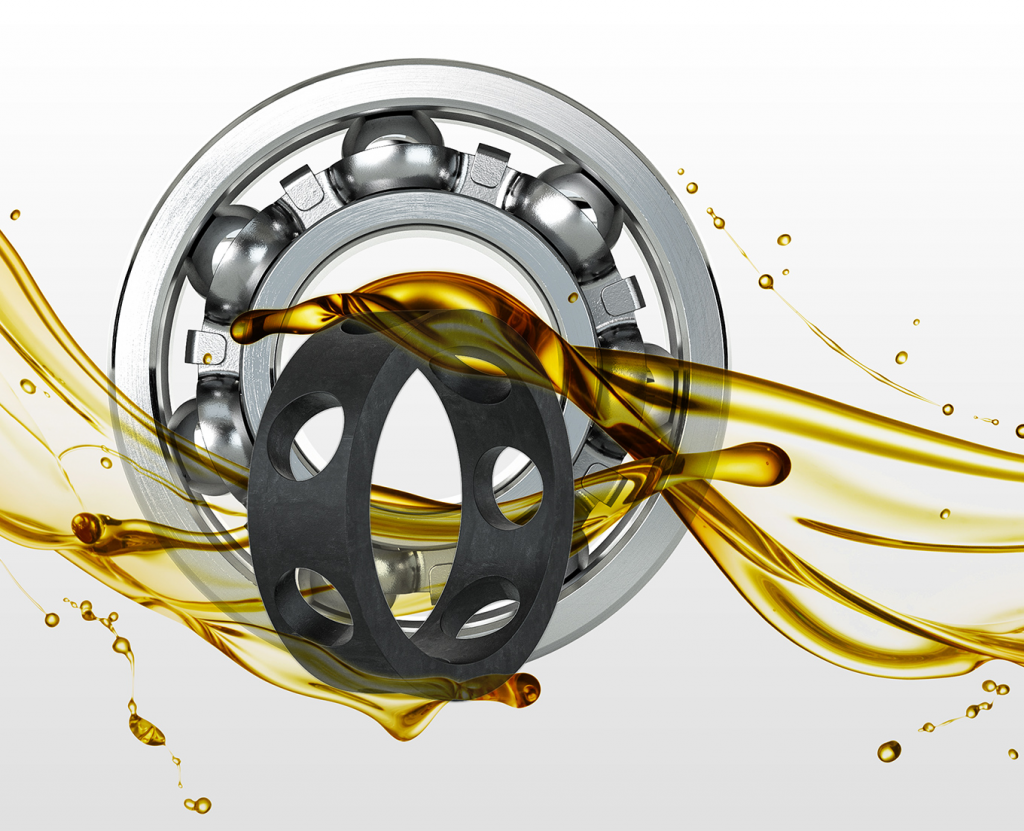
Design of Miniature Angular Contact Bearings
Miniature angular contact bearings are made of high-performance bearing steels such as 440C, AISI 52100 and Cronidur 30. Hybrid versions use any of these steel types for outer and inner rings but are then combined with the use of ceramic balls. Hybrid Miniature Angular Contact bearings with ceramic balls are considered high speed spindle type bearings.
When specified with Cronidur 30, they have extremely high corrosion resistance, and the load ratings are the same as AISI 52100. The load capacity and speed rating of the bearings depend on the material used, the precision and the design of the bearing.
Miniature angular contact bearings designed as a high precision highly toleranced bearing with ceramic balls (hybrid type) can operate at extremely high speeds. For example, a miniature bearing with dimensions 4mm idx7mm ODx2mm wide, designed as an ABEC 7 with ceramic balls with oil will reach 455,000 rpm. You can increase speed ratings by 10% through each class of bearing. ABEC 5 to 7 to 9, for example, will yield 10% increases in speed ratings. In the above example you could increase the speed rating from 455,000 rpm to 500,000 rpm by increasing the tolerance to ABEC 9 from ABEC 7.
Load Capacity and Speed Rating
The load capacity of miniature angular contact bearings is determined by the contact angle, number of balls, ball size and bearing material used. The higher the contact angle, the higher the axial load capacity of the bearing. The number and size of balls also affect the load capacity of the bearing. The speed rating of the bearing is determined by the maximum speed at which the bearing can operate without overheating.
Working Principle of Miniature Angular Contact Bearings
Miniature angular contact bearings operate on the principle of rolling contact between the balls and the raceway, providing efficient load handling capabilities essential for high-precision and high-speed applications.
Contact Angle and Axial Load
The contact angle is a critical parameter in miniature angular contact bearings. It is defined as the angle between the line connecting the centers of the balls and the line perpendicular to the raceway. This angle directly affects the axial load capacity of the bearing. A higher contact angle results in a higher axial load capacity, making these bearings particularly suitable for applications requiring the support of significant axial forces.
For instance, in high-speed spindles, the precise control of axial loads is important in maintaining stability and accuracy. Similarly, in robotics, where both precision and the ability to handle dynamic loads are essential, a well-designed contact angle ensures the bearings can support the necessary axial forces without compromising performance. In medical devices, where reliability and precision are paramount, the optimized contact angle allows these bearings to function effectively under varied load conditions.
Radial Load and Its Impact
Miniature angular contact bearings are good at handling both axial and radial loads due to their unique design. The radial load capacity is influenced by the size and number of balls within the bearing. Bearings with larger or more balls can distribute the load more effectively, enhancing their ability to manage radial forces.
In applications such as CNC machining, where high precision and reliability are required, these bearings ensure smooth and accurate operation. The capacity to handle radial loads efficiently also makes them ideal for use in aerospace applications, where both reliability and performance under stress are critical. In robotics, the ability to manage both radial and axial loads ensures that the robotic components can operate smoothly and accurately, even under dynamic conditions.
By understanding the principles of rolling contact, contact angle, and load handling capabilities, engineers can better select and utilize miniature angular contact bearings to optimize the performance and reliability of their systems. This knowledge ensures that the bearings chosen will meet the specific demands of the application, providing both efficiency and longevity.
Applications of Miniature Angular Contact Bearings
Miniature angular contact bearings are used in a wide range of industries, including aerospace, medical devices, robotics, and machine tools.
Miniature angular contact bearings are widely used in medical devices where precision and reliability are crucial. Applications include dental drills, surgical tools, and diagnostic equipment. These bearings ensure smooth and precise operation, which is essential for the accuracy and effectiveness of medical procedures.
In robotics, these bearings are used in joints and rotary components where high precision and speed are necessary. They support both the axial and radial loads that robotic arms and actuators experience during operation. The use of miniature angular contact bearings in robotics enhances the precision and responsiveness of robotic systems.
High-speed spindles in various industries rely on miniature angular contact bearings for their ability to operate at high speeds with low friction and minimal heat generation. These bearings are designed to provide high precision and stability, which is essential for applications such as CNC machining, grinding, and drilling.
Conclusion
Miniature angular contact bearings are critical components in high-speed and high-precision applications. Their design and working principles enable them to handle both axial and radial loads. Depending upon the bearing material specified, they have excellent performance characteristics in harsh environments. The choice of material and design of the bearing determine the load capacity and speed rating of the bearing. With their small size and high load capacity, miniature angular contact bearings play a crucial role in many industrial and medical applications.
Find and buy Miniature Angular Contact bearings online from Pacific International Bearing Sales Inc.