Ruland Manufacturing Co., Inc., established in 1937, is a leading producer of high-performance shaft collars and couplings. Ruland’s expertise in precision motion control components – from crafting bicycle pump parts to a valve used in the first American spacewalk – underpins the quality of their products. PIB Sales provides local access to these components. In conveyor systems that demand high accuracy, zero-backlash jaw couplings have become indispensable. They ensure precise power transmission with no play (backlash) between driving and driven shafts, which is critical for indexing conveyors, positioning systems, and other industrial equipment requiring exacting repeatability.
Why Choose Ruland Jaw Couplings
Ruland’s zero-backlash jaw couplings offer a combination of torsional rigidity and vibration damping that makes them well-suited for precision conveyors with frequent start-stop cycles.
Key benefits include:
- Zero Backlash Operation. The hubs and the elastomeric spider are designed with a tight press-fit curved jaw profile that eliminates any gap or play, so torque is transmitted without backlash. This ensures accurate registration of conveyor movements even under reversing loads.
- Vibration Damping. The polyurethane spider absorbs shock and vibration, which protects motors and sensitive conveyor components from impulse loads. A softer spider offers greater damping (for smoother operation), while a harder spider offers higher stiffness.
- Fail-Safe Design. Jaw couplings are inherently fail-safe – if the spider were to wear out or fail, the interlocking jaws of the hubs would continue to transmit torque (with metal-to-metal contact).
- Misalignment Compensation. The three-piece jaw coupling can accommodate all three types of misalignment (angular, parallel, axial). The spider’s flexibility allows up to about 1° of angular misalignment and a small amount of parallel offset and end float (axial motion) to be tolerated, preventing undue bearing loads.
- High Torsional Stiffness. With the hardest spider option, Ruland jaw couplings exhibit high torsional rigidity, meaning minimal twist under load – an important factor for maintaining registration on precision indexing conveyors. Using a harder spider yields greater torque capacity and stiffness, which is beneficial for fast acceleration profiles on servo-driven conveyors.
- Quality Materials and Build. Ruland machines the coupling hubs from high-grade aluminum bar stock (2024-T351 or 7075-T651) for a strong yet lightweight hub. The hubs have a bright, smooth finish to ensure a precise fit on shafts. Hardware (clamp screws or set screws) are alloy steel with black oxide for durability. The spiders are molded from an advanced polyurethane for durability and consistent performance. Every Ruland coupling is made in their Massachusetts factory under tight quality control.
- Balanced for High Speed. Unlike some couplings, Ruland’s jaw couplings have a standard balanced design. This allows vibration-free operation at speeds up to 8,000 RPM – a critical feature for conveyors in high-speed inspection or packaging systems where even slight vibration can cause positioning errors.
PIB Sales ensures these Ruland couplings are readily available and offers engineering assistance for selection and integration. This local support, combined with Ruland’s proven product quality, provides conveyor OEMs and end-users with confidence in their power transmission solution.
In summary, Ruland jaw couplings deliver zero-backlash precision, shock absorption, and reliable fail-safe operation, all of which are highly desirable in modern precision conveyor systems. Next, we will explore the construction and options of these jaw couplings in detail.
Zero-Backlash Jaw Coupling Design and Operation
Ruland’s jaw couplings consist of three pieces: two metallic hubs and one elastomer spider. Each hub features a series of curved jaws that interlock with the jaws of the opposite hub, with the spider sandwiched between them. This design gives the coupling its key characteristics:
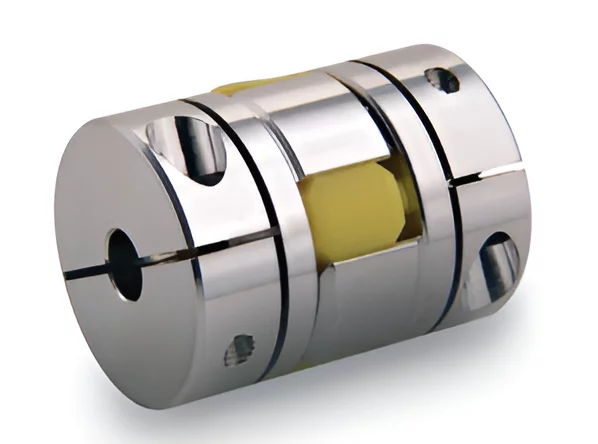
Curved Jaw Profile
The hubs have precision-machined curved jaws. When assembled, the spider’s lobes are compressed between these curved jaws. The curvature concentrates forces toward the center of the spider lobes, ensuring a tight fit that eliminates backlash. Unlike straight jaw couplings, the curved jaws maintain contact over a range of misalignment, and together with the pre-loaded spider, prevent any gap or slop in torque transmission.
Elastomer Spider
The spider is a torque-transmitting element made of polyurethane, available in multiple durometers (hardness levels). It has lobes (sometimes called “legs”) that fit between the hub jaws. All Ruland spiders are press-fit onto the hub jaws – one half of the spider engages each hub. This preload is what assures zero backlash under normal operation. The spider’s material and shape also provide vibration damping by absorbing shock loads, which is especially beneficial for conveyors starting and stopping frequently. The spider’s legs have raised contact points on their tips, which touch the bottom of the jaw slots. These bumps serve two purposes: they keep the hubs slightly separated to ensure no metal-to-metal contact (maintaining electrical isolation between shafts), and they allow the coupling to handle its maximum angular misalignment without binding.
Fail-Safe Jaw Interlocking
In normal operation, torque is carried through the spider. However, if the spider is sheared or removed, the jaws of the two hubs will interlock. They are designed so that one hub’s jaws can drive the other hub directly in the absence of the spider (albeit with backlash and without damping). This fail-safe feature means a conveyor won’t suddenly lose drive even if the spider fails – it provides a measure of safety to bring the system to a controlled stop for maintenance.
Clamp or Set Screw Hubs
Ruland offers the hubs in two mounting styles – clamp style (denoted “JC” for inch or “MJC” for metric series) or set screw style (“JS” or “MJS”). Clamp-style hubs have an integrated split and cap screw that cinches the hub firmly around the shaft when tightened, providing a strong, mar-free connection. Set screw style hubs use one or two threaded set screws that tighten onto the shaft (Ruland positions them 90° apart on larger sizes for better holding power). For high-precision applications, the one-piece clamp style is often preferred for its superior concentricity and balance. However, set screw hubs provide a cost-effective solution and a slightly more compact length in small sizes. Notably, designers can mix-and-match hub styles in one coupling (e.g., one clamp hub and one set-screw hub) to suit different shaft mounting needs – both hub types will mate with the same spider as long as they are the same series size.
In essence, the Ruland jaw coupling operates by bonding the two shafts together with a cushion of elastomer between them. The spider’s preload and the curved jaws ensure zero backlash and consistent torque transmission, while the spider’s elasticity allows for slight misalignments and reduces vibration. This combination of attributes is what makes these couplings ideal for precision conveyor drives that require both accuracy and reliability.
Hub Selection Guide
For metric conveyors and equipment, Ruland offers metric-series jaw coupling hubs designated “MJC” (Metric Jaw Clamp) or “MJS” (Metric Jaw Set-screw). These have metric bore diameters and hardware, but are otherwise equivalent in performance to the inch series. Table 2 gives the range of metric sizes:
Table 1 – Ruland Jaw Coupling Hubs (Metric Series)
Outer Diameter OD (mm) | Hub Length L (mm) | Overall Coupling Length L (mm) | Bore Range (mm) | Clamp Screw (metric) | Set Screw (metric) |
15.0 mm | 7.6 mm | 21.8 mm | 3–6 mm | M2 | M3 (1×) |
19.1 mm | 9.8 mm | 27.2 mm | 4–8 mm | M2.5 | M3 (1×) |
25.4 mm | 11.9 mm | 35.3 mm | 6–12 mm | M3 | M4 (2×) |
33.3 mm | 15.0 mm | 44.5 mm | 8–16 mm | M3 | M4 (2×) |
41.3 mm | 18.0 mm | 53.0 mm | 10–20 mm | M4 | M5 (2×) |
50.8 mm | 20.8 mm | 61.0 mm | 12–25 mm | M5 | M6 (2×) |
57.2 mm | 28.7 mm | 80.0 mm | 14–30 mm | M6 | M8 (2×) |
The metric series covers bore sizes from 3 mm up to 30 mm. Part numbers follow the format “MJCXX-YY-A” for clamp hubs (where XX is the coupling size and YY is the bore in mm), or “MJSXX-YY-A” for set screw hubs. For example, a coupling for 12 mm and 15 mm shafts could use one MJC41-12-A hub and one MJC41-15-A hub (41.3 mm OD series), or their set screw equivalents, plus a spider. The dimensions (OD, length, etc.) for size 41 are the same whether clamp or set screw style. As with the inch series, all standard metric hubs are aluminum alloy. The clamp screws and set screws are metric hardware (class 12.9 alloy steel) and should be tightened to Ruland’s recommended torques for a secure grip.
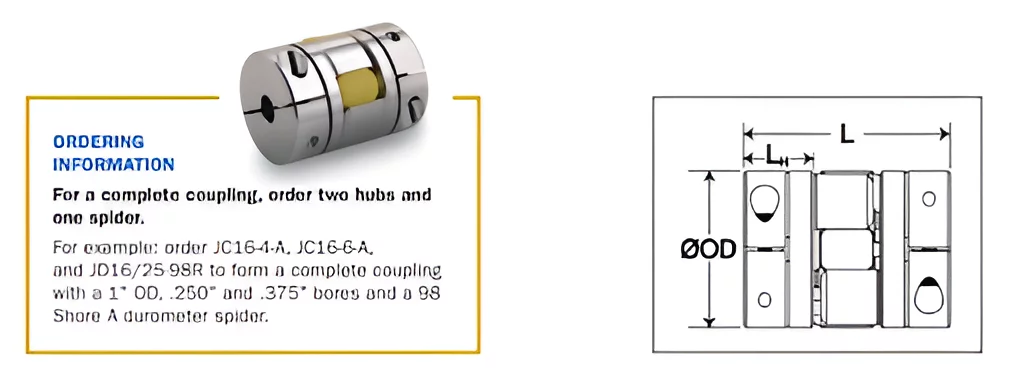
In both inch and metric series, Ruland can also provide keyways in the hubs if needed (part numbers with a “K” denote keyed versions). Keyed hubs are common in more heavy-duty conveyors or legacy systems to meet ANSI or DIN shaft standards. However, for many precision conveyor applications, the keyless clamp style provides sufficient torque transmission and easier phasing adjustment on the shaft.
Spider Selection Guide
The elastomer spider insert is the heart of the jaw coupling, and its material hardness (durometer) allows the user to tune the coupling’s performance for their application. Ruland spiders come in three polyurethane hardness options:
- 85 Shore A – “Soft” (Blue): Highest elasticity for maximum shock absorption and vibration damping. This soft spider minimizes the transmission of shock loads and can reduce resonances in conveyor drive systemsfile-kfir59yshmlxhvan6cezz4. The trade-off is lower torsional stiffness and reduced torque capacity.
Conveyors transporting fragile objects, or systems requiring a measure of vibration isolation between the motor and the load. (Blue spiders are marked with “85A”.)
- 92 Shore A – “Medium” (Yellow): Intermediate characteristics offering a balance between damping and torsional rigidity. It provides moderate shock absorption with moderate stiffness.
General-purpose conveyors and indexing tables where some vibration damping is needed without sacrificing too much positioning accuracy or torque capacity. (Yellow spiders marked “92A”.)
- 98 Shore A – “Hard” (Red): Most rigid option, with highest torsional stiffness and strength. It transmits the most torque with minimal twist, at the cost of damping ability.
Servo-driven conveyors or gantries require tight positional accuracy and fast response. Also suitable for start-stop applications with high peak torques. (Red spiders marked “98A”.)
Each spider is color-coded (Blue 85A, Yellow 92A, Red 98A) for easy identification. Physically, all durometers share the same shape and dimensions for a given coupling size – they are interchangeable in the hub. When replacing a spider or assembling a new coupling, you simply choose the hardness that best fits the application’s needs for stiffness vs. damping.
Torque and Misalignment Capacities: Harder spiders can transmit higher torque but allow slightly less misalignment, while softer spiders transmit less torque but can flex more. Table 3 illustrates the differences using a Size 16/25 coupling (1″ or 25 mm OD, mid-size) as an example:
Table 2 – Performance of Different Durometer Spiders (for 1″ / 25 mm OD Coupling)
Spider Durometer (Color) | Torsional Stiffness (Deg/ℓb·in) | Approx. Nominal Torque | Angular Misalignment (max) | Parallel Misalignment (max) | Axial Motion (max) |
98 Shore A (Red) | ~0.024 deg/ℓb·in (very stiff) | 85 ℓb·in (9.6 N·m) nominal 170 ℓb·in (19 N·m) peak | 0.5° – 0.8° (slight) | 0.005″ (0.13 mm) | 0.020″ (0.51 mm) |
92 Shore A (Yellow) | ~0.067 deg/ℓb·in (medium) | 55 ℓb·in (6.2 N·m) nominal 110 ℓb·in (12.4 N·m) peak | ~1.0° (moderate) | 0.006″ (0.15 mm) | 0.020″ (0.51 mm) |
85 Shore A (Blue) | ~0.108 deg/ℓb·in (compliant) | 35 ℓb·in (4.0 N·m) nominal 70 ℓb·in (7.9 N·m) peak | 1.0°+ (up to 1.5° max) | 0.008″ (0.20 mm) | 0.020″ (0.51 mm) |
The values above are representative of the size 16/25 coupling. Larger couplings can handle higher torque (up to about 278 ℓb·in / 31 N·m nominal with 98A spiders on the largest size), while smaller couplings handle less. Angular misalignment up to approximately 1° is tolerated across all spiders (the soft spider can flex slightly more before the hubs contact). Parallel misalignment capacity is limited – a few thousandths of an inch – because jaw couplings are primarily intended for precise alignment; excessive parallel misalignment will concentrate stress in the spider. Axial motion (end float) is about 0.020″ (0.5 mm) total for each coupling size – the raised pads on the spider legs maintain this gap between hubs. For best results, design your conveyor system so that shafts are as closely aligned as possible, and use the coupling’s misalignment capability only to accommodate minor mounting tolerances or thermal expansion.
Spider Part Numbers: Ruland spiders are ordered separately using part numbers of the form JD**XX/YY**-**DURO**. Here XX/YY denotes the two coupling sizes (inch/metric) that the spider fits, and DURO indicates the durometer with a letter code (R = 98 Red, Y = 92 Yellow, B = 85 Blue). For example, JD16/25-98R is the red 98 Shore A spider for coupling size 16 (1″ inch series or 25 mm metric series)file-kfir59yshmlxhvan6cezz4. One spider fits both hubs of the coupling. Table 4 lists the available spider part numbers covering all sizes:
Table 3 – Spider Inserts for Ruland Jaw Couplings
Spider Part Number | For Coupling Size (OD) | Durometer (Color) | Nominal Torque (ℓb·in) | Peak Torque (ℓb·in) |
JD10/15-98R | 0.590″ / 15 mm (Size 10/15) | 98 Shore A (Red) | 9 ℓb·in | 18 ℓb·in (est.) |
JD10/15-92Y | 0.590″ / 15 mm | 98 Shore A (Red) | 6 ℓb·in (est.) | 12 ℓb·in (est.) |
JD10/15-85B | 0.590″ / 15 mm | 85 Shore A (Blue) | 5 ℓb·in | 10 ℓb·in (est.) |
JD12/19-98R | 0.750″ / 19 mm (Size 12/19) | 98 Shore A (Red) | 16 ℓb·in | 32 ℓb·in |
JD12/19-92Y | 0.750″ / 19 mm | 92 Shore A (Yellow) | 11 ℓb·in | 22 ℓb·in |
JD12/19-85B | 0.750″ / 19 mm | 85 Shore A (Blue) | 8 ℓb·in | 16 ℓb·in |
JD16/25-98R | 1.000″ / 25 mm (Size 16/25) | 98 Shore A (Red) | 36 ℓb·in | 72 ℓb·in |
JD16/25-92Y | 1.000″ / 25 mm | 92 Shore A (Yellow) | 24 ℓb·in | 48 ℓb·in |
JD16/25-85B | 1.000″ / 25 mm | 85 Shore A (Blue) | 16 ℓb·in | 32 ℓb·in |
JD21/33-98R | 1.313″ / 33 mm (Size 21/33) | 98 Shore A (Red) | 85 ℓb·in | 170 ℓb·in |
Due to space, only smaller sizes are partially listed; larger spider part numbers continue the pattern up through JD36/57 for the largest size (2.25″/57 mm OD). Nominal torque is the manufacturer’s recommended continuous torque limit for each spider, while peak torque is the short-duration capacity (e.g., during acceleration) – typically about double the nominal. If peak torques are exceeded, the spider may deform permanently or fail, so sizing the coupling with appropriate service factors is important (consult Ruland’s catalog for full ratings). In general, the 98 Shore A spiders have approximately 2× the torque capacity of 85 Shore A spiders of the same size, with the 92 Shore A roughly midway between. All spider materials are polyurethane, usable in temperatures from –10°F to +180°F. They offer electrical isolation between hubs and do not require lubrication or maintenance aside from periodic inspection.
Spider selection tips:
For most precision conveyor systems, the 92 Shore A (medium, yellow) spider is a good starting choice as it balances shock absorption with torsional rigidity. If the conveyor carries delicate products or if drive vibration is a concern (for instance, indexing glass substrates or sensitive electronics), consider the 85 Shore A soft spider to cushion the motion. On the other hand, if precise indexing and minimal rotation deflection are top priority (e.g. servo-driven pallet conveyors or pick-and-place systems where positioning is critical), the 98 Shore A hard spider may be preferred. Remember that the spider can be swapped out relatively easily, so it is possible to try one durometer and change to another in the field to fine-tune performance. All three spider types are fully compatible with any given hub set, as they share the same geometry.
Ordering and Installation
Specifying a complete Ruland jaw coupling for your conveyor is straightforward. You will need two hubs and one spider. Typically, you will choose the hubs first (to fit your shaft diameters and attachment preference), then select a spider durometer based on the application requirements. Ruland’s part numbering makes it easy to identify the correct components:
- Hubs: Use JC (clamp) or JS (set screw) prefix for inch-series, or MJC/MJS for metric. The numbers after the prefix indicate the coupling size and bore. For example, JC21-8-A is an inch-series clamp hub for the size 21 coupling (1.313″ OD) with a 0.500″ bore (8/16 = 1/2″) in aluminum. Likewise, MJC33-15-A would be a metric clamp hub for size 33 (33.3 mm OD) with a 15 mm bore. Each hub includes the necessary screw hardware.
- Spider: Use JD prefix followed by the size pairing and durometer code. For instance, a spider for the 1″ (25 mm) coupling in 92 Shore A would be JD16/25-92Y. The spider part number ensures you get the correct hardness and that it will properly fit the coupling size.
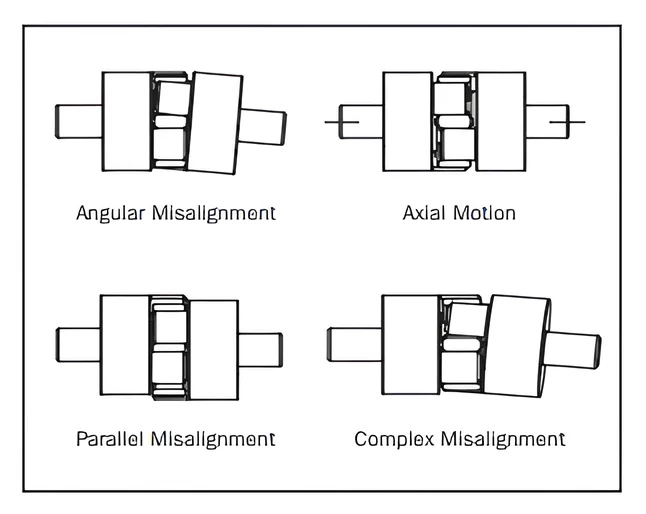
When placing an order through PIB Sales, be sure to specify each part number. PIB Sales can assist in confirming that the hub bore dimensions match your motor and shafting, and that the chosen spider hardness is suitable. It’s often useful to provide application details (torque, speed, alignment conditions) to get guidance on the best coupling configuration.
Check Misalignment – Align the two shafts as closely as possible. Verify that any misalignment is within the coupling’s capability (typically <1° angular and a few thou parallel). Large misalignments will stress the spider and should be corrected by realigning the machinery.
Install Hubs – If using clamp-style hubs, slide each hub onto its shaft so that the end of the shaft is flush with or slightly inside the hub face (each hub’s shaft penetration, see Figure 2, should ideally be about 70% of the hub length to fully support the spider). For set screw hubs, ensure the set screw(s) will land on the shaft (on a flat or key if present) and not on a thread or keyway edge. Do not tighten yet.
Insert Spider – Place the spider onto one of the hubs. Push it until the spider’s legs bottom out on that hub’s jaw shoulders. The spider should be snug – you may need to press firmly as the fit is intentionally tight. The “raised points” on the spider will keep it slightly proud.
Join Hubs – Bring the second hub in and align its jaws with the gaps in the spider. Push the second hub into the spider until its jaws also fully engage and the raised pads touch the base of the jaws. There will be a small gap between the hub faces – this is normal (it ensures no contact between hubs). Some force may be required for full engagement, especially with a hard spider – this preload is what eliminates backlash.
Tighten Hubs – For clamp hubs, ensure the hub is positioned correctly on the shaft (with the interlocking happening at about the mid-thickness of the spider) and then tighten the clamp screw to the specified torque (see Ruland’s torque chart; e.g. an M4 clamp screw should be torqued to ~4.6 Nm). Clamp screws should be tightened firmly and evenly – use a calibrated torque wrench for best results. For set screw hubs, first tighten the set screw on one hub to spec (e.g. an M5 set screw to ~4 Nm), then tighten the second hub’s set screw. In larger hubs with two set screws, tighten both (alternating between them to incrementally reach torque).
Verify – After installation, check that there is a slight gap between the two hubs (you might slip a thin piece of paper between to confirm no contact). Also, rotate the system slowly by hand to ensure the coupling turns smoothly without binding.
Mounting a Ruland jaw coupling on a conveyor drive is relatively simple, but following the proper procedure will ensure zero-backlash performance:
Following these steps will ensure the coupling is properly preloaded and has zero backlash. Over time, the spider may wear and shrink slightly, so it’s good practice to inspect the spider periodically. A tell-tale sign of wear is if you start to feel backlash (play) in the system; that indicates the spider’s legs might be wearing down, and replacement could be needed. Fortunately, replacing the spider is easy – just loosen the hubs and swap in a new insert – and the hubs can be reused indefinitely.
Performance Comparison to Other Coupling Types
Modern motion control systems have several coupling styles to choose from (beam, bellows, disc, Oldham, etc.), each with different strengths. Ruland’s zero-backlash jaw couplings strike a balance among key performance factors, especially for conveyor systems that require both precision and some compliance.
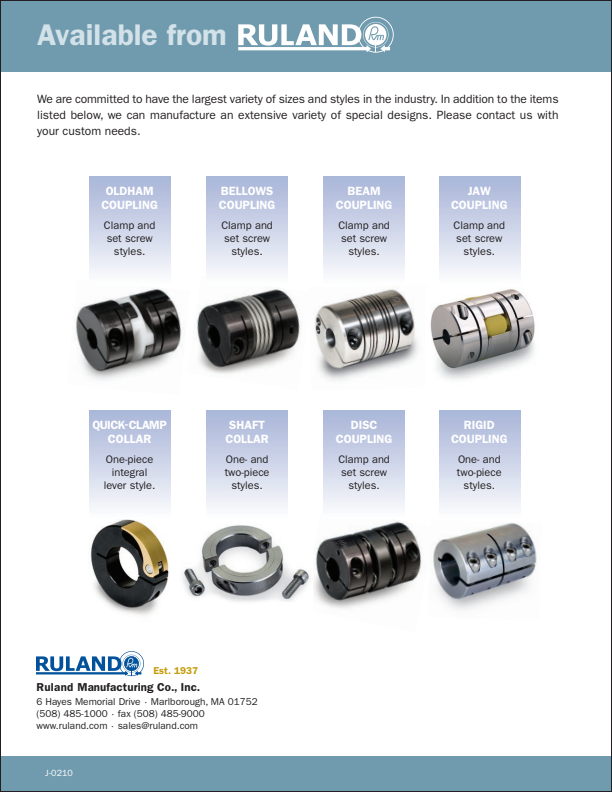
As illustrated in Figure 3, jaw couplings (particularly with different spider durometers) fill a unique position:
- Torque and Stiffness: They can handle significant torque, on par with or better than beam couplings and Oldham couplings of similar size, especially when fitted with a hard spider. Their torsional rigidity is moderate: not as high as all-metal bellows or disc couplings, but much higher than flexible beam couplings. This makes jaw couplings a strong choice for indexing conveyors where some compliance is desired to protect the system, but too much twist would cause position errors.
- Misalignment and Damping: Jaw couplings accommodate angular and small parallel misalignments and crucially provide dampening of vibrations. Beam couplings can handle more misalignment, but at the cost of vibration springiness; bellows and disc handle very little misalignment. Oldham couplings can handle parallel misalignment even better than jaw couplings, due to their three-piece sliding disk design, but Oldhams have a backlash (unless preloaded) and their disks wear over time. Jaw couplings are considered maintenance-free – they don’t require lubrication, and the spider typically has a long service life, while Oldham disks might need periodic replacement in stop-start conveyor use.
- Inertia and Balance: With aluminum hubs and a lightweight spider, jaw couplings add minimal inertia to the system – an important consideration for fast-moving conveyor drives (low inertia means the motor doesn’t have to work against a heavy coupling). They are also balanced by design for high-speed operation, unlike some single-piece beam couplings, which can introduce vibration at high RPM. Bellows and disc couplings are also low-inertia and high-speed, but again, they lack the damping that jaw couplings provide.
- Electrical Isolation: The polyurethane spider electrically isolates the two hubs (no metal-to-metal contact), which can be beneficial if your conveyor’s motor drive and driven components need isolation (to break ground loops or protect sensitive sensors from stray currents). Metallic couplings like bellows or rigid types do not offer this, and even beam or disc couplings still have metal continuity. Oldham couplings with plastic center disks do provide isolation, but as noted, they have other trade-offs.
In summary, Ruland jaw couplings offer a balanced compromise: they are rigid enough for accurate positioning, yet forgiving enough to smooth out shocks and misalignment. This combination often makes them the ideal choice for precision conveyors, compared to other coupling styles, which might be too rigid (and thus transfer shocks) or too flexible (and introduce positioning error).
Solutions from PIB Sales
While jaw couplings are extremely versatile, PIB Sales also provides a full range of other Ruland coupling solutions to meet various application needs. Depending on your conveyor or machinery requirements, you might consider:
- Oldham couplings. Three-piece couplings with two hubs and a floating center disk (usually plastic). They allow generous parallel misalignment and exhibit zero backlash when preloaded. In conveyors, Oldhams are useful if shafts are notably offset or where electrical isolation is needed. They have a fail-safe like jaw couplings (if the disk fails, hubs interlock to some degree). However, Oldhams introduce a slight radial compliance, and the disk is a wear element.
- Beam couplings. One-piece aluminum couplings with helical cuts (spiral beams) that give flexibility. They can accommodate more angular misalignment and axial motion than jaw couplings, and have zero backlash. They are suitable for light-duty encoders or small conveyors, but they have lower torque capacity and can act like a spring under load (lower torsional stiffness). Ruland offers both six-beam and four-beam versions, in aluminum or stainless steel, to handle different torque/misalignment profiles.
- Bellows couplings. These couplings have thin metal bellows connecting the hubs. They combine zero backlash with very high torsional rigidity, making them excellent for precise motion control. They can handle some angular misalignment, but no damping. In a conveyor context, bellows couplings would be chosen for the most exacting positioning tasks (e.g., vision inspection conveyor drives) where any twist must be minimized.
- Disc couplings. Consists of two hubs connected by one or more thin, flexible discs (stainless steel) bolted between them. Ruland’s miniature disc couplings allow a bit of misalignment and have zero backlash, with high stiffness similar to bellows couplings. They are often used in precision servo-driven systems. For conveyors, disc couplings could be used in indexing tables or robotic palletizers where positioning is critical. They are lightweight and can run at high speeds, but like below, they do not dampen vibration.
- Rigid couplings. As the name implies, these have no flexibility – they lock two shafts together as one. Ruland makes one- and two-piece rigid couplings, and they are the most torsionally stiff option (essentially infinite stiffness). They should only be used when shafts are precisely aligned, as they cannot accommodate misalignment. In conveyors, rigid couplings might be used to join stub shafts or gearboxes where alignment is controlled, and any compliance would be detrimental.
- Shaft Collars and Clamping Devices. In addition to couplings, PIB Sales can supply Ruland’s quick-clamp collars (which use a cam lever for tool-free clamping) and standard shaft collars (one- or two-piece). While not couplings, these are often used on conveyor systems as mechanical stops, guides, or for mounting components. They share the same quality of finish and clamping mechanism as the coupling hubs, ensuring they won’t mar the shaft and will hold alignment.
Each of these solutions is available through PIB Sales. If a jaw coupling isn’t the perfect fit for a specific conveyor scenario, PIB’s sales staff can help identify if one of the above coupling styles might be more suitable (for example, an Oldham coupling for a notably misaligned drive, or a bellows coupling for a high-precision indexing table).
Please contact us at [email protected] or visit www.pibsales.com.