Ball bearings are used in a wide range of mechanical applications to reduce friction between two moving parts. Radial ball bearings and Angular contact ball bearings are two common types of ball bearings that differ in their design and application. This article will explore the advantages, disadvantages, and applications of each type, providing a comparison to help engineers choose the right bearing for their needs.
Radial Ball Bearings
Radial ball bearings are designed to handle radial loads, which are perpendicular to the axis of rotation. They are widely used in numerous applications including electric motors, fans, and pumps, where they provide low friction and high-speed operation. The number of applications for ball bearings is endless. All markets including Industrial, Automotive, Aerospace and Defense, as well, Robotics and Agriculture apply the use of radial ball bearings extensively in their design.
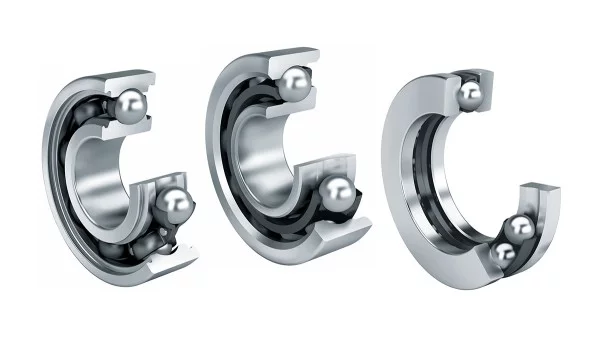
Radial Ball bearings come in all types of designs making them versatile for use in a majority of applications. Radial ball bearings come in single row, double row, thin section and other configurations making them ideal for both standard and high speed, low and high loads and useful if properly selected for not only radial loads but can handle some axial and combined loads with limits. Make sure you evaluate the use of ball bearings completely before considering other options because these bearings are going to be the most economical and easy to find and replace in the marketplace.
Benefits of Radial Ball bearings
Radial ball bearings, also known as deep groove ball bearings, are essential components in many mechanical applications due to their numerous advantages. These bearings are engineered to support both radial and axial loads, making them versatile and capable of handling various loading conditions. Their rolling element construction significantly reduces friction, enhancing efficiency and minimizing energy consumption. This low-friction characteristic is particularly beneficial in high-speed applications where maintaining low resistance is crucial.
Additionally, radial ball bearings offer high precision and accuracy, ensuring smooth and reliable operation in applications requiring tight tolerances. Their construction allows for a longer service life, especially under high-speed and high-load conditions, reducing the frequency of replacements and maintenance. Radial ball bearings are also versatile, available in various sizes and configurations, making them suitable for a wide range of applications, from small instruments to large industrial machinery.
Ease of maintenance is another significant advantage of radial ball bearings. They require minimal upkeep, and their lubrication needs are straightforward, contributing to lower overall maintenance costs. Moreover, radial ball bearings operate quietly due to the rolling elements, which is advantageous in noise-sensitive environments.
When to use Radial Ball bearings?
Radial ball bearings are particularly useful in the following scenarios:
- Their low friction and efficient load distribution make them ideal for electric motors, fans, and centrifuges.
- Suitable for applications requiring the support of both radial and axial loads simultaneously.
- Ideal for industries where longevity and reliability are paramount, such as automotive components and industrial machinery.
- Practical in environments where maintenance access is limited or costly, such as remote installations and automated systems.
- Beneficial for applications where noise reduction is essential, including household appliances, office equipment, and HVAC systems.
Applications
- Electric motors;
- Fans;
- Pumps;
- Conveyors.
Angular Contact Ball Bearings
Angular contact ball bearings are designed to handle both radial and axial loads, which are parallel and perpendicular to the axis of rotation, respectively. They have a variety of contact angles that allows them to withstand high axial loads without deformation, making them suitable for applications that require high precision and speed.

Angular contact ball bearings can handle both radial and axial loads, making them suitable for applications with combined loads.
Angular contact ball bearings have high-speed capabilities due to their low-friction design. Angular contact ball bearings provide high precision and accuracy due to their ability to maintain contact with both inner and outer raceways.
These bearings are generally offered in both single and double row designs. The single row design has a solid inner and outerring and the balls are retained using a steel, phenolic brass or polymide cage. The races are offset from each other along the bearing axis.
Double row angular contact bearings are designed to handle especially heavy loads and can support axial loads in both directions. The double row version is suitable for designs where rigid and axial guidance is necessary. High precision versions of these bearings are used extensively in high speed spindles, machine tools and robotics. Many high technology designs in Aerospace, Industrial and Scientific areas are good candidates for using Angular contact bearings needing pure thrust or a combination of both radial and axial load requirements.
Benefits of Angular Contact Ball Bearing
Angular contact ball bearings are designed to handle both radial and axial loads, thanks to their unique construction. The inner and outer ring raceways are offset relative to each other in the direction of the bearing axis, allowing them to support high axial loads in one direction and moderate radial loads. This design feature makes them highly suitable for applications requiring combined load support.
One of the key benefits of angular contact ball bearings is their ability to operate at high speeds while maintaining stability and precision. They are constructed to withstand high rotational speeds without compromising performance, making them ideal for applications where both speed and accuracy are critical. The contact angle, which can be adjusted during manufacturing, further enhances their load-carrying capacity and performance under axial loads.
Angular contact ball bearings are also known for their rigidity. The preloading process, which applies a constant axial load during assembly, increases the stiffness of the bearing assembly, reducing deflection and improving accuracy under load. This rigidity is particularly beneficial in precision applications where maintaining alignment and reducing vibration is crucial.
In terms of lubrication, angular contact ball bearings require careful management to ensure optimal performance and longevity. They typically use grease or oil, and the lubrication system must be designed to accommodate the high-speed operation and axial load support. Proper lubrication minimizes friction and wear, contributing to the extended service life of these bearings.
When to use Angular Contact Ball Bearing?
Angular contact ball bearings are particularly useful in the following scenarios:
- Ideal for applications requiring high rotational speeds and precision, such as in machine tool spindles and turbines.
- Suitable for situations where both axial and radial loads need to be supported, such as in automotive and industrial machinery.
- Essential in applications demanding high rigidity and accuracy, such as in robotics, aerospace components, and precision instruments.
- Optimal for applications with significant axial loads in one direction, including pumps, compressors, and gearboxes.
- Beneficial in scenarios where maintaining alignment and reducing vibration under load is critical, such as in high-speed milling and grinding machines.
Comparison
Radial ball bearings and angular contact ball bearings differ in their design, load capacity, speed capabilities, and application. Radial ball bearings are suitable for handling radial loads with some limited capacity for both radial and axial, while angular contact ball bearings are designed for axial loads with an ability to handle both radial and axial loads when installed correctly. Angular contact ball bearings are often used in higher speed applications than radial ball bearings, but both are capable of high speeds.
When it comes to choosing the right bearing, engineers should consider their application requirements and determine which type of bearing is most suitable. If the application involves only radial loads, then a radial ball bearing may be the best choice. However, if the application involves mixed loads or high-speed operation, then an angular contact ball bearing may be the better option. Do not without proper investigation assume that one of these types of bearings is the only way to go. Both types of bearings can equally be used in a lot of applications so it would be prudent to look at the economical reasons and availability of types before specifying one over the other.
Choosing the right bearing
To choose the right bearing, engineers should consider the following factors:
- Type of load (radial, axial, or combined) or all of these;
- Speed requirements;
- Precision requirements;
- Temperature range;
- Lubrication requirements;
- Maintenance requirements.
By analyzing these factors, engineers can determine which type of bearing is most suitable for their application and select the appropriate bearing size, clearance, and preload.
Conclusion
Radial ball bearings and angular contact ball bearings are two common types of ball bearings that differ in their design, load capacity, speed capabilities, and application. By understanding the advantages, disadvantages, and applications of each type, engineers can choose the right bearing for their needs and ensure optimal performance and reliability.
Still have a question or need to discuss something? Contact us to get help.