In robotics, the precision functioning of mechanical components is required for optimal performance. Bearings, serving as vital components in robotic systems, play a pivotal role in reducing friction and facilitating smooth rotational and linear motion. Robots, like humans, move forward and backward, side to side, upward and downward, and rotate. Robotic bearing motion can be defined as linear motion (back and forth) and/or rotational motion, either along or in between the axis.
Different types of bearings possess unique characteristics that will accommodate these movements. This article delves into the fascinating world of bearings, exploring their distinct types, underlying principles, and their impact on robotic systems.
IKO Crossed Roller Bearings
Crossed roller bearings are critical as one of the first types of bearings you need to familiarize yourself with for use in Robotics incorporating articulating arms. Articulating arms are commonly used in automation machinery and robotics to move position or rotate heavy objects. IKO is the leader in crossed roller bearings, which are available through Pacific International Bearing Sales.
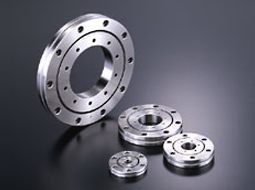
Kaydon Reali-Slim® Bearings
Kaydon is a leader in slim section bearings used in Robotics. Designers look to lighter weight and use Kaydon bearings to allow for maximized payloads with reduced inertia. When space requirements are a concern, Kaydon’s products meet the standard for compact components, reducing weight by 83% and space by 85% when you compare Kaydon to a standard 6010 radial ball bearing.
Kaydon’s Reali-Slim bearings feature a constant cross-section regardless of bore diameter while providing precision and significant dynamic capacity. Reali-Slim Type X four-point bearings accommodate combined radial, thrust, and overturning moment loads. The Type X four-point bearing provides a simple aspect to a robot’s overall design by replacing a pair of angular contact bearings with one.
Kaydon’s Duplex pairs are used for low torque and higher stiffness, and when preloaded, eliminate the need to shim. If needed, Kaydon Cartridge bearings offer a single inner and outer race for optimal torque performance. Applications include robotic surgery, artificial limbs, personal robots, and exoskeletons.
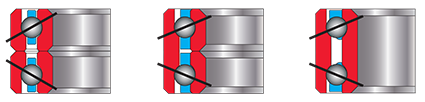
Kaydon is the leader in Reali-Slim® Thin Section bearings, Slewing Ring bearings, Reali-Slim TT® Turntable bearings, Duplex and Super Duplex, and Cartridge bearing assemblies, all of which are available through Pacific International Bearing Sales Inc.
INA Plain Bearings
Due to their diverse and specific characteristics, Schaeffler plain bearings are used in almost all industrial sectors and very specifically in Robotics applications. Any sort of joint or pivot point is a viable candidate for a spherical plain bearing which allows for misalignment and rotation. Plain bearings, also known as sleeve bearings or journal bearings, are characterized by their simplicity and versatility. These bearings consist of a shaft rotating within a cylindrical bushing, usually made of materials such as bronze, brass, or composite polymers. While plain bearings may not possess the same load capacity as rolling element bearings, they offer distinct advantages for certain robotics applications.
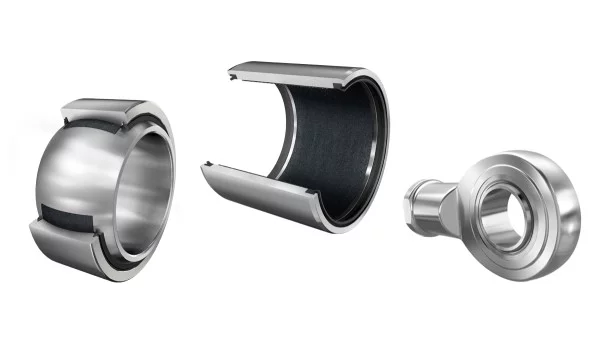
Rolling Element Bearings
Rolling element bearings are prevalent in robotics and consist of an inner race, an outer race, and rolling elements such as balls or rollers. These bearings are classified into ball bearings and roller bearings.
Ball bearings are commonly used due to their suitability in numerous applications. Their ability to distribute loads evenly, combined with reduced friction, enables efficient rotation in robotic joints.
Roller bearings, including cylindrical, tapered, and spherical, are utilized in robotic applications involving heavy radial loads or misalignment. These bearings provide increased contact area, enabling them to withstand higher loads. In robotic arms that handle heavy payloads, cylindrical roller bearings efficiently support the load while maintaining motion accuracy.
Self-Lubricating Bearings
Self-lubricating plain bearings, incorporating materials like PTFE (polytetrafluoroethylene) or graphite, eliminate the need for external lubrication. These bearings reduce maintenance requirements and are ideal for robotic systems operating in harsh environments or inaccessible areas where regular lubrication is impractical. Radial spherical plain bearings comprise inner and outer rings with maintenance-free sliding layers made from ELGOGLIDE®, PTFE composite, or PTFE-bronze film. They are thus suitable for alternating dynamic loads. Large spherical plain bearings from d = 320 mm belong to the X-life premium class.
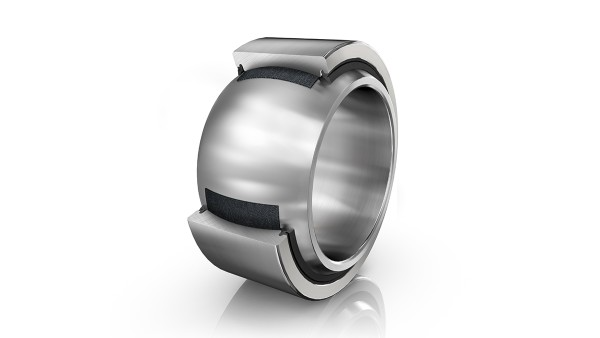
Hydrodynamic Bearings
Hydrodynamic bearings leverage the principle of fluid film lubrication to minimize friction. By maintaining a continuous oil film between the shaft and the bearing surface, hydrodynamic bearings offer exceptionally low friction and high load-carrying capacity. They are well-suited for high-speed robotic applications, such as robotic machining or spindle assemblies.
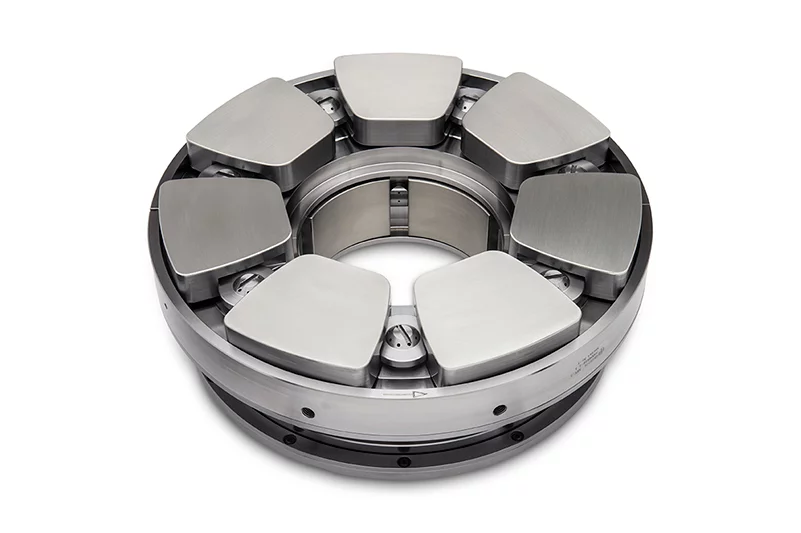
Magnetic Bearings
Magnetic bearings exploit magnetic levitation to eliminate physical contact between the rotating and stationary parts. The absence of mechanical friction enables precise control over rotor position and allows for ultra-smooth and vibration-free operation. Magnetic bearings find applications in sensitive robotic systems, such as precision robotics used in semiconductor manufacturing or scientific research.
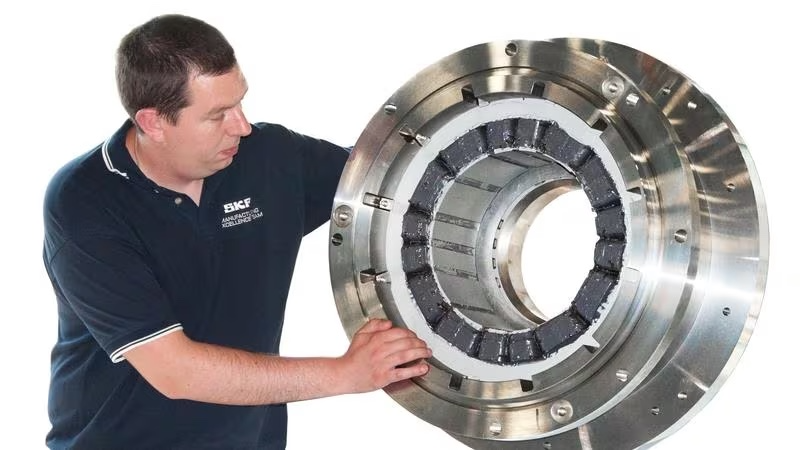
Impact on Robotic Performance
The choice of bearing type has a significant impact on robotic performance metrics, including accuracy, efficiency, and longevity.
Precision and Accuracy
High-precision bearings with low friction coefficients enable accurate positioning of robotic joints and end-effectors, ensuring precise execution of tasks. For instance, in pick-and-place operations, the choice of low-friction ball bearings can minimize errors, leading to improved accuracy in object manipulation.
Energy Efficiency
Bearings with low friction characteristics reduce energy consumption, enhancing the overall efficiency of robotic systems. By reducing internal losses, the use of appropriate bearings can extend battery life in mobile robots or optimize power usage in industrial robotic arms, resulting in cost savings and improved sustainability.
Durability and Reliability
The load-carrying capacity and robustness of bearings determine their ability to withstand operational stresses. Choosing bearings with adequate load ratings and appropriate materials ensures prolonged system life and reliability, minimizing maintenance requirements and downtime.
Bearing selection plays a crucial role in determining system performance. Whether it be rolling element bearings, plain bearings, magnetic bearings, or special designs, each type offers distinct advantages for different robotic applications. By considering the unique requirements of a robotic system, engineers can optimize performance, accuracy, and efficiency, propelling robotics into new frontiers of innovation and advancement.
Still have a question or need to discuss something? Contact us to get help.