Every bearing will sooner or later become unserviceable over its intended life. Even when it is installed and serviced according to manufacturers recommendations. Raceway surfaces and rolling contact surfaces are subjected to compressive loads, and the surfaces eventually become subject to flaking.
However other failure modes which are a more common cause of failure include seizing, breakage, wear, false brinelling, and corrosion. In many cases, these failures are due to improper handling, poor selection, bad bearing design and poor maintenance. This article is intended to provide an overview discussion on key points to follow as a standard maintenance guideline.
Inspection of Bearings
Inspecting the bearings after initial installation while the machine is in operation will help in preventing future bearing failures. The following is a list of procedures you should follow.
Inspection when machine is running
Check the bearing temperatures and bearing vibration/noise and determine if the bearing is lubricated properly or needs more lubrication.
Inspection of bearings after operation
Bearings should be carefully examined in periodic maintenance inspections for you to note any damage. If damaged the bearing can be analyzed and the cause of failure determined. Remedies can then be provided to prevent further problems.
It is important to determine inspection procedures and establish regular inspection intervals.
Bearing Temperature
Bearing temperature generally will increase at start-up and stabilize at a temperature slightly lower than at start-up (normally 10 to 40 ̊C higher than room temperature) over a set period of time. The time for the operating temperature to stabilize depends on the size, type, speed, and lubrication. The heat dissipation depends on the operating environment of the surrounding components. The stabilization can range from as little as 20 minutes to several hours.
The thing to watch is if the bearing temperature does not stabilize but continues to rise. If the temperature continues to rise it may be the result of one of the following reasons:
- Extremely insufficient or excessive lubricant
- Poor installation of the bearings
- Extremely small bearing clearance or extremely heavy load
- Extremely high friction between lip and seal groove
- Improper lubricant type
- Creep between the fitting surfaces
If any of these conditions are present then operation should be stopped and an appropriate corrective action should be taken. A desirable bearing operating temperature is generally below 100 ̊C.
Bearing Noise levels
The following Table lists typical abnormal bearing sounds and their causes. Please note that the descriptions of some of these sounds are rather subjective and thus could vary considerably from person to person.
Sound | Features | Causes |
Buzz Roar Howl | Rough raceway, balls, or roller surfaces. | Dust/contamination. Rough raceway, balls, or roller surfaces. Damaged raceway, balls, or roller surfaces. |
Hissing | Small bearings. | Rough raceway, balls or roller surfaces. |
Chatter | Generated intermittently at regular intervals. | Contact with labyrinth or other sections. Contact between cage and seal. |
ScreechHowl (grinding sound) | Resonance, poor fit (poor shaft shape). Deformed raceway. Vibration in raceway, balls, or roller surfaces (minor sound considered normal for large bearings). | Damaged raceway, balls, or roller surfaces. |
Crunch Chatter | Felt when bearing is rotated by hand. | Damaged raceway (felt at regular intervals). Damaged balls or rollers (felt at irregular intervals). Dusi/contamination, deformed raceway. |
Rustle Rattle | Large bearings. Small bearings Continuous at high speeds. | Primarily in cylindrical roller bearings, changes with changes in speed sounds metallic when loud. Eliminated temporarily when refilling grease. |
Whir Hum | Disappears as soon as power is switched off. | Electromagnetic sound of motor. |
Tinkle | Generated at irregular intervals (remains constant with changes in speed). Primarily with small bearings. | Dusi/contamination. |
Rustle Clatter Patter Clutter | Tapered roller bearings Generated· Large bearings continuously at small bearings regular intervals at high speeds. | Normal if sound generated by cage is clear. Inadequate grease if generated at low temperatures-+ use soft grease. Worn cage pockets, insufficient lubrication, operating with insufficient bearing load. |
Fizz Pop Growl | Noticeable at low speeds. Generated continuously at high speeds. | Clashing sound from inside cage pockets, insufficient lubrication. Eliminated by reducing clearance or applying preload. Rollers hitting each other in full-roller bearings. |
Clang Clatter | Loud metallic clashing sound in thin section type large bearings at low speeds. | Unstable sound from rolling elements. Deformed raceway. Key grating. |
Squeak Squeal Growl | Too high a consistency of lubricant (grease). Too large radial clearance. Insufficient lubricant. | Rough raceway, balls, or roller surfaces. Raceway, rollers, or balls are deformed by wear. Large clearance due to wear. |
Screech Shrill Shriek | Metal-to-metal spalling sound. High pitch. | Spalling between rollers and ribs of roller bearings. Too small clearance. Insufficient lubricant. |
Quiet Fizzing/Popping | Generated irregularly on small bearings. | Bursting sound of bubbles in grease. |
Sputter Crackle | Grating sound generated irregularly. | Fitting flange slipping. Mounting surface grating. Key or other grating. |
Large overall sound pressure. | Rough raceway, balls or roller surfaces. Raceway, rollers, or balls are deformed by wear. Large clearance due to wear. |
Bearing Vibration
Damage to the bearing can be detected early on by measuring the vibration of the machine. The degree of bearing damage is determined using quantitative analysis of the amplitude and frequency of the vibration. You should be careful to understand that values measured differ depending on the measuring point and the operating condition of the bearing. Try to create measurement data and then establish evaluation criteria for each machine.
Lubrication
Lubricate the bearing so as to provide a film of oil for the rolling contact surfaces and sliding contact surfaces which circumvents direct metal-to-metal contact. Effective lubrication of the rolling elements provides the following benefits:
- Reduces friction and abrasion;
- Transports heat generated by friction;
- Prolongs service life;
- Prevents rust and corrosion;
- Keeps foreign objects like dust and dirt and corrosion away from rolling elements and raceways.
Grease lubrication
Grease is commonly specified lubricating rolling-element bearings because it is easy to apply and simplifies the sealing system.
Carefully examine the type and properties of the base oil, thickener and additives of the grease, then select a grease appropriate for the operating condition of the bearing. Most manufacturers catalogs list a variety of greases but often just a few cover most bearing applications and are considered standard by these same companies.
Oil lubrication
Oil lubrication is generally called out for high-speed or high-temperature operations. It is also ideal for dissipating heat away from the bearing.
Oil viscosities required for the operating temperatures of bearings are found in manufacturers catalogs. The viscosity, viscosity index, oxidation resistance, corrosion resistance, and foaming resistance are criteria for selecting the best oil for your application. Please consult with us at [email protected] for assistance.
Relubrication
Grease deteriorates over time the longer they are in operation. Standard maintenance should include relubrication intervals dependent upon the type of grease, bearing dimensions, speed and other factors such as where the bearing is installed and ease of access. Oil lubrication may also need to have a maintenance interval and analysis of operation during its life.
Bearings Evaluated following its Service Life
When bearings have been removed from service a periodic inspection should be done visually checking for symptoms to determine if the bearing’s operating life was satisfactory.
If any abnormality is found then the bearing should be further examined to determine remedies.
Bearing Failures and Solutions
In most cases, bearings will be capable of meeting the calculated fatigue life if handled properly. If premature failure occurs it likely is due to selection, handling, lubrication or mounting errors.
It is also possible that determining actual failure causes is not possible. It is important to consider the location of the bearing in the machine and determine if surrounding components are contributing to the failure.
Mounting and Dismounting of Bearings
For bearing handling use gloves. When moving larger bearings use special lift and carrying tools designed specifically for mounting and dismounting bearings. Both SKF and Schaeffler offer these special types of tools and can be purchased from PIB by going to www.pibsales.com. The use of heat and oil-resistant gloves is recommended when handling hot or oily bearings. These gloves should have a durable outside and a soft non-allergenic inside. We recommend SKF TMBA gloves.
If large, heavy bearings are to be moved or held in position using a lifting tackle they should not be suspended at a single point utilizing a steel band or fabric belt. A spring between the hook of the lifting tackle and the belt facilitates proper positioning for the bearing when it is to be pushed onto a shaft.
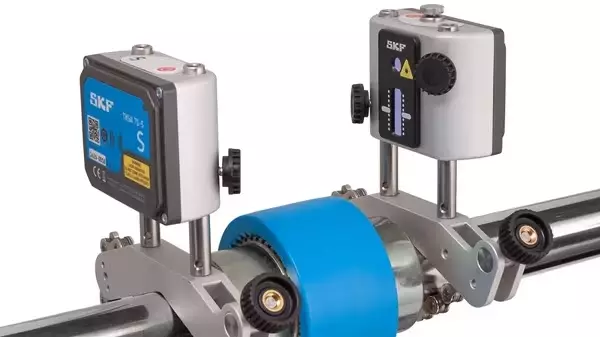
Alignment tools
Misalignment of shafts, belt drives, and chain drives will contribute to machinery breakdowns.
Accurate alignment will prevent a large number of machinery breakdowns and reduce the number of shutdowns. Accurate alignment will help to extend the life of the bearings and machines.
In today’s challenging environment for cost reduction, the necessity of accurate alignment is needed more than ever.
Preparing for Mounting of bearings
Prior to the mounting process, one must ensure that the bearing, the shaft, and the housing are clean and free of any foreign particulates. It’s important to remember that even microscopic debris, when lodged between rolling elements, will cause excessive wear. Bearings should be kept in their original packaging until the moment of installation to prevent contamination.
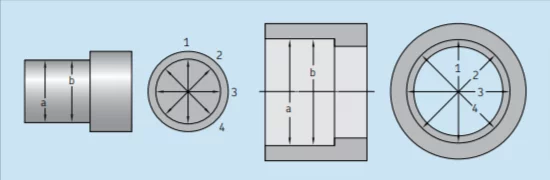
Mounting
The methods employed for mounting are contingent on the bearing’s design, size, and the application’s specificities.
The principle of interference fits, characterized by the formula:
ΔD=α×D×ΔT where
- ΔD signifies the expansion in diameter,
- α denotes the material’s thermal expansion coefficient,
- D represents the bearing’s original diameter, and
- ΔT is the temperature variation and is predominantly utilized.
Cold mounting is often used for small to medium-sized bearings, employing specialized tools to ensure uniform force distribution. Conversely, larger bearings often use heat for mounting, utilizing controlled temperature differentials to facilitate a smoother fitting process, typically achieved with induction heaters.
Removal Tips
Removing bearings, especially those in service for an extended period, requires specialized tools like bearing pullers. Application of force should be even and gradual to prevent damage to the shaft, bearing, or housing. A post-dismounting analysis, inspecting for wear patterns or deformities, can offer insights into the operational conditions and potential deviations from optimal machinery performance.
- Preparation: Power off the machinery and ensure that any load on the bearing is removed. Prep the workspace and gather the necessary tools.
- Removal Approach:
Utilize bearing pullers or extraction tools to provide a uniform force.
For bearings mounted using an interference fit, induction heaters may be used to expand the bearing and facilitate its removal.
In cases of a tight fit or a bearing that’s been in operation for an extended period, penetrating lubricants can aid the removal process.
- Post-Removal Inspection: Once removed, the bearing should undergo a detailed inspection to ascertain wear patterns and potential damages, offering insights into the operational health of the machinery.
This mounting and removal process ensures that bearings will obtain their maximum potential in terms of efficiency and life.
Shaft and housing fits
The interface between bearings, shafts, and housings plays an important role in the proper functioning of mechanical systems. Achieving the right fit between these components is essential for long bearing life and optimal performance.
Engineers determine the correct fit for bearing installations and must be followed by the installer for the best outcome. Bearings generally will have an interference, transition, or clearance fit.
Both housing and clearance fits must be adhered to so the bearings will operate at maximum efficiency.
Major manufacturing companies such as SKF, Schaeffler, NTN and NSK offer housing and shaft fit charts for reference. Please contact us at Pacific International Bearing Sales for further help at [email protected].
Maintenance Tools
1. Bearing Pullers
A bearing puller is a mechanical tool specifically designed for the dismounting of bearings from a shaft. It typically consists of a central mandrel and two or more adjustable arms that grip the bearing securely. By turning the mandrel, a constant axial force is applied, enabling the removal of the bearing without damaging adjacent components. Different configurations, such as three-arm or two-arm pullers, cater to various bearing sizes and applications.
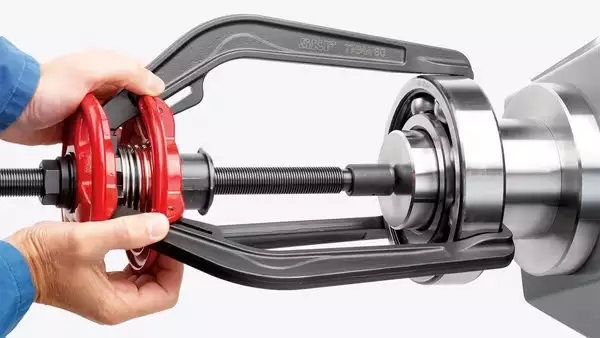
2. Bearing Induction Heaters
These devices utilize electromagnetic induction to generate controlled heat, facilitating the thermal expansion of bearings. Comprising a coil encased within a metallic core, bearing induction heaters pass an alternating current through the coil, inducing a magnetic field. The bearing, when placed within this field, heats uniformly. This controlled heating ensures that the bearing can be mounted onto the shaft with reduced force, minimizing the risk of installation damage.
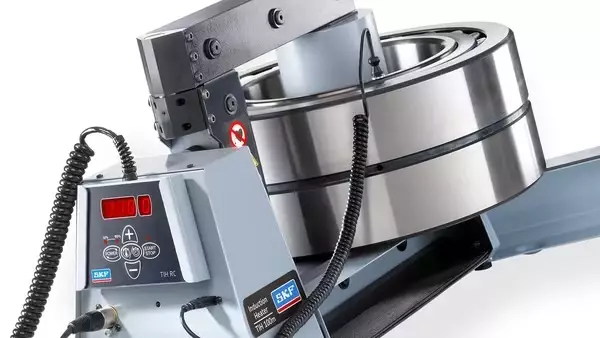
3. Shaft Alignment Tools
Shaft misalignment can lead to uneven load distribution in bearings, reducing their operational life. Laser shaft alignment tools are designed to achieve precise alignment between two connected shafts. Utilizing laser diodes and detectors, these tools measure angular and radial deviations, providing real-time feedback to technicians. With such data, necessary adjustments can be made, ensuring optimal bearing function.
4. Lubrication Dispensers
Correct lubrication is vital for bearing longevity. Lubrication dispensers, which include manual grease guns and automatic lubricators, deliver a specified amount of lubricant to the bearing. Precision in lubrication application reduces frictional wear, prevents contamination ingress, and ensures efficient heat dissipation.
5. Stethoscopes and Vibration Analyzers
For diagnostic purposes, mechanical stethoscopes and vibration analyzers are employed. Mechanical stethoscopes, equipped with a probe, allow technicians to listen to the operational sounds of a bearing, identifying irregularities like pitting or misalignment. Vibration analyzers, on the other hand, measure the amplitude and frequency of vibrations from the bearing. By analyzing this data, one can ascertain issues like imbalance, misalignment, or early signs of wear.
Conclusion
Bearings play a pivotal role in machinery operation. Adopting a good maintenance strategy, as detailed in this discussion, can optimize equipment efficiency, minimize operational interruptions, and yield considerable economic benefits.
Still have questions or want to discuss something? Please Contact us at [email protected].