Understanding your application requirements, operating environment, loads, and speeds are the basics for getting started in your search for the best bearing design for your application.
Our article will provide insights and expert advice on bearing selection to improve efficiency and reduce costs, allowing you to make informed decisions and achieve optimal results.
Bearing Types and Their Applications
The most common types of bearings include ball bearings, roller bearings, needle bearings, thrust bearings, tapered roller, cylindrical, spherical, and plain bearings.
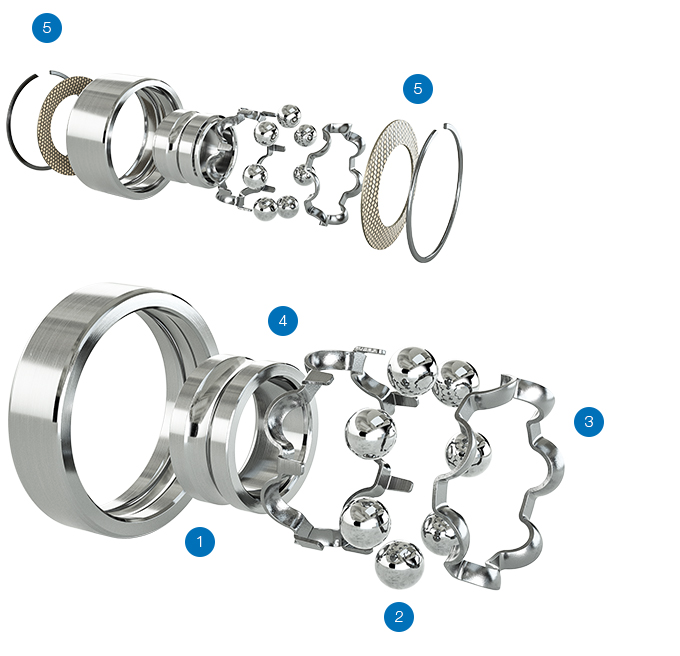
Ball bearings are designed to handle both radial and axial loads. Ball bearings have two raceways and outer and inner rings. The rings are separated by a row of steel balls that reduce friction and enable smooth rotation. Ball bearings are commonly used in applications like electric motors, pumps, gearboxes, wheels, and many different automotive applications.
Radial deep groove ball bearings are referred to as single row radial ball bearings. Most major manufacturers like SKF, FAG, NMB, and TPI offer open as well as sealed or shielded versions. They are composed of the following parts and materials:
- Outer rings are commonly made of chrome steel 52100
- Common rolling elements are ceramic or steel set of balls
- The retainer or cage is made of sheet steel or plastic in one or two part designs
- Inner rings are most commonly made of chrome steel, also known as AISI 52100 or SAE 52100
- Non-corrosive shields and seals made of sheet steel, Teflon-coated fiberglass fabrics, or Buna N rubber.
Roller bearings are designed to handle heavy radial loads and consist of cylindrical, spherical, or tapered rollers. They are commonly used in applications such as conveyor systems, large gearboxes, and wind turbines.
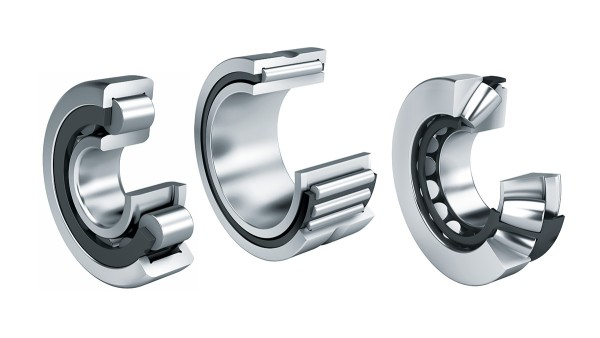
Needle bearings are used in applications with limited space for handling radial loads. They consist of thin cylindrical rollers that have a small diameter compared to their length.
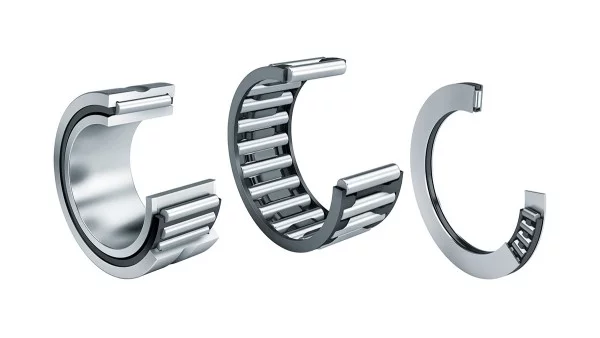
Plain bearings, also known as bushings, are used to handle light radial loads, and are typically made of brass, bronze, or plastic. They are commonly used in applications such as lawnmowers, washing machines, and textile machinery.
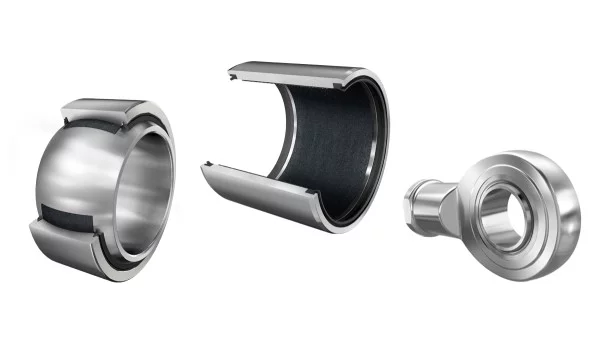
Understanding the characteristics of each type of bearing and their suitable applications is critical to ensuring the optimal performance and longevity of mechanical systems.
Bearing Selection Guide
For optimum performance and longevity, your electric motor’s bearing selection is essential. Selecting the best bearing for your application will be made easier if you understand its operating requirements.
When selecting a bearing, consider the following factors:
- Loading Capability
Both radial and axial loads unique to the application must be supported by the bearing. Choose high load rating bearings for heavy-load applications to make sure they can withstand the stresses without failing. Premature bearing wear and failure can be avoided by accurately calculating the load capacity.
- Speed of Operation
Bearings must minimize heat production and friction while operating effectively at the necessary speed. Specialized bearings, like ceramic or hybrid bearings, are frequently needed for high-speed applications since they are made to function dependably at greater rotational speeds without experiencing undue wear.
- Maintenance Needs
Choose bearings with a long service life and ease of maintenance. To streamline maintenance procedures and increase operating life, bearings with integrated seals and pre-lubrication should be specified. Maintaining constant performance and reducing downtime requires routine and easy access for maintenance and repair.
- Price
Cost and performance must be balanced. While keeping costs down is important, spending more on high-quality bearings can save maintenance expenses over time and extend service life. Make sure that important performance factors like load capacity and environmental resistance are not sacrificed in favor of less expensive bearings.
Explore our comprehensive bearings catalog to find the perfect bearing for your needs. We offer a wide range of bearings categorized by size and specifications to meet your application requirements. Visit PIB Sales today and discover high-quality, cost-effective solutions for all your bearing needs.
Factors to Consider in Bearing Selection
When selecting a bearing, consider the following factors:
- Load Capacity. The bearing must be able to support the load requirements of the application.
- Operating Speed. The bearing must be able to operate at the required speed without generating excessive heat or wear.
- Environmental Conditions. The bearing must be able to withstand environmental conditions, such as temperature, humidity, and exposure to dust or chemicals.
- Maintenance Requirements. The bearing must be easy to maintain and have a long service life.
- Cost. The bearing must provide a balance between cost and performance.
Analyzing Bearing Performance
Analyzing bearing performance is a key step in selecting the right bearing for your application. This involves assessing the bearing’s performance in terms of load capacity, speed, and service life. By analyzing bearing performance, you can determine whether the bearing is suitable for your application or if adjustments are needed.
Methods for Analyzing Bearing Performance
The following are some methods for analyzing bearing performance:
Vibration analysis is used to monitor the vibration levels and frequencies to find anomalies such as imbalance, misalignment, or problems in bearings.
RMS vibration level | 3.5 mm/s (ISO 10816-1 standards) |
Peak frequency | 120 Hz (related to bearing defect frequencies) |
Imbalance detection | 0.02 g.mm (measured imbalance) |
Misalignment indicator | 0.05 mm (axial displacement) |
The process of temperature monitoring is using sensors to continuously measure the bearings’ temperature and spot any unusual rises that might point to problems.
Normal operating temperature | 60°C |
Alarm threshold | 80°C |
Critical temperature | 90°C (beyond which bearing failure may occur) |
Recorded peak temperature | 85°C |
To guarantee that the bearings are properly lubricated, lubrication analysis examines the lubricant’s viscosity, degree of contamination, and chemical makeup.
Viscosity at 40°C | 68 cSt (centistokes) |
ISO cleanliness code | 16/14/11 (indicating levels of particle contamination) |
Water contamination level | 200 ppm (parts per million) |
Ultrasound testing uses high-frequency sound waves to detect issues such as lubrication failure, cavitation, and early-stage bearing wear.
Ultrasound level | 0.5 dBµV (decibels microvolt) |
Lubrication failure indication | >0.7 dBµV (decibels microvolt) |
Early wear detection | 0.6 dBµV (decibels microvolt) |
Wear debris analysis examines particles found in the lubricant to assess the bearing’s condition, determining the type and severity of wear.
Particle size distribution | 5-100 microns |
Wear particle count | 5000 particles/ml |
Dominant material | Ferrous particles (indicating bearing material wear) |
Wear rate | 10 mg/1000 hours |
Frequent and accurate performance analysis lowers maintenance costs and downtime by assisting in the early detection of possible issues.
Steps for Optimizing Bearing Selection
To optimize bearing selection, we suggest following a systematic approach that considers all the necessary factors:
- As stated previously, you must identify the bearing requirements for your application
- Start by identifying the load requirements, operating speed, environmental conditions, and maintenance requirements for your application. This will help narrow down the options and identify the most suitable bearing types.
- Consider the environmental factors and maintenance requirements
- Consider the environmental conditions in which the bearing will operate, such as temperature, humidity, and exposure to dust or chemicals. Also, consider the maintenance requirements, such as the frequency of lubrication and replacement.
- Determine the appropriate bearing type
- Based on the load requirements, operating speed, environmental conditions, and maintenance requirements, select the appropriate bearing type, such as ball bearings, roller bearings, needle bearings, or plain bearings.
- Analyze bearing performance and make adjustments as needed
- Analyze the bearing’s performance in terms of load capacity, speed, and service life. Adjust as needed, such as selecting a bearing with a higher load capacity or a different lubrication type.
Conclusion
Bearing selection is a critical process that requires careful consideration of factors such as load capacity, operating speed, environmental conditions, and maintenance requirements. By following a systematic approach and analyzing bearing performance, you can select the right bearing for your application, improve efficiency, and reduce costs. It is essential to work with a reputable bearing supplier who can provide expert advice and support throughout the bearing selection process.
Still have a question or need to discuss something? Contact us to get help.