Thrust ball bearings are designed for supporting axial forces. Thrust bearings are used when axial forces are too high to be transmitted by the use of radial ball bearings or where rigidity for guidance is required. In general small and medium-sized thrust ball bearings when used in normal applications are equipped with pressed steel cages. When the size of the thrust bearing is larger than machined cages steel or brass cages would be specified.
This article will present the most common types of single and double acting thrust ball bearings and their unique features.
First, there is the single-direction Thrust ball bearing either with grooved raceways or flat washers. The second type is the Double direction thrust ball bearings with a common center ring with grooves on both sides. Changing the rolling elements allows for Tapered roller thrust bearings, Cylindrical roller thrust bearings, needle roller thrust, and spherical roller thrust bearings. Another type we will discuss is the angular contact thrust ball bearing.
Single Direction Thrust Ball Bearings
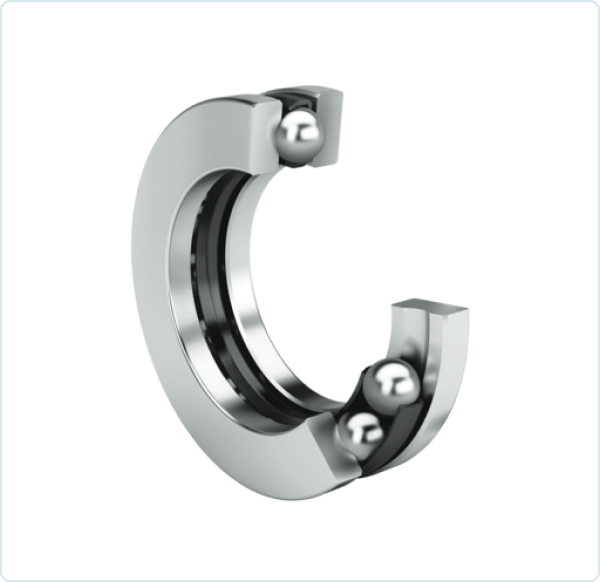
The Single Direction thrust ball bearing consists of two grooved washers and a set of balls within a cage. This bearing can also be supplied with flat washers. Under axial loads and good rolling conditions, the balls are guided in the apex of the groove. In less than desirable operating conditions such as when centrifugal forces are present then the balls are pushed outwards at high rotary speeds and very low speeds.
Double Direction Thrust Ball Bearings
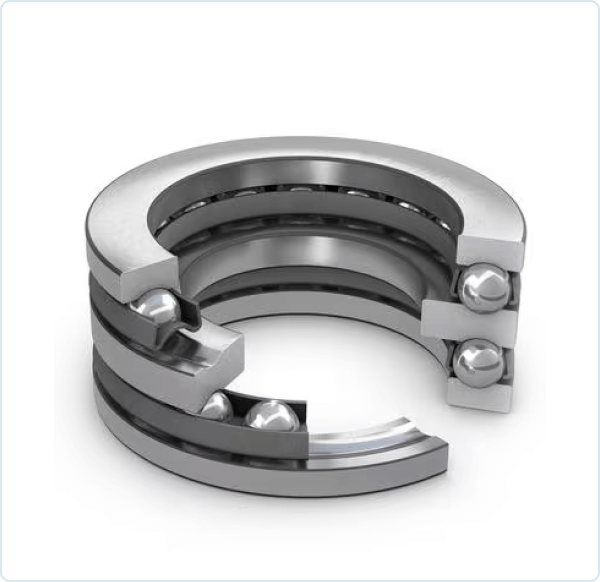
The double direction ball bearing consists of two sets of balls with two housing rings being the same as for the single direction type. The center ring has grooves on both sides and when mounted on the shaft can transmit thrust loads in either direction. This bearing cannot be used under pure radial loads. This double-acting thrust ball bearing is used for reversing axial forces and is used to allow for misalignment resulting from out of square ring seats during installation.
Angular Contact Thrust Ball Bearings
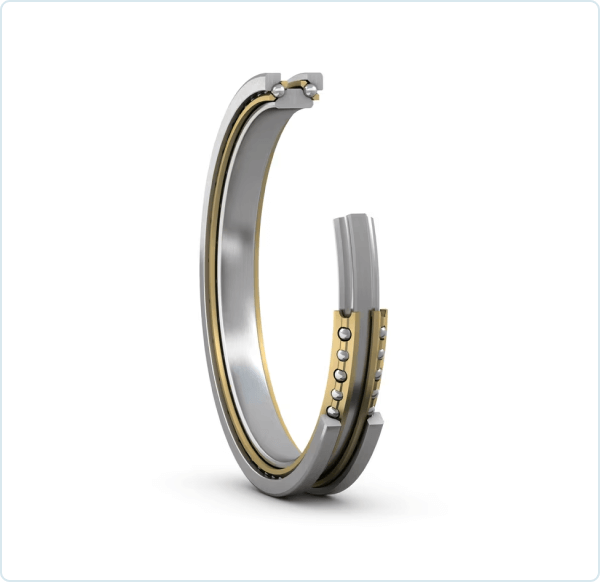
As opposed to single direction thrust ball bearings with grooved raceways the raceways for Angular contact thrust ball bearings are designed so that under certain contact angles the forces are transferred from one ball path to the other. Because of the contact angle, one shoulder on the shaft washer and one shoulder on the housing washer is raised up. The bearing contact angle ensures rigid guidance of the balls of the axially preloaded bearing. For high speed machine tool spindles where rigid guidance is required the single and double acting angular contact thrust ball bearings are ideal.
Spherical Roller Thrust Ball Bearings
A spherical roller thrust ball bearing contains a set of asymmetrical barrel rollers. The rollers are inclined so steeply to the rotary axis the bearing can accommodate high axial forces and considerable radial forces. The barrel rollers are supported by the high inner ring lip and can self-align in the spherical outer raceway.
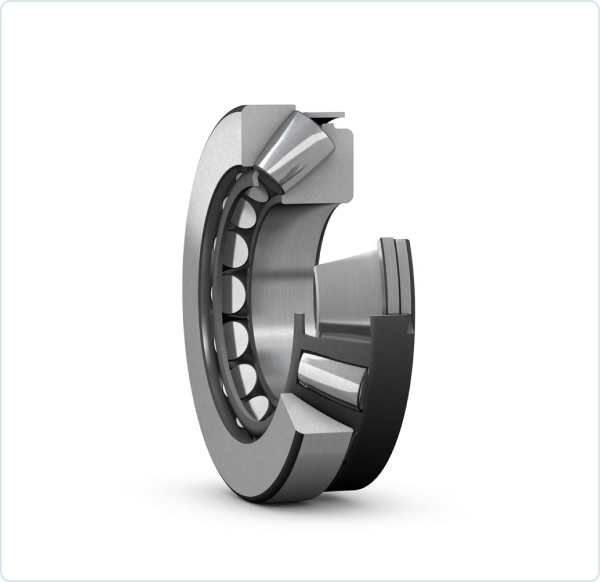
This design providing for self alignment also becomes impervious to shaft deflections. Similar to the other designs the spherical roller thrust bearing is provided with machined brass or pressed steel cages. Some applications for this type of bearing include column bearings for cranes, propeller thrust blocks in ship building, slewing column bearings in heavy equipment engineering, and heavy worm gears.
Cylindrical Roller Thrust Bearings
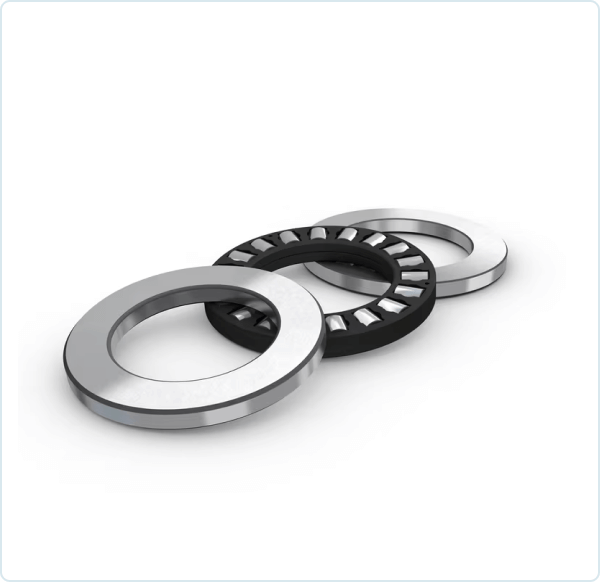
In the case of Cylindrical Roller thrust ball bearings they are generally manufactured as single acting consisting of two plain lipless washers and a set of cylindrical rollers in star formation held together in a cage. Cylindrical roller thrust bearings are manufactured with or without flanges for guiding the rollers. With many rows of rollers, pure rolling cannot occur between the rollers and the flat rings so these bearings must only be used in slow speed applications. These bearings can move in the radial direction. Sliding happens at the inner and outer ends of the rollers during rotation. A machined shaft guided brass cage is commonly used for the retention of the guided rollers.
Needle Roller Thrust Bearings
Needle roller thrust bearings are designed utilizing roller in place of ball bearings using flat washers where the mounting height is small. Needle roller thrust bearings despite their small diameter compared to length have high load carrying capacity.
Tapered Roller Thrust Bearings
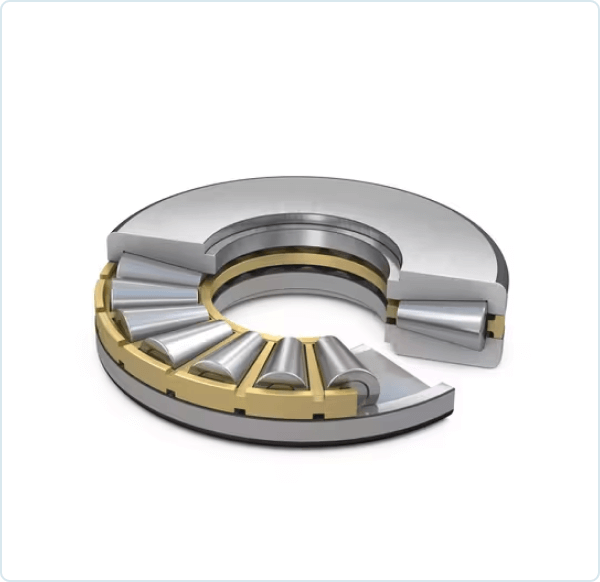
Tapered roller thrust bearings are produced in several designs. The most common design is where the raceway of the shaft washer is conical with the housing washer being flat. The tapered angle of the rollers is selected to permit the extended contact lines to intersect on the bearing axis.
The rollers are guided by the lip of the shaft washer and generally retained in a machined brass cage. This bearing can align itself in the radial direction.
Still have a question or need to discuss something? Contact us to get help.