GMN Bearing
GMN has consistently delivered cutting-edge solutions for various industries earning a reputation for excellence and reliability in the field of bearing technology.
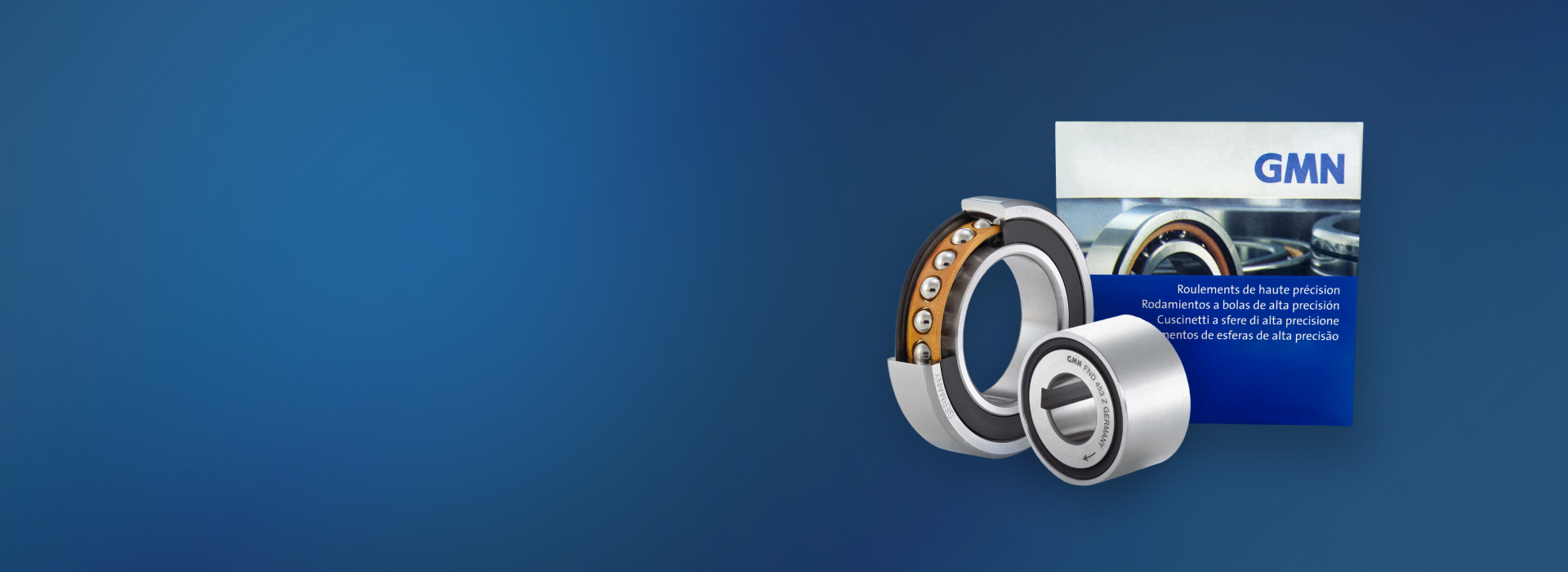
GMN Bearings
Over the years, GMN Bearings has demonstrated remarkable adaptability by evolving to meet the dynamic demands of the market. Their unwavering dedication to innovation and uncompromising quality has positioned them at the forefront of the bearing industry. GMN caters to a wide array of customers in diverse sectors, such as aerospace, medical equipment, machine tools, and automotive applications, providing tailor-made solutions to meet their unique needs.
About GMN Bearings
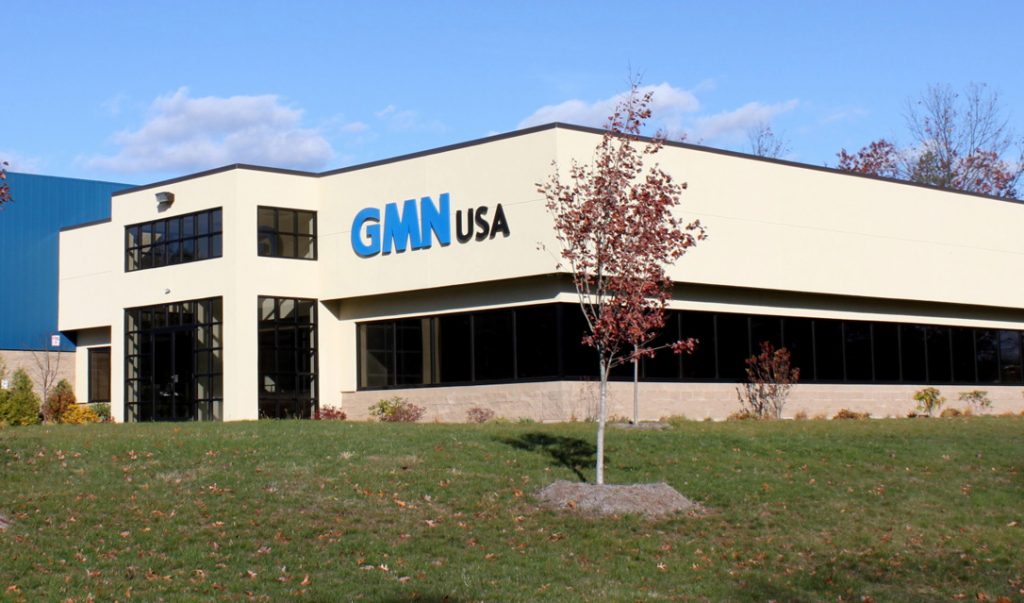
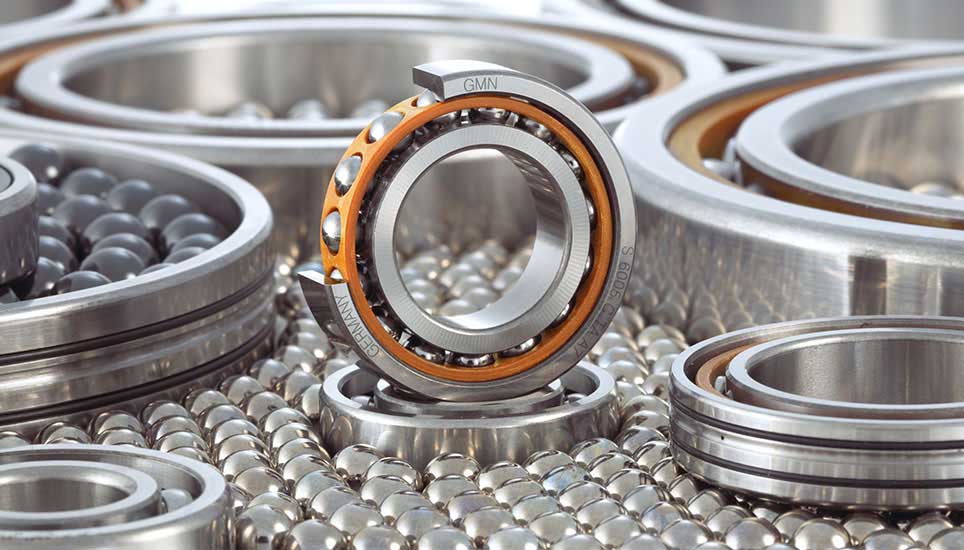
GMN is under the leadership of its fourth generation family owned business. GMN Paul Müller Industrie GmbH & Co. KG in Nuremberg manufactures high-precision ball bearings, machine spindles, freewheel clutches, non-contact seals and electric drives.
1908 Georg Müller opens his mechanical workshop;
1923 Start of ball bearing production (angular ball bearing E5);
1928 Start of “high-precision ball bearing” production;
1932 Start of production for the patented “tempo grinding spindles”;
1937 Motor-driven grinding spindle with 5 kW motor for a grinding depth of up to 1,000 mm;
1952 Belt-driven grinding spindle with 105,000 rpm
- Electric spindle for grinding holes with a grinding depth of 2,000 mm
1953 First water-cooled HF spindle with up to 30,000 rpm;
1963 Patent registration freewheel clutch;
1966 Start of production for sprag type freewheel clutches with 4 mm sprag height;
1967 Start of production for sprag type freewheel clutches with 16 mm sprag height;
1976 Start of production for non-contact labyrinth metal seals;
1978 First HF spindle for automatic tool change;
1979 Start of production for non-contact labyrinth plastic seals;
1981 High-speed milling with magnetic bearing spindle (25 kW, 30,000 rpm);
1982 HF spindle with 24,000 rpm for aluminum machining;
1983 High-speed HFS (milling) and HSS (grinding) spindles with oil injection lubrication;
1985 HF spindle with speed factor up to 1.8 mill. mm/min
- Development of the oil-air lubrication
1987 Start of production for sprag type freewheel clutches with 8 mm sprag height;
1988 Ball bearing cage made of PEEK for temperatures up to 250 °C and grease lubrication;
1989 Spindle series for internal grinding with oil-air lubrication
- High-speed HF spindle for machining centers
- Development and testing of active magnetic-bearing high-speed spindles
1991 Spindle series for internal grinding with a speed coefficient up to 2.5 mill. mm/miHF
spindle for machining centers with HSK, internal coolant supply, rotary encoder, short
acceleration and braking times;
1997 Complete bearing systems for X-ray tubes;
2002 HF spindle with 80 kW at 16,500 to 30,000 rpm and a removal rate of 8 l/min;
2003 Spindle series for internal grinding with speed coefficient of up to 2.8 mill. mm/min
- High-performance grinding spindle with 125 kW at 20,000 rpm
- Small milling spindles for automatic tool change and with encoder-free synchronous motor.
- HF spindle for rotary milling centers with Hirth shaft locking
- Sealed spindle bearing design for maximum speeds and increased service life
2004 HF spindle with HSK 25 and 75,000 rpm, internal coolant supply and encoder;
2005 HF spindle with 120 kW at 13,500 to 30,000 rpm and removal rate of > 10 l/min;
2006 Internal grinding spindle with 250,000 rpm and speed coefficient 4.5 mill. mm/min;
2008 Spindle bearing with a hole diameter of 75 to 120 mm;
2010 Spindle bearing with optimized inner ring geometry for maximum speeds with a hole
diameter of 75 to 120 mm.
GMN Products
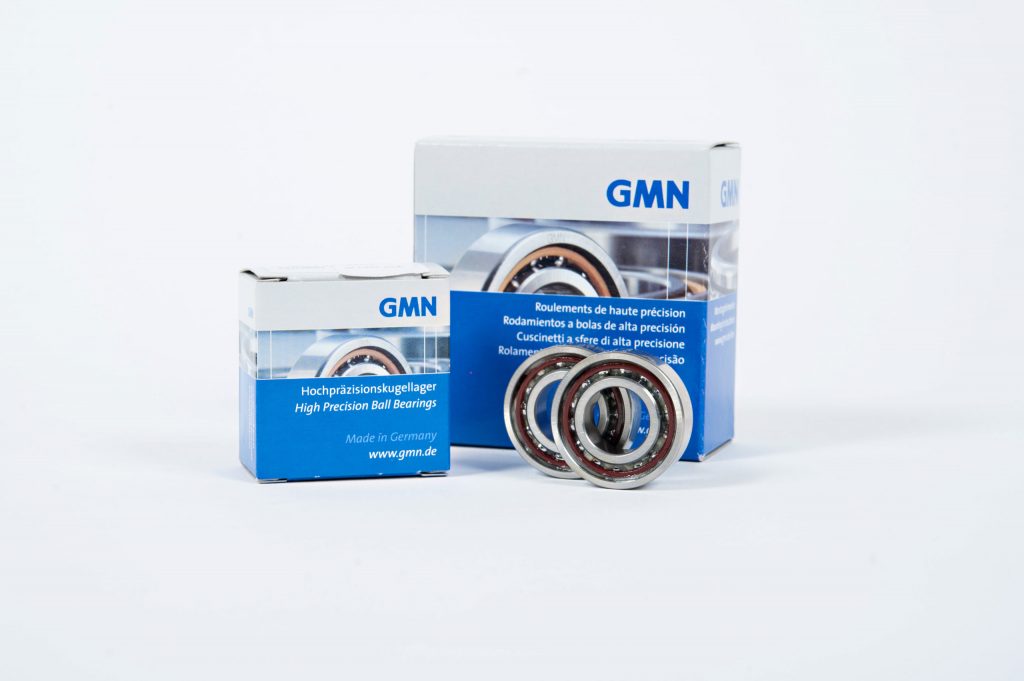
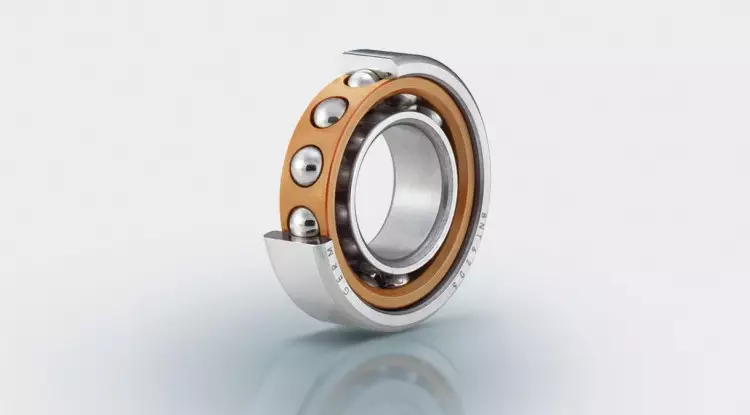
GMN Bearings has an extensive range of precision bearings. The GMN product portfolio includes:
- Angular Contact Ball Bearings
Engineered to accommodate both radial and axial loads, GMN’s angular contact ball bearings excel in high-speed applications and precision machinery.
- Spindle Bearings
GMN spindle bearings are known for their precision and high rotational speeds, GMN spindle bearings play a critical role in various machining applications, like CNC machines and milling centers.
- Deep Groove Ball Bearings
With low-friction attributes and exceptional quality, GMN’s deep groove ball bearings find themselves in a wide array of applications, from household appliances to industrial machinery.
- Radial Ball Bearings
GMN’s radial ball bearings are specially designed to support radial loads, ensuring smooth operation and minimizing friction for maximized machine efficiency.
- Hybrid Bearings
Featuring ceramic balls, GMN’s hybrid bearings elevate performance levels, reduce friction, and extend service life.
- Special Custom Bearings
GMN takes immense pride in its ability to tailor bearings to meet specific customer requirements.