Calculation of external forces
In selecting bearings their main purpose is to transmit forces between machine parts while in rotation. To determine the design, material, and size of the bearing start with calculating the magnitude and direction of the forces acting on the bearing. In determining the correct bearing size and material you start by understanding the magnitude, direction, and possible changes in them. As a rule, the load must never reach a magnitude where permanent deformations developing in the raceways exceed the permissible limit.
Calculating the actual forces can be challenging as the bearing load may be constant or vary. So it is important to determine the varying loads and possible shock loading.
Generally experience with the application and its loads may be one possible method used for load calculation. The other is using the available engineering data such as maximum loads, speeds, and environment.
Calculation of bearing loads
Once you have calculated or estimated all the external forces you must now consider what loads may act on the bearing. First, you must change the system of external forces into forces acting at the respective bearing centers. Bearing centers are the points on the bearing axis through which the load lines of the rolling elements pass. This point is fixed in bearings with a constant contact angle. Several bearing types like double-row radial balls and tapered rollers will have two centers. Double-row bearings will use the geometrical center point as the only center where tapered roller bearings have two apexes towards each other or away from each other.
If bearings are mounted on a shaft having more than two centers the design is indeterminate and so the designer must take into account the reaction forces. You must take into account shaft elasticity and the distance between supports. In cases like this one, the load distribution will depend upon the magnitude of the force. Calculations can be made using statistical laws. Depending on mounting and other circumstances the radial loads exerted on one bearing will transfer internal axial loads on the opposing bearing.
Formulas for calculating thrust loads can be found in bearing manufacturers catalogs.
Experience regarding load variation for different machines and devices has made it possible for Engineers to use empirical coefficients and special calculation methods widely available in standard bearing tables. Manufacturers like INA, Schaeffler, RBC, and SKF support engineers with massive amounts of data for load calculator purposes.
Selection of life and safety factors
Selecting a life factor is in essence the same concept as selecting bearing life. When you determine a desired life requirement then the value of the life factor can be known.
Selection of bearing types
The selection of bearing type is a relatively simple process. First and foremost is to understand the requirements in the bearing application. Then research and understanding the basic characteristics of different types of bearings will lead you in the right direction. Some examples include applications for small high speeds where radial ball bearings would be the first consideration. For large heavy duty applications, the first stop would be roller bearings. Where you might experience misalignment between bearings then self-aligning ball bearings would be chosen. Understand the application needs and then contact your distributor for help in selecting the best bearing not only for type but for economies of manufacturing scale. You don’t want to select a bearing that is hard to find or expensive when a neighboring size might be readily available.
Visit www.pibsales.com for more information and assistance.
At PIB Sales, we provide design assistance that moves the selection process along. Our expertise and comprehensive manufacture catalogs are designed to help you select the ideal bearing. Whether you’re dealing with complex load conditions or specialized performance requirements, PIB Sales can help in making informed decisions.
Visit the Schaeffler Groups website for bearing selection assistant help.
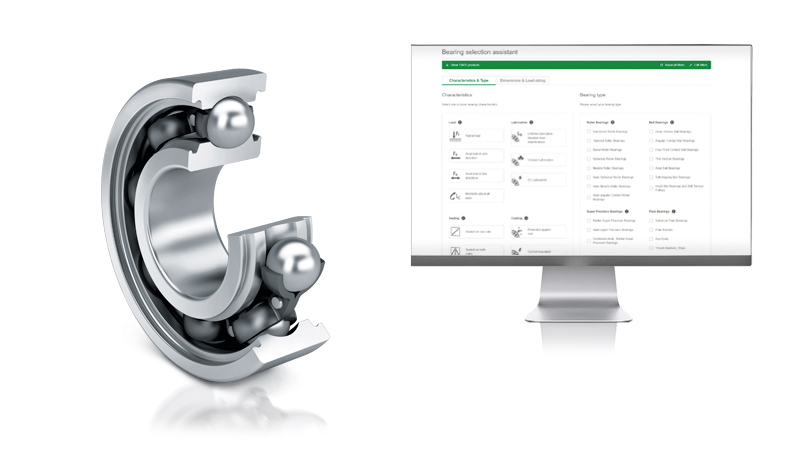
Overview of Bearing Types
PIB offers a diverse selection of bearings, each engineered to meet specific requirements in various industrial applications. Below, we detail each bearing type available in our online store, focusing on their technical aspects, typical applications, and relevant part numbers where applicable.
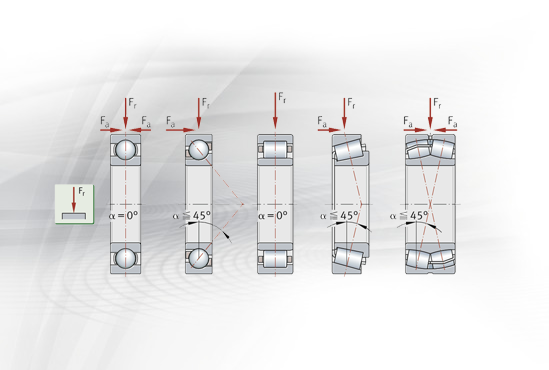
Angular Contact Bearings
Angular contact bearings are designed to handle both radial and axial loads due to their angled contact points. They are available in several configurations:
- Single Row Angular Contact Ball Bearings have a contact angle that allows them to support axial loads in one direction. They are commonly used in high-speed applications such as pumps and compressors. Examples include Schaeffler’s 7206-B, which supports high-speed operations with precision.
- Double Row Angular Contact Ball Bearings provide higher rigidity and can handle axial loads in both directions. This makes them suitable for applications like machine tool spindles and automotive hubs, where balanced load handling is essential. Part numbers such as 3204-BD-XL are typical.
- Four Point Contact Ball Bearings are a type of single-row angular contact bearing designed to handle axial loads in both directions with minimal space requirements. These bearings are ideal for applications where space is constrained but load requirements are high.
Radial Ball Bearings
Radial ball bearings are designed primarily for radial loads and can also handle moderate axial loads. They are versatile, offering low friction and high-speed capabilities, making them suitable for electric motors, gearboxes, and general machinery.
- Miniature Ball Bearings are used in applications requiring compact size and high precision, such as small motors and instrumentation. These bearings offer low friction and quiet operation.
- Thin Section Bearings are engineered for applications where space and weight are critical factors, such as in robotics and aerospace. They maintain load capacity while reducing overall system dimensions, making them ideal for high-precision environments.
Needle Roller Bearings
Needle roller bearings have a high load-carrying capacity relative to their size due to their elongated cylindrical rollers. They are perfect for applications where radial space is limited:
- Needle Roller Bearings and Cage Assemblies provide excellent radial load support in compact designs, making them suitable for gearboxes and automotive transmissions. For instance, INA’s NK35/20-TV is a popular choice.
- Needle Roller Angular Contact Bearings can handle both radial and axial loads in compact spaces, used extensively in automotive and industrial machinery where alignment and load support are crucial.
- Needle Roller Axial Ball Bearings combine radial and axial load capabilities, often used in applications requiring compact solutions for axial and radial force management.
Cylindrical and Tapered Roller Bearings
- Cylindrical Roller Bearings offer high radial load capacity and are ideal for applications with heavy loads and high speeds. They are commonly used in industrial gearboxes and electric motors. Precision cylindrical variants, such as INA’s SL045014-PP, provide superior accuracy and performance in high-speed conditions.
- Tapered Roller Bearings are specifically designed for combined radial and axial loads. Their tapered design allows them to handle heavy loads efficiently, making them suitable for automotive wheel hubs and heavy machinery.
Spherical Bearings
Spherical bearings are known for their ability to handle misalignment between the shaft and housing:
- Spherical Plain Bearings are designed to accommodate oscillatory motion and can handle heavy radial loads along with some axial loads. These bearings are used in applications like hydraulic cylinders and heavy equipment linkages, with common part numbers including INA’s GE 20 DO.
- Spherical Roller Bearings support heavy radial loads and moderate axial loads in both directions, while also accommodating shaft misalignment. These bearings are ideal for use in heavy-duty applications such as conveyors and mining equipment.
Linear Bearings
- Linear Ball Bearings provide low-friction linear movement and are used in precision machineries, such as CNC machines and automation equipment. They offer smooth travel and high accuracy, essential for applications requiring precise positioning.
- Linear Guides & Carriages offer high rigidity and support for linear motion in heavy-load applications. They are used in manufacturing systems where precise and repeatable motion is critical.
Specialized Bearings
- Cam Followers & Yoke Rollers are designed to follow cam paths and support heavy radial loads with moderate speeds. They are commonly used in automated machinery and cam drives, offering robust performance under repetitive motion.
- Drawn Cup Roller Clutch Bearings provide one-way rotational movement, used in indexing and overrunning applications. They are often found in conveyor systems and office automation equipment.
- Rod Ends provides a simple, compact solution for connecting control systems and linkages in pivoting mechanisms. They accommodate misalignment and support oscillatory motion, making them useful in aerospace and industrial applications.
- Thrust Bearings are designed specifically for axial load support, providing high load capacity in a compact form. These bearings are used in applications like automotive gearboxes and marine propulsion systems, where axial loads are predominant.
At PIB Sales, our extensive catalog includes detailed specifications, part numbers, and expert support to help you select the right bearing type for your specific needs. Whether you are dealing with complex load scenarios or specialized motion requirements, our team is ready to assist you in finding the ideal bearing solution. For more information or assistance, please contact us directly.
Bearing Selection Guide
A well-thought-out selection process should take into account various factors such as load conditions, speed, precision, and environmental influences. Here’s a customized bearing selection checklist and detailed guide to help you select the right bearing type for your application.
Bearing selection checklist
Step | Evaluation Criteria | Key Considerations |
1 | Bearing Type | Assess the magnitude, direction, and nature of loads (radial, axial, or combined). Determine if the bearing fits the installation space and meets operational requirements. |
2 | Bearing Arrangement | Evaluate whether single or multiple bearings are needed. Confirm if the arrangement can effectively handle the loads and operational dynamics. |
3 | Dimensions and Service Life | Verify that the bearing’s dimensions align with space constraints and that the service life matches the application’s reliability requirements. |
4 | Speed, Accuracy, Fits, and Clearance | Ensure the bearing supports the required speed, maintains the necessary running accuracy, and has appropriate fits and internal clearances to avoid operational issues. |
5 | Preload and Rigidity | Determine if the bearing preload is appropriate to maintain rigidity under load, reducing deflection and vibration in precision applications. |
6 | Lubrication and Stability | Check if the lubrication system supports the bearing’s operational longevity and if it maintains stability over extended periods. |
7 | Surrounding Components | Analyze the interaction of the bearing with adjacent parts, including seals, housings, and lubricants, to ensure optimal assembly performance. |
8 | Mounting and Maintenance | Consider the ease of mounting and dismounting for maintenance purposes. Select bearings that allow efficient handling, especially in applications requiring frequent inspection. |
How to Select the Right Bearing Type
1. Installation space
The installation space dictates the maximum allowable dimensions for bearings. Start by assessing the shaft diameter and the corresponding bearing bore size. For compact spaces, options like miniature or thin-section bearings may be suitable. Choose a bearing that maximizes load capacity while fitting within the spatial constraints.
2. Load characteristics
Bearings must be selected based on the nature of the loads: radial, axial, or a combination. Radial loads are best handled by deep groove ball bearings or cylindrical roller bearings, which offer high load capacities for radial forces. For axial loads, consider thrust bearings or angular contact ball bearings, which are specifically designed to manage forces parallel to the shaft. Combined loads, which include both radial and axial forces, are well-suited to angular contact bearings or tapered roller bearings, providing balanced support.
3. Rotational speed
Rotational speed directly impacts bearing selection. Bearings are rated by their maximum permissible speeds, influenced by their design and lubrication type. High-speed applications require bearings like angular contact ball bearings or precision cylindrical roller bearings that can minimize friction and heat generation. Always verify that the bearing’s speed rating exceeds the application’s operational speeds to prevent overheating and premature failure.
4. Running accuracy
Running accuracy is critical in applications requiring precise movement, such as spindles in CNC machines or precision instruments. Select bearings with higher tolerance classes (e.g., ISO P4 or P5) to ensure the required accuracy. The choice of running accuracy influences the bearing’s ability to reduce vibration and maintain consistent operation at high speeds.
5. Rigidity and Preload
Applications like machine tools or automotive drives, where precision is paramount, benefit from bearings that can be preloaded to enhance stiffness. Angular contact ball bearings and tapered roller bearings are commonly preloaded to improve rigidity, reduce clearance, and enhance overall performance by controlling elastic deformation.
6. Misalignment capabilities
Misalignment between the shaft and housing can affect bearing performance and lifespan. Self-aligning ball bearings and spherical roller bearings are designed to accommodate angular misalignments, allowing for greater flexibility in assembly and operation. These bearings can tolerate up to a few degrees of misalignment, making them suitable for applications where perfect alignment cannot be maintained.
7. Mounting and maintenance
Consider how often the bearing will need to be mounted or dismounted. Bearings that are easy to install and remove, such as those with separable components (e.g., cylindrical roller bearings), simplify maintenance tasks. For bearings that require frequent inspections, opt for designs that facilitate quick access and reassembly.
8. Environmental factors
Environmental conditions, such as exposure to dust, moisture, or chemicals, necessitate the selection of bearings with appropriate seals and corrosion-resistant materials. For extreme temperatures, bearings made from special alloys or those with solid lubricants may be required to maintain performance and longevity.
For further assistance or specific inquiries, PIB Sales offers a wide range of bearing options to meet your exact needs. Contact us at [email protected] for personalized assistance and access to our complete catalog of high performance bearings.