Humanoid robots demand advanced motion components that deliver precision, strength, and reliability. From joint bearings that handle complex loads to couplings that ensure smooth power transmission, every component choice impacts performance. Selecting the right motion component partner – a supplier/manufacturer who can provide high-quality parts and engineering support – is crucial for robotics engineers. This guide explores key factors in choosing motion components for humanoid robots and highlights how working with an expert partner like Pacific International Bearing (PIB) Sales (an authorized distributor for IKO, Ruland, SKF, Schaeffler Group, and others) can help optimize your design.
Motion Requirements in Humanoid Robotics
Humanoid systems have unique and stringent motion requirements. Engineers must balance multiple factors when selecting components:
- High Load Capacity & Rigidity: Robot joints (like hips, knees, arms) encounter multi-directional loads – axial (thrust), radial, and moment (torque from lever arms). Components must support heavy combined loads with minimal deflection. High rigidity ensures the robot remains stable (critical for balance) and achieves precise, repeatable movements without wobble.
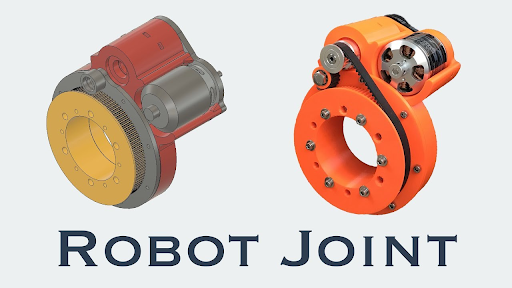
- Precision & Zero Backlash: To mimic human motion (fine manipulation or smooth walking gait), any slack or play in the joints is unacceptable. Zero-backlash components (both bearings and couplings) are essential so that commanded movements translate exactly into robotic motion. This often entails selecting preloaded bearings with very tight clearances and zero-backlash couplings (e.g., beam, bellows, disc, jaw types) pibsales.com.
- Compact, Lightweight Design: Humanoids are size- and weight-constrained components that should provide high performance in a small envelope. For example, a single crossed roller bearing can replace a pair of traditional bearings, saving space and weight in a joint. Similarly, lightweight aluminum couplings (with stainless steel only where needed) help minimize inertia on servo axes. Lower component mass improves battery life and dynamic response.
- Misalignment & Flexibility: Perfect alignment is difficult to achieve in complex assemblies. Flexible couplings must accommodate misalignment (angular, parallel, axial) between motors and driven joints. They protect motor and bearing life by relieving stress while accurately transmitting torque. The amount of misalignment a coupling can handle (and whether it also dampens shocks/vibrations) varies by design (discussed in the coupling section).
- Durability & Low Maintenance: Humanoids often perform repetitive actions thousands of times. Components should be long-life and maintenance-free where possible. For instance, bearings with integrated lubrication (sealed or with IKO’s C-Lube technology) and couplings that operate without wear debris or periodic adjustment keep the robot running reliably. Selecting corrosion-resistant materials or special coatings is also important if the robot will operate in harsh environments (dust, moisture, extreme temperatures).
By considering these factors, engineers can narrow down which bearing types, coupling styles, and other motion components will best meet their robot’s needs. Next, we’ll dive into specific solutions – and their part numbers, specs, and advantages – for humanoid joint design.
Precision Bearing Solutions for Robot Joints
Bearings are at the heart of every rotary joint in a humanoid robot. They must support the robot’s weight and motions without excess play. Traditional robot designs often used pairs of thin-section ball bearings to support joint loads, but humanoids benefit from more advanced solutions like crossed roller bearings (CRBs).
Crossed Roller Bearings for High-Load Joints: Crossed roller bearings consist of cylindrical rollers arranged in an X pattern (each roller is at 90° to the next). This allows one compact bearing to carry loads in all directions simultaneously (radial, axial in both directions, and moment). The result is exceptional stability and stiffness in a small package – exactly what high-torque humanoid joints need. For example, in a robot’s hip or knee, a single CRB handles the complex forces as the leg swings and bears weight, whereas two conventional bearings would be required in a back-to-back arrangement. Using one integrated bearing saves space, weight, and often cost.
Key benefits of IKO crossed roller bearings:
- High Rigidity & Accuracy: Because the rollers make line contact with the raceways (unlike point contact in ball bearings), deformation under load is minimal. This gives CRBs very high stiffness and minimal joint deflection, which in turn ensures precise, smooth motion even under heavy loads. In practice, a full-size humanoid may use 14–20 crossed roller bearings in its various joints (shoulders, elbows, hips, etc.) to achieve human-like articulation.
- Slim Profile: Advanced CRB designs, like the IKO CRBH series (High-Rigidity Type Crossed Roller Bearings), feature a low-profile cross-section ideal for robotics. For instance, IKO CRBH208AUU is a high-rigidity crossed roller bearing with a 20 mm bore, 36 mm outer diameter, and only 8 mm width – perfect for a compact wrist or elbow joint. Despite its small size, it has a dynamic load rating of around 2,910 N (static ~2,430 N), handling multi-axis loads in tight spaces. Larger sizes in the CRBH series handle even higher loads for major joints like hips or shoulders. For example, a CRBH7013AUU (70 mm bore, 100 mm OD, 13 mm width) can support ~20,100 N dynamic and ~27,700 N static load, providing the strength and rigidity needed for a humanoid hip. (Note: “UU” in IKO part numbers indicates seals on both sides for lifetime lubrication.)
- Preload and Clearance Options: To achieve zero backlash in a robot joint, bearings can be ordered with specific internal clearances or preloads. A light preload (negative clearance) eliminates even the slightest play. For crossed rollers, manufacturers offer clearance grades like C1 or even slight preload classes (often denoted “T1”) to tighten the bearing. Adding a light preload or using a C1 clearance bearing can eliminate joint backlash and allow ultra-smooth motion. Be sure to work with your supplier to choose the appropriate clearance/preload – too much preload increases friction, whereas too much clearance introduces play. The goal is a minimal clearance or slight preload for precision in robotics.
Real-World Bearing Specs: For a sense of scale, a medium-sized crossed roller like IKO CRBH4010AUU (40 mm bore × 65 mm OD × 10 mm width) is rated for ~8,610 N dynamic and 10,600 N static capacity. A larger CRBH11020A (110 mm bore × 160 mm OD × 20 mm width, open type) can handle roughly 52,400 N dynamic load, despite its thin profile of 20 mm. These high capacities are paired with accuracy grades (e.g., P5/P6 precision) suitable for smooth, backlash-free joint rotation. Such bearings typically allow maximum rotational speeds on the order of a few hundred to 1,000+ RPM (more than sufficient for humanoid limb joints). Always verify the load ratings (dynamic, static) and life calculations against your robot’s worst-case forces to ensure a suitable safety margin.
Mounting and Customization: It’s not just the bearing itself, but how you integrate it. Leading suppliers like IKO can customize crossed roller bearings with mounting flanges, special bolt hole patterns, or integrated housings to simplify assembly. This is valuable in humanoid robots where joint components must fit in tight, complex assemblies. Proper mounting (typically press-fitting the bearing’s inner or outer ring per the spec and using recommended housing tolerances) is critical to performance. A good partner will provide guidance on fits and even deliver pre-assembled bearing units if needed to ensure alignment.
Linear Guides for Sliding Motion
Not all humanoid movements are rotary – some are linear (e.g., telescoping limbs, sliding joints in fingers or a robot’s neck). Miniature linear guides are the component of choice for such motions. These consist of a rail and carriage with recirculating balls or rollers that allow precise sliding movement with low friction. In a robotic hand, for instance, each finger joint might use a tiny linear guide to achieve extension and contraction, much like human finger bones sliding via tendons.
IKO Linear Way Series: IKO’s miniature linear guides (e.g., Linear Way L and ML series) are well-suited for humanoid applications. The LWL series in particular offers ultra-compact sizes. One example is the IKO LWL9B – a miniature carriage on a rail only 9 mm wide.
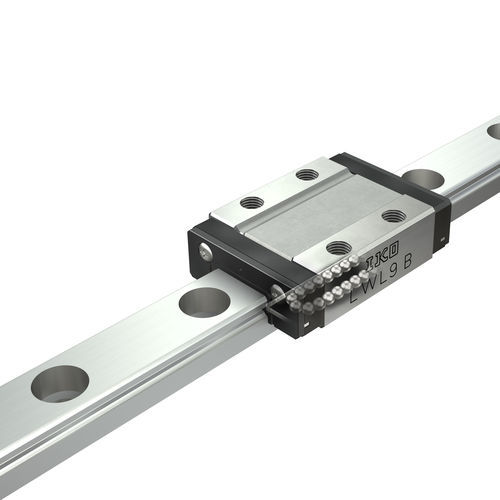
Despite its size, the LWL9B uses two rows of steel balls in four-point contact with the rail, giving it surprising load capacity and stiffness for delicate motions. The dynamic load rating of an LWL9B block is on the order of 1,810 N (with a static capacity of ~2,760 N), which is plenty for small gripper mechanisms and finger assemblies. For slightly larger linear axes (say an extending arm segment or torso lift), bigger mini-guides like LWL12B or LWL15B can be used – e.g., an LWL15B can handle ~4,980 N dynamic load while still only 15 mm rail width. These guides often come with built-in C-Lube (capillary lubrication) that makes them maintenance-free for thousands of cycles, an important feature for reducing upkeep in robots.
Engineers can choose standard block lengths or long blocks for greater stability. In critical linear axes (perhaps a sliding neck joint allowing the head to tilt), using two carriages in parallel on one rail can further increase moment capacity and rigidity. Thanks to their modular nature, linear guides are easy to integrate – they bolt to the structure and provide instant, precise linear motion. Just ensure to select a guide size that comfortably supports the applied loads (including any moment loads if one carriage is used) and consider adding end stops or buffers to prevent overtravel in a humanoid’s moving limbs.
By leveraging both advanced rotary bearings and linear guides from a partner like IKO, humanoid robot designers can achieve smooth rotation and translation in every degree of freedom. Next, we look at transmitting power into these joints, which is where shaft couplings come in.
Flexible Couplings for Robotic Actuators
In humanoid robots, servo motors or gearboxes drive the joints, and shaft couplings connect these drives to the joint mechanisms. The right coupling ensures torque is transmitted with high fidelity (no backlash) while cushioning the system against misalignment and shock. Ruland Manufacturing is a premier supplier of couplings, and Pacific International Bearing Sales Inc. (PIB) offers the full range of Ruland servo couplings to meet different design needs. Below, we compare common coupling types and their characteristics for robotics:
A poorly chosen coupling can introduce positioning errors, wear out bearings, or even fail under dynamic loads. Key factors include:
- The coupling must handle the peak torque of the joint without twisting (wind-up). High torsional stiffness is critical for accurate servo response.
- No assembly is perfectly aligned – couplings should compensate for angular misalignment (shafts at a slight angle), parallel offset, and axial motion (shaft end-play or thermal expansion). Different coupling designs specialize in different misalignment modes.
- Most modern servo couplings are designed to be zero-backlash, so they don’t introduce play when reversing direction. Some types (those with plastic or elastomer elements) can also damp vibrations and shocks, which helps protect gearboxes and improve control smoothness.
- Coupling size and material affect the inertia seen by the motor. Compact, lightweight couplings (often aluminum-bodied) are preferred to keep system inertia low for better dynamic performance.
Let’s examine several coupling options available and how they stack up:
Coupling Comparison Chart: The table below summarizes major servo coupling types used in robotics and their performance features:
Coupling Type | Torsional Stiffness | Misalignment Tolerance | Notable Features & Applications |
Rigid Coupling (solid clamp/spacer) | Very High (no flex, one solid piece) | None – shafts must be perfectly aligned (no angular or parallel offset allowed) | Zero backlash and highest precision, but rigid couplings transmit all forces – use only if you have exact alignment and no need for relief. Rare in humanoids, except maybe for test jigs or very short aligned connections. |
Beam Coupling (Helical cut) | Moderate (single-beam = lower, multi-beam = higher) | High angular & axial, moderate parallel (especially multi-beam designs) | One-piece aluminum or stainless coupling with spiral cuts. Flexible and zero-backlash. Single-beam styles suit low-torque encoders or sensors; multi-beam (e.g., Ruland P-Series) handle higher torque with improved parallel misalignment. |
Bellows Coupling | Very High (highest of flex types) | Low – only small misalignments (a few arc-min angular, <0.1 mm parallel) | Metallic stainless steel bellows connect two hubs. Delivers zero backlash and extremely high torsional rigidity for precision positioning. Requires near-perfect alignment and offers no damping (transmits shock). Typically used in high-precision axes (e.g., robot joint driving a gear reduction or precision cam) where accuracy outweighs misalignment needs. Balanced for high RPM (often 10,000+). Example: A Ruland MBC41-16-16-A bellows coupling (41 mm OD, 16 mm bores) is rated for up to 10,000 RPM and provides rock-solid torque transmission. |
Disc Coupling (Single or Double Disc) | Very High (just slightly below bellows) | Moderate misalignment if double-disc (single-disc: small angular only; double-disc: adds parallel tolerance) | Consists of two hubs connected by one or two thin spring steel discs. Zero-backlash. A double-disc coupling (spacer with two disc packs) handles parallel offset and angular misalignment while remaining torsionally stiff. Good for high-speed, high-precision applications that need some flexibility. All-metal design means no damping, but also no wear parts. |
Jaw Coupling (Curved Jaw + Spider) | Moderate (depends on spider hardness) | Moderate – about 1° angular, a small parallel offset | Two aluminum or steel hubs with interlocking jaws and an elastomer spider insert. Zero-backlash in operation (spider is preloaded) and fail-safe – if the spider fails, jaws still interlock to transmit torque. Offers shock absorption and vibration damping (especially with softer spiders). Ideal for servo applications with rapid start/stop or vibrations. Misalignment capability is lower than Oldham/beam, but enough for minor shaft offsets. |
Oldham Coupling | Moderate | High parallel misalignment (up to 5–10% of coupling diameter), moderate angular, and some axial | Three-piece design: two hubs with slots + a middle disk (usually acetal or nylon) that transmits torque in a sliding manner. Zero-backlash (the disk is under slight compression) and excellent at handling parallel misalignment. The plastic disk provides electrical isolation and absorbs shocks, protecting the system. Easy to replace the insert disk for maintenance. Oldhams have lower torsional stiffness than beam/disc/bellows, but their misalignment capacity is unmatched, making them useful in robots where alignment of motors to mechanisms is tricky. |
Controlflex Coupling | Low–Moderate | Very high – excellent for all types (angular, parallel, axial) with minimal bearing load | A special coupling using a “frog-leg” shaped flexible plastic element between two metal hubs. Zero backlash and extremely gentle on bearings (it introduces very little reaction force even under misalignment). Great for delicate systems (small motors, encoders) where protecting components is key. |
Table: Comparison of servo coupling types for robotics. Each coupling type offers zero backlash (when properly installed) and has specific strengths. Bellows and disc couplings deliver the highest precision but require careful alignment. Beam couplings are versatile for moderate needs. Jaw and Oldham couplings introduce plastic elements that allow more misalignment and shock damping – useful for robots dealing with shocks or larger assembly tolerances. Controlflex is a niche solution for small, misalignment-prone connections. In practice, engineers often narrow choices by required torque and misalignment first, then consider factors like stiffness and maintenance.
Coupling selection tips:
Always check the coupling’s torque rating (including service factor for repetitive motion) and misalignment limits against your application. For example, if a wrist motor in a humanoid needs to handle 3 Nm of torque and has a slight misalignment to the forearm joint, a multi-beam or jaw coupling might be ideal. If a precise knee joint drive requires 0.1° accuracy, a bellows or disc coupling is more appropriate. Also consider environmental factors – e.g., if the robot operates near sensitive electronics, a coupling that provides electrical isolation (Oldham, Controlflex, jaw with non-conductive spider) can be beneficial. Ruland provides part number charts to mix and match hub bores (you can often have one side metric, one side inch, especially with two-piece couplings like jaw or Oldham) to fit different shaft sizes – this flexibility simplifies integration.
Finally, installation and maintenance: Most Ruland couplings are clamp-style hubs for easy installation and concentricity. They are generally maintenance-free (no lubrication needed). For jaw and Oldham types, keep an eye on the spider or disk insert over time – they can wear and may need replacement after prolonged use, but swapping them is quick and inexpensive. Carry a few spare inserts for critical robots to minimize downtime.
With the right coupling selected, your humanoid’s motors will deliver smooth, accurate power to its joints. But choosing the best components is only half the battle – the other half is working with a supplier partner who can support your needs. In the next section, we discuss the importance of collaboration with a motion component partner in achieving an optimal design.
Partnering for Successful Integration
Selecting high-performance components is easier when you have a trusted motion component partner to guide you. The complexities of humanoid robotics – tight design envelopes, custom requirements, and high performance criteria – often call for collaboration with component manufacturers early in the design process. Here’s what the right partner can do for you:
- Expert guidance & custom design: A knowledgeable supplier (like IKO for bearings or Ruland for couplings) will assess your needs and educate your team on options, helping navigate trade-offs. They can propose customizations if off-the-shelf parts don’t perfectly fit. For example, IKO’s engineers might suggest a modified crossed roller bearing with a flange or a special housing to drop into your robot’s joint, eliminating extra brackets. They might also recommend a slight preload or a different clearance class to hit your stiffness target. Ruland can provide couplings with custom bore sizes, keyways, or balanced designs for high speed. This level of tailoring ensures the components integrate seamlessly into your design rather than forcing compromises.
- Early collaboration = fewer redesigns: Engaging with the component partner during the design phase can prevent costly changes later. They’ll help you consider things like proper fits/tolerances, mounting configurations, and even how to test the components. If your humanoid has unique motions (say a waist that rotates almost 360° or a leg that extends significantly), your partner can verify that the selected bearings and couplings can handle those use-cases (maybe suggesting a higher capacity model or different coupling type if needed). As IKO notes, they will even test and validate custom parts to ensure they perform as expected in the field. This reduces risk and boosts reliability when the robot is built.
- Quality and reliability focus: Working with established brands ensures you get proven, high-quality components. IKO, for instance, manufactures to strict quality standards (ISO certified) and employs heat-treated alloy steels (often 52100 bearing steel) or stainless steel for corrosion resistance. Their bearings can be coated (black chrome, etc.) for harsh conditions. Such options might not be obvious without partner input. Similarly, Ruland’s couplings are precision-machined and tested; their rigid quality control means you receive consistent zero-backlash performance. This reliability is critical – humanoid robots are expensive, and you don’t want to risk a joint failing due to an inferior bearing or a coupling cracking. A good partner supplies genuine parts with full traceability and support.
- Lifecycle support & maintenance: Motion component partners can advise on lubrication intervals (if any), provide spare parts quickly, and even help troubleshoot if a component isn’t performing ideally. For example, if a joint is running hotter than expected, your bearing supplier might suggest a different grease or a switch to a sealed bearing with a low-friction seal. In many cases, partners offer products that minimize maintenance – e.g., IKO’s C-Lube linear guides that self-lubricate for 20,000 km of travel, or sealed-for-life bearings that don’t require relubrication. Using these options on a humanoid reduces the need to tear down the robot for servicing.
In short, PIB, as your motion component partner, acts as an extension of your engineering team. They bring deep experience from across the robotics industry and can help you avoid pitfalls while optimizing performance. Pacific International Bearing Sales (PIB) has positioned itself as exactly this kind of partner – as an authorized distributor of IKO bearings and Ruland couplings, PIB offers both products and in-house expertise to assist robotics engineers at every step. We’ve helped clients select the perfect cross roller bearing for a new humanoid ankle design, choose between a bellows vs. disc coupling for a high-speed arm, and configure linear slides for compact gripper mechanisms – all through a combination of technical know-how and a broad inventory of precision components.
FAQ
Q: Why use crossed roller bearings instead of standard ball bearings in humanoid joints?
A: Crossed roller bearings (CRBs) offer a unique combination of high load capacity, rigidity, and compactness that is ideal for humanoid robots. A single CRB can support loads in all directions (radial, axial, and moment) simultaneously, which typically would require two angular contact ball bearings in a “back-to-back” pair. By using one CRB per joint, you save space and weight – crucial in a humanoid’s design. Additionally, the line-contact rollers in a CRB result in minimal deflection under load, meaning the joint will not wobble or lose accuracy when the robot lifts something heavy. In short, CRBs provide greater stiffness and precision than standard ball bearings, in a smaller package. Many humanoid designers have found that upgrading a joint to a crossed roller bearing (like the IKO CRBH series) immediately improves the robot’s stability and motion accuracy.
Q: How can I eliminate backlash in a robotic joint?
A: Backlash (mechanical play) can be virtually eliminated by careful component selection and setup. First, choose zero-backlash components – for bearings, this means using preloaded or tight-clearance bearings (e.g., selecting a C1 clearance crossed roller, or adding shims to induce a light preload). Crossed roller bearings are often available in slight preload classes specifically to achieve zero clearance. Second, use zero-backlash couplings between motors and joints – all the Ruland flexible couplings (beam, bellows, disc, jaw, Oldham, etc.) are designed for zero-backlash torque transmission. For example, Ruland jaw couplings preload their spider element to remove play, and Oldham couplings use a slight press-fit disk. Finally, ensure your assembly practices are precise: any loose fits or keyways can introduce tiny amounts of play. By using the right components and proper installation, you can achieve essentially backlash-free joints, which is essential for smooth, precise humanoid movements.
Q: Which type of coupling is best for a high-precision robot axis versus a high-misalignment axis?
A: If you need utmost precision and torsional rigidity (for instance, a high-accuracy robot arm joint or a torso rotation axis with a large moment of inertia), a bellows coupling is often the top choice due to its zero-backlash and very high stiffness. Bellows couplings will keep positioning error to an absolute minimum – but they require that your shafts are very well aligned (within a few thousandths of an inch) because they don’t tolerate much misalignment. On the other hand, for an axis where misalignment is significant or unavoidable – perhaps a secondary arm joint or a drive where mounting isn’t perfectly concentric – an Oldham coupling or Controlflex coupling is better. Oldham couplings can handle large parallel misalignments (up to 10% of their diameter) while remaining zero-backlash. Controlflex couplings can accommodate substantial misalignment in all directions with very low reaction forces, making them great for protecting delicate components. They trade off some torsional rigidity, so they’re best for light or feedback-type applications. In summary: use rigid or bellows couplings for highest precision when alignment is assured; use Oldham or Controlflex when misalignment is a bigger concern than absolute stiffness; and disc or jaw couplings fill the middle ground (offering high precision with a bit more misalignment capacity and shock absorption, respectively).
Q: What maintenance do these motion components require in a robot?
A: One advantage of modern motion components is that many are maintenance-free or low-maintenance. Quality bearings for robotics often come pre-lubricated and sealed – for example, IKO crossed roller bearings with suffix “UU” have built-in seals and grease that typically last the life of the robot under normal conditions. Linear guides in the miniature range can include self-lubricating technology (IKO’s C-Lube) that continuously applies lubricant, meaning you don’t need to re-grease periodically. For couplings, most designs (beam, bellows, disc, rigid) have no sliding or wear parts and thus require no maintenance at all – just install them and they’ll run without attention. The only coupling types that might need maintenance are those with polymer inserts (jaw and Oldham couplings). Over years of heavy use, the elastomer spider in a jaw coupling or the center disk in an Oldham coupling can wear or develop slight backlash. The good news is that checking and replacing these inserts is quick and easy, and they are inexpensive spare parts. Many robot builders will inspect the Oldham disks or jaw spiders during scheduled maintenance (e.g., every 6–12 months of operation) and replace them if signs of wear or fatigue are observed. By following manufacturer guidelines and scheduling inspections of wear parts, you can ensure your humanoid robot’s motion components stay in optimal condition for a long service life.
Q: Can PIB help if I need a very specific or custom motion component?
A: Yes – one of the key benefits of working with PIB Sales is our ability to coordinate custom solutions. As a distributor for manufacturers like IKO and Ruland, we can leverage their engineering teams to develop special components for your needs. If you require a non-standard bearing size, a modified mounting flange, a particular coating for a corrosive environment, or an unusual coupling configuration, we will work with you to get it made. Often, the process involves discussing your requirements with our engineers, who then consult with the factory design teams. Because we’ve been in the bearing industry for decades, PIB has the experience to know what modifications are feasible and how to implement them. We have delivered solutions ranging from custom preloaded crossed roller bearings for surgical robots to custom coupling hubs that mate different shaft sizes. Even if it’s not a catalogue item, chances are we can help source the exact motion component you need.
Conclusion
Pacific International Bearing Sales Inc. (PIB) makes it easy to source the motion components you need for your robotics project.
Online ordering: Many standard bearings and couplings can be ordered directly through our website. Visit the PIB Sales online catalog to browse products – you can search by part number or filter by specifications. For example, if you know the Ruland coupling series or IKO bearing model you need, our site allows quick selection and adds it to your cart. Ruland servo couplings are available for online purchase, and you’ll find IKO linear guides and bearings listed with detailed specs. This is ideal for straightforward orders and fast processing.
Prefer to talk to a human or have a more complex request? Give Pacific International Bearing Inc. a call at 800-228-8895. Our experienced sales staff is here to discuss your project requirements, provide guidance on component selection, and take your order over the phone. We also provide quotations for large volumes or special-order items.
Please visit [email protected] .