Pacific International Bearing Sales Inc. provides services for coating bearings used in Industrial and commercial applications. Coatings for bearings are used as surface treatments so bearings can operate in demanding environments generally improving their performance and life.
Bearing coatings provide the following benefits:
• corrosion resistance;
• wear resistance;
• surface hardness modification;
• surface roughness change;
• increased or reduced friction;
• sliding and emergency running properties;
• increased or reduced lubricant or fluid adhesion (wetting properties);
• electrical insulation;
• chemical shielding;
• aesthetic requirements;
• hydrogen barrier.
In applications requiring specialty coatings, there are a number of different methods for producing galvanic layers, chemically produced layers, thermally sprayed layers, kinetically sprayed layers, melted layers, vacuum deposited layers, dip coat layers, and paint layers.
All of these require very different manufacturing approaches. Each type of coating requires special handling and application knowledge when applied to bearing surfaces. It is a good practice to contact your local distributor of bearings. Pacific International Bearing Sales Inc. can assist in understanding your application needs and making recommendations. Please contact us at [email protected].
Why Use Bearing Coatings?
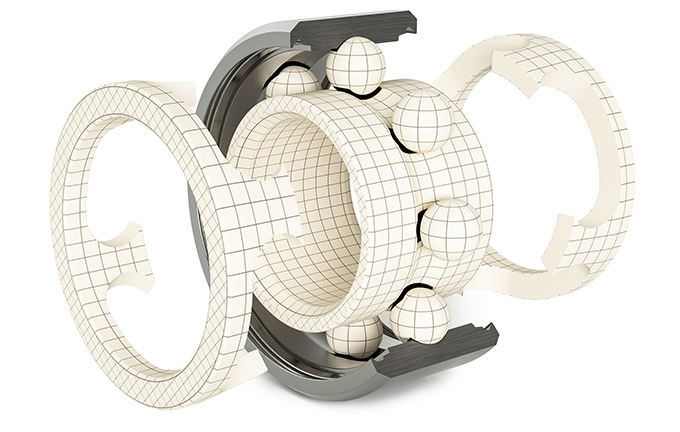
Ball and Roller bearings rely on lubrication to minimize friction and wear. But as I mentioned earlier many conditions require bearings to be protected so they can operate efficiently:
- Reduced Friction: Certain coatings, like those with polytetrafluoroethylene (PTFE) or molybdenum disulfide (MoS2), have inherently low friction coefficients. This translates to smoother operation and less energy loss.
- Enhanced Wear Resistance: Coatings can be much harder than the underlying bearing material. This provides a sacrificial layer, protecting the bearing itself from wear during demanding operations.
- Improved Load Capacity: Some coatings, like those with ceramic materials, boast superior hardness and load-bearing capabilities. This allows bearings to handle higher loads without failure.
- Reduced Corrosion: Corrosion can significantly shorten bearing life. Specific coatings can act as a barrier, protecting the bearing from aggressive environments or contaminants.
- Accommodate Boundary Lubrication: In situations with minimal lubrication, coatings can help prevent seizure by providing a low-friction interface. This is particularly beneficial during cold starts or under heavy loads.
As I have explained, coatings extend bearing life, improve efficiency, and enhance reliability in various applications. It is important to understand the variety of options and types of coatings available before making a decision.
Types and Applications
- Polymer Coatings (PTFE, Polyimide): These are popular choices for their low friction properties and excellent wear resistance during mixed lubrication regimes. Common applications include internal combustion engines, compressors, and pumps.
- Metallic Coatings (Chromium, Chromium Nitride): These coatings offer superior hardness and wear resistance, making them ideal for high-load applications like gearboxes and rolling mills. They can also improve corrosion resistance.
- Ceramic Coatings (Titanium Nitride, Silicon Nitride): These boast exceptional hardness, wear resistance, and high-temperature capabilities. They are often used in demanding environments like racing engines, aerospace components, and food processing equipment.
- Diamond-Like Carbon (DLC): This advanced coating offers a unique combination of low friction, high hardness, and excellent wear resistance. It finds application in demanding environments like automotive transmissions and high-performance machinery.
The choice of coating depends on operating conditions and required performance improvements. Factors like load, lubrication type, operating temperature, and desired wear resistance all play a role in selecting the optimal coating. It is important to understand the application so as to select the most beneficial coating.
Application Methods
Several methods are used to apply these specialized layers to bearings:
- Physical Vapor Deposition (PVD): This technique bombards the bearing surface with high-energy particles, dislodging material from a target that condenses as a thin film on the bearing. Popular for metallic and ceramic coatings.
- Chemical Vapor Deposition (CVD): Here, a gaseous precursor reacts on the bearing surface to form the desired coating. This method is suitable for complex coatings like diamond-like carbon (DLC).
- Electroplating: This technique uses an electric current to deposit a metallic coating from an electrolyte solution onto the bearing surface. Often used for chromium plating.
- Spray Coating: This method involves spraying a liquid or suspension containing the coating material onto the bearing surface, followed by a curing process. Primarily used for polymer coatings.
Each method offers its own advantages and limitations, and the choice depends on factors like the coating material, desired thickness, and cost considerations.
Other Considerations for Using Bearing Coatings
- Multilayer Coatings: By combining different coating materials in a layered structure, engineers can achieve a synergistic effect, optimizing various performance aspects.
- Nanostructured Coatings: Coatings with features on the nanoscale can offer exceptional properties like improved wear resistance and reduced friction.
- Environmentally Friendly Coatings: As environmental concerns grow, there’s a push for developing non-toxic and easily recyclable coating materials.
- Tribological Coatings: These coatings are specifically designed to optimize the tribological properties (friction, wear, and lubrication) of the bearing surface.
Technology improvements continue to assist the bearing industry for better performance and reliability in bearing coatings.
Summary
Bearing coatings represent a powerful tool for extending bearing life, improving efficiency, and boosting reliability. Please contact Pacific International Bearing Sales Inc for further information and please visit our website.
For more information on coatings here is a good catalog pdf from SKF.