Cross roller bearings are specialized rotary bearings designed for high precision and rigidity. Unlike conventional bearings, they use cylindrical rollers arranged orthogonally (at 90°) in a single, compact unit so that one bearing can carry loads in all directions (radial, axial, and moment). This unique design eliminates the need for separate radial and thrust bearings, making cross roller bearings indispensable in precision engineering applications where accuracy, stiffness, and space savings are critical. TPI Bearings (Tung Pei Industrial Co.) is a leading manufacturer of precision bearings founded in Taiwan in 1966. In 1967, TPI entered a joint venture with Japan’s NTN, and today it is a world-class bearing producer with factories in Taiwan, China, and Indonesia. TPI’s product range includes deep groove, angular contact, and cross roller bearings, all recognized for their quality across industries such as machine tools, robotics, and medical equipment. PIB Sales offers the broadest inventory of TPI products. Engineers and procurement managers can leverage PIB’s knowledgeable support and stock availability to find the optimal TPI cross roller bearing for their needs. Please watch the video to learn more about the TPI Bearing Company.
What Are Cross Roller Bearings?
Cross roller bearings consist of an inner ring, an outer ring, and multiple cylindrical rollers. The rollers are placed in a crisscross arrangement, with each roller oriented perpendicular to the next, rolling in V-shaped raceway grooves ground into the rings. This configuration (see Figure 1 below) provides line contact between rollers and raceways, greatly reducing elastic deformation under load. As a result, a single cross roller bearing can sustain heavy loads from any direction with minimal deflection. The inner and outer rings include precision-machined raceway grooves at a 90° angle, allowing the orthogonal rollers to share loads efficiently.
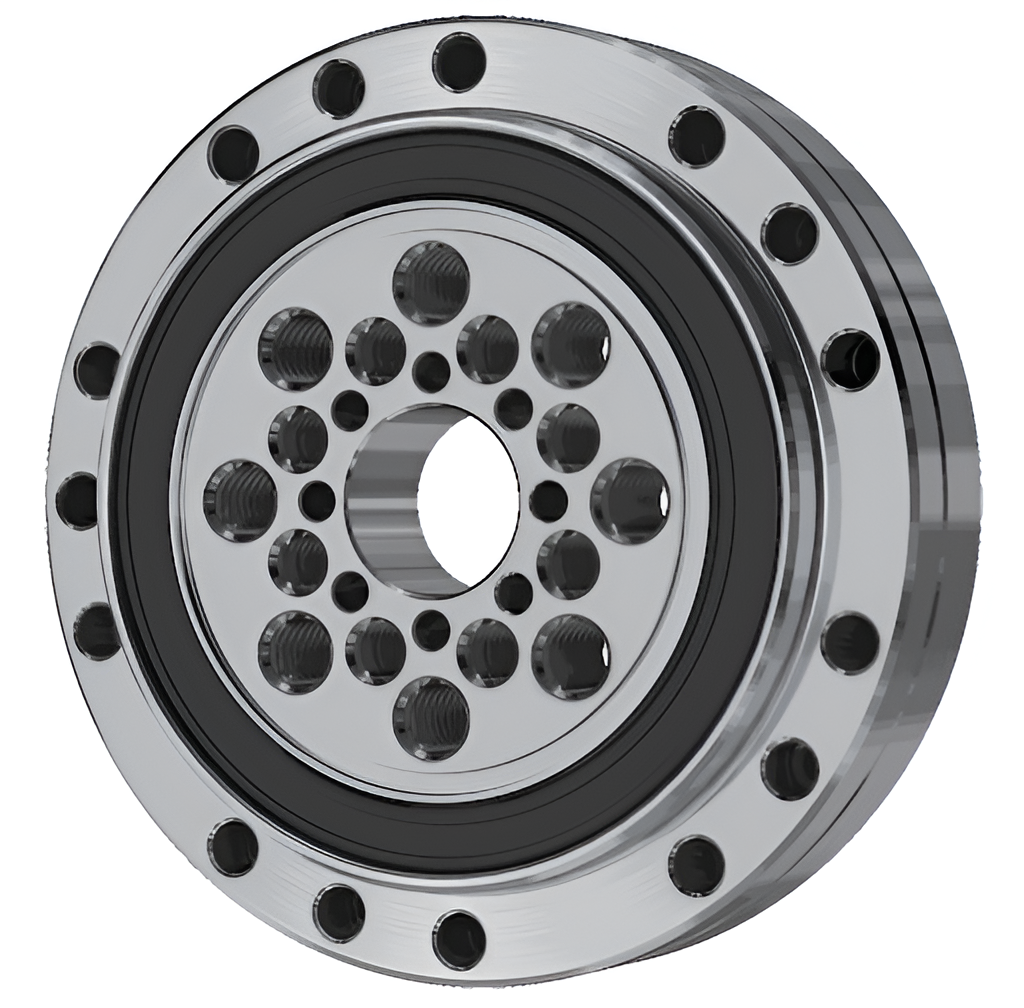
Structurally, most cross roller bearings have the inner or outer ring split into two halves. In TPI’s design for strainwave (harmonic) drives, the outer ring is split into two pieces that are clamped by bolts, while the inner ring is one solid piece. Splitting one ring facilitates insertion of the maximum number of rollers (“full complement”) for higher load capacity. It also means the assembled bearing will not come apart during handling or operation – the two outer ring halves are securely fixed together to capture the rollers. Many cross roller bearings, including TPIs, come preloaded or with minimal clearance by design, so that all rollers contact the raceways without play. Additionally, built-in seals are commonly provided on both sides (denoted by “UU” in part numbers) to retain lubricant and prevent contamination. Overall, the cross roller bearing’s compact and robust structure yields a component with high rigidity, high rotational accuracy, and the ability to carry combined loads in a single, space-saving unit.
Applications of TPI Cross Roller Bearings
Thanks to their unique capabilities, TPI cross roller bearings are used in a wide range of demanding applications. They are especially popular in robotics and automation. For example, industrial robot arms use cross roller bearings in the articulating joints and strain wave (harmonic) reducers of the robot, where high stiffness and compact size are needed for precise motion. Cross roller bearings are also found in the swiveling tables of CNC machining centers and precision rotary indexers, providing smooth, accurate rotation under heavy cutting loads. In the semiconductor and medical industries, the slim-profile cross roller bearings enable high-precision rotation in confined spaces – common uses include medical imaging devices (CT/MRI gantries, robotic surgical tables) and measurement instruments, where zero backlash and high accuracy are paramount.
Another key application area is rotary tables and positioning stages. Cross roller bearings (often of the high-rigidity type) serve as the core of many precision rotary tables, delivering excellent rotational accuracy and load capacity for metrology or assembly systems. Even under complex loads, the crossed rollers maintain stable movement, which is crucial for these devices. More broadly, any machine that requires high-precision, wobble-free rotation – from radar antenna mounts to telescope gimbals – can benefit from a cross roller bearing. In summary, TPI cross roller bearings are found in:
- Industrial robots and cobots. Robotic joint actuators and harmonic drive outputs (for both industrial and collaborative robots)
- Machine tools. Precision rotary tables, indexing heads, and swivel axes of machining centers and grinding machines.
- Medical devices. Imaging equipment, surgical robot joints, and other mechanisms requiring compact, high-accuracy rotation.
- Automation & measuring equipment. Rotary stages are used in coordinate measuring machines (CMMs), semiconductor wafer rotation stages, and laser scanning devices.
By using one cross roller bearing in place of multiple conventional bearings, designers can achieve a more compact and rigid mechanism, a decisive advantage in these advanced applications.
TPI Cross Roller Bearing Series Overview
TPI offers a range of cross roller bearing series to meet different design requirements. The main series includes CRB, CRBC, CRBH, CRBS (often used in machine tools, automation, and general industry,) and the RA family of bearings (developed for robot strainwave drives, with variants like RA-C, RA-G, RA-GC). Each series has unique features in terms of ring configuration, thickness, and integration options. The table below summarizes the key characteristics of these series:
Table 1 – Overview of TPI Cross Roller Bearing Series.
Series | Construction (ring type) | Preload options |
Both inner and outer rings are one-piece (integral). | Outer ring split (2-piece); inner ring solid. | C0 (preload), C1, C2 clearances available. |
CRBC | Inner ring split (2-piece); outer ring solid. | C0, C1, C2 available (often set with slight preload). |
CRBH | Usually provided preloaded (C0) or with very low clearance due to one-piece construction. | C0 (preload), C1, and C2 clearances available. |
CRBS | Outer ring split; inner ring solid (similar to CRB construction but slim dimensions). | Typically available with light preload (C0) or slight clearance (C1) due to thin rings. |
RA | Outer ring split; inner ring solid (designed for strainwave drive integration). | Usually provided in CC0 (preload) for zero backlash. Also available with slight clearance if needed (C1). |
RA-C | Outer ring split; inner ring solid. | C0 or light clearance. Cage prevents roller contact, so the bearing runs smoothly even without preload. |
RA-G | Outer ring split; inner ring solid, with gear. | Typically comes preloaded (C0) to ensure zero backlash in the geared interface. |
RA-GC | Outer ring split; inner ring solid, with gear and cage. | Preload or slight clearance as required – often light preload to maintain positioning accuracy in the gear mesh. |
Each series is tailored to specific needs, from general-purpose high-rigidity types (CRB/CRBC) to ultra-thin lightweight types (CRBS/RA) and integrated solutions with gears (RA-G variants). All series are manufactured to high precision standards and can be ordered in various accuracy grades (typically equivalent to ABEC-5/P5 or higher) and preload conditions. When choosing a series, consider the mechanical layout (which ring will be stationary or rotating), space constraints, and whether additional integration (like mounting holes or gears) is beneficial for your design.
CRA and CRC Series – Cross Roller Bearings for Strainwave Drives
TPI has developed two highly specialized families of cross roller bearings optimized for use in strainwave (harmonic) gear reducers and compact robotic joints: the CRA series and the CRC series. These bearings offer compact integration, precision performance, and ease of mounting—ideal for collaborative and industrial robot arms.
CRA Series (Cross Roller Bearings for Harmonic Drive Output)
The CRA series features a split outer ring and integral inner ring, specifically engineered for use in harmonic drive outputs.
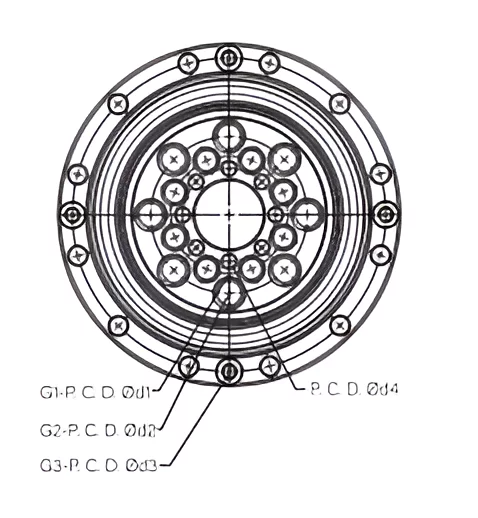
These bearings are preloaded to eliminate backlash, ensuring stable positioning even under reversing loads or vibration. With integrated mounting holes and high moment stiffness, the CRA series is perfect for compact actuator units.
Key specifications (excerpt):
Bearing Type | Bore (d) [mm] | OD (D) [mm] | Width (B) [mm] | Dyn. Load Cr [kN] | Stat. Load C0r [kN] | Moment Mᶜ [Nm] | Rigidity K [×10⁶ Nm/rad] |
CRA1116 | 11 | 42.5 | 16.5 | 4.23 | 5.46 | 36.9 | 4.38 |
CRA1016 | 10 | 49.5 | 16.5 | 4.76 | 6.79 | 57.6 | 7.75 |
CRA1416 | 14 | 56.5 | 16.5 | 5.20 | 8.10 | 81.9 | 12.8 |
CRA2018 | 20 | 73.5 | 18.5 | 8.64 | 13.59 | 140.4 | 24.2 |
CRA2621 | 26 | 92.0 | 22.5 | 13.5 | 22.5 | 281.7 | 53.9 |
These bearings are supplied with optimized preload and offer high stiffness and tilt rigidity, crucial for accurate robotic movement. They are configured for direct mounting via integrated hole patterns and support compact reducer assembly with minimal clearance and deflection.
CRC Series (Cross Roller Bearings with Integrated Flange)
The CRC series expands on the CRA concept with larger diameters and optimized geometry for high-capacity torque transmission. It features mounting holes on both the inner and outer rings, enabling highly compact integration into rotary actuators and direct-drive motors.
Select CRC Bearing Dimensions:
Bearing Type | ID [mm] | OD [mm] | Width (B) [mm] | Flange Bolt Hole Pattern |
CRC3815 | 38 | 70 | 15.1 | A1–P.C.D 64, 4-M4 |
CRC5418 | 54 | 96 | 18.5 | A1–P.C.D 74, 4-M4 |
CRC6720 | 66 | 110 | 20.7 | A1–P.C.D 88, 4-M4 |
CRC8824 | 84 | 142 | 24.4 | A1–P.C.D 106, 4-M4 |
This series is particularly well-suited to robotic rotary modules, strainwave reducers, and cobot wrist joints. Its low profile combined with strong load-handling capacity allows for compact, high-torque motion systems.
Selection Criteria for Cross Roller Bearings
Choosing the best cross roller bearing for a given application involves evaluating several factors. Below is a guide to help engineers and procurement managers select the correct TPI cross roller bearing series and specifications:
- Load requirements (Radial, Axial, Moment). Start by determining the maximum loads the bearing must support in each direction. All TPI cross roller bearings can handle combined loads, but their load capacities differ by series and size. If the application has extremely high radial or axial loads, a standard high-capacity series like CRB/CRBC (with full complement rollers) may be appropriate. For heavy overturning moments (e.g., a cantilevered table), consider larger diameter cross rollers or high-rigidity types (CRBH series). Check the dynamic and static load ratings in TPI’s catalog for candidate bearings – the selected bearing should comfortably exceed the peak loads for safe operation.
- Rotational accuracy and stiffness. Identify how precise and rigid the rotation needs to be. If the mechanism requires zero backlash and minimal elastic deflection (for instance, a precision indexing table or robot reducer output), choose a bearing that can be preloaded (C0 class) and that has a stiff construction. High-rigidity series like CRBH or preloaded RA series are ideal in such cases. If ultra-high accuracy is needed, also consider specifying a higher precision grade (such as P4 or P2, if available) – though TPI’s standard cross rollers are already made to tight tolerances. For less demanding accuracy (say, ±0.01 mm runout is acceptable) or for smoother motion, a bearing with slight clearance (C1) and a cage may suffice (e.g., CRBC with C1 class).
- Mounting and space constraints. Examine the design envelope and mounting configuration. Determine the bore diameter and outer diameter you can accommodate, as well as the width of the bearing. TPI’s cross roller offerings range from standard profile (CRB/CRBC, relatively thicker rings) to slim profile (CRBS/RA series, much thinner rings). If you need to minimize weight or thickness, the CRBS or RA series might be the best fit, as they have a low cross-section height. However, note that slim bearings, while lighter, may handle slightly lower loads than an equivalently sized standard bearing. Also consider the mounting: if you want to bolt the bearing directly to surrounding components, look for series that include mounting holes or flanges (many RA series bearings have this). If the design requires a hollow shaft or an integrated gear, the RA-G/RA-GC series could reduce part count by combining those functions with the bearing. Always ensure there is access for tightening the mounting bolts and that the adjacent structure supports the bearing adequately (flat, rigid mounting surfaces).
- Which ring rotates? In cross roller bearings, one ring is usually fixed to the base, and the other is attached to the rotating part. For optimal performance, the one-piece (unsplit) ring should typically be the rotating ring in high-precision applications. This is because the split ring (two-piece), when clamped, can introduce a slight eccentricity if not perfectly matched. For instance, if you plan to have the inner ring rotate (common in turntables where the table is on the inner ring), a bearing like CRB (split outer ring, solid inner) is designed for that scenario. Conversely, if the outer ring rotates (e.g., a rotating arm mounted on a stationary inner ring), a CRBC bearing (split inner, solid outer) might maintain better symmetry for the rotating outer ring. In practice, the differences are small, but they can affect super-precision applications. So, choose CRB vs. CRBC based on which ring is the moving part: CRB for rotating inner ring, CRBC for rotating outer ring (as a general rule). The RA series for strainwave drives all have split outer rings (since usually the outer ring is fixed to a gearbox case and the inner ring rotates with the output flange). If needed, consult TPI’s engineering team or documentation for recommendations on ring configuration for your use case.
- Preload and clearance class. Decide whether your application benefits most from a preloaded bearing (C0) or one with slight clearance (C1/C2). As discussed, preload gives maximum stiffness and accuracy at the cost of higher friction. Precision positioning systems (robot arms, measuring instruments) usually use CC0 preloaded bearings for rigidity. On the other hand, if the bearing will rotate continuously at a relatively high speed or you want to minimize heat generation, a bit of clearance (C1) might be better. Also consider the thermal conditions: in high-temperature environments, a C1 or C2 bearing may avoid binding as the parts expand. TPI supplies cross rollers in these classes, so match the class to your performance needs. If unsure, C0 is a safe default for most low-speed, high-precision tasks, while C1 might be chosen for smooth motion applications. Always avoid adding additional preload inadvertently by heavy press-fits – if you intend to press the bearing into a housing, you might select C1 clearance so that the fit tolerance will take up the clearance and effectively create a preload once assembled.
- Precision grade. Cross roller bearings can be made in different accuracy grades (often coded P0, P6, P5, P4, P2 in increasing precision). TPI’s standard cross roller bearings already meet high precision standards (often equivalent to ABEC-5/P5 or better). If your application is extremely sensitive (such as nano-positioning or aerospace inertial systems), you may require P4 or P2 grade bearings. Check what grades TPI offers for the specific series – often, the RA series for robotics is supplied in high precision by default. Tighter grades will have lower runout and matching of ring ID/OD deviations, but they can cost more. Select the grade that meets your accuracy budget; overspecifying precision can add unnecessary cost.
- Environmental factors. Consider any special environmental requirements. If the bearing will be exposed to moisture or corrosive conditions, you might need stainless steel versions or special coatings – check with TPI if they offer a variant, or consider external coatings. If the application is in a cleanroom or vacuum (semiconductor tools, medical devices), ensure the grease and seals are compatible (TPI can provide details on the type of grease pre-packed in the bearings). For vacuum use, you may need a dry bearing (no grease) or a different lubricant, which would be a custom selection. In most cases, the standard bearing with lithium soap grease and nitrile rubber seals will be suitable for general industrial environments.
By evaluating these factors – loads, accuracy, space, configuration, preload, precision grade, and environment – you can narrow down the TPI cross roller bearing that best fits your project. TPI’s catalog and technical support can provide detailed specifications for each series to finalize the selection. Remember that the correct choice will ensure long life, consistent precision, and reliable operation in your application, so it’s worth taking the time to match the bearing to your requirements.
Part Number System
TPI’s cross roller bearings use an alphanumeric part number code that identifies the bearing series, size, special features, and clearance. Decoding the part number can help you verify you’ve selected the correct bearing configuration. Let’s break down an example part number:
Example Part Number: RAU3008UUCO
- RAU – This prefix denotes the series and type of bearing. In this case, RAU indicates an RA series cross roller bearing (a thin type for robot strainwave drives). The “U” in RAU is part of TPI’s designation; for RA series bearings, it often signifies a standard variant in that family. (Note: In some catalogs, RA and RAU may be used interchangeably for the thin crossed roller series with mounting holes – the exact prefix can vary by region, but the functionality is the same.) Essentially, RAU tells us this is a Robot Arm cross roller bearing, thin type, with a unified ring design suitable for harmonic drives.
- 30 – The bore diameter of the bearing in millimeters. Here, “30” means the bearing’s inner diameter is 30 mm. TPI typically uses two-digit numbers for the bore in the part number. Common cross roller sizes range from small (~20 mm bore) to large (200+ mm), depending on the series.
- 08 – The width of the bearing in millimeters. “08” indicates this bearing is 8 mm wide. In cross roller part numbers, the two-digit number following the bore often represents the cross-sectional height/width. A width of 8 mm for a 30 mm ID suggests a very thin bearing (consistent with RA series design). The outer diameter could be inferred from series data (for RA series, a 30 mm bore might have ~ +40 mm added for OD, but OD is not directly given in the code here).
- UU – The seal configuration. “UU” means double-sided seals, i.e., the bearing has seals on both sides (often rubber contact seals). This is common for TPI cross rollers – sealed on both sides to keep grease in and contaminants out. If the code were “ZZ” it might indicate metal shields, or “NN” (as per some standards) would mean no seals (open bearing). In our example, UU confirms it’s a sealed bearing ready for use without separate sealing by the customer.
- C0 – The internal clearance/preload class. “C0” (also written CC0) designates that this bearing is a zero-clearance (preloaded) bearing. In other words, it has been manufactured for the tightest internal fit, typically giving a slight preload once installed. This matches our expectations for a high-precision RA series bearing, as most are supplied in a preload condition to eliminate play. (If the code was C1 or C2, it would indicate those clearance classes instead.) In some part number systems, C0 might not be explicitly stated if it’s the default, but TPI includes it here to be clear.
Putting it together, RAU3008UUCO is a TPI cross roller bearing from the RA thin series, 30 mm bore, 8 mm width, sealed on both sides, with zero internal clearance (preload). Such a bearing would typically have a one-piece inner ring, two-piece outer ring, and likely be intended for a harmonic drive or similar precision application. Always cross-reference the part number with TPI’s catalog data: for instance, RAU3008UUCO corresponds to a specific item with known outer diameter, dynamic load rating, etc., which can be confirmed in the product tables.
Other common code elements: If present, a suffix like “-P5” or “-P4” might denote the ABEC accuracy class (P5 for ISO Class 5, P4 for Class 4, etc.), but TPI often builds the precision into the base part number for cross rollers. Sometimes manufacturers also include a code for the cage type (e.g., “A” for alloy separator, or no letter for full complement as in the PMI code reference). In TPI’s numbering, the presence of “C” in RA-C or “GC” in RA-GC inherently tells us a cage is used. If you see “X” or other letters, they might indicate a special variant or custom design. For standard offerings, the format above (Series + size + seals + clearance) covers most of what you need to know. By understanding each segment of the code, you can quickly verify that, for example, you are ordering a sealed, preloaded bearing of the correct size and series for your project.
If you’re designing a new high-precision rotary mechanism or looking to upgrade an existing system for better accuracy, now is the time to leverage the advantages of TPI cross roller bearings. Contact PIB Sales, whether it’s a standard catalog bearing or a custom solution, PIB can help find the optimal fit. By choosing TPI, you gain the quality of a top-tier manufacturer and the support of knowledgeable sales staff at PIB. Empower your machines with the performance of cross roller bearings and experience the difference in precision and reliability.
For further information, contact us at [email protected] or visit www.pibsales.com.