Robotic arms, particularly articulated arms, are widely used across a wide range of industries, from automotive manufacturing to advanced medical procedures. These versatile machines mimic the movements of the human arm, providing precision, strength, and repeatability in tasks that require high levels of accuracy. In this article, we delve into the inner workings of articulated robotic arms, focusing specifically on their operating principles and the role that bearings play in their performance.
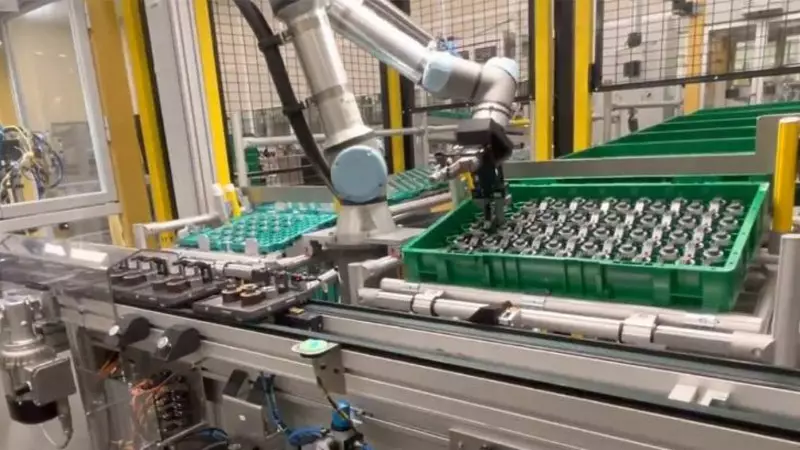
Types of Robotic Arms
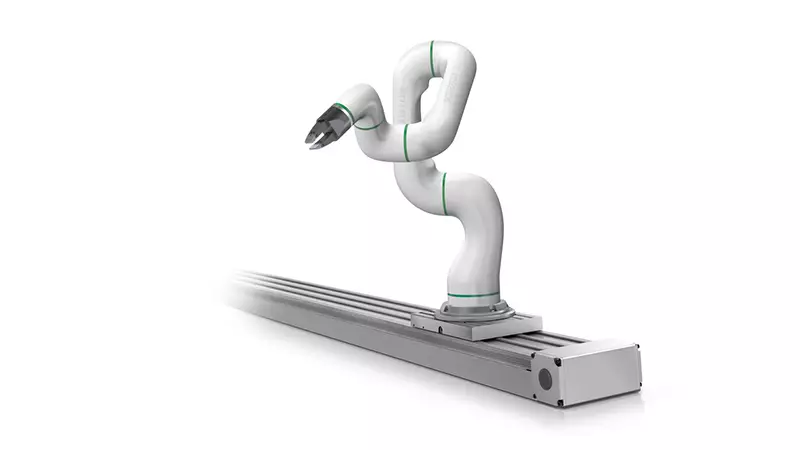
Articulated robotic arms are the most common type of industrial robot, closely resembling the movement of a human arm with multiple joints that provide a high degree of flexibility. These arms consist of rotary joints that enable motion along multiple axes, typically ranging from three to six degrees of freedom (DoF). The design of an articulated arm allows for a wide range of movements, including rotation, pivoting, and angular displacement, making them ideal for tasks that require precision and versatility.
The primary components of an articulated robotic arm include the base, shoulder, elbow, wrist, and end effector. Each joint is powered by actuators, typically electric motors, which are responsible for driving the movement. The joints are connected by links, and the combination of these joints and links allows the arm to achieve various positions and orientations.
The degrees of freedom in an articulated arm are crucial to its functionality. A basic three-axis arm can move in the X, Y, and Z directions, while more advanced arms with five or six DoF can perform more complex tasks, such as orienting the end effector in any direction. The higher the DoF, the greater the arm’s capability to navigate around obstacles and reach challenging positions, making it indispensable in dynamic and complex environments.
SCARA (Selective Compliance Articulated Robot Arm)
The SCARA robot, distinguished by its Selective Compliance in the horizontal plane, offers a unique combination of rigidity in the vertical axis and flexibility in the horizontal plane. This design allows SCARA robots to perform tasks that require precision and speed in two-dimensional space, such as pick-and-place operations, assembly, and material handling.
SCARA robots typically have four degrees of freedom, with two parallel rotary joints that provide selective compliance. This compliance is beneficial in applications where lateral force is applied, as the robot can absorb some of the impact, reducing the potential for misalignment or damage. The vertical rigidity ensures that the SCARA can maintain accuracy in tasks such as inserting components into tight spaces.
Comparison with articulated arms: Compared to articulated arms, SCARA robots are faster and more precise in operations that involve horizontal movement. However, they are less versatile in three-dimensional tasks due to their limited vertical flexibility. SCARA robots are often preferred in high-speed assembly lines where precision and speed are critical, whereas articulated arms are chosen for more complex tasks that require greater flexibility and reach.
Cartesian and Gantry Robots
Cartesian robots, also known as linear or gantry robots, operate on three orthogonal axes (X, Y, and Z) that move in straight lines. These robots are characterized by their rigid, rectangular design, which provides high precision and repeatability in linear motions. The structure of Cartesian robots allows them to cover large workspaces, making them ideal for tasks such as CNC machining, 3D printing, and automated assembly.
Gantry robots are a subset of Cartesian robots, typically larger in scale, designed for handling heavy loads over extensive areas. They are often used in applications like palletizing, where the robot needs to move large objects across a wide area, or in large-scale 3D printing, where precision and stability over a large build area are required.
The primary advantage of Cartesian and gantry robots is their simplicity and accuracy in linear tasks. They are easy to program and maintain, with the added benefit of scalability, making them suitable for applications that demand large, precise movements. However, their limited degrees of freedom restrict their use to tasks that do not require complex, multi-axis movements, where articulated or delta robots might be more suitable.
Delta and Parallel Robots
Delta robots, also known as parallel robots, are designed with a unique triangular configuration that allows for high-speed and precise operations. The robot consists of a base that supports three arms connected to a single-end effector. The arms move in parallel, providing a highly dynamic and agile movement ideal for tasks requiring rapid pick-and-place actions.
The key advantage of delta robots is their speed and precision in handling lightweight objects. They are widely used in the food industry for packaging and sorting, where their ability to perform high-speed repetitive tasks is invaluable. Their parallel kinematic structure also makes them suitable for delicate tasks in electronics assembly, where precision and care are required to handle small components.
While delta robots excel in speed and precision, their design limits them to tasks that involve small, lightweight objects. They are not as versatile as articulated arms in terms of reach and flexibility, nor can they handle the heavy loads that Cartesian or gantry robots can manage. However, in specialized high-speed environments, delta robots are unparalleled in performance.
Contact Pacific International Bearing for more information on bearings used in robotic applications [email protected].
Collaborative Robots
Collaborative robots, or cobots, are designed to work alongside humans in shared workspaces, offering a blend of safety, flexibility, and ease of use. Unlike traditional industrial robots, which are often caged to prevent human contact, cobots are equipped with advanced sensors, force control, and AI algorithms that allow them to detect and respond to human presence, ensuring safe operation.
Cobots are typically lighter and more compact than traditional robots, with ergonomic designs that make them easy to deploy and redeploy across different tasks. They are used in various industries, from automotive assembly to small-scale manufacturing, where they assist human workers in tasks such as machine tending, inspection, and simple assembly processes.
The primary advantage of cobots is their ability to enhance productivity without the need for extensive safety measures, making them cost-effective and easy to integrate into existing workflows. Their user-friendly interfaces allow even non-experts to program and operate them, reducing the learning curve and increasing flexibility in production processes.
Cobots are also designed to be highly adaptable, and capable of performing a wide range of tasks with minimal reconfiguration. This makes them ideal for small and medium-sized enterprises (SMEs) that require versatile, scalable solutions to remain competitive in fast-changing markets.
Operating Principles of Robotic Arms
Kinematic Chains and Linkages
Robotic arms function through a series of interconnected components known as kinematic chains, where each link and joint contributes to the arm’s overall movement capabilities. These kinematic chains are essentially mechanical linkages that define how the robotic arm moves, similar to the bones and joints in a human arm. The primary role of these chains is to ensure that motion is transmitted effectively from the base of the robot to the end effector, which interacts with the external environment.
Each joint in the chain offers a specific degree of freedom (DoF), allowing movement in a particular direction, whether rotational or linear. For example, a revolute joint permits rotation around a fixed axis, akin to a hinge, while a prismatic joint allows sliding motion along a straight path. The combination and configuration of these joints determine the robotic arm’s ability to navigate through its workspace, which is the area within which the arm can operate.
Kinematic chain types:
- Open kinematic chain
This configuration is common in articulated arms, where the links and joints are arranged sequentially, allowing the end effector to move freely within its operational range. This setup provides great flexibility but requires precise control to manage its potentially wide range of motion. - Closed kinematic chain
Found in parallel robots like Delta robots, these configurations offer higher stability and are capable of handling greater loads due to their looped structure. However, this comes at the cost of reduced flexibility and a more constrained workspace.
Key Components:
- Links – these are the rigid segments between joints, analogous to the bones in a skeleton.
- Joints – joints of articulation that enable movement, including both revolute (rotational) and prismatic (linear) types.
Component | Function | Example |
Joints | Enable rotation or translation | Revolute (rotational), Prismatic (linear) |
Links | Connect joints, determine arm structure | Segments between joints |
Open chain | Provides flexible, extensive movement | Common in articulated arms, SCARA robots |
Closed chain | Offers stability, high load-bearing capacity | Found in Delta and parallel robots |
Actuation methods
The movement of robotic arms is powered by actuators, which convert various forms of energy into mechanical motion. Depending on the requirements of the task, different types of actuators — electric, hydraulic, or pneumatic — can be employed, each offering distinct advantages and limitations. The choice of actuator not only determines the arm’s movement capabilities but also influences its efficiency, precision, and the type of maintenance it will require.
Electric actuators are the most prevalent in modern robotics due to their precision and ease of control. These actuators use electric motors to drive the joints, providing high accuracy and smooth motion, which is crucial for tasks that demand fine manipulation. They are particularly favored in industrial settings for tasks like assembly and material handling, where repeatability and consistency are paramount.
Hydraulic actuators leverage pressurized fluids to generate movement, making them suitable for applications that require high-force outputs. These actuators are often found in large-scale industrial robots or equipment that must handle heavy loads, such as in construction or heavy machinery automation. However, hydraulic systems are more complex, requiring pumps, fluid reservoirs, and regular maintenance to ensure leak-free operation.
Pneumatic actuators use compressed air to produce motion, offering a simpler and more cost-effective solution, especially for high-speed, low-load applications. While less precise than electric actuators, pneumatic systems excel in environments where rapid, repetitive tasks are needed, such as in packaging or pick-and-place operations.
How Bearings Influence Robotic Arm Performance
The quality and type of bearings used can significantly influence the accuracy with which the arm can position and move its end effector. High-precision applications, such as robotic surgery, semiconductor manufacturing, and intricate assembly tasks, require bearings that offer minimal friction and tight tolerances.
Examples of Bearings Used:
- IKO Crossed roller bearings bearings provide excellent rotational accuracy and high rigidity, making them ideal for applications where precision is critical. IKO designs and manufactures a variety of crossed roller bearings that can handle radial, thrust and moment loads at the same time.
- These compact bearings feature rollers crossed at right angles between inner and outer rings.
- Widely used in machine tools, industrial robots and medical equipment because of their high rotational accuracy.
- Roller guide options include a cage or separator as well as a full complement design. Both the cage and separator styles offer a small coefficient of friction for high-speed rotation. Full complement bearings handle heavy loads at low speeds.
- Sealed and open designs are available. Sealed bearings incorporate synthetic rubber seals to protect against dust, dirt and grease.
- Angular contact ball bearings (SKF 7200 Series): Known for their ability to support high axial loads in one direction, these bearings are used in joints where precise angular movement is required. The 7200 series from SKF is commonly used in robotic wrists and elbows, where accuracy is paramount.
In high-precision tasks, even slight deviations can lead to errors, so the choice of bearings directly impacts the performance and reliability of the robotic arm.
The load-bearing capacity of a robotic arm is heavily influenced by the type of bearings used in its joints and structure. Bearings must be capable of supporting both the static and dynamic loads encountered during operation without compromising performance.
- Spherical roller bearings (FAG 22200 series): The series offers excellent load distribution and can accommodate misalignment, which is crucial in maintaining stability under heavy loads.
- Tapered roller bearings (SKF 30200 series): Tapered roller bearings are often used in applications where both radial and thrust loads are present, such as in the pivot points of robotic arms.
Proper load distribution across the bearings ensures that the robotic arm can handle various tasks without experiencing excessive wear or failure.
The longevity of robotic arms is directly tied to the performance of their bearings. Bearings that are designed for high performance can extend the operational life of the robotic arm, reducing downtime and maintenance costs.
- Deep groove ball bearings (TPI 6000 series): These are widely used in applications where low maintenance is desired. The TPI 6000 bearing is ideal for use in lightweight radial bearing applications.
- Sealed bearings (TPI bearings) are designed to prevent contaminants from entering the bearing assembly, extending life and reducing the need for frequent maintenance.
- Precision ball bearings (TPI 6800 series): These narrow series bearings are specifically designed to minimize vibration and noise, making them ideal for applications where smooth, quiet operation is critical.
- Hybrid ceramic bearings (PIB Brand): These bearings use ceramic balls instead of steel, which reduces weight, lowers friction, and significantly cuts down on vibration and noise. The PIB Hybrid series is commonly used in high-speed robotic arms where these factors are crucial for maintaining performance.
By selecting bearings designed for low vibration and noise, manufacturers can enhance the overall performance of robotic arms, leading to smoother operation and increased accuracy.
Future Trends in Bearing Technology for Articulated Robotic Arms
As robotic systems, especially articulated arms, continue to become more advanced and important to industries such as manufacturing, healthcare, and logistics, the technology supporting them, including bearings, is also evolving rapidly. Bearings ensure smooth, precise, and reliable motion in robotic arms, which must operate with extreme accuracy under dynamic conditions. Below are the key trends shaping the future of bearing technology for articulated robotic arms:
1. Lightweight and compact designs
With the increasing need for smaller, more agile robots, particularly in precision manufacturing and medical applications, bearings are being designed to be lighter and more compact without sacrificing load capacity or durability. Advanced materials like lightweight alloys and composite materials are being utilized to reduce weight while maintaining structural integrity. Compact bearings not only improve the overall efficiency of robotic arms but also enable the design of smaller robots capable of working in tight spaces.
2. High-speed bearings for faster operations
Modern industries demand robotic arms that can operate at higher speeds to improve productivity. Bearings are evolving to support faster rotational speeds while maintaining precision. Advances in lubrication technology, reduced friction designs, and optimized internal geometries are allowing bearings to perform efficiently even at extreme speeds. This is particularly critical in assembly lines, pick-and-place applications, and other tasks requiring rapid, repetitive motion.
3. Integration of Smart Bearings for Predictive Maintenance
One of the most exciting trends is the rise of smart bearings, which integrate sensors to monitor critical performance parameters such as temperature, vibration, and load. These smart bearings enable real-time data collection and predictive maintenance, reducing downtime and avoiding unexpected failures. For articulated robotic arms operating in high-stakes industries like healthcare or logistics, this technology is becoming a game-changer, as it ensures uninterrupted performance and improves operational efficiency.
4. Energy-efficient bearing solutions
With the growing emphasis on sustainability, energy efficiency is a major focus for robotic technology. Bearings with low-friction designs and advanced lubrication systems are being developed to minimize energy consumption in robotic arms. These improvements not only reduce operational costs but also align with global efforts to achieve greener manufacturing processes.
5. Customized bearings for specific applications
Industries are increasingly demanding bearings tailored to the unique requirements of specific applications. For articulated robotic arms, this includes bearings with non-standard sizes, unique load capacities, and application-specific materials. The rise of customization ensures that robotic arms are equipped with bearings perfectly suited to their operating conditions, enhancing their overall performance and longevity.
Bearing technology for articulated robotic arms is advancing in tandem with the rapid evolution of robotics. From smart monitoring capabilities to lightweight designs, the trends outlined above highlight how bearings are becoming more integral to the development of agile, efficient, and reliable robotic systems. As industries continue to innovate, bearings will remain a cornerstone of robotic performance, enabling a new generation of intelligent and adaptable machines.
By keeping up with these trends, PIB Sales ensures access to the latest bearing technologies that meet the evolving demands of robotic applications. Our expertise in high-performance bearings helps clients stay ahead in their industries by equipping their robotic systems with cutting-edge solutions. Let us help you find the perfect bearing for your robotic applications!
Contact us today for more info. Visit us at www.pibsales.com.