This guide, presented by PIB Sales, provides a comprehensive selection framework for cylindrical roller bearings. It covers basic design principles and troubleshooting common issues. The article aims to equip professionals in various industries with the knowledge necessary to make informed decisions about bearing selection and maintenance, ultimately enhancing the efficiency and reliability of their machinery.
Understanding Cylindrical Roller Bearings
The following series are already available in the TB design from Pacific International Bearing Sales Inc. www.pibsales.com
Design | Series | From bore code | From bore diameter |
N, NJ, NU, NUP | 2E | 48 | 240 |
N, NJ, NU, NUP | 22E | 44 | 220 |
N, NJ, NU, NUP | 3E | 34 | 170 |
N, NJ, NU, NUP | 23E | 34 | 170 |
N, NJ, NU, NUP | 10 | 80 | 400 |
N, NJ, NU, NUP | 19 | 600 | 600 |
Cylindrical roller bearings are mechanical components widely used in industrial applications. They are designed to support heavy radial loads and operate with high precision. These bearings consist of cylindrical-shaped rollers that are held in place by an inner and outer raceway, allowing for efficient rotation while maintaining stability.
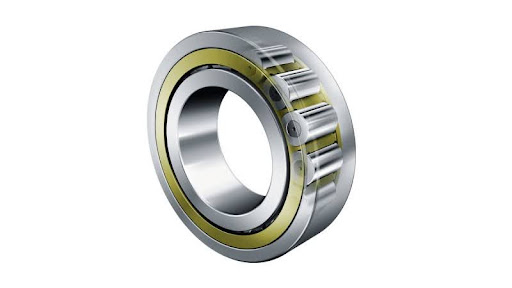
One of the key features of cylindrical roller bearings is their ability to handle radial loads, which are forces applied perpendicular to the axis of rotation. They excel in applications where there is a need to support heavy loads, such as in conveyor systems, gearboxes, and automotive transmissions.
These bearings are characterized by their part numbers, which typically include designations like NN3016K or NJ220E. The part number provides information about the bearing’s size, configuration, and other specifications, making it essential for selecting the right bearing for a particular application.
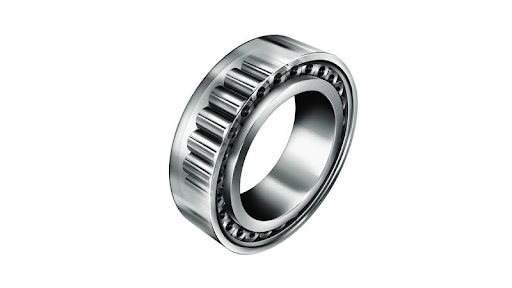
For instance, the “NN” series represents double-row cylindrical roller bearings ideal for applications requiring high radial load capacity. The “NJ” series denotes single-row bearings with a rib on one side of the outer ring, suitable for applications with limited axial displacement.
The manufacturing of cylindrical roller bearings demands high precision equipment. Reputable manufacturers invest in advanced engineering techniques to ensure the bearings meet stringent performance standards. This process starts with selecting high-quality materials, such as high-carbon chrome steel, for their strength and wear resistance. Meticulous design and machining of the roller and raceway geometry ensure smooth operation and minimal friction.
The design of the cage is crucial for maintaining roller alignment and spacing. Material choice is also important for optimal performance. Heat treatment, which involves quenching and tempering, enhances component hardness and longer life.
The precision of these bearings is enhanced by advanced technology, such as CNC machining and automated quality control systems. As a result, cylindrical roller bearings meet the exacting demands of industrial applications, delivering reliable and accurate performance.
Factors and Steps to Consider in Selection
When selecting cylindrical roller bearings, several key factors must be considered:
Load capacity and speed requirements. It’s crucial to assess the radial and axial load requirements of your application, as well as the desired operational speed. Higher load capacities might necessitate bearings with greater radial dimensions or multi-row designs.
Environmental and operational conditions. The operating environment is a significant consideration. Bearings operating in high-temperature or corrosive environments may require special materials or coatings. Similarly, applications in contaminated or wet conditions might need bearings with specific sealing solutions.
Application specifics. The specific requirements of your machinery, such as space constraints and alignment accuracy, should guide the selection of bearing type and size. For example, applications with limited radial space might benefit from single-row cylindrical roller bearings, which offer a compact design while still providing high load-bearing capacity.
Cylindrical roller bearing selection checklist:
Load Analysis:
- Determine the magnitude and type of load (radial, axial, or both).
- Identify dynamic and static load requirements.
Speed and Operating Conditions:
- Determine the operating speed and critical speed.
- Assess environmental factors, including temperature and contaminants.
Bearing Dimensions:
- Calculate the required bore diameter, outer diameter, and width.
- Ensure compatibility with shaft and housing dimensions.
Lubrication Considerations:
- Select the appropriate bearing material (e.g., chrome steel, stainless steel).
- Choose the bearing design (single-row, double-row) based on load capacity and application requirements.
Radial Clearance and Preload:
- Determine the required radial clearance or preload settings.
- Ensure proper axial movement and eliminate play.
Mounting and Installation:
- Assess fit tolerances for the shaft and housing.
- Evaluate the method of mounting to prevent misalignment.
Bearing Material and Design:
- Select the appropriate bearing material (e.g., chrome steel, stainless steel).
- Choose the bearing design (single-row, double-row) based on load capacity and application requirements.
Conclusion
Selecting the right cylindrical roller bearing can significantly impact the efficiency and longevity of your machinery. This guide, provided by PIB Sales, aims to simplify this process by offering valuable insights into the design, selection, and maintenance of these bearings. For more details about cylindrical roller bearings and expert assistance in choosing the right product for your needs, we invite you to explore the catalog at PIB Sales website. With our expertise and comprehensive range of products, we are committed to enhancing the performance and reliability of your machinery. You can also contact us at [email protected].