Schaeffler recently introduced the PSC Series Precision Planetary Gear Units for Robots and is available from Pacific International Bearing Sales Inc.
Overview of PSC Series Precision Planetary Gear Units
The PSC Series precision planetary gear units are a significant advancement in drive technology, tailored for robotic applications. The PSC Series precision planetary gear units enhance positioning accuracy, repeatability, and overall performance, making them an ideal choice for industrial and collaborative robot (cobot) applications.
The PSC Series integrates a helical gear stage at the input and unique tooth technology to ensure minimal torsional backlash throughout the operating life. This design feature is crucial for maintaining high precision and reliability in robotic movements and operations. The gear units boast a torsional backlash of ≤ 0.1 arcmin, highlighting their exceptional precision.
A standout feature of the PSC Series is its rigid bearing arrangement, which provides high torsional and tilting rigidity. This rigidity is essential for supporting significant forces and tilting moments encountered in robotic applications. These gear units have a compact design that offers a high torque density within a minimal envelope.
The versatility of the PSC Series is reflected in its wide range of variants, including nine different sizes with both solid and hollow shaft designs and various motor attachment options. This flexibility allows for extensive customization to match the required torque and speed ranges for diverse applications, from small cobots to large industrial robots.
Schaeffler offers a design intended for a long operational life of up to 20,000 hours, the PSC Series gear units are built to endure the demands of continuous use in harsh industrial environments. Schaeffler’s rigorous engineering standards and quality control measures support this longevity.
Technical Specifications and Performance
The PSC Series precision planetary gear units by Schaeffler are designed to deliver exceptional performance in robotic and industrial applications. These gear units are engineered with cutting-edge technology to ensure high precision, durability, and operational efficiency. Below is a detailed examination of their technical specifications and performance features.
Design and construction. The PSC Series gear units include an integrated helical gear stage at the input. This design ensures minimum torsional backlash and improves the overall precision of the gearbox. The gear teeth are designed using proprietary tooth technology, which contributes to extremely low and consistent torsional backlash across the whole operational life.
Torsional rigidity is an important consideration for the PSC Series gear units. It is defined as the ratio of the torsional torque exerted on the gearbox from the outside to the resulting torsion angle at the output. Torsional rigidity is measured in Nm per arcminute. The gear units have a high torsional rigidity due to their sturdy design and rigid bearing arrangements.
Parameter | Description |
Torsional backlash | ≤ 0.1 arcmin |
Torsional rigidity | High rigidity ensured through rigid bearing arrangements |
Measurement method | Gearbox loaded bidirectionally with increasing torque up to nominal value, torsion angle recorded |
Efficiency | Over 90% under full load, ensuring stable temperature and low energy consumption |
Tilting rigidity refers to the gear unit’s ability to resist bending moments resulting from external forces. The PSC Series gearboxes exhibit high tilting rigidity due to their robust design and precise engineering. This parameter is measured in Nm/arcmin, ensuring that the gearbox can handle significant forces without compromising performance.
The synchronous running accuracy of the PSC Series is a measure of the maximum transmission error, defined as the fluctuation amplitude of the output rotary motion. It is given in angular seconds (arcsec). The gear units maintain high synchronous running accuracy by minimizing transmission errors, which is crucial for applications requiring precise motion control.
Parameter | Description |
Synchronous running accuracy | High accuracy with minimal transmission error, given in angular seconds (arcsec) |
Measurement method | Gearbox rotated without load in trailing mode, input and output rotary motion recorded |
The efficiency of the PSC Series gear units is a testament to their advanced engineering. Efficiency is defined as the ratio of output to input power and is typically less than 1 due to power losses from friction. The PSC Series achieves an efficiency of ≥ 90%, making them highly effective for continuous industrial operations.
Precision Planetary Gearboxes
Gearbox mounting kits from Schaeffler can be integrated directly into the system. These kits are available in several versions, each designed to cater to different needs and operational environments.
Version | Features |
Solid shaft version V | Ideal for high torque applications, ensuring robust performance and stability. |
Hollow shaft version H | Facilitates the passage of supply cables, offering versatile integration options. |
Food grade lubrication | Suitable for hygienic environments, ensuring compliance with food industry standards. |
Rotary shaft seals | Available in standard NBR and optional VITON, providing long-lasting durability and protection in various environmental conditions. |
Protective sleeve for hollow shaft | Offers additional protection for the hollow shaft against contaminants and physical damage. |
These mounting kits include a separate input pinion as standard, which is supplied loose. The transmission ratio is determined by whether a plug-in pinion (ER) or slip-on pinion (AR) is used. The hollow shafts are particularly suitable for the passage of supply cables, ensuring that the gearboxes can be adapted to meet specific operational needs.
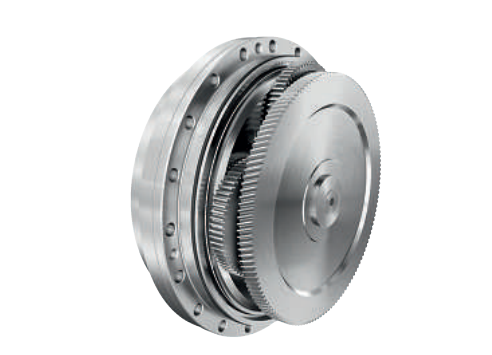
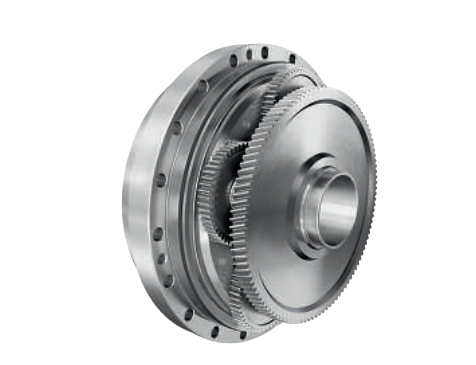
The three-stage construction with a solid shaft is a key configuration of the PSC Series gearboxes. This design is focused on maximizing torque handling and ensuring robust performance in demanding applications.
Technical specifications:
Parameter | Description |
Centre distance (A) | The distance between the input shaft and the middle of the gearbox, ensures precise alignment and optimal performance. |
Distance between housing locating face and input shaft surface (B) | Ensures that the gearbox is securely mounted, providing stability during operation. |
Gear tooth width of the pinion (C) | Designed to withstand high loads, contributing to the durability and efficiency of the gearbox. |
The following table provides detailed specifications for the PSC Series precision planetary gearboxes with solid shafts, illustrating their nominal torque capacities, input pinion types, and critical dimensions.
Gearbox Dimensions:
Gearbox | Nominal Torque (Nm) | Input Pinion | Centre Distance (A) (mm) | Distance Between Housing Face and Input Shaft Surface (B) (mm) | Gear Tooth Width (C) (mm) |
---|---|---|---|---|---|
PSC030-V-E | 50 | AR16 | 60 | +0.022 / +0.037 | 14.5 |
PSC030-V-E | 63 | AR16 | 60 | +0.022 / +0.037 | 14.5 |
PSC030-V-E | 100 | AR16 | 60 | +0.022 / +0.037 | 14.5 |
PSC030-V-E | 125 | AR16 | 60 | +0.022 / +0.037 | 14.5 |
PSC050-V-E | 200 | AR12 | 75 | +0.027 / +0.042 | 15 |
PSC050-V-E | 250 | AR12 | 75 | +0.027 / +0.042 | 15 |
PSC050-V-E | 320 | AR12 | 75 | +0.027 / +0.042 | 15 |
PSC080-V-E | 400 | AR16 | 85 | +0.030 / +0.047 | 15.5 |
PSC080-V-E | 500 | AR16 | 85 | +0.030 / +0.047 | 15.5 |
PSC112-V-E | 630 | AR16 | 95 | +0.030 / +0.052 | 17 |
The solid shaft version is designed to handle high torque and precise motion control, making it particularly suitable for applications that require robustness and accuracy. The detailed construction and precise measurements ensure that the gearboxes can withstand significant forces without compromising performance.
For more information or to discuss custom orders, please get in touch with us at [email protected]
Integration and Applications in Robotics
The PSC Series Precision Planetary Gear Units by Schaeffler are designed to seamlessly integrate into robotic systems, providing the high performance and reliability required for advanced robotic applications. These gear units offer exceptional precision, rigidity, and efficiency, making them ideal for various robotic uses ranging from industrial automation to service robots.
Mechanical Compatibility and Mounting Options:
The PSC Series gear units are engineered with a range of mounting options to ensure mechanical compatibility with various robotic platforms. The gearboxes can be easily integrated into robotic arms, joints, and other moving parts, thanks to their compact design and versatile mounting kits. The available configurations include solid shaft and hollow shaft versions, catering to different mechanical requirements:
- Solid shaft version – ideal for applications requiring high torque and rigidity. This version ensures a robust connection to the robotic components, minimizing deflection and maintaining precise positioning.
- Hollow shaft version – this configuration is particularly useful for robots that require cable routings through the gear unit, such as articulated arms and collaborative robots (cobots). The hollow shaft allows for the passage of electrical cables, pneumatic lines, or hydraulic hoses, simplifying the design and reducing external clutter.
Electrical and Control Integration:
The integration of PSC Series gear units into robotic systems extends beyond mechanical aspects. These gear units are designed to work seamlessly with various motor types and control systems commonly used in robotics. The high precision and low backlash of the gear units ensure accurate transmission of motion commands, enhancing the overall control and performance of the robot.
- Servo motors – the gear units can be paired with servo motors to achieve precise control over speed and position. The high torsional rigidity and low backlash of the PSC Series ensure that the servo motors can operate at their full potential, providing smooth and accurate motion.
- Stepper motors -when integrated with stepper motors, the gear units help in maintaining consistent torque output and precise positioning, which is essential for tasks requiring repetitive and accurate movements.
- Advanced control systems – the compatibility with advanced robotic control systems allows for seamless integration of the PSC Series gear units. The precise feedback provided by the gear units’ low backlash and high rigidity improves the accuracy of motion control algorithms, enhancing the robot’s performance in complex tasks.
Applications in Robotics
Industrial Robotics:
In industrial robotics, the PSC Series gear units are widely used due to their ability to handle high loads and maintain precision over long operating periods. They are essential components in the following applications:
- Robotic arms and manipulators – the high torque and rigidity of the PSC Series gear units make them ideal for robotic arms and manipulators used in assembly lines, welding, and material handling. The precise motion control ensures accurate placement and manipulation of objects.
- Automated guided vehicles – the gear units contribute to smooth and precise navigation, enabling the vehicles to follow predefined paths accurately and handle varying load conditions without compromising performance.
- CNC machines and automated machining – the PSC Series gear units provide the necessary precision and rigidity for CNC machines and automated machining centers, ensuring high-quality production with minimal errors.
Service Robotics:
Service robots, which operate in environments ranging from healthcare to domestic applications, benefit significantly from the integration of PSC Series gear units. The gear units provide the necessary performance characteristics for tasks that require both precision and reliability:
- Medical robots – in medical applications, such as surgical robots and diagnostic machines, the gear units ensure precise control and smooth operation. The low noise generation and high efficiency are particularly beneficial in sensitive environments.
- Cleaning and maintenance robots – for robots used in cleaning and maintenance, the robust design and high efficiency of the PSC Series gear units ensure long operational life and reliable performance, even in demanding conditions.
- Entertainment and educational robots – in the entertainment and educational sectors, the gear units enable robots to perform complex movements and interactive tasks with high precision, enhancing user experience.
Collaborative Robots (Cobots):
Collaborative robots, designed to work alongside humans, require gear units that offer both high performance and safety. The PSC Series gear units meet these requirements through their precise control and ability to handle varying loads and forces:
- Assembly and inspection – in collaborative assembly and inspection tasks, the gear units ensure that the cobots can perform delicate operations with high accuracy and repeatability.
- Pick-and-place operations – the high precision and low backlash of the gear units make them ideal for pick-and-place operations, where precise positioning and handling of objects are crucial.
Emerging Technologies and Future Trends:
The PSC Series gear units are also well-suited for emerging technologies and future trends in robotics, such as:
- Autonomous vehicles – the precision of the gear units enhances the performance of autonomous vehicles, providing accurate control over steering and movement.
- Advanced AI and machine learning applications – in robotics powered by AI and machine learning, the gear units provide the necessary precision and control to execute complex algorithms and tasks with high accuracy.
- Integration with IoT – the compatibility with Internet of Things (IoT) devices allows for real-time monitoring and control of the gear units, enabling predictive maintenance and optimization of robotic systems.
You can order Schaeffler’s PSC Series gear units and other precision products from Pacific International Bearing Sales. By selecting from our comprehensive online shop, you can ensure you are equipping your robotic systems with the best in precision engineering.