Humanoid robots are designed to perform movements similar to those of the human body. Humanoid robots are increasingly used in manufacturing, healthcare, and research. Numerous bearings are employed for the efficient function and reliability of the robot.
In robotic systems with multiple degrees of misalignment proper bearing selection is essential for optimal performance. Bearings are integral in hip, knee, and ankle mechanisms, where even minor inefficiencies in rotational movement can compromise balance and energy efficiency.
For manufacturers developing humanoid robots, the choice of bearings directly impacts cost benefit, performance, longevity, and operational efficiency. PIB Sales, a supplier of precision-engineered bearing solutions, provides components designed to withstand continuous motion cycles, high loads, and extreme operating conditions.
This article examines how bearings influence humanoid robot performance in motion control. We can offer key bearing selection criteria, and the latest bearing innovations for improving robotic efficiency.
What Is a Humanoid Robot? Understanding Robotic Motion
Humanoid robots are highly complex systems that replicate human movement, interaction, and adaptability. Unlike industrial robots, which are optimized for repetitive tasks in structured environments, humanoid robots must navigate unpredictable spaces, maintain balance, and manipulate objects dynamically. Achieving this level of autonomy and control requires advanced mechanical engineering, sophisticated motion control strategies, and continuous adaptation to external conditions.
One of the primary engineering challenges in humanoid robotics is replicating human biomechanics with artificial components. The human body is an extremely efficient mechanical system that uses over 650 muscles and 206 bones to distribute forces effectively while moving with minimal energy expenditure. In contrast, humanoid robots rely on actuators, motors, and rigid mechanical structures, which lack the natural flexibility and energy efficiency of biological systems. Engineers have developed hybrid actuation mechanisms, such as those seen in the RH5 humanoid robot, which integrates series-parallel hybrid actuators to reduce weight while enhancing structural stiffness and dynamic performance. This system allows the robot to handle payloads of up to 5 kg in each hand, significantly improving its ability to perform real-world tasks.
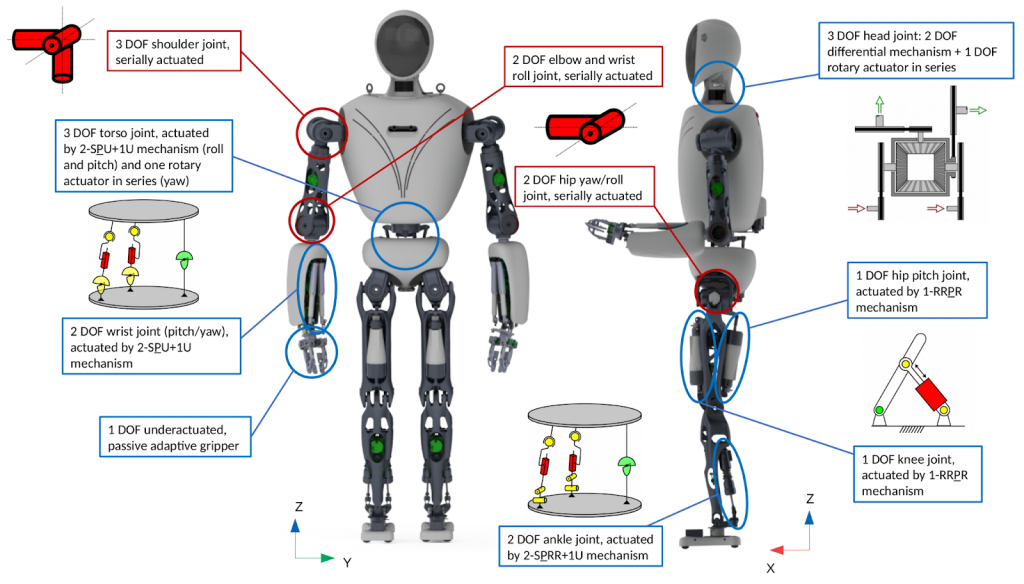
Another significant challenge is achieving stable bipedal locomotion. While wheeled robots maintain constant contact with the ground, humanoid robots must dynamically shift their center of gravity with each step. This process requires advanced zero-moment point control algorithms, which help maintain stability by ensuring that the robot’s weight remains within its support base. Modern humanoid robots utilize Model Predictive Control frameworks, which predict future states and optimize movement parameters in real time. These systems allow robots to adjust their walking patterns dynamically, maintaining stability even on uneven terrain.
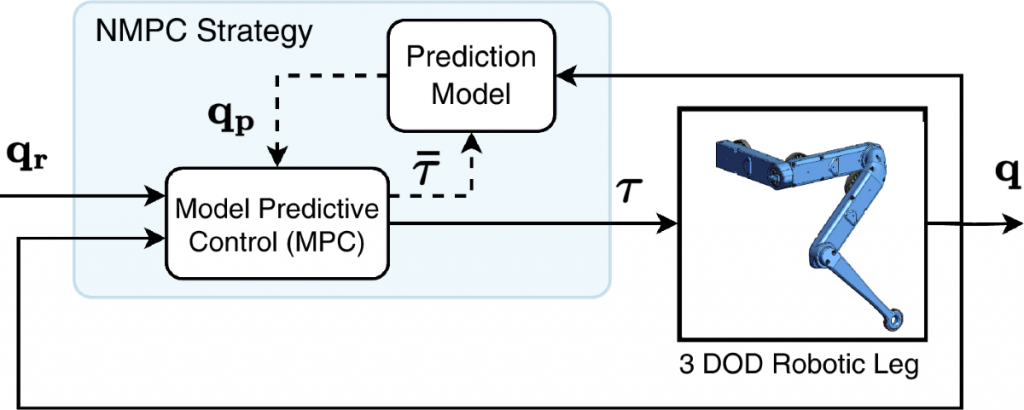
However, motion control alone is not enough — humanoid robots must also interact with their surroundings and manipulate objects with precision. Human hands, with 27 degrees of freedom, allow for highly adaptive grip strength, precise micro-adjustments, and real-time tactile feedback. Most robotic hands lack this level of sophistication, making fine motor control a major challenge. To improve robotic dexterity, engineers have developed:
- Force-sensitive actuators and artificial tendon systems, allow humanoid robots to grasp and manipulate objects more effectively.
- Tactile sensors and reinforcement learning algorithms, enable robots to learn from human demonstrations and refine their grip strategies over time.
Perception is another critical component of humanoid robotics. For a robot to interact effectively with its surroundings, it must process vast amounts of data in real time. Modern humanoid robots rely on computer vision, depth sensing, and LiDAR technology to construct an accurate representation of their environment. These systems enable robots to recognize objects, anticipate motion patterns, and adjust their actions based on sensory input. The integration of machine learning-based perception algorithms has further improved adaptability, allowing robots to make real-time decisions based on complex environmental variables.
Despite these advancements, several challenges remain:
- Energy efficiency continues to be a major hurdle, as humanoid robots generally consume far more power per step than the human body. Research is ongoing to develop low-energy actuation systems and optimized power distribution models to address this issue.
- Mobility and dexterity improvements are still needed, as humanoid robots lack the flexibility, natural fluidity, and responsiveness of human motion. Emerging technologies, such as neuromorphic computing and bio-inspired robotics, aim to bridge this gap by enhancing humanoid systems’ real-time adaptability.
Humanoid robots represent a convergence of mechanical engineering, artificial intelligence, and sensory feedback systems. As advancements in actuation, motion control, and machine learning continue to drive innovation, humanoid robots are becoming increasingly capable, efficient, and applicable across various industries. Their potential to assist in healthcare, manufacturing, and research underscores the importance of continued development in robotic motion and control technologies.
The Role of Bearings in Humanoid Robot Performance
Humanoid robots rely on precision bearings to achieve smooth motion, stability, and long-term reliability. Bearings serve as the critical interface between moving parts, enabling rotation, load distribution, and friction reduction. Without these components, the complex articulation required in humanoid joints, actuators, and linkages would be impossible. Manufacturers such as THK, IKO, and others have developed specialized bearing solutions tailored to meet the demanding requirements of robotic applications.
In humanoid robots, bearings must address specific challenges, including high axial and radial loads, continuous rotational movement, and misalignment compensation. The choice of bearing type significantly impacts the robot’s performance in terms of efficiency, durability, and precision. For instance, crossed roller bearings (CRBs) from manufacturers like IKO are known for their ability to handle large axial, radial, and moment loads simultaneously while maintaining a compact design.
Motion control and load management
The effectiveness of a humanoid robot’s motion control system depends heavily on the performance of its bearings. Joints such as hips, knees, and elbows experience complex multi-directional forces, requiring bearings with exceptional load-handling capabilities. For example:
- IKO Crossed Roller Bearings eliminate the need for separate radial and thrust bearings by combining their functions into one unit. This not only saves space but also reduces weight, which is critical for maintaining a humanoid robot’s energy efficiency.
- Four-point contact bearings are another example, designed to handle radial and axial loads in both directions. They are often used in robotic actuators, allowing for compact and cost-effective solutions
Bearing type | Load type supported | Key application | Example product |
Crossed roller bearings | Radial, axial, moment loads | Joint articulation | IKO CRB50050, THK RA20013, NSK RA7008, Hiwin CRB25 |
Four-point contact | Radial, bidirectional axial loads | Rotary actuators | THK HCR Series, SKF QJ1244, NSK QJ1020, NTN QJ328 |
Deep groove ball | Radial, limited axial loads | Linear actuators | NTN 6805 LLU, SKF 6205, NSK 6008DU, FAG 6208-C-2HRS |
Angular-contact ball | High axial loads in one direction | Robotic wrists and arms | SKF 7210 BECBM, NSK 7205A, NTN 7010C, Timken 2MM207WI |
Spherical plain bearings | Misalignment Compensation | Linkages and joint assemblies | IKO GE15ES, SKF GEZ100ES, Timken GE30 KRRB, THK SB25 |
RNN bearings | Heavy axial loads, compact design | High-torque rotary actuators | NSK NN3010K, SKF NN3022K, FAG NNCF5032V, IKO NART40VR |
The table highlights specific product examples and their use cases, offering engineers insights into selecting bearings that meet the needs of humanoid robotic systems.
Compact design and integration
Space constraints in humanoid robots demand bearings that are not only efficient but also compact. For instance, linear actuators often incorporate deep groove ball bearings, which provide high precision and low clearance in tight spaces. Meanwhile, spherical plain bearings are used in linkage systems to manage misalignment, ensuring smooth motion across multiple degrees of freedom.
Manufacturers such as THK offer linkage components like Dog Bone assemblies, which integrate spherical bearings at each connection point. This reduces wear caused by misalignment and improves the robot’s overall reliability.
Maintenance-free operation
Minimizing maintenance requirements is essential for humanoid robots operating in remote or inaccessible environments. Bearings with self-lubricating properties, such as IKO’s maintenance-free spherical plain bearings, help achieve consistent performance over thousands of cycles without degradation. This is particularly important for robots designed for long-term deployment in hazardous or industrial applications.
- Bearings with integrated seals further extend lifespan by protecting internal components from dust, debris, and contaminants.
- Seals such as those in THK’s SRB series also prevent lubricant loss, ensuring consistent motion performance even in high-friction environments.
Balancing clearance and torque
Proper clearance and torque balance are vital for maintaining precision in humanoid robotics. Excessive clearance leads to vibrations and misalignment, while too little torque can result in excessive energy consumption. To optimize this balance, advanced bearings are designed to provide:
- Bearings like SKF’s angular-contact ball bearings are engineered for consistent positioning accuracy, ensuring precise movements in robotic arms and wrists.
- Reducing friction not only enhances energy efficiency but also prolongs the lifespan of the bearing and the robot itself.
This interconnected approach — combining motion control, compact design, maintenance efficiency, and torque optimization — ensures that humanoid robots can perform their tasks reliably in diverse conditions. By selecting the right bearings, manufacturers can achieve significant improvements in performance, durability, and cost efficiency, supporting the development of next-generation robotic systems.
To explore and order all types of bearings designed for humanoid robots, visit the PIB Sales Shop and browse their extensive selection of high-performance components.
Key Factors in Selecting Bearings for Humanoid Robots
The success of humanoid robots depends significantly on selecting the right bearings. These components handle complex loads, ensure precision motion, and enable durability in challenging conditions. Below are the essential factors to consider when choosing bearings for humanoid robots, presented concisely while retaining their technical importance.
Load-bearing and precision motion
In humanoid robots, joints such as hips, knees, and elbows experience multi-directional forces — a combination of radial, axial, and moment loads. Bearings must not only handle these forces but also enable precise and stable movement.
For example, IKO Crossed Roller Bearings (CRBs), like the CRB50050, are designed to combine radial and thrust bearing functions in a single unit, saving weight and space while ensuring excellent load support. Similarly, angular-contact ball bearings, such as SKF 7210 BECBM, are ideal for robotic arms, offering high axial load capacity and the rigidity needed for fine motion control.
Space efficiency
Humanoid robots require compact components to fit into tight design spaces, particularly in areas like wrists and necks. Bearings need to provide high performance while minimizing size and weight.
Thin-section bearings, such as the Kaydon Reali-Slim® series, are specially designed to optimize space while maintaining strength. Meanwhile, four-point contact bearings, like the NSK QJ1020, can support axial and radial loads in both directions, making them versatile and space-saving solutions for actuators and joint mechanisms.
Durability and maintenance-free operation
Humanoid robots are often deployed in environments where regular maintenance is impractical. To ensure consistent performance over long periods, bearings with self-lubricating or sealed designs are essential.
For instance, IKO GE15ES spherical plain bearings eliminate the need for frequent lubrication, reducing downtime. Bearings with integrated seals, such as those in the THK SRB series, protect internal components from contaminants like dust and moisture, extending their operational life even in harsh environments.
Friction reduction and high-speed capability
Dynamic tasks, such as logistics or healthcare assistance, require bearings that minimize friction and support high-speed motion. Low-friction designs improve energy efficiency and reduce heat buildup, ensuring long-term reliability.
Deep groove ball bearings, like TPI 6805 LLU, provide smooth operation at high speeds, making them ideal for rotary and linear actuators. For even greater efficiency, hybrid ceramic bearings combine reduced friction with superior heat dissipation, maintaining performance under prolonged use.
Adaptability to misalignment and variable loads
In real-world scenarios, humanoid robots encounter uneven surfaces and dynamic load changes. Bearings must adapt to these conditions to ensure reliable operation.
Spherical plain bearings, such as SKF GEZ100ES, are designed to handle misalignment effectively, ensuring smooth motion in robotic joints. Advanced linkage systems, like THK Dog Bone assemblies, incorporate spherical bearings to absorb stresses from dynamic movements and reduce wear on components.
Get the Right Bearings for Your Robotics Applications
Precision bearings are at the core of every high-performance humanoid robot. The right selection ensures smooth motion, load stability, and long-term reliability, making all the difference in robotic efficiency. Whether it’s crossed roller bearings for joint articulation, self-lubricating spherical bearings for maintenance-free operation, or thin-section bearings for compact spaces, each component plays a crucial role in enabling advanced robotic movement.
A wide range of high-precision bearings from IKO, THK, SKF, TPI, and other leading manufacturers is available for robotic applications. These bearings are engineered to withstand high loads, dynamic forces, and continuous operation, ensuring optimal performance in complex environments.
To find the perfect bearing solutions for humanoid robots and other advanced automation systems, explore the PIB Sales Shop. A full selection of robotics-grade bearings is available, with expert support to help you choose the ideal components for your project. Get the reliability and precision your robot needs — shop now or contact us directly for tailored recommendations.