Humanoid robots depend on precision and smooth operation to replicate human-like movements. Bearings are important in ensuring joint efficiency, reducing friction, and supporting high loads — all critical for creating fluid and reliable robotic motion. Engineers designing these systems understand that the wrong bearing choice can lead to inefficiencies, increased wear, and shortened operational life.
For professionals seeking long life and reliability, PIB Sales offers a wide selection of quality bearings tailored to the demands in robotics. With offerings like robot joint bearing design guides, we provide insights and products to help engineers elevate performance. Let’s explore how advanced bearings are driving breakthroughs in humanoid robotics.
Importance of Motion Systems in Humanoid Robots
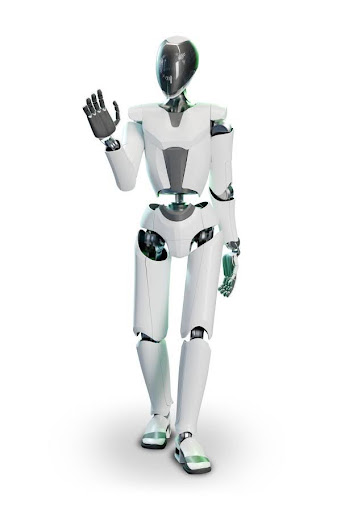
The role of motion systems in humanoid robots cannot be overstated, as they are vital for enabling lifelike movement and functionality. These systems are tasked with replicating complex human motor functions, such as walking, grasping objects, maintaining balance, and transitioning between postures. Achieving such high-performing motion requires exceptional precision, agility, and long-term reliability. Bearings, as integral components of motion systems, are fundamental to ensuring smooth operation, reducing energy loss, and enhancing durability in repetitive and complex tasks.
In humanoid robots, motion systems facilitate balance through the smooth actuation of joints and limbs, crucial in dynamic environments where the robot must respond to uneven surfaces or external perturbations. For example, the bearings used in knee joints support rotational and axial loads, ensuring fluid movement and proper weight distribution during walking or running. Similarly, shoulder and wrist bearings allow for dexterous arm and hand movements required for manipulating tools or performing delicate tasks. These components must combine precision with robustness to handle continuous stress from prolonged operational cycles, often with extremely tight design tolerances.
Key challenges in motion systems include optimizing precision, minimizing wear, and ensuring durability against mechanical stress. The bearings used must deliver high-load capacity while maintaining minimal friction, which is essential for maintaining energy efficiency and reducing heat generation. For instance, advanced crossed roller bearings, such as the IKO CRBF series, are engineered to excel in applications demanding precise movement under complex loading conditions. Their unmatched ability to support radial, axial, and moment loads within a single bearing makes them uniquely suited for humanoid robotics. In these robots, where joints and actuators must achieve a fine balance between agility, strength, and compactness, the CRBF series bearings address multiple challenges simultaneously.
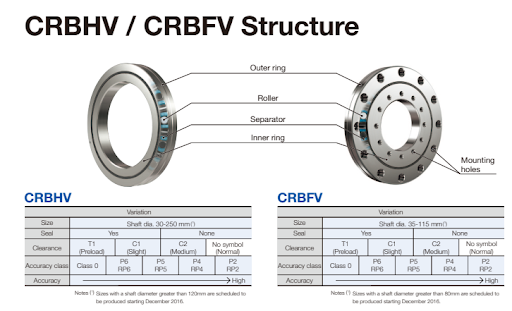
Let’s look at specific configurations in the CRBF series:
Model | Shaft Dia (mm) | Seal options | Accuracy class | Load support (Dynamic/Static) | Preload variations |
CRBFV | 35–115 | Yes / None | P2 to P6 | Dynamic: Up to 240 kN / Static: 490 kN | T1, C1, or C2 |
CRBHV | 30–250 | Yes / None | P2 to P6 | Dynamic: Up to 320 kN / Static: 620 kN | T1, C1, or C2 |
The CRBFV models are especially useful in humanoid robots with smaller joint requirements, while the CRBHV bearings are ideal for supporting the main joints, such as knees, where higher loads and extended motion cycles exist.
By implementing the IKO CRBF series, engineers can overcome common limitations in humanoid robot motion systems, such as jerky movements, inefficient energy use, and mechanical failures. These bearings deliver exceptional precision and reliability, ultimately empowering robotic systems to achieve a new standard of agility and performance.
In humanoid robots, joint actuators are subjected to multi-directional forces generated by dynamic motion, external loads, and weight redistribution during tasks like walking or carrying objects. The IKO CRBF series is specifically designed to handle such conditions. These bearings utilize rollers arranged at a 90° angle, which allows them to effectively bear radial loads, axial thrust, and moment loads with greater efficiency than conventional bearing options.
For example:
- Radial Loads: Applied during rotational movements of the wrist or ankle.
- Thrust Loads: Most apparent in the knees and elbows when supporting the robot’s arm or leg motions.
- Moment Loads: Encountered during sharp angular movements, such as a robotic arm extending outward while maintaining a heavy load.
By supporting all these load types simultaneously, the CRBF series eliminates the need for multiple bearings, which simplifies design integration and reduces joint complexity. This leads to space savings and lighter overall robotic structures — key advantages in humanoid robot development.
Access our catalog for tailored options at PIB Sales.
Role of Bearings in Humanoid Robot Motion Systems
Bearings are indispensable components in humanoid robot motion systems, ensuring precision, durability, and efficiency in critical operations. Among various bearing types, crossed roller bearings stand out for their ability to handle complex robotic joint requirements where multi-directional loads, compact design, and high rigidity are essential. Designed for advanced applications, the IKO crossed roller bearings (CRBF, CRBH, CRBS, etc.) provide the structural, precision, and load-handling features needed to replicate human-like movements effectively.
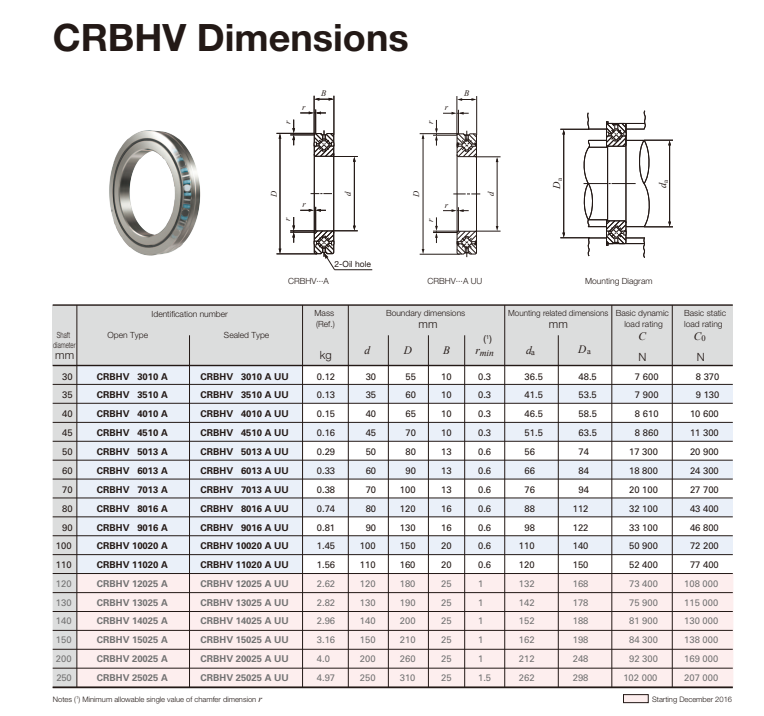
Here is an in-depth look at the role of advanced crossed roller bearings in humanoid robotics, focusing on their unique features, performance, and mounting methodologies.
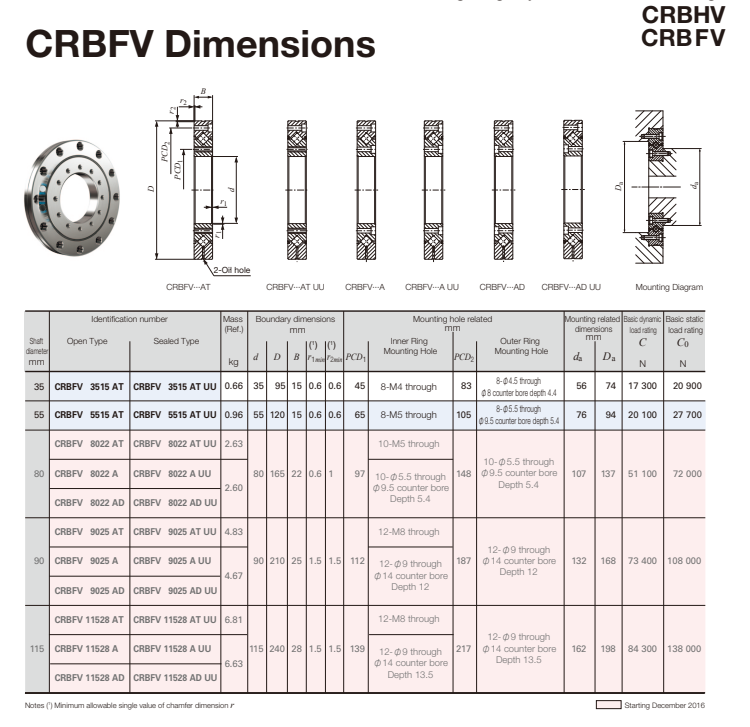
The diverse range of crossed roller bearings from IKO is tailored to meet specific design criteria in applications such as humanoid robot joints and actuators. Below is a detailed table showcasing the three main types of crossed roller bearings relevant for humanoid robots (as depicted in the image):
Application in Humanoid Robots:
- High rigidity type Crossed Roller Bearings: ideal for joints under high dynamic loading, such as shoulders or hips, where stability is critical.
- Slim type: suited for compact applications like wrist actuators or dexterous hands, where minimal bearing width is necessary for tight installations.
Multi-directional load handling
Crossed roller bearings are unique in their ability to simultaneously handle radial, axial, and moment loads, making them highly effective in humanoid robot joints subjected to dynamic forces. For applications such as knees or ankles, these bearings eliminate the need for multiple bearing types.
The cylindrical rollers positioned in a 90° angular orientation ensure a uniform distribution of forces, providing:
- Radial Load Support during actions like rotation or pivoting.
- Axial Thrust Handling while carrying or lifting loads.
- Moment Load Stability during movements requiring bending or twisting in joints.
This feature reduces excess component volume, enabling engineers to design more compact and integrated systems for humanoid robots.
Structural Benefits of Crossed Roller Bearings
The robust inner ring and outer ring construction of crossed roller bearings enhances both durability and operational stability in humanoid robots. For example:
- IKO CRBH High Rigidity Bearings are designed with unified inner and outer rings, providing extreme rigidity even under vibration or impact forces, such as sudden shifts in balance.
- The thin-profile CRBS series ensures reduced material weight, critical for improving the energy efficiency of lightweight humanoid robots.
The incorporation of separators or cages between rollers minimizes frictional contact, further improving motion smoothness and reducing heat generation. This is particularly beneficial for joints like wrists or elbows that experience constant operational stress.
Mounting Methods for Simplified Integration
The proper mounting of crossed roller bearings is essential for ensuring their performance in humanoid robotics. Two primary mounting options are common in high-performance bearings like IKO’s:
Methods
- General Crossed Roller Bearings. These bearings typically require housings and fixing plates to secure them in place. While effective, this method often necessitates additional space and complex designs.
- High Rigidity Type Bearings. These support direct mounting to the system for easier installation in space-constrained areas. This is particularly useful in humanoid robots where minimizing assembly bulk is essential.
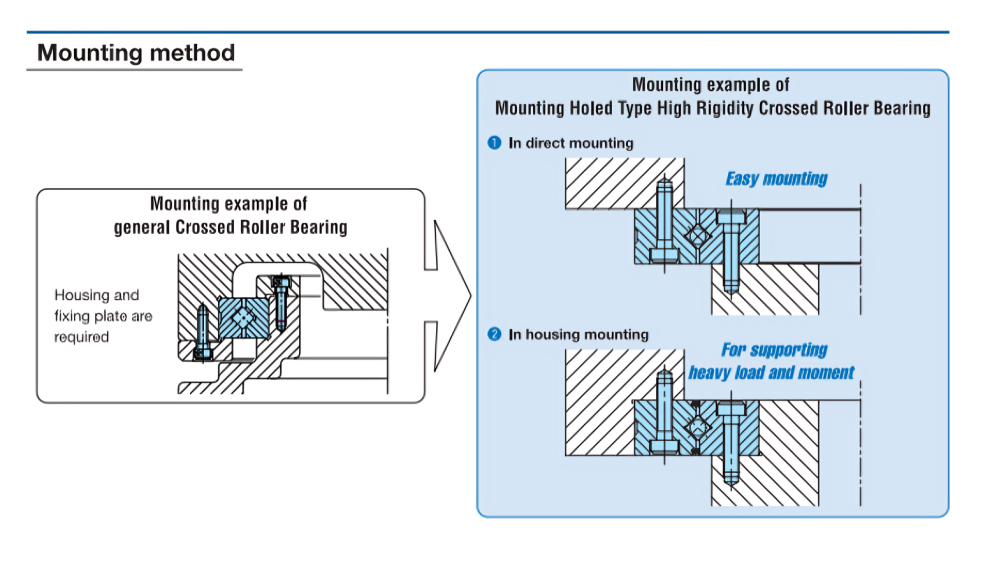
Identification and Configuration: Ensuring Precision
To meet the design needs of humanoid robots, crossed roller bearings like the CRBF series are available in various configurations with customizable features. The example number codes in the chart below clarify the identification system used to specify bearing parameters:
Bearing identification numbers
For instance:
CRBF 80 22 A UU C1 P6
CRBF = Model code.
80 = Bore diameter of 80 mm.
UU = Sealed on both sides to eliminate contamination risks.
C1 = Slight clearance adjustment for high-contact performance.
P6 = High precision class ensuring motion accuracy.
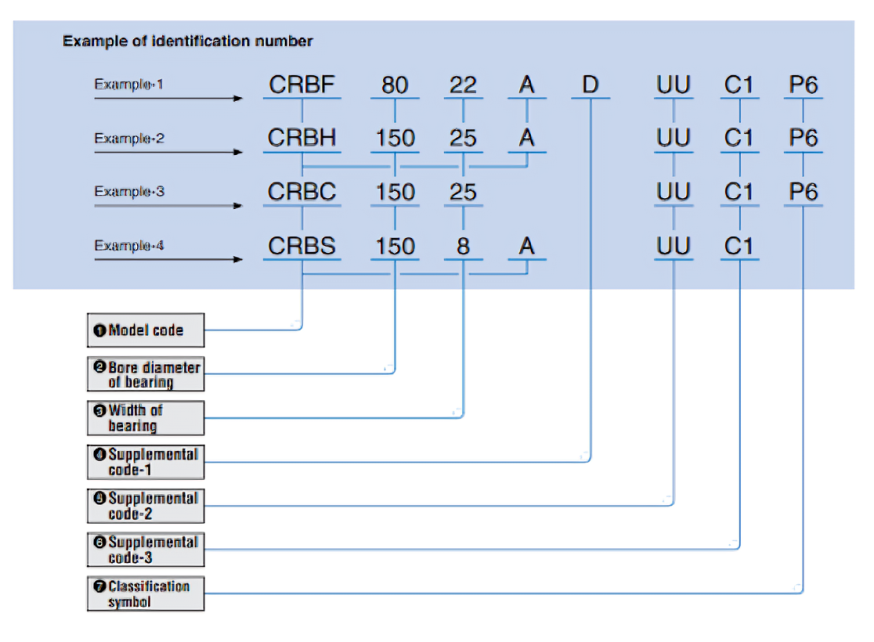
Such customization ensures that bearings meet the required load factors, precision, and environmental operating conditions for humanoid robotics.
With solutions like the IKO CRBH and CRBS series, crossed roller bearings play a transformative role in advancing humanoid robots, aligning their design with practical needs and long-term reliability.
Need a custom bearing solution? Start a consultation with PIB Sales.
Improving Motion Systems with Advanced Bearings
In humanoid robots, motion systems demand high levels of precision, durability, and efficiency to replicate lifelike actions. Bearings, as the cornerstone of these systems, provide the critical support needed to reduce friction, handle complex loads, and ensure long-term reliability. Advanced bearings, particularly crossed roller bearings like the IKO CRBF series, have a transformative effect on motion optimization, directly enhancing robot capabilities. This section will delve into specific improvements linked to efficiency, durability, precision, and maintenance.
Optimizing for efficiency
Efficiency in robot motion systems is essential, particularly in humanoid robots operating in energy-conscious applications such as industrial automation or service environments. Bearings designed with low-friction properties play a pivotal role in improving energy utilization and reducing overall heat generation.
- Energy savings with low-friction bearings
Robots expend significant energy to overcome rotation resistance in joints. Advanced crossed roller bearings minimize this resistance through optimal surface polishing, high-quality separators, and precision-aligned rolling elements.
For instance, bearings with advanced surface treatments and coatings reduce friction coefficients to nearly 40% lower than traditional bearings. As a result, energy consumption in actuators operating under load-intensive conditions decreases significantly.
- Extended hardware lifespan
Reduced frictional forces result in lower heat production, which limits material wear and failure risks. This directly leads to longer component lifespans in critical joints, such as the robot’s hips, knees, or shoulders.
For humanoid robots operating 24/7 in industrial or rehabilitation tasks, using low-friction bearings translates to increased duty cycles, meaning the joints retain performance for extended periods without frequent replacements or repairs.
- Smoother motion
Reduced friction also equates to smoother motion transitions. Humanoid robots achieve finer control over balance and posture while exhibiting lifelike movements. For example, a wrist joint powered by low-friction crossed roller bearings ensures smooth, continuous motions during operations like object manipulation.
Enhancing durability
Humanoid robots are subjected to repetitive stress cycles and demanding mechanical loads, particularly during tasks such as walking, climbing stairs, or lifting objects. Advanced bearing materials are critical for ensuring durability under high-impact scenarios.
- High-Performance Materials
Bearings made from advanced materials, such as ceramic composites or hybrid configurations (steel and ceramic), stand out for their resistance to wear and thermal expansion.
Ceramic bearings, for instance, are 60% lighter than steel, reducing the overall weight of robotic joints while maintaining comparable strength. Their non-corrosive nature also makes them ideal for robots operating in moisture-prone or chemically active environments.
- Impact resistance
Robots involved in dynamic maneuvers, such as jumping or rapid repositioning, demand bearings capable of withstanding sudden force loads. The rigidity offered by high-grade crossed roller bearings ensures minimal deformation under such impacts, contributing to consistent performance over time.
Improving precision
Precision is a non-negotiable requirement in humanoid robotics, where minute errors in joint angles or rotations can disrupt delicate tasks such as using tools, grasping objects, or interacting with humans. Bearing with tighter manufacturing tolerances addresses these challenges directly.
- Tighter tolerances for motion accuracy
Crossed roller bearings like the IKO CRBF series maintain high precision with tolerances as fine as P2 class (<2 µm deviation). This ensures exact alignment in rotating or oscillating systems, essential for robotic joints performing synchronized multi-axis movements.
In humanoid robots, this precision translates to more predictable motion behavior, which is necessary for performing fine motor tasks such as threading a needle or assembling small mechanical components.
- Enhanced fine motor skill execution
Humanoid robots incorporating high-precision bearings can excel in tasks requiring dexterity, such as healthcare robots handling surgical instruments or industrial robots assembling fragile objects.
For example, wrist and hand actuators with ultra-precise bearings achieve sub-millimeter accuracy, allowing robots to manipulate objects with human-like coordination.
Precision-focused bearings elevate overall system competency, enabling humanoid robots to handle real-world complexities with greater ease and reliability.
Minimizing maintenance needs
Humanoid robots must operate with minimal downtime, particularly in commercial and critical applications like caregiving or hazardous environment handling. Bearings designed with self-lubricating or advanced lubrication technologies ensure smoother operation while reducing the need for frequent maintenance interventions.
- Self-lubricating bearings
Bearings with self-lubricating materials or integrated grease retention systems extend operating lifecycles by eliminating lubrication-related wear.
For instance, some bearings achieve up to 50,000 operational hours without requiring external lubrication — an invaluable feature for robots deployed in hard-to-access areas like hazardous sites.
- Grease-free and maintenance-optimized bearings
Advanced sealed bearings, such as CRBF···UU models, prevent contaminants like dust and moisture from entering, reducing internal wear. These sealed systems ensure prolonged performance while simplifying maintenance routines, as operators do not need to halt processes frequently to service or replace bearings.
- Reduced downtime in assembly robots
A humanoid robot in an assembly line fitted with self-lubricating crossed roller bearings can function continuously for extended shifts without risking joint seizure or lubrication loss. This reliability enhances productivity and ensures smoother workflow integration.
- Ease of integration
Bearing designs for straightforward mounting (e.g., direct mounting in the IKO CRBH series) allow operators to install or replace components quickly, saving time during system maintenance or redesign phases.
Frequently Asked Questions
Whether you’re an engineer looking to understand technical specifications or are simply curious about the mechanics of robotic motion, these answers aim to guide you. Let’s tackle some frequently asked questions.
What role do bearings play in humanoid robots?
Bearings are essential components in humanoid robots, ensuring smooth motion and precise movements. They support rotating and sliding parts, reducing friction and wear to improve overall efficiency. For instance, high-quality precision roller bearings are often used in robotic joints, optimizing load distribution and enhancing durability. If you’re curious about the specifics, this guide on bearing FAQs addresses common technical questions regarding ball bearings and their selection.
How do bearings improve humanoid robot stability?
Smooth and stable motion is critical when humanoid robots perform tasks such as walking or navigating uneven surfaces. Bearing designed for robotics enhances stability by ensuring consistent load dynamics and reducing vibrations. This is particularly crucial in actuators where even minor instabilities could disrupt balance. For more on this, PIB Sales offers products tailored to robotic systems that help maintain operational stability.
What types of bearings are commonly used in robotics?
In humanoid robots, several types of bearings are widely utilized, including:
- Ball Bearings: Ideal for rotating and low-load applications.
- Roller Bearings: Used for high-load, high-precision tasks.
- Thin Section Bearings: Preferred for applications where space and weight are concerns.
- Crossed Roller Bearings: Provide excellent rigidity and support for complex multi-axis movements.
Each bearing type offers specific advantages, depending on its intended application. This page provides more insights into robotic applications and component choices.
How does bearing maintenance impact robot performance?
Proper maintenance greatly affects the performance and longevity of a humanoid robot’s motion systems. Regular lubrication and cleaning prevent premature wear and ensure smooth operation. Advanced materials and design features like sealed bearings can eliminate contamination risks, reducing the need for frequent servicing.
For instance, bearings integrated into joint actuators, like these specialized models, are optimized for such rigorous applications, extending both functionality and lifespan.
Can bearings handle high-load scenarios in humanoids?
Yes, specially designed bearings can manage extreme load conditions without compromising on performance. Components like precision roller bearings or customized crossed roller bearings are engineered to withstand both axial and radial forces. This robustness ensures humanoid robots maintain efficiency and reliability even in demanding tasks.
For additional information on load management strategies and advanced designs in robotics, this resource delves into the technologies enabling these capabilities.
The Bottom Line
Advanced bearings are at the core of improving motion systems in humanoid robots. Their role in enhancing efficiency, durability, precision, and maintenance cannot be overstated. Bearings such as the IKO CRBF crossed roller series empower robots to achieve lifelike movements, extended operational lifespans, and robust reliability, even under high-stress conditions. By integrating such advanced technologies, engineers can design humanoid robots that excel in performance, enabling them to meet the evolving demands of industries ranging from healthcare to manufacturing.
Collaborating with trusted suppliers is essential to finding tailored bearing solutions that meet your robotic system’s unique requirements. Choosing the right partner ensures access to high-quality components, technical expertise, and ongoing support, enabling your projects to succeed both technically and economically.
To explore top-tier bearings designed specifically for robotic systems, visit PIB Sales. As a reliable distributor, PIB Sales offers premium solutions to help engineers optimize robot performance with precision-engineered bearings. Take the next step in advancing your motion systems today!