Optimizing the performance of warehouse robots provides efficiency and productivity for any automated warehousing operation. Achieving full optimization involves the use of high-quality precision bearings in most robotic mechanisms used in warehouse operations.
In this article, we will explore the key considerations in selecting bearings, their role in ensuring smooth and reliable operations, and the best practices for installation and maintenance. Our aim is to equip readers with the necessary knowledge to make informed decisions when selecting and maintaining bearings, ultimately enhancing the efficiency and reliability of their warehouse robot systems.
For humans, the task of picking and placing objects is simple. Robots need to use the most precise components, including bearings along with AI and precision machine actuators to perform the most mundane tasks needed in warehouse operations.
Warehouse operations have expanded astronomically in recent times thanks to the revolution started by Amazon, with thousands of companies now providing JIT picking and shipping around the clock and around the world.
The following are a list of the different types of robotic type equipment needed in a modern warehousing operation:
- Cobots, also known as collaborative robots, are semi-autonomous mobile robots designed to assist or replace human workers performing an array of tasks around the warehouse.
- Articulated robotic arms are pick-and-place robots. They have multi-jointed arms which are used to pick and place products or perform other programmable duties in the warehouse processing area.
- Automated Guided Vehicles (AGVs) help to transport materials, supplies, and inventory within warehouse facilities.
- Automated Storage and Retrieval Systems (AS/RS) refer to a group of computer-controlled systems that help automate inventory management and store/retrieve goods on demand.
- Goods-to-Person (G2P) technology operates on the same principle as an AS/RS system. G2P technology leverages an automated storage system to deliver items to stationary pick stations where human operators fulfill orders.
Benefits of Warehouse Robotics
Savvy companies are leveraging warehouse robotics to improve order fulfillment and better manage inventory while staying ahead of the competition.
Robotic companies like RightHand Robotics are developing the concept of using machine vision and intelligent grippers to make piece-picking robots more adaptable. This approach will reduce the amount of training needed to operate the robots with the goal of equipping each machine with equivalent hand-eye coordination.
Robotics companies are also utilizing an end-of-arm tool that combines suction with novel underactuated fingers, which will give robots more flexibility than their counterparts that rely solely on suction cups or simple pinching grippers.
As warehouse robot improvements are rapidly evolving, specialized bearings become more important. As warehouse robots move into the next phase, precision linear and rotary motion are essential. Warehouse robots will ultimately reduce the number of people doing mundane tasks while people can work in roles like quality control, customer contact, and fulfillment and overseeing the robots.
Understanding Bearings’ Role in Warehouse Robots
Thin section ball bearings are generally used in applications with space, weight, and load constraints like robotics.

Kaydon thin section bearings have many features and benefits for robotics, including:
- Thin cross section. For applications where space is limited, Reali-Slim® thin section bearings provide for a very compact design.
- Lightweight. Reali-Slim® thin section bearings provide significant weight savings, generally resulting in cost savings.
- Low friction
- High stiffness
- High running accuracy
Buy Kaydon bearings from Pacific International Bearing Sales Inc.
RBC Bearings offers a wide variety of thin section bearing styles for demanding robotic applications.
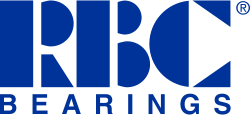
Standard radial ball bearings are designed where when the bore size increases, the width and the thickness of the bearing changes proportionately. Thin section bearings reduce cost because the cross section stays the same when the bore diameter increases, thereby improving design efficiency as compared to standard bearing geometries.
Modern warehouse robotic designs rely on a compact design and less weight. These requirements make thin section bearings an ideal solution.
Standard cross sections range from 3/16 to 1 inche while bore sizes can go up to 40 inches. Stainless steel and other materials are available depending on application needs, and seals are available on all sizes and standard cross sections. Super duplex configurations give added rigidity and can also be applied to all sizes.
For many applications, a four-point contact thin section bearing is used to replace two bearings.
Single Row Radial Ball Bearings
These are the most common type of bearings used in warehouse robots. They utilize balls to minimize friction and enable smooth rotation. A deep groove on each inner and outer ring of the bearing sustains radial and axial loads or combinations of both, making them one of the most versatile and useful types of ball bearings. Single row radial ball bearings are suitable for various applications due to their high load capacity.
Buy TPI bearings in online store Pacific International Bearing.

Roller bearings employ cylindrical or tapered rollers to distribute loads efficiently, making them ideal for handling heavy loads and can accommodate both radial and axial forces. Roller bearings are commonly used in warehouse robots for applications that require high load capacities and shock resistance.
Buy spherical and other roller bearings
INA crossed-roller bearings can be used for high-precision warehouse robotic applications. Crossed roller bearing dimensions conform to ISO dimension series 18 as per DIN 616. The construction of the bearing has outer rings, inner rings, rolling elements, and plastic spacers. The outer ring is split and is held together using three retaining rings.
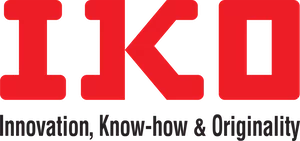
These bearings are designed to support axial forces from both directions as well as radial forces, tilting moment loads, and any combination of loads. Robotic designs needing two bearing positions using crossed roller bearings can be reduced to a single bearing position, which is why crossed roller bearings are rigid and have high running accuracy.
Pacific International Bearings Sales stocks both IKO and INA crossed roller bearings.
Rigid Bearings for Handling Axial Loads
Thrust needle roller bearings have needle type rollers with cages made from surface hardened steel plates.
Thrust needle roller bearings have a rigid structure, good lubricant capacity, and the lowest sectional height of all thrust bearings. They are designed to withstand high-speed rotation while maintaining a low coefficient of friction.
Pacific International Bearings distributes both IKO and INA, as they are the two leading manufacturers of thrust needle type roller bearings.
Thrust bearings are designed to withstand axial loads, making them suitable for applications where there is a need to support heavy loads in a specific direction. They ensure stable and precise movement in warehouse robots, especially during tasks such as pushing or lifting heavy objects.
IKO and INA thrust roller bearings have caged cylindrical rollers. This type of thrust bearing is often specified in applications requiring high accuracy at high speeds and fluctuating heavy loads.
These bearings are designed with a rigid cage to precisely guide the rollers. Thrust roller bearings can handle heavy loads at high rotational speeds.

Application examples include driving mechanisms for robotics, machine tools, and high-pressure pumps.
SKF manufactures super-precision angular contact ball bearings for shaft diameters from 6 to 360 mm, and are readily available from stock at Pacific International Bearing Sales Inc.
Angular Contact Bearings
Angular contact bearings are designed to handle both radial and axial forces simultaneously. They enable robots to operate with high accuracy and precision, making them suitable for applications that require controlled movement and positioning.
Purchase SKF, FAG, or TPI ACBB bearings for your robotics application.

Tapered Roller Bearings
Tapered roller bearings can support large radial and axial forces and are commonly used in applications where there are combined loads. They provide robust performance for warehouse robots operating under heavy-duty conditions. Tapered roller bearings can be customizable in certain circumstances to match your specific needs in areas like speeds, loads, contamination, temperature, and vibration conditions.
Tapered roller bearings consist of a cup and cone assembly. The cup is the outer ring whereas the cone assembly consists of inner ring, rollers, and cage. The two components mate to create the tapered assembly. Tapered roller bearings accommodate combined loads and provide low friction during operation. By adjusting one single row tapered roller bearing against a second tapered roller bearing and applying a preload, the result is a rigid bearing for various applications.
Tapered roller bearings are found in bearing applications where there is a need to increase performance, reduce friction, or increase power density.
In theory, many types and sizes of bearings can be applied in robotic applications depending on the requirement. Working with knowledgeable and experienced suppliers can provide great insight, saving time and money solving complex robotic movement concerns.
Importance of Selecting the Right Bearing for Specific Robot Applications
Choosing the appropriate bearing for a specific warehouse robot application is important for achieving optimal performance and longevity. The right bearing selection ensures smooth motion, minimizes energy consumption, increases its life, and enhances overall efficiency. Failure to select the right bearing can result in decreased robot performance, increased downtime, and potential system failures.
Factors to consider when choosing bearings for warehouse robots include:
- Load Capacity
- Speed and Precision Requirements
- Environmental Factors
- Lubrication Requirements
- Maintenance and Longevity Considerations
Bearing Solutions for Robotic Systems
Different robotic tasks require specific types of bearings to withstand various loads, movements, and environmental conditions. In this section, we will provide guidelines for selecting appropriate bearings based on common robotic applications:
- Joint and Arm Movements
Robotic systems with jointed arms are usually made up of 4 to 6 joints and would be used for several manufacturing applications. They closely resemble a human arm, having a wrist, forearm, elbow, and shoulder. The different joints allow them the required degrees of freedom of movement. These robots require bearings that can handle both radial and axial loads, oscillation movements, and certain degrees of misalignment. Some examples of bearings used in this application include spherical plain bearings, rod end bearings, single row radial ball bearings, and many others. Pacific International Bearing can assist in this selection for your application.
- Conveyor Systems
Conveyor systems in warehouses involve continuous rolling motion. For these applications, deep groove ball bearings or even unground ball bearings are commonly used. These bearings offer low friction, high load capacity, and are capable of handling both radial and axial loads.
- Rotary Actuators
Rotary actuators in robotic systems require bearings that can support high momentum loads and provide smooth rotation. Crossed roller bearings or slewing bearings are commonly employed in such applications. These bearings have a compact design, a high load-carrying capacity, and excellent rotational accuracy.

Slewing bearings have an inner ring and an outer ring, one of which usually incorporates a gear. There are attachment holes in both rings that, when engaged, allow for power transmission with a quick and simple connection with mating machine components.
- Linear Motion Systems
Robotic systems often incorporate linear motion systems for precise positioning and movement. Linear ball bearings or profile rail guides are commonly used in these applications. These bearings offer low friction, high accuracy, and smooth linear motion.
- Articulated Robots
Articulated robots consist of multiple interconnected joints, requiring bearings that can handle complex movements and loads. Combination bearings, such as spherical plain bearings or rod end bearings, are often utilized in articulated robot applications. These bearings allow for articulation, rotation, and oscillation while maintaining stability and load-bearing capabilities.
Conclusion
The adoption of robotics in modern warehouses has revolutionized the logistics industry, bringing forth significant improvements in efficiency and productivity. These automated systems have enabled precise and efficient order picking, streamlined inventory management, and optimized material handling processes. However, it is important to recognize that the performance of warehouse robots relies heavily on the quality and reliability of the bearings they utilize. High-quality bearings play a critical role in ensuring the smooth and optimal operation of warehouse robots.
The selection of appropriate bearings based on specific robotic applications, such as joint and arm movements, conveyor systems, rotary actuators, linear motion systems, and articulated robots is essential. By choosing bearings that can handle the loads, movements, and environmental conditions associated with each task, companies can maximize the performance and longevity of their robotic systems.
Still have a question or need to discuss something? Contact us to get help.