The concept of non-contact bearings traces its roots back to the early 20th century when the theory of magnetic levitation and the utilization of magnetic fields to support loads gained prominence. However, it was not until the latter half of the century that significant advancements in magnetic technology allowed for practical applications of non-contact bearings.
The Principle of Non-Contact Magnetic Bearings
The principle of non-contact magnetic bearings relies on the interaction between magnetic fields and electric currents. The bearing system consists of two main components: a stationary part (stator) and a rotating part (rotor). The stator contains electromagnets, which generate a magnetic field, while the rotor carries permanent magnets or electromagnetic coils.
When an electric current is passed through the stator electromagnets, a magnetic field is created. This magnetic field induces eddy currents in the rotor, which in turn creates an opposing magnetic field. The repulsive or attractive forces between the stator and rotor magnetic fields enable the levitation and stable suspension of the rotor without physical contact.
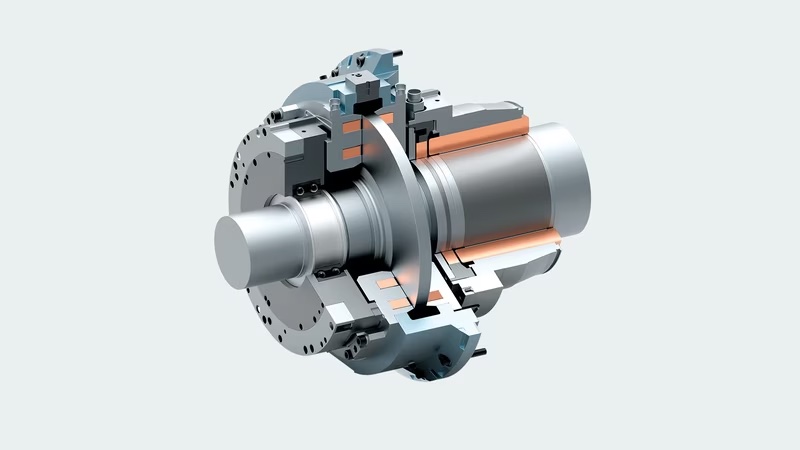
SKF Active magnetic bearings operate without any surface contact thus eliminating bearing friction and wear. Electromagnets generate forces in radial and axial directions to levitate the shaft, allowing contact-free rotation. The SKF control system monitors and adjusts the current in the electromagnets maintaining shaft position. SKF magnetic bearings are very precise and stable. SKF magnetic bearings are useful in a wider operating range than conventional bearings.
SKF magnetic bearings features and benefits:
- Lower maintenance than conventional bearings
- Very high reliability with energy savings
- Free from contamination
- Instantaneous starting and stopping
- Built in controls
Construction Features
Stator Configuration
The stator of a magnetic bearing typically consists of several electromagnets arranged in a circular or annular pattern. These electromagnets are evenly spaced around the circumference and are energized by an external power supply. The number and arrangement of the electromagnets may vary depending on the specific design and application.
Rotor Configuration
The rotor, on the other hand, carries permanent magnets or electromagnetic coils. Permanent magnets are often used in small-scale applications, while electromagnetic coils provide greater flexibility and control in larger systems. The rotor is designed to rotate freely and is supported by the magnetic fields generated by the stator.
Magnetic Field Generation
When an electric current flows through the stator electromagnets, a magnetic field is created around each electromagnet. The magnetic fields generated by the electromagnets are carefully controlled and synchronized to create a stable levitation and suspension system.
Magnetic Field Interaction
The interaction between the magnetic fields of the stator and rotor is fundamental to the principle of non-contact magnetic bearings. When the rotor rotates, the permanent magnets or electromagnetic coils on the rotor induce eddy currents in the surrounding conducting material (such as the rotor itself or additional elements).
Eddy Currents and Magnetic Forces
The eddy currents, in turn, create their own magnetic fields that oppose the magnetic field of the stator electromagnets. These opposing magnetic fields generate repulsive or attractive forces, depending on the specific configuration and control strategy of the magnetic bearing system.
Force Control and Stability
The forces between the stator and rotor magnetic fields are carefully controlled and regulated to maintain stable levitation and rotation. Feedback control systems, such as position sensors and control algorithms, are employed to monitor and adjust the magnetic fields and forces. This allows for precise control and stabilization of the rotor position and orientation.
Control Algorithms
Sophisticated control algorithms are used to dynamically adjust the currents in the stator electromagnets based on feedback from position sensors. These algorithms consider factors such as rotor position, rotational speed, and external disturbances to optimize the stability, performance, and energy efficiency of the magnetic bearing system.
Friction Elimination and Increased Efficiency
Traditional bearings are plagued by friction, which leads to energy losses and reduced efficiency. Non-contact magnetic bearings mitigate this issue entirely, as there is no physical contact between the bearing and the shaft. With friction eliminated, energy consumption is significantly reduced, enabling enhanced efficiency in linear motion systems. Calculations have shown that by replacing mechanical bearings with non-contact magnetic solutions, energy savings of up to 30% can be achieved, leading to increased productivity and reduced operating costs.
Precise Control and Stability
Linear motion applications often require precise control over position, speed, and acceleration. Non-contact magnetic bearings excel at delivering exceptional control due to their inherent stability and responsiveness. These bearings can respond instantaneously to changes in load or external disturbances, allowing for precise positioning and smooth movement. Furthermore, the absence of mechanical contact eliminates the possibility of wear and tear, ensuring consistent performance and long-term stability.
Enhanced Reliability and Maintenance
Traditional bearings are susceptible to wear, leading to frequent maintenance and replacement. In contrast, non-contact magnetic bearings have a significantly longer lifespan and require minimal maintenance. Without physical contact, there is no mechanical wear, resulting in reduced downtime and increased reliability. These bearings are particularly advantageous in critical applications where downtime can have severe consequences, such as in aerospace, medical equipment, and semiconductor manufacturing.
Real-World Applications and Future Prospects
- Power Generation
Non-contact magnetic bearings are extensively used in power generation systems, including gas turbines, steam turbines, and hydroelectric generators. Their ability to operate at high speeds and eliminate frictional losses makes them ideal for these applications. Scientific studies have demonstrated the improved efficiency, reduced maintenance requirements, and enhanced reliability of magnetic bearings in power generation, leading to cost savings and increased overall system performance.
- Industrial Machinery
Non-contact magnetic bearings are employed in a range of industrial machinery, such as high-speed compressors, pumps, motors, and spindles. These bearings offer precise control, reduced vibrations, and enhanced performance, leading to increased productivity and operational efficiency. Scientific research has showcased the benefits of magnetic bearings in terms of energy savings, improved stability, and reduced maintenance costs in industrial machinery applications.
- Transportation Systems
One of the most promising applications of non-contact magnetic bearings is in transportation systems, specifically magnetic levitation (maglev) trains. Maglev trains utilize the repulsive forces of magnetic bearings to levitate the train above the tracks, eliminating the need for traditional wheels and reducing friction. This enables trains to travel at high speeds with reduced energy consumption and minimal maintenance requirements. Scientific studies have demonstrated the feasibility and advantages of magnetic levitation in terms of increased speed, reduced operating costs, and improved passenger comfort.
- Energy Storage
Non-contact magnetic bearings are used in flywheel energy storage systems, where the rotational motion of a flywheel is maintained using magnetic fields. Magnetic bearings enable high-speed rotation with minimal energy losses, making them suitable for energy storage applications. Scientific research has highlighted the benefits of magnetic bearings in terms of high efficiency, fast response times, and prolonged operational lifetimes in energy storage systems.
Future Prospects
The future prospects of non-contact magnetic bearings are promising, driven by ongoing research and technological advancements. Here are some key areas of future development:
- Miniaturization: Researchers are exploring ways to miniaturize magnetic bearings for applications in micro-electromechanical systems (MEMS) and nanotechnology, enabling precise control and stability at a smaller scale.
- High-Temperature Applications: Advancements in magnetic materials and cooling techniques are being pursued to extend the operating temperature range of magnetic bearings, enabling their use in high-temperature environments such as aerospace and energy systems.
- Advanced Control Strategies: Scientists are investigating advanced control algorithms, machine learning techniques, and sensor integration to enhance the performance, reliability, and fault tolerance of magnetic bearing systems.
- Integration with the Internet of Things (IoT): The integration of magnetic bearings with IoT technologies enables remote monitoring, predictive maintenance, and optimization of bearing performance based on real-time data, leading to improved reliability and cost-effectiveness.
Non-contact magnetic solutions have emerged as a groundbreaking technology in the field of bearing engineering, revolutionizing the way machines operate across a wide range of industries. Through the application of high-performance magnets and sophisticated control systems, these innovative bearings offer unparalleled reliability, efficiency, and performance. As research and development continue to push the boundaries of magnetic technology, the future holds even greater potential for non-contact magnetic solutions to transform the industrial landscape, enabling more advanced and sustainable machinery.
Pacific International Bearing offers SKF magnetic bearings for electrically driven centrifugal and Gas storage compressors. SKF magnetic bearings are use in Gas treatment turboexpanders, Gas lift or reinjection compressors, Subsea compressors, Gas transport, Ethylene/Polyethylene and Industrial air compressors, Freon Chillers, Power Generation turbogenerators and pressure let down turbogenerators.
Still have a question or need to discuss something? Contact us to get help.