Pacific International Bearing Sales Inc is a strategic robotics component source for designers and customers. In addition to linear and rotary bearings, we offer Schaeffler robotic system components, precision gearboxes, pivot bearing supports, drive motors, and sensors.
In this article, we feature linear 7th axis solutions featuring Schaeffler, Ewillix, INA, IKO, and NB bearing products.
The 7th axis in Industrial robotic applications refers to the linear movement necessary to travel along another axis other than in 4, 5 or 6-axis machines. Simply the 7th axis allows for robots to move between workstations. Mounted on a linear rail the robot can move along its pathway to perform other tasks. Having a 7th axis replaces the need for additional robots. Providing access with a linear movement adds reach so that smaller more compact robots can be utilized. Linear movements for robotic arms can be accomplished using various linear rails, actuators, ball screws, etc.
As we will discuss in this article Schaeffler offers a plug and play range extender either in a ball screw or belt driven design. In addition to prepackaged range extenders, you have many other choices.
Below are a few precise linear movement options manufactured by NB,IKO and INA, in my opinion, some of the best linear bearing Manufacturers in this field.
NB Linear Actuator BG type is a compact single axis linear actuator that integrates a slide guide and precision ball screw.
The NB Linear Actuator BG type is one example of a very precise method for linear 7th axis movement. The NB design offers a compact design and will outperform conventional Positioning Tables. This is made possible by a unique “U” shaped guide rail and slide block which provides multiple functions of a guide block and a ball screw nut combined into a single unit. Go to Pacific International Bearing Sales for further information.
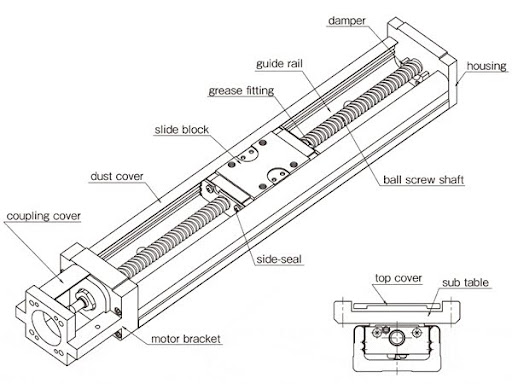
Benefits in using the NB BG type Linear actuator are:
- Reduced installation time
- Needs no adjustment providing an integrated linear slide guide rail and precision ball screws.
- Highly rigid yet in a compact envelope
- Features a unique U-shaped linear slide guide rail and four-point contact
- High accuracy in positioning
- Highly accurate and precision machined components including the linear slide guide rail, linear guide block, and ball screw
- Space-saving design
- BG single-axis linear stage actuators can be used in compact applications
INA Profiled Rail Linear Guides
High-speed KUVE-B-HS profiled rail linear guides offer speeds of up to 10 meters per second without losses in load carrying capacity and rigidity. For further information on INA linear rails contact Pacific International Bearing Sales Inc.
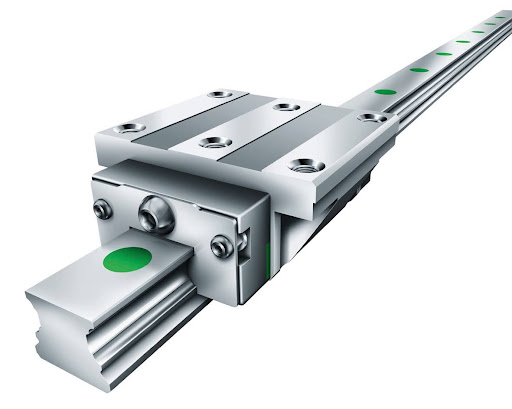
Four, five or six-axis robots are stationary so they operate in a single space so the addition of the 7th axis provides more utility and efficiency.
Over time, robotics advanced from basic machines to complex, multi-axis systems that have revolutionized many industries. Among the advancements, the linear axis has significantly enhanced the reach and precision of robotic arms. Traditional robotic systems have struggled being inflexible and are expensive to maintain.
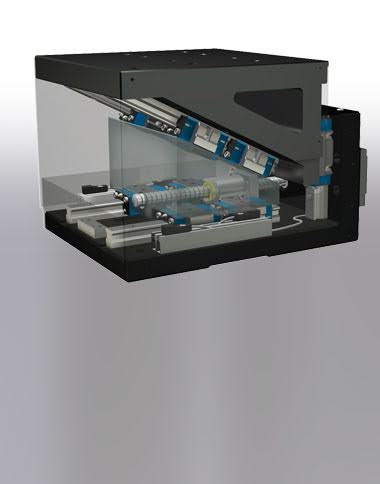
The introduction of adaptable configurations with interchangeable components has brought a new level of versatility and efficiency. These systems can be easily customized and upgraded to meet specific operational needs, reducing downtime and minimizing expenses.
For more information regarding INA robotics solutions.
IKO designs and manufactures a wide variety of specialized tables that serve as reliable positioning mechanisms within industrial equipment and machinery. IKO Linear motion rolling guides are available in rail sizes from 1 to 85 millimeters . IKO linear guides will handle large, heavy loads or fit into space- and weight-constrained robotic devices. They also provide smooth motion, accurate performance and good rigidity to deliver precise, repeatable motion.
IKO Pick and Place Models (NT…XZ)
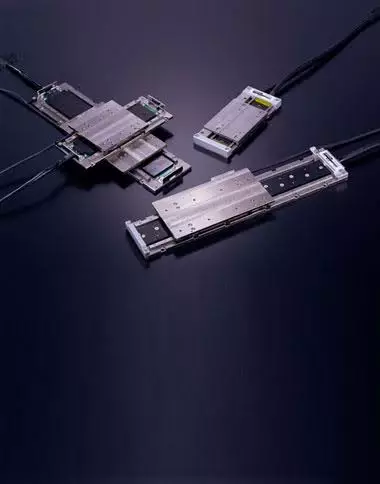
Pick and Place models (NT…XZ) offer maximum thrust of 50 N (x axis) and 25 N (z axis), with stroke lengths of 45 mm (x axis) and 10 mm (z axis). Units feature a super thin profile of just 18 mm. This series uses C-Lube Linear Way ML miniature linear motion rolling guide in the table guiding parts.
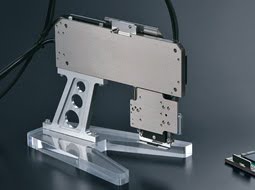
For more information on IKO Pick and Place models go to this link.
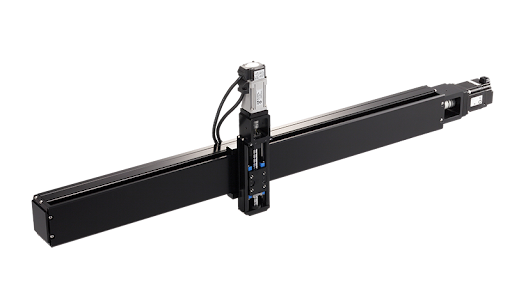
IKO offers many styles and sizes with a range from small to extra large. IKO offers the world’s smallest track rail having a 1-mm width. Other IKO models include those built for high rigidity and load capacity for larger machines.IKO offers roller type rolling guides, ball type rolling guides, ball splines, anti-creep crossed roller ways, ball slides, and both linear and rotary bushings to meet the needs of different robotic applications and machine geometries.
IKO is used extensively in these application examples
- Automobile manufacturing
- Assembly robots
- Welding robots
- Painting robots
- Positioning robots
- Human-collaborative robots (cobots)
- Scalar robots
- Gantry systems
- Warehouse picking, sorting and palletizing systems
- Semiconductor pick and place machines
- Surgical and rehabilitation robots
- Lab automation
More on 7th Axis as a Modular Design Solution
While Schaeffler already offers range extenders as a fully customized seventh axis for lightweight robots and cobots, a solution for industrial robots has not been available. For the most part designs of the 7th axis as a linear solution have been customized.
Schaeffler decided to offer a modular system composed of all the necessary drive components, such as linear guidance systems in the form of a linear recirculating ball or linear recirculating roller bearings along with guideway assemblies and accessories. Schaeffler offers the optional addition of Schaeffler DuraSense for condition monitoring, or automatic, requirement-based minimal lubrication. The range for the seventh axis is complemented by components and systems from the Lifetime Solutions range, including automatic lubricators from the Concept series, suitable lubrication gears for reliable lubrication of the toothed rack, and the new intelligent lubricator OPTIME C1.
Ewellix
In 2023 Schaeffler acquired Ewellix based in Sweden.
Ewellix provides positive solutions to complete vertical and horizontal adjustment in an intelligent way. Ewellix offers a wide range of “ready to mount” linear axis solutions. They are designed for different applications, giving any robot an extended operational range.
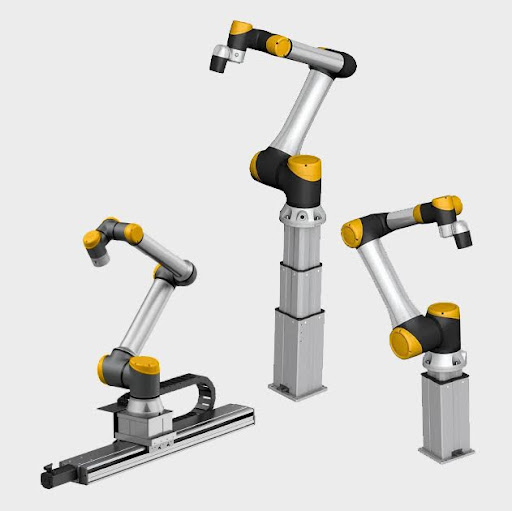
Buy Ewillix linear products from Pacific International Bearing Sales Inc.
Plug-and-Play Ready Range Extender
Schaeffler offers plug-and-play-ready linear modules as a range extender to create significantly larger working ranges for robots. Choose from a triple toothed belt drive or a ball screw drive depending on the application. By using two linear modules from the extensive range of Schaeffler modular systems, X-Z axis systems can be easily achieved for cobots. The extended travel distance in two axes often provides an option of using smaller and lighter robots.
Looking for a strategically ideal partner to supplement your robotics portfolio with configurable and ready-to-assemble linear systems? With no logistical outlay for your company? We have the solution.
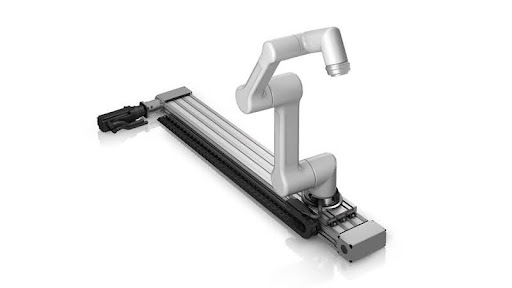
For more information on the Schaeffler Plug and Play range extender please contact us at and visit Ewellix
The 7th axis in robotics, often referred to as the linear or external axis, is an additional degree of freedom that allows a robotic arm to move linearly along a specified path. This axis greatly increases the reach and versatility of robotic systems by allowing movement along a rail or track, extending the robot’s reach beyond its stationary position. Detailed breakdown of its components and operational principles:
The 7th axis operates on the principle of linear motion, providing an extra dimension of movement to the robotic arm. This linear motion is typically achieved through a combination of mechanical components and precise control systems. The fundamental equation governing the linear motion is:
d(t)=v(t)×t+12a(t)×t2
where:
- d(t) is the displacement as a function of time.
- v(t) is the velocity as a function of time.
- a(t) is the acceleration as a function of time.
This equation helps in determining the position of the robotic arm at any given time along the linear path.
The core of the 7th axis is the rail system, which provides a stable platform for the linear movement of the robotic arm. The rail is engineered to handle the dynamic loads and stresses exerted by the moving arm, ensuring smooth and precise travel. Materials like hardened steel or aluminum are commonly used for their strength and durability.
The motor and drive mechanism are crucial for converting electrical energy into linear motion. Servo motors are preferred due to their high precision and ability to provide consistent torque. Typically, servo motors are used due to their precision and control capabilities. The motor’s torque (τ) is given by:
τ=r×F
where:
- τ is the torque.
- r is the radius or the lever arm.
- F is the force applied.
The drive mechanism may involve rack-and-pinion systems, belt drives, or screw drives, each offering unique advantages:
- Rack-and-Pinion: Provides high precision and load capacity.
- Belt Drives: Known for smooth and rapid movement.
- Screw Drives: Offers excellent accuracy for precise positioning.
Accurate control of the 7th axis relies on feedback systems such as encoders and resolvers. These devices provide real-time data on the position and velocity of the robotic arm, allowing the control system to make necessary adjustments. The feedback loop ensures that the arm moves as intended, maintaining precision and reliability.
The control system for the 7th axis integrates with the robot’s main controller. It processes input signals from the feedback devices and adjusts the motor commands to achieve the desired motion. The control algorithm typically employs PID (Proportional-Integral-Derivative) control to minimize error:
u(t)=Kpe(t)+Ki∫0te(τ)dτ+Kd de(t)d(t)
where:
- u(t) is the control signal.
- Kp,Ki, and Kd are the proportional, integral, and derivative gains, respectively.
- e(t)is the error signal.
d and Capacity:
The load capacity of the 7th axis is determined by the mechanical design and the drive system’s specifications. The maximum load (F max) that the system can handle without deformation or failure is given by:
Fmax=σy×ASF
where:
- σy is the yield strength of the material.
- A is the cross-sectional area of the rail.
- SF is the safety factor.
The 7th axis system must dynamically respond to changes in load and speed to maintain optimal performance. This involves continuous monitoring and adjustment of parameters such as torque and acceleration. Advanced control algorithms and real-time feedback enable the system to adapt to varying operational conditions, ensuring consistent performance.
Advantages of the 7th Axis
The inclusion of the 7th axis in robotic systems offers several significant advantages, enhancing the overall capability, efficiency, and flexibility of robotic operations. Here are the key benefits:
1. Extended reach and workspace
The 7th axis provides linear movement along a rail or track, significantly extending the operational range of the robotic arm. This allows robots to cover larger work areas without needing to be repositioned manually, making them ideal for tasks that require movement across expansive spaces, such as assembly lines, large-scale painting, and material handling.
Impact on reach and workspace:
Metric | Traditional 6-Axis | 7th Axis Addition |
Maximum reach | Fixed range | Extended by rail length |
Workspace coverage | Limited | Significantly larger |
Need for repositioning | Frequent | Reduced |
2. Improved efficiency
By enabling robots to move linearly along an axis, the 7th axis reduces the need for multiple robots or manual repositioning. This increases the efficiency of operations by allowing continuous work over a broader area, minimizing downtime and improving overall productivity.
Efficiency metrics:
Metric | Traditional 6-Axis | 7th Axis Addition |
Cycle time | Longer | Shorter |
Downtime | Higher | Lower |
Operational speed | Moderate | Increased |
3. Precision
The 7th axis improves the precision and accuracy of robots over extended ranges. In practical applications like CNC machining or laser cutting, maintaining consistent quality over long distances is crucial. The additional linear movement allows for smoother and more controlled operations, ensuring high precision in tasks that require extended reach.
Metric | Traditional 6-Axis | 7th Axis Addition |
Positional accuracy | High | Higher |
Motion control | Comlex | Simplified |
4. Reduced wear and tear
Without a 7th axis, robots often need to make complex, repetitive movements to cover large areas, which can lead to increased wear and tear on joints and components. In real-world use, the linear movement provided by the 7th axis simplifies these movements, distributing mechanical stress more evenly and reducing wear. This has been observed in heavy-duty applications like construction robotics, where reduced wear extends the operational life of the equipment.
5. Simplified integration
Modular design principles allow for easy integration of the 7th axis into existing robotic systems. This simplifies upgrading and scaling operations. For example, in logistics, as the volume of goods increases, additional rail segments can be added to extend the reach of robotic arms, enabling them to handle larger workloads without significant changes to the overall system.
Applications of Modular Systems in the 7th Axis
The integration of modular systems in the 7th axis has significantly enhanced the versatility, efficiency, and precision of robotic operations across various industries.
In automotive manufacturing, the 7th axis allows robotic arms to move along assembly lines, performing tasks like welding, painting, and component installation. This ensures consistent weld quality, reduces cycle times, and improves workflow efficiency.
In the aerospace industry, the 7th axis is vital for assembling large aircraft components and performing maintenance tasks. Robots can install rivets and fasteners with high precision, apply coatings uniformly to prevent corrosion, and efficiently traverse aircraft for inspections and repairs, reducing downtime and enhancing operational efficiency.
Logistics and warehousing benefit from the 7th axis in automated storage and retrieval systems (AS/RS) and palletizing operations. Robots can move along aisles to pick and place items, conduct inventory counts, manage stock levels efficiently, and palletize goods along conveyor belts, increasing order fulfillment speed and accuracy.
In the pharmaceutical industry, the 7th axis enhances laboratory automation and production line efficiency. Robots can move samples between analysis stations, fill vials with precise dosages, and inspect products for defects, improving workflow efficiency, reducing contamination risk, and ensuring compliance with quality standards.
Electronics manufacturing sees improvements with the 7th axis in PCB assembly and quality assurance. Robots can place components on PCBs with high precision, accurately solder components, and perform detailed inspections, ensuring reliable electrical connections and maintaining product quality.
In medical and healthcare applications, the 7th axis enhances surgical robotics and medical device manufacturing. It provides precise control for minimally invasive procedures, improving patient outcomes by reducing recovery times and minimizing surgical trauma. Robots can perform complex surgeries like joint replacements with high accuracy, assemble intricate medical devices consistently, and package and sterilize them, ensuring hygiene and reducing contamination risks.
Table of some 7th Axis Applications:
Industry | Applications and Tasks |
Automotive | Welding, Painting, Component Installation |
Aerospace | Riveting, Surface Treatment, Maintenance |
Logistics & Warehousing | AS/RS, Inventory Management, Palletizing |
Construction | Modular Construction, Site Inspection |
Food & Beverage | Packaging, Palletizing, Sanitization |
Pharmaceutical | Laboratory Automation, Production Line Automation |
Electronics | PCB Assembly, Quality Assurance |
Medical & Healthcare | Surgical Robotics, Medical Device Manufacturing |
Final Thoughts
The integration of modular systems in the 7th axis has undeniably revolutionized the field of robotics, providing unprecedented flexibility, efficiency, and precision across various industries. From automotive manufacturing to aerospace, logistics, construction, food and beverage, pharmaceuticals, electronics, and healthcare, the advantages are clear. Robots equipped with the 7th axis can perform a wider range of tasks more accurately and over larger areas, leading to enhanced productivity and reduced operational costs.
The ability to move along a linear path without the need for frequent repositioning allows for more seamless operations and higher-quality outputs. This advancement not only optimizes current workflows but also opens the door to new possibilities in automation, paving the way for future innovations.
Please contact PIB Sales today to explore how we can support your business needs. Call us to learn more about our complete robotics solutions offering.