Dental handpieces are widely used in dental procedures to drill, polish, and cut teeth. Dental procedures require high-speed rotation to ensure accuracy and efficiency. Miniature high-speed ball bearings are an integral component of dental handpieces. Dental handpiece bearings help to reduce friction, noise, and vibration while ensuring smooth operation.
Miniature High-Speed Ball Bearings
Miniature high-speed ball bearings are designed to withstand high speeds and heavy loads while maintaining precision and accuracy. Bearings used in dental applications are small, typically ranging from 1mm to 10mm in diameter, and operate at up to 500,000 rpm. High precision miniature bearings can be designed with low friction and low noise features, making them ideal for use in dental handpieces.
Miniature high-speed ball bearings are made from stainless steel, ceramic, and hybrid materials. Stainless steel bearings are the most commonly used and offer excellent strength and durability. Ceramic bearings offer superior performance due to their high stiffness, low density, and resistance to wear and corrosion. Hybrid bearings are a combination of ceramic and stainless steel, offering the benefits of lightweight and higher speeds and are becoming the standard in the dental handpiece device.
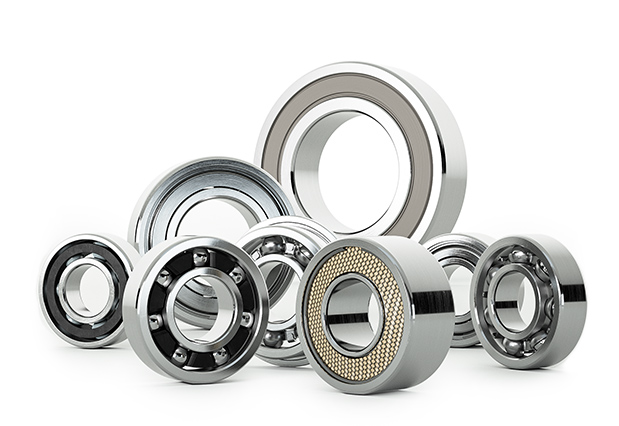
Overview of dental Handpieces
Dental handpieces are essential tools used by dentists and dental hygienists for various dental procedures. These devices require precision and accuracy during operation.
Miniature high-speed ball bearings play a crucial role in dental handpieces as they allow for smooth and precise movements of the device’s rotating parts, ensuring high-speed operation without vibration or noise. These bearings are highly durable and resistant to wear, which helps to extend the lifespan of the handpiece and reduce maintenance costs. They also generate minimal heat during operation, reducing the risk of damage to the handpiece and discomfort for the patient.
Myonic brand Miniature high-speed ball bearings are typically designed with low-friction properties, which helps to limit the energy consumption of the handpiece and improve its overall efficiency. Overall, the use of miniature high-speed ball bearings in dental handpieces is essential for achieving optimal performance, longevity, and patient comfort.
NSK brand provides high-precision miniature bearings tailored for dental equipment, particularly in the ABEC9 (P2) accuracy class. These bearings are manufactured with close toleranced bore diameters between 0.0025 mm and 0 mm, which significantly minimizes micro-vibrations and noise levels. This level of precision is achieved due to advancements in production technologies, specialized testing, and measurement methods.
Designed for dental air turbines, NSK’s range includes four series of deep groove and angular contact ball bearings, offering more than 40 variations in types and sizes. These bearings typically feature external diameters of 6.35 to 7 mm, bore diameters around 3 mm, and widths between 2.3 and 2.8 mm. They are lubricated with CF1, a high-performance, low-viscosity oil, ensuring optimal operation.
To purchase NSK bearings, you can visit the PIB Sales online shop.
Dental Bearing Installation
When installing a dental bearing, good practices should be followed for the best fit between the bearing’s bore and the shaft, with an optimal interference range of 0 to 2 mm. The shaft’s roundness deviation should be maintained at less than 2 micrometers (μm) to ensure proper alignment and function.
During installation, it is essential to apply the pressing force directly onto the inner ring of the miniature bearing. This approach prevents damage to the bearing’s accuracy by avoiding unnecessary pressure on the steel balls or the grooved sleeve of the ring.
After placing a pair of bearings on the turbine, it’s important to apply lubricating oil following the installation and clean the bearings thoroughly before seating them in the machine head. Be mindful not to use acetone or ethanol as cleaning agents.
Additionally, when installing the dental drill bearing into the handpiece, an axial preload of 1 to 2 Newtons (N) should be applied to the bearing pair. This specific preload ensures optimal high-speed performance of the dental drill.
Biocompatible Materials
Biocompatibility is an essential consideration when designing miniature high-speed ball bearings for dental handpieces. The materials used in these bearings must be non-toxic, non-reactive, and capable of withstanding the harsh conditions of the oral environment.
Examples of biocompatible materials used in miniature high-speed ball bearings include ceramic materials such as zirconia and alumina, and stainless steel and titanium. Ceramic materials are particularly popular due to their excellent biocompatibility, corrosion resistance, and high strength. Stainless steel and titanium are also commonly used due to their durability and resistance to wear and corrosion.
Additionally, some manufacturers may incorporate specialized surface coatings or treatments to enhance the biocompatibility and performance of the bearings, further ensuring their safety and effectiveness for dental applications.
Low Friction and Low Noise
Reducing friction and noise is another critical factor when designing miniature high-speed ball bearings for dental handpieces. Elevated levels of friction and noise can lead to discomfort for the patient and increase wear and tear on the handpiece. To reduce friction and noise, manufacturers may use specialized materials and coatings in the bearing’s design.
Examples of materials used to reduce friction include polymers like PEEK and PTFE, as well as ceramic coatings such as diamond-like carbon (DLC) and titanium nitride (TiN). Well known dental bearing and handpiece manufacturers like Myonic and NHBB use specialized lubricants and coatings to further reduce friction and noise while maintaining biocompatibility and durability.
By minimizing friction and noise, miniature high-speed ball bearings can help to improve patient comfort, extend the life of the dental handpiece, and enhance the overall efficiency of dental procedures.
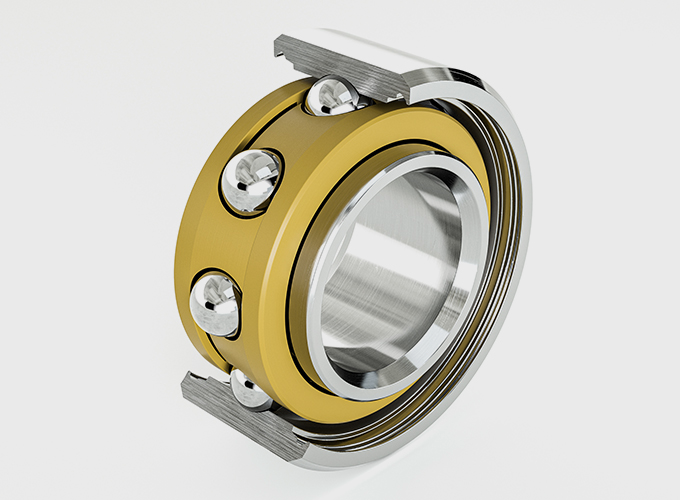
Miniature high-speed ball bearings are integral components of dental handpieces, providing the necessary support for rotating elements, reducing friction and noise, and ensuring the smooth operation of these devices. The use of biocompatible and corrosion-resistant materials ensures patient safety and the longevity and reliability of dental handpieces.
Dental professionals must choose high-quality miniature high-speed ball bearings to guarantee the success of dental procedures and improve patient comfort.
Miniature ball bearing suppliers
PIB Sales is a trusted supplier of miniature ball bearings, offering a wide selection of materials including stainless steel, chrome steel, and ceramic. For applications that involve exposure to harsh, corrosive environments—such as contact with blood or caustic gases—PIB provides materials specifically designed to withstand these conditions.
Our miniature bearings are versatile and can be used across a broad range of automation applications, making them ideal for challenging environments. Whether you require bearings for robotics, dental tools, or power tools, PIB offers options with protective coatings, shields, and specialized lubricants tailored for both industrial and medical uses.
At PIB, our engineers are committed to supporting you throughout your project, helping to identify the best bearing solutions.
Many of the largest and most reliable bearing manufacturers such as NMB, NSK, NHBB, SKF, FAG, and Myonic are ideally used in dental handpieces and other medical applications.
Buy Dental Handpiece Bearings Online Now.