Pacific International Bearing Inc offers Schaeffler’s comprehensive portfolio of bearing products aimed at industrial robotics. Schaeffler offers standard bearing components such as radial and angular contact ball bearings, cylindrical roller bearings, needle and spherical roller bearings.
Schaeffler has progressed beyond bearing only offerings with special developments that are matched to suit articulated robots. These new products include crossed roller bearings with and without gear teeth and XZU series angular contact needle roller bearings and strain wave gears.
Overview of Robotic Arm Mechanisms
Today, smaller robots and collaborative robots, also known as cobots, are being increasingly used for the automation of monotonous handling and assembly tasks.
Schaeffler has come up with a new bearing type aimed at use in articulated arms for lightweight robots and Cobots. The XZU series angular contact needle roller bearing is a new design offering 30% more tilting rigidity and 20% less friction than crossed roller bearings of the same size. It is even possible to change out a crossed roller bearing in existing Cobot joints with the Schaeffler XZU bearing of the same size. Please contact Pacific International Bearing Sales Inc for assistance in choosing the XZU bearing for your application.

To be clear this bearing is an improvement and is an alternative to crossed roller bearings used in robot and cobot arm joints. Again it is a product that can be put into existing products in the field as an upgrade and will outperform their crossed roller counterparts. Contact Pacific International Bearing Company to purchase XZU double row series angular contact needle roller bearings.
With the advent of the newly designed Schaeffler bearing supports for lightweight robot construction users now have an option to obtain better performance from lightweight robots and cobots.
The double-row XZU-series angular contact needle roller bearing has a large number of rolling elements, rigid line contact, and an internal support distance because of two separate raceways.
I cannot emphasize enough how through the use of XZU bearings will enable the customer an option to obtain optimum values with up to 30% more tilting rigidity and 20% less friction in comparison with crossed roller bearings of the same size. Schaeffler’s optimized cage design has lubrication pockets, which retain the lubricant in the rolling contact This feature reduces friction.
Another benefit to robot manufacturers is that they can now design smaller, lighter, and more rigid articulated arms using the new XZU angular contact needle roller bearings. In lightweight robots, the advantages include the oscillation of the robot arm is significantly reduced and the control rigidity is improved.
Would you like to discuss a specific project with us or obtain more information about our robotic sector-specific solutions? Contact us at [email protected].
New precision strain wave gears for lightweight robot construction
In addition to the improvements made with the introduction of the XZU double row angular contact needle roller bearing, Schaffler developed its own RT series Strain Wave Gear. We believe Schaeffler made a major advancement in technology and performance by using the XZU bearing in its own RT series Strain Wave Gear product.
RT2 and RT1 series precision strain wave gears & RT1-T series sensorized precision strain wave gears
In many cases, lightweight robots require less than high accuracy and have lower load requirements and so Schaeffler developed two options in offering a standard RT2 series and a High Torque RT1 series strain wave gear. The Standard and HighTorque range is supplemented by perfectly matched bearing supports and drives. The interesting development is that from these innovations from Schaeffler, we can now offer the most compact, the most powerful, and the most economical solutions for the majority of applications in robotics.
The RT2 Standard units are currently available in five sizes of 14, 17, 20, 25, and 32 with ratios from 50 to 160 mm and nominal torques from 18 to 372 Nm.
Standard Torque offers an extremely broad range of options and easy integration into your design. The HighTorque range (RT1) outperforms the most high-performance competing products.
The two product ranges use different types of precision strain wave gears. Integrating the XZU double row angular contact needle roller bearing results in superior performance and has created a dominant position for us in the area of robotic development..
Depending on the load capacity, available space, and dynamics, the Schaeffler robotic products offer: excellent positional accuracy, zero backlash, high nominal and peak torques, exceptionally long service life, low space requirements, and extremely low weight
Standard torque series (RT2)
The Schaeffler Standard units consist of a precision strain wave gear and an XZU output bearing with high load carrying capacity and high tilting rigidity depending on the drive configuration. The RT2 Standard units are currently available in five sizes of 14, 17, 20, 25, and 32 with ratios from 50 to 160 mm and nominal torques from 18 to 372 Nm.

Precision strain wave gears RT1-T with torque sensor
Pacific International Bearing Inc is now offering the new RT1-T series precision strain wave gears featuring a torque sensor system.
We are offering end users an option to replace their existing strain wave gear with our RT1-1 torque sensor version.
When using the RT1-1 sensor version you will have improved dynamics when the sensorised version. RT1-1 sensors are used in each cobot joint and combined with vibration compensation by robot manufacturers using control technology.
Consequently, higher velocities are achieved while maintaining positioning accuracy. This is achievable through the active compensation of vibrations.
Advantages of your cobot
- Compact design with integrated microelectronics and embedded AI No additional space required
- Very simple upgrade for non-sensor-based cobots
- Available in four sizes 14, 17, 25, and 32 Ideal for use in collaborative applications
- No influence on the mechanical system or on torsional rigidity High-precision
- Sensotect coating with structure in the sub-micrometer range
- Excellent long-term stability of the sensor technology over the entire operating life
- Unaffected by temperature
- Direct torque measurement; minimal deviation in hysteresis and linearity
- High sensitivity
- Precise torque measurement for very high requirements
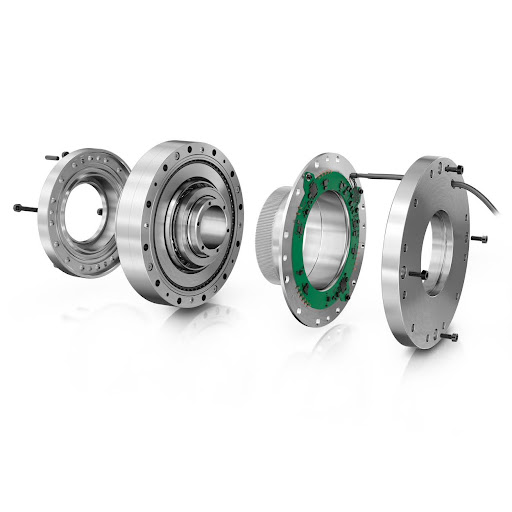
Would you like to discuss a strain wave gear specific project with us or obtain more information about our robotic sector-specific solutions? Contact us at [email protected]
Go here where you will find further information about our products from the industrial robotics and lightweight robotics area.
Engineering Challenges in Lightweight Robot Construction
The pursuit of high-performance lightweight robots hinges on advancements in key enabling technologies, and bearing supports are no exception. While innovative designs, such as double-row angular contact needle roller bearings, offer significant potential for increased joint stiffness, reduced friction, and enhanced load capacity, these advantages must be translated into tangible improvements at the system level. Achieving this requires careful consideration of several interconnected engineering challenges.
The fundamental challenge is to effectively integrate these advanced bearings into the overall robot design, optimizing performance across multiple domains:
Transform tearing stiffness into improved positional accuracy and dynamic performance. A bearing with increased tilting stiffness offers the potential for improved positional accuracy and reduced settling time. The increase can be as much as 30%. However, the ability to realize these benefits depends on the robot’s control system and structural characteristics:
- Control system design. The control system bandwidth, measured in Hz, must be high enough to capture and respond to the increased stiffness of the joint. The sensor is also relevant.
- Structural resonances. The robot arm structure should be designed to minimize structural resonances within the operating frequency range. This can be achieved through careful material selection, optimized geometry, and the use of damping materials.
- Bearing preload. Properly preloading the bearings, typically achieved through shimming or other adjustment mechanisms, is essential for maximizing stiffness and minimizing backlash.
Managing increased load capacity and its impact on structural design. Bearings capable of supporting higher loads allow for the design of lighter and more compact robot arms without sacrificing performance or reliability. However, this requires careful attention to the structural design of the arm itself:
- Lightweight materials with a high specific strength-to-weight ratio and specific stiffness-to-weight ratio must be selected. Carbon fiber-reinforced polymer composites, with their high strength and stiffness, are a common choice but require careful consideration of their anisotropic properties and manufacturing challenges.
- FEA simulations are essential for optimizing the arm structure and minimizing stress concentrations. The FEA model should include detailed representations of the bearing supports and their interaction with the surrounding structure.
The integration of innovative gearboxes also needs to have Fan EA simulation to evaluate stress.
Minimizing friction and maximizing energy efficiency. Reducing friction within the bearing support directly translates into improved energy efficiency and reduced heat generation.
In summary, fully realizing the potential of advanced bearing systems in lightweight robots requires a holistic engineering approach that considers the interactions between bearing performance, control system design, structural design, and material selection.
Integration with Strain Wave Gears
Strain wave gears, commonly known as harmonic drives, play a crucial role in lightweight robotics, particularly in compact articulated arms and cobot applications. These highly efficient, zero-backlash gear systems provide precise torque transmission and high reduction ratios, allowing robots to execute smooth, controlled movements even under heavy loads. However, their performance is heavily dependent on the bearing supports that stabilize and guide their motion.
Schaeffler’s XZU double-row angular contact needle roller bearings are specifically engineered for integration into strain wave gears, providing enhanced rigidity and uniform frictional resistance. One of the main advantages of this bearing type is its ability to withstand high radial and axial loads, ensuring that the flex spline — the critical component that deforms to transfer torque — remains stable during operation. Traditional crossed roller bearings, while effective, often introduce higher friction and require additional structural reinforcement, whereas the XZU series allows for a compact, lightweight design without compromising performance.
Another challenge in strain wave gear integration is maintaining durability over extended duty cycles. The continuous elastic deformation of the flex spline exerts significant stress on internal bearing components, requiring solutions that enhance wear resistance and fatigue strength. To address this, Schaeffler has developed RTWH DuraWave precision strain wave gears, which incorporate optimized 3D tooth geometry and advanced material coatings to reduce friction and improve longevity. These innovations not only extend the service life of robotic joints but also enhance positioning accuracy, a critical factor in applications such as surgical robotics and semiconductor handling.
The combination of high-performance bearings and strain wave gear technology enables manufacturers to develop smaller, lighter, and more agile robotic arms. By integrating Schaeffler’s precision-engineered bearing supports, robotic systems benefit from lower energy consumption, reduced mechanical losses, and superior motion control, making them more adaptable to modern automation challenges. As lightweight robotics continues to evolve, the synergy between bearing design and strain wave gear innovation will play a pivotal role in shaping the future of high-performance robotic applications.
Conclusion
At Pacific International Bearing Sales Inc., we specialize in providing a comprehensive range of high-quality bearings and components tailored for robotic applications. Our expert team is ready to assist you in selecting the ideal bearings for robotic arms. Contact us today to ensure your robotic systems operate at their peak efficiency. Explore our online catalog and request a consultation at [email protected]. Buy Schaeffler bearings, strain wave gears, and other robotic related products at www.pibsales.com.